Additive Manufacturing in Medicine – how 3D Printing can save lives
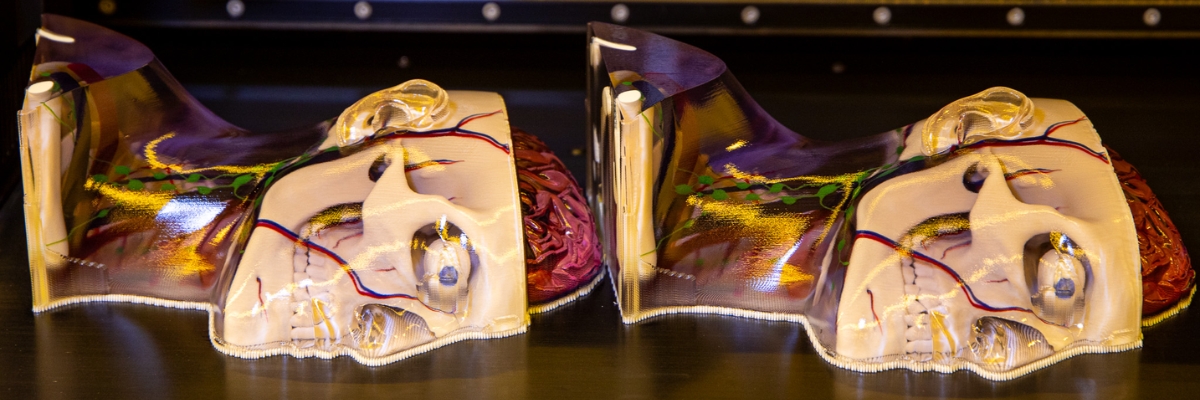
Hardly any other science has made such steady progress in the history of mankind as medicine. From bloodletting as a universal remedy and insane therapeutic approaches such as sitting in a rotting whale for 30 hours to cure rheumatism (this is no joke!), to the iron lung and the almost inflationary prescription of methamphetamines, to the present day, when highly complex brain operations and heart transplants can be performed.
This progress is far from over. There are always breakthroughs in the cure of previously incurable diseases, such as cancer and HIV, and new non-invasive surgical procedures that minimise the risk to patients during surgery.
Additive manufacturing is increasingly playing a role in this progress. Whether it's advances in patient safety and well-being, advances in surgical preparation and simplification for surgeons, or advances in precisely fitting implants and organs, 3D printing is at the forefront.
Additive manufacturing is not limited to just one area of medicine. Dentistry, neurosurgery, veterinary medicine, and even forensics are now using 3D printing and its advantages.
I would like to dedicate this blog post to the many advantages and applications of 3D printing in medicine. So, without further ado, let's start with one of the largest of these areas of application.
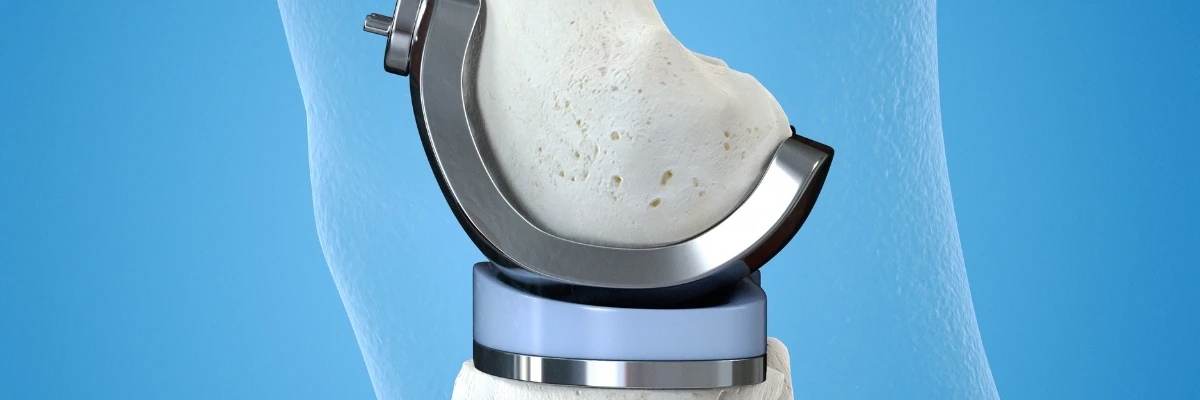
Implants
High costs and long waiting times – the problems of implants
Implants of any kind are expensive. Even uniform implants can cost thousands of euros to manufacture. If customised implants are needed, the costs quickly skyrocket.
In addition to the costs, there are sometimes long waiting times. While uniform implants can be obtained quickly, waiting times of several weeks to several months are planned for customised implants.
For many patients, these waiting times are associated with great pain. In emergency situations, standardised implants are often used to skip the waiting time – but in the worst case, this can lead to complications and thus to further pain for the patient.
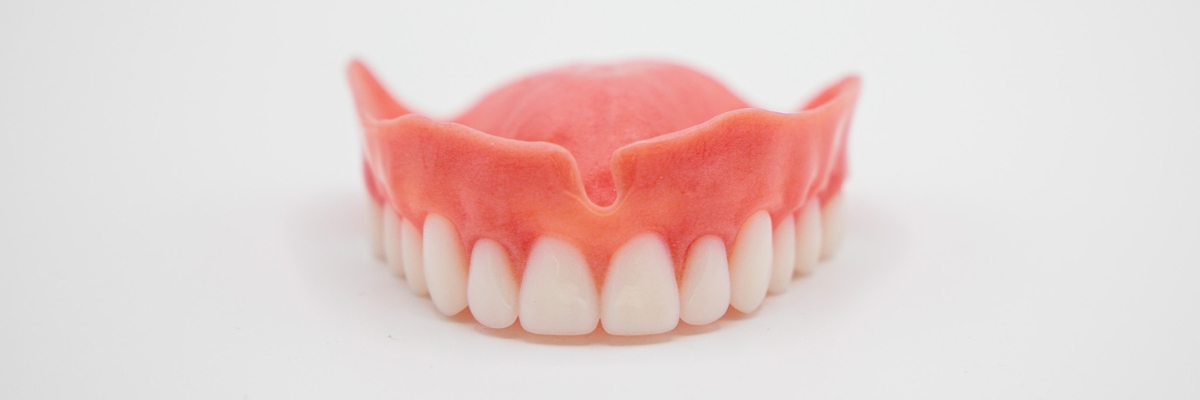
How Additive Manufacturing can solve these problems
Additive manufacturing offers a solution to these problems. It enables a much faster and more cost-effective production of implants. This production can also be relocated directly to hospitals to avoid long delivery times. As a result, emergency surgeries can be performed much faster with precisely fitting implants, which can save patients' lives.
Titanium is the metal most commonly used for implants. It offers excellent strength, durability and biocompatibility. That being said, there are many other materials that can be used to make implants, thanks to the wide range of materials available. For example, PEEK and silicone can now be used to manufacture implants.
3D printing is suitable for a wide range of different implants. Teeth, knee joints, cruciate ligaments, as well as parts of the pelvic bone and sternum are now among the standard applications for additive manufacturing in the field of implants.
Furthermore, jaw and even skull implants are now possible with the help of additive manufacturing. Just a few months ago, a PEEK skull implant was successfully transplanted into a patient at the University Hospital in Salzburg.
3D-printed implants are also creating new possibilities for animals. From prosthetic legs for dogs to a new beak for parrots, additive manufacturing is opening up new possibilities in veterinary medicine.
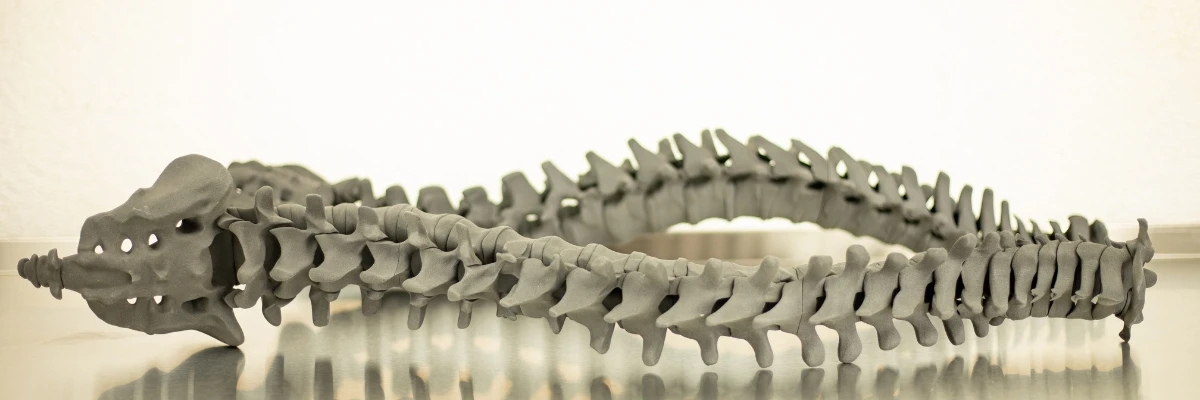
More applications and materials – what the future holds
Implants are becoming more and more important. The average age is increasing, people are getting older and so are their bones, teeth and joints. In the last 20 years, the number of dental implants required alone has risen from around 380,000 to around 1.3 million. In 2021, there were a total of 172,011 knee implants in German hospitals, and even the number of people under the age of 60 with knee implants is steadily increasing.
The fast and cost-effective production of implants of all kinds will therefore become increasingly important in the future. At the same time, additive manufacturing will continue to develop to provide medicine with more materials, more purposes and more possibilities.
One development that I would particularly like to focus on is research into materials with antimicrobial, i.e. infection-fighting, properties for additive manufacturing. Researchers at the University of Bath in the UK, in collaboration with Ulster University, published a press release presenting their latest findings in this research at the beginning of April 2023.
To summarise briefly: The material is able to kill 70% of bacteria in just 15 minutes, even at a high concentration of aggressive E. coli bacteria.
Such an antimicrobial material can drastically reduce the risk of infection, thereby reducing treatment time and costs, as fewer extensive follow-up operations are needed due to infection, while also increasing patient well-being.
In addition to reducing costs and time, additive manufacturing also increases patient safety. However, this is not only due to antimicrobial materials. An important aspect of patient safety is the preparation of surgeons for an operation – and here, too, additive manufacturing can help.
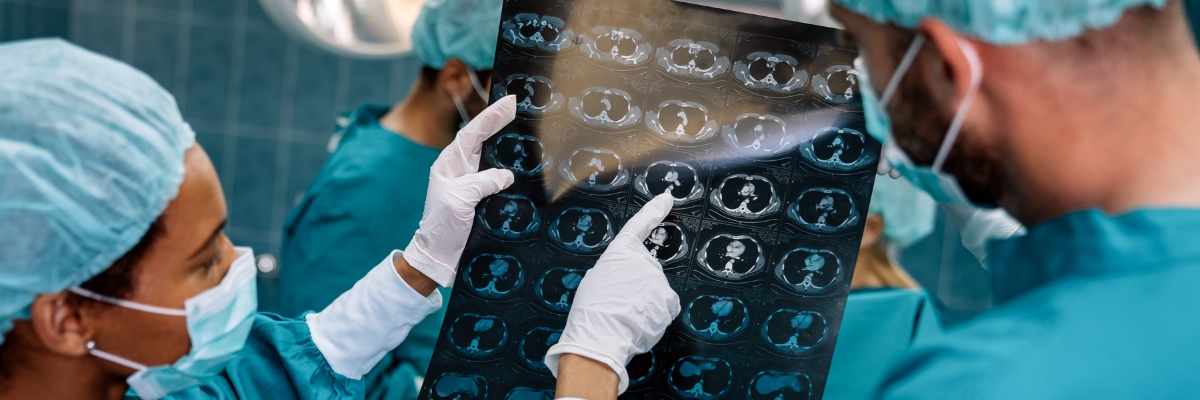
Pre-operative Preparation
Small errors with drastic consequences
The third leading cause of death in the United States is medical error. No matter how advanced technology becomes, as long as operations have not been completely taken over by robots, there will always be human error in medicine that costs patients their lives.
During an operation, it doesn't take a major lapse in concentration; a brief moment of inattention or an unforeseen haemorrhage is enough to cause a life-threatening complication.
Of course, 3D printing cannot magically reduce the margin for error to zero. It can never ensure that all doctors are prepared for all possible difficulties at all times. But additive manufacturing can facilitate the preparation and even the training of surgeons and make it more realistic.
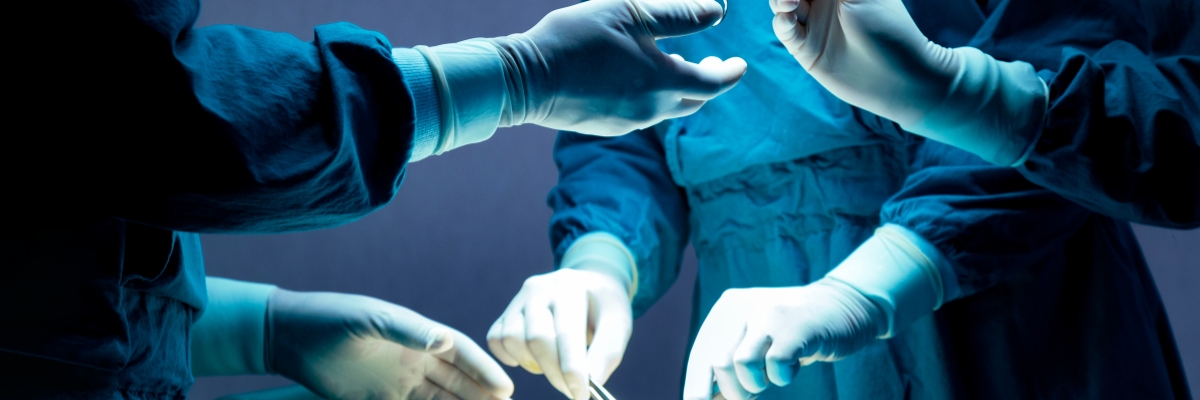
More reality in practice means fewer mistakes in practice
Surgical models can be produced with great speed and precision using 3D printing. The increased speed helps to give surgeons more time to prepare, while the increased precision makes the preparation more realistic, reducing errors and giving surgeons the opportunity to better anticipate unforeseen circumstances.
In many cases, these surgical models can even be directly adapted to the patient's characteristics. The size, shape, weight and many other factors of these models, whether they are organs, joints or bones, can be reproduced as a digital model based on CT scans and then printed out on a 3D printer.
However, realistic models not only help practising surgeons – trainee surgeons also benefit from them. Until now, students have mainly used organs, joints, bones, etc. from deceased people, but these were very expensive and difficult to obtain. 3D printing enables the fast, precise and cost-effective replication of all these practice models, so students can continue to receive a realistic education without the exorbitant costs previously associated with it.
Last but not least, these models also help patients and their relatives before surgery. With the help of these models, surgeons can show their patients in detail how the operation will proceed, what problems might arise and how these problems can be overcome. For some patients and relatives, this demonstration before the operation can provide reassurance – even if others, like me, for example, would faint just by seeing it.
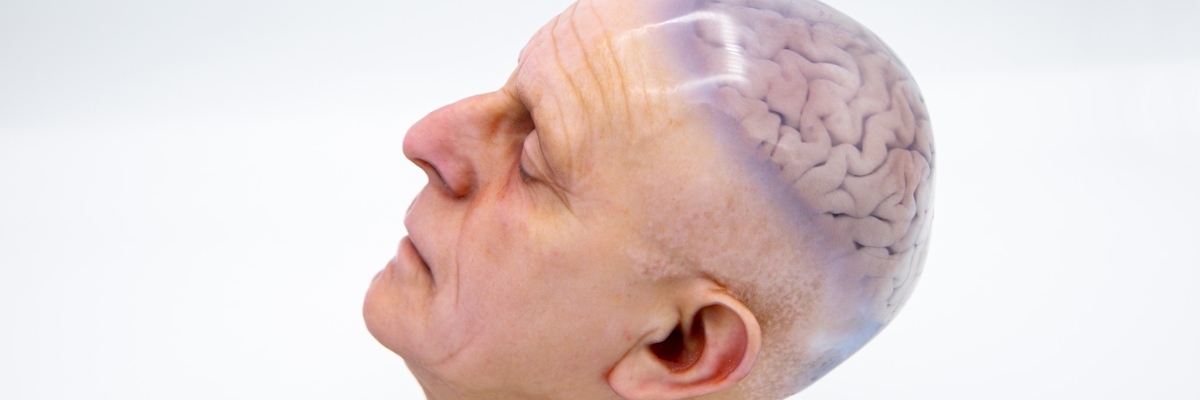
More details and subtleties – What the future holds
Additive Manufacturing is becoming more and more detailed, precise and fast. New technologies are being developed, new printers are coming onto the market, new materials are being produced – permanently.
For surgeons, whether practising or aspiring, this means a higher level of detail with the smallest subtleties for practice and preparation. And the closer the training model is to reality, the more likely it is that errors can be prevented.
Many clinics and hospitals already use 3D printing to prepare for operations. From the University Hospital Leipzig to the Hôpital Marie-Lannelongue near Paris and the Seattle Children's Hospital, 3D printing is already helping many surgeons around the world.
Over time, this technology will continue to spread, giving even more surgeons the opportunity to prepare their operations on realistic models, thus saving patient lives worldwide.
Perhaps, hopefully, additive manufacturing will even drastically change the statistics on causes of death by massively reducing medical errors. I can't predict the future, but it is undoubtedly possible.
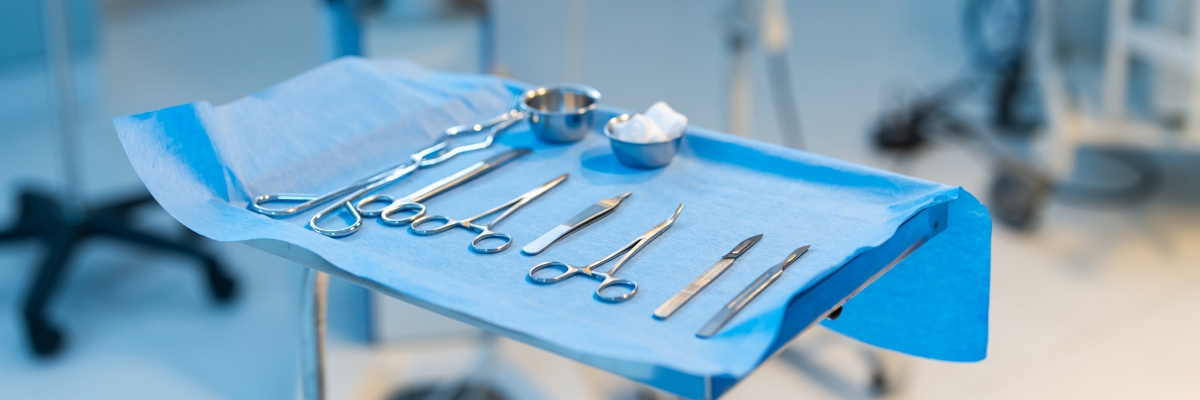
Medical Instruments
Life-saving and expensive
Medical instruments are essential in every hospital. Scalpels, surgical guides, wound hooks, curettes and a whole range of other wondrous devices are used to enable surgical procedures.
These instruments are usually produced in very small numbers. This is mainly due to the different dimensions in which all these instruments are needed. Due to this small production number, the instruments are often relatively expensive – a single wound hook, for example, can cost over 15 euros – and due to the many different dimensions, many individual instruments are still needed overall, which multiplies the costs.
In addition to the costs, availability can also be a problem. During the coronavirus pandemic, there were some shortages of medical instruments because their production was largely outsourced to Asia.
Additive manufacturing cannot solve both problems – but it can help to alleviate them!
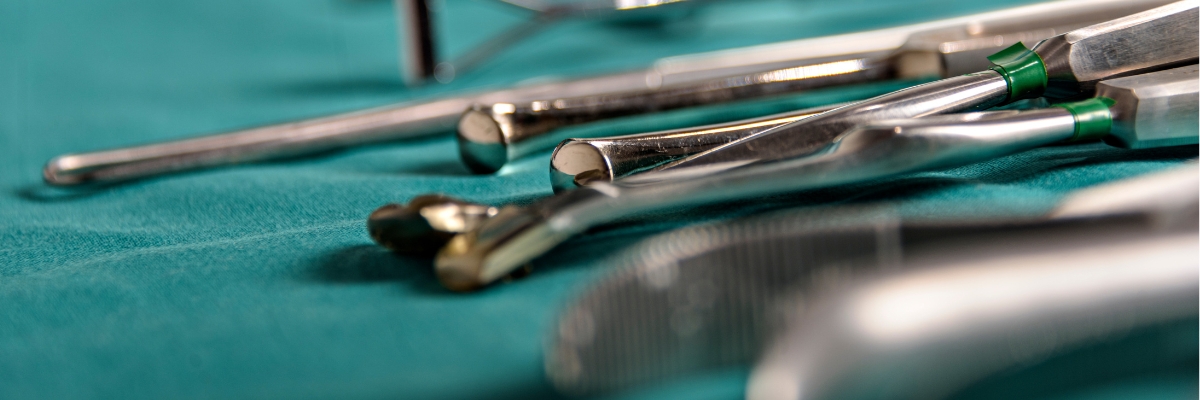
More customised instruments enable more precise work
Before we get to the costs and availability, I would like to highlight another huge advantage of additive manufacturing of medical instruments – increased customisation.
Additive manufacturing enables new geometries that would be impossible with conventional manufacturing. This allows certain instruments to be refined, other instruments to be connected, and almost all instruments to be customised for the doctor and patient. This gives doctors and surgeons more options for perfectly adapting their instruments to the circumstances, without incurring massive additional costs.
The costs of medical instruments, whether individual or universal, can be massively reduced by additive manufacturing. In a 3D printer, several different components can be produced in a single printing process, and therefore different dimensions of the same instrument. This not only reduces costs but also the time needed for production.
Reducing the manufacturing time is also important to increase availability. This means that, in the event of bottlenecks, the required instruments can simply be produced in-house, which also saves storage space.
This in-house production can also help hospitals in developing countries. Instead of long waiting times for delivery and very high cumulative costs, a one-time investment in a 3D printing system is sufficient to produce instruments quickly, easily and cheaply in-house.
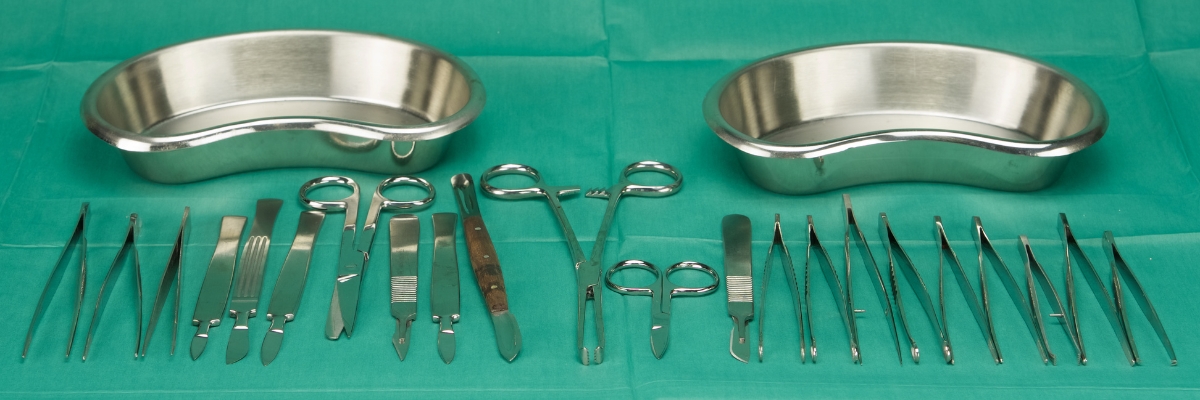
Faster reactions and more complex instruments – What the future holds
Even if the coronavirus pandemic now seems to be in the past, we should not forget the lessons it taught us. One of the most important lessons is undoubtedly that production in emergency situations requires the fastest possible response!
From one day to the next, masks, test sticks, protective equipment and much more were in short supply. Since most of this medical equipment is no longer produced in Europe, global travel restrictions were devastating, especially at the beginning of the pandemic.
Additive manufacturing can very effectively prevent a repeat of such situations in the future. Even during the pandemic, test sticks and masks, for example, were produced using additive manufacturing to compensate for delivery failures.
In these three years, yes, it really has been that long since the start of the coronavirus pandemic, 3D printing has become much more widespread, partly because of the pandemic. Many more medical institutions are now using a 3D printer to support their production of medical instruments.
This widespread use means that additive manufacturing can provide much more help in emergency situations to avoid supply bottlenecks. Of course, it would simply be better not to have any emergency situations with supply bottlenecks – but right now, everything is going haywire anyway, so it's better to be over-prepared than to regret a lack of preparation in the end. Especially in medicine.
The ever-increasing complexity of components that can be manufactured using 3D printing will also play a major role in the future of medical instruments. This means that an increasing number of different instruments can be manufactured using additive manufacturing. The development of completely new instruments through additive manufacturing and the great freedom of design that it offers will certainly also play a role in the future.
However, what many researchers and medical professionals are focusing on much more when it comes to the future is the production of fully functional organs using 3D printing. What may still sound like a distant future to some has been extensively researched and developed for a long time, and the results are truly amazing.
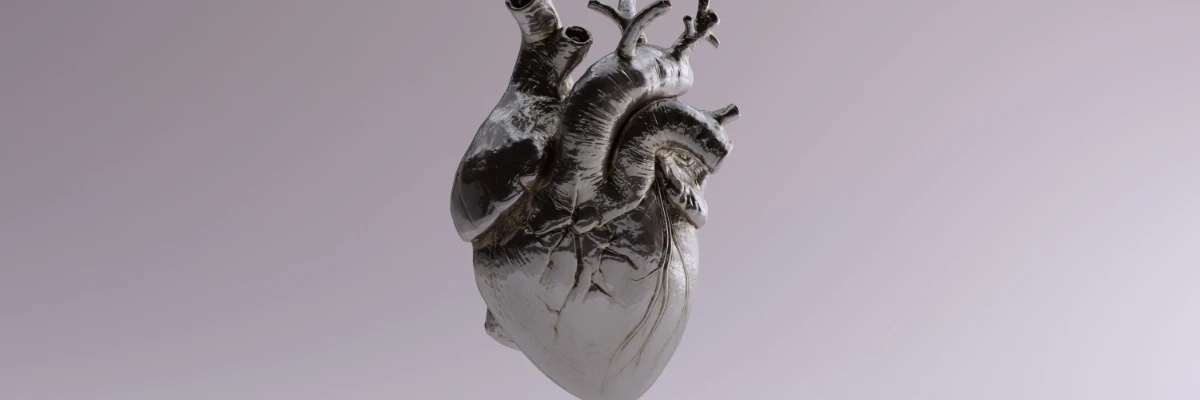
Organs
8,200 waiting – 960 donating
According to an article in the Oncology Journal, the number of organ donors in 2024 has decreased. While there were still 965 donors in 2023, there were 12 fewer in 2024. At the same time, approximately 8,260 people are waiting for an organ transplant that can at least improve their lives, and in many cases save them.
The organ donation rates are far too low to help everyone in need. Last year, 2,695 people were helped by the transplantation of one or more organs. In correlation to the numbers on the waiting list, this is obviously not enough.
There are various reasons why people decide against organ donation. And even if they do decide in favour of it, many requirements have to be met for an organ donation – the most important of which is that the patient has to die in the intensive care unit, as they have to continue to be ventilated in order to continue to supply the organs with oxygen.
Organ donations are also essential for medical research. Tests for drugs can be carried out on such organs, which speeds up the approval process for effective cures.
There is a lack of both donors and organs. Unfortunately, additive manufacturing cannot do anything about the lack of donors – but it can help with the lack of organs, at least in the future.
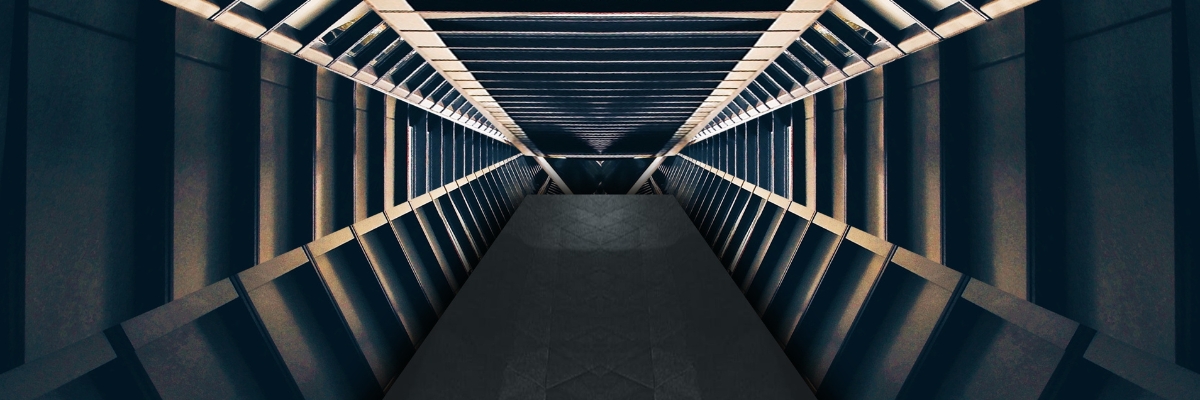
From science fiction to reality
3D printing of organs sounds surreal to many people – probably rightly so. Having a machine produce a fully functional organ seems like a creative idea of a science fiction author. However, research into making 3D printing of organs a reality is progressing in leaps and bounds.
For example, Boston University has already developed a miniature replica of a human heart that can be produced using additive manufacturing. This miniature heart, known as miniPUMP, consists of human heart and stem cells as well as microscopically small, 3D-printed acrylic parts. Thanks to its living tissue, it can beat independently – just like a real human heart.
In Brazil, miniature liver models have been produced entirely using additive manufacturing. These mini-organs, made from human blood cells, are able to perform all the necessary functions for humans, according to the researchers.
Active research is also being conducted into the additive manufacturing of kidneys. For example, the US company United Therapeutics and the Israeli biotechnology company CollPlant are working together to enable perfect reconstructions of kidney tissue using 3D printing. In the first step, such kidney tissue could spare people with kidney failure dialysis; in the second step, it could enable complete replicas of kidneys.
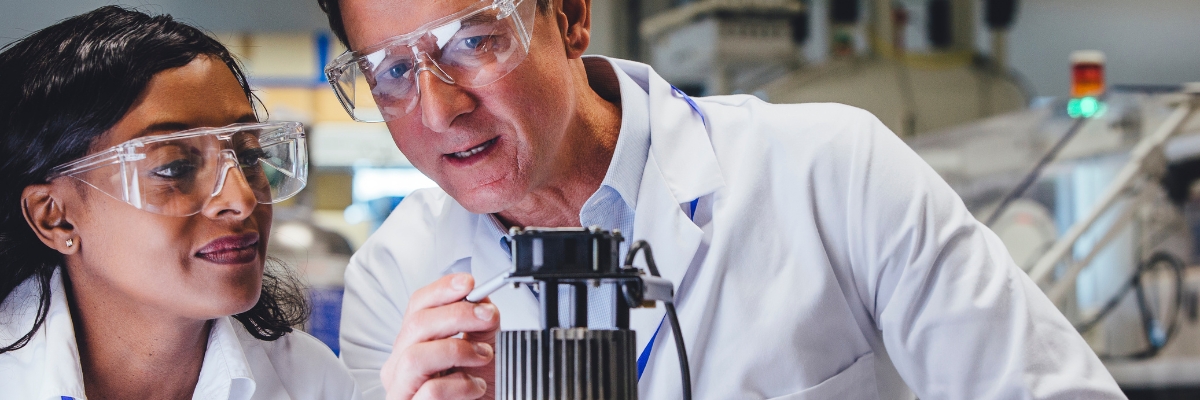
Empty waiting lists and better research – What the future holds
Research into the additive manufacturing of organs is still at the beginning of a long journey. It will be some time before we can transplant the first fully functional organ.
Nevertheless, the projects that already exist, of which there are many more than I have listed, give hope. The hope is that the number of available organs will multiply, leading to fundamental changes in both medical research and organ donation statistics.
Exactly when that day will come, however, is still written in the stars. Estimates of when this goal can be achieved vary widely, ranging from a few years to several decades. But no matter how long it takes, hope remains.
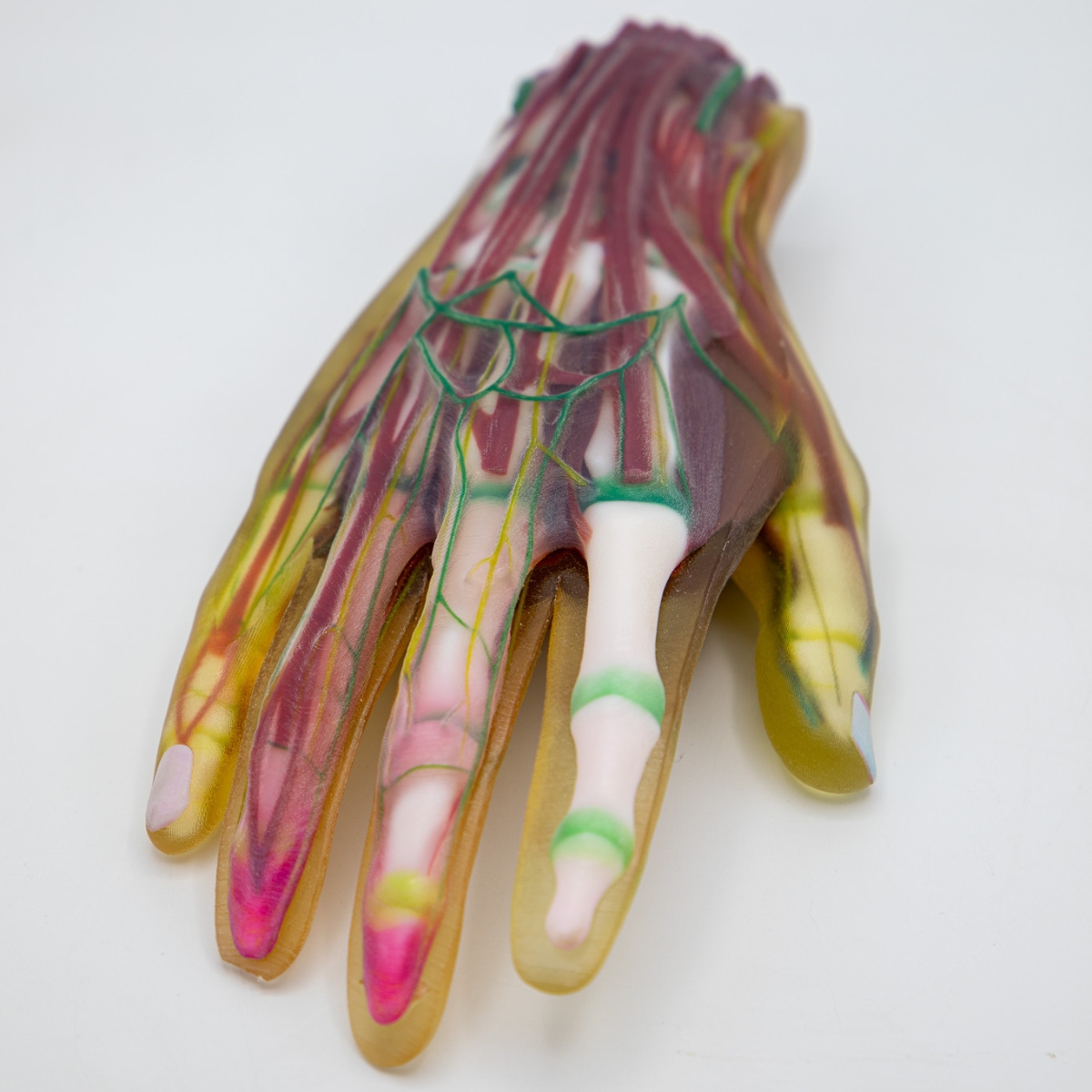
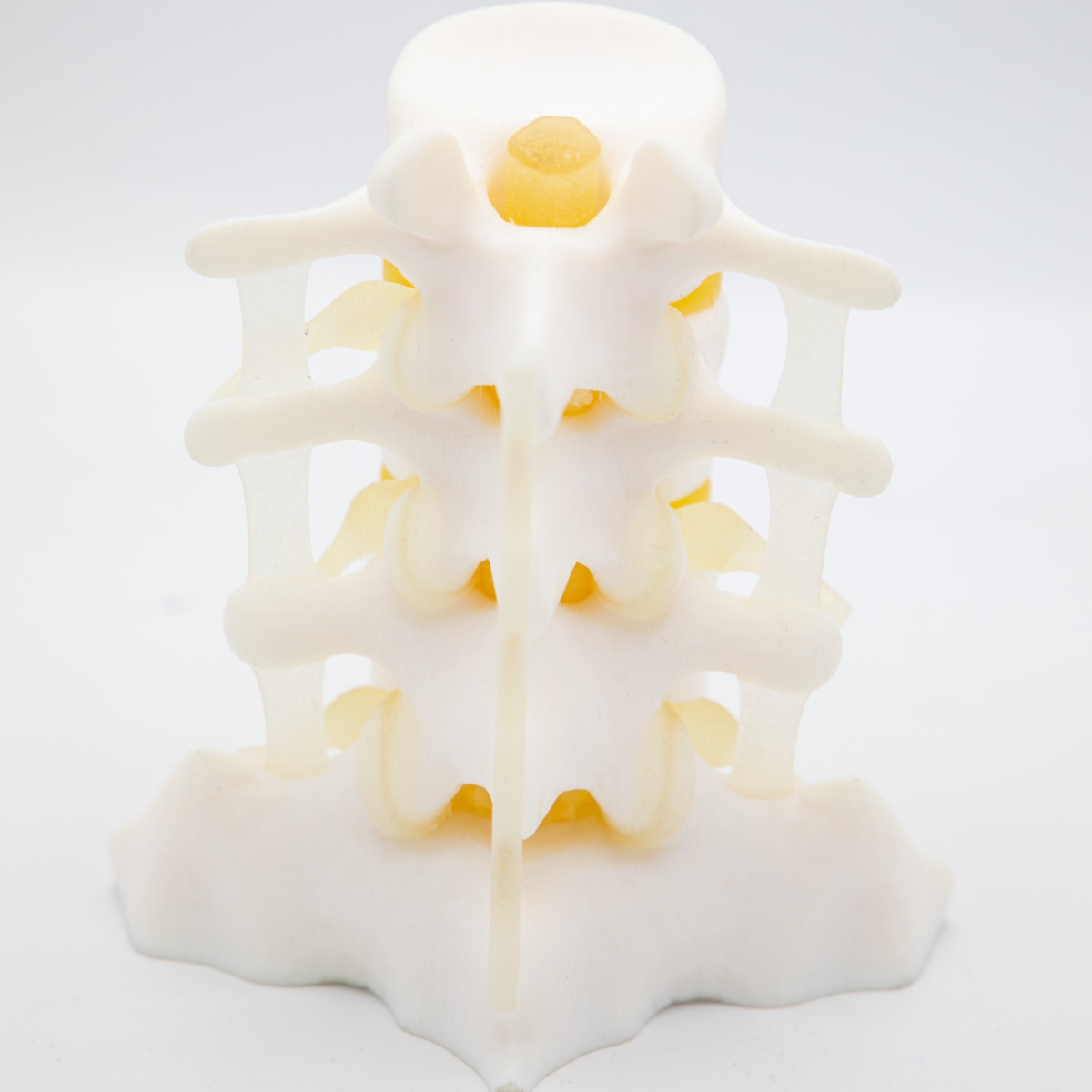
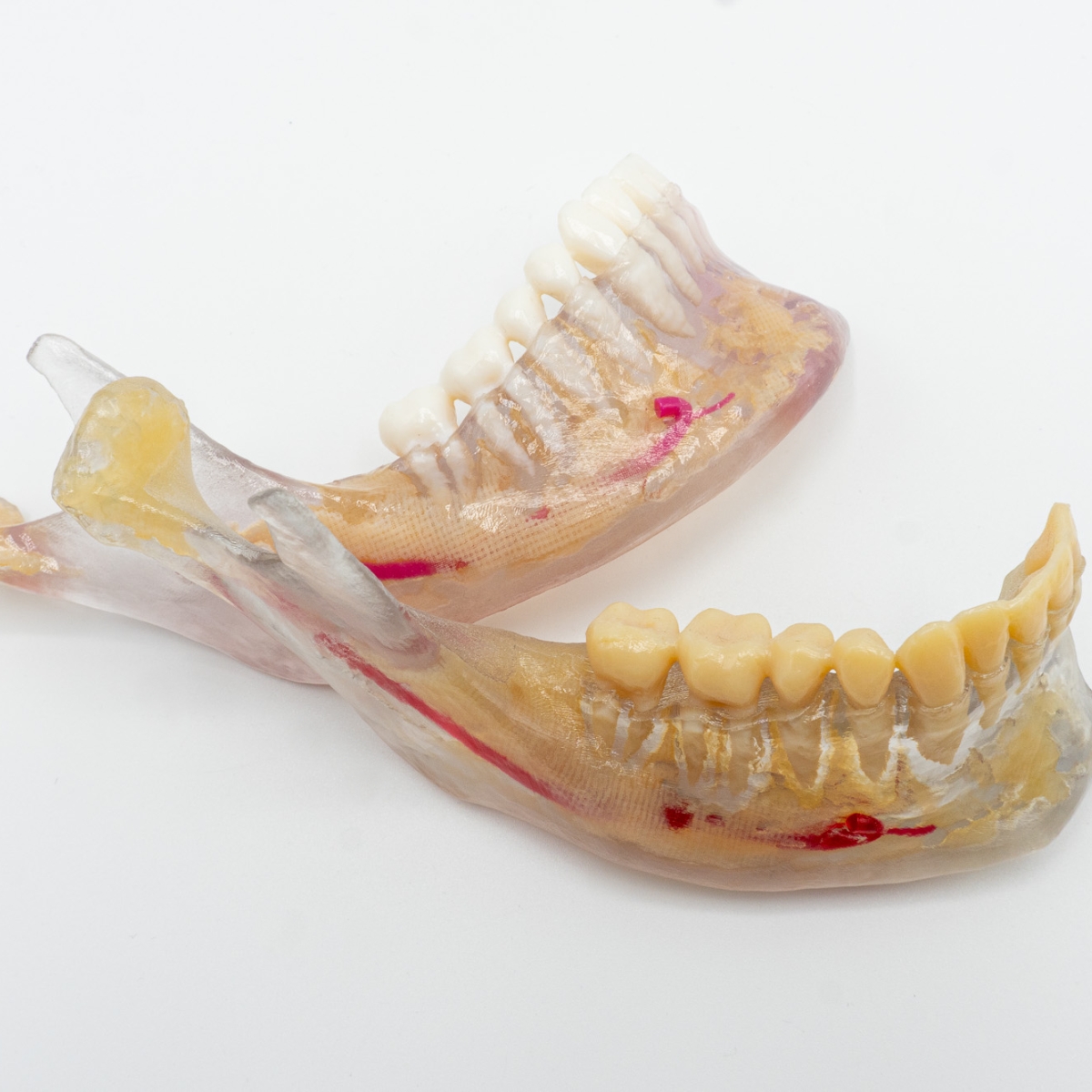
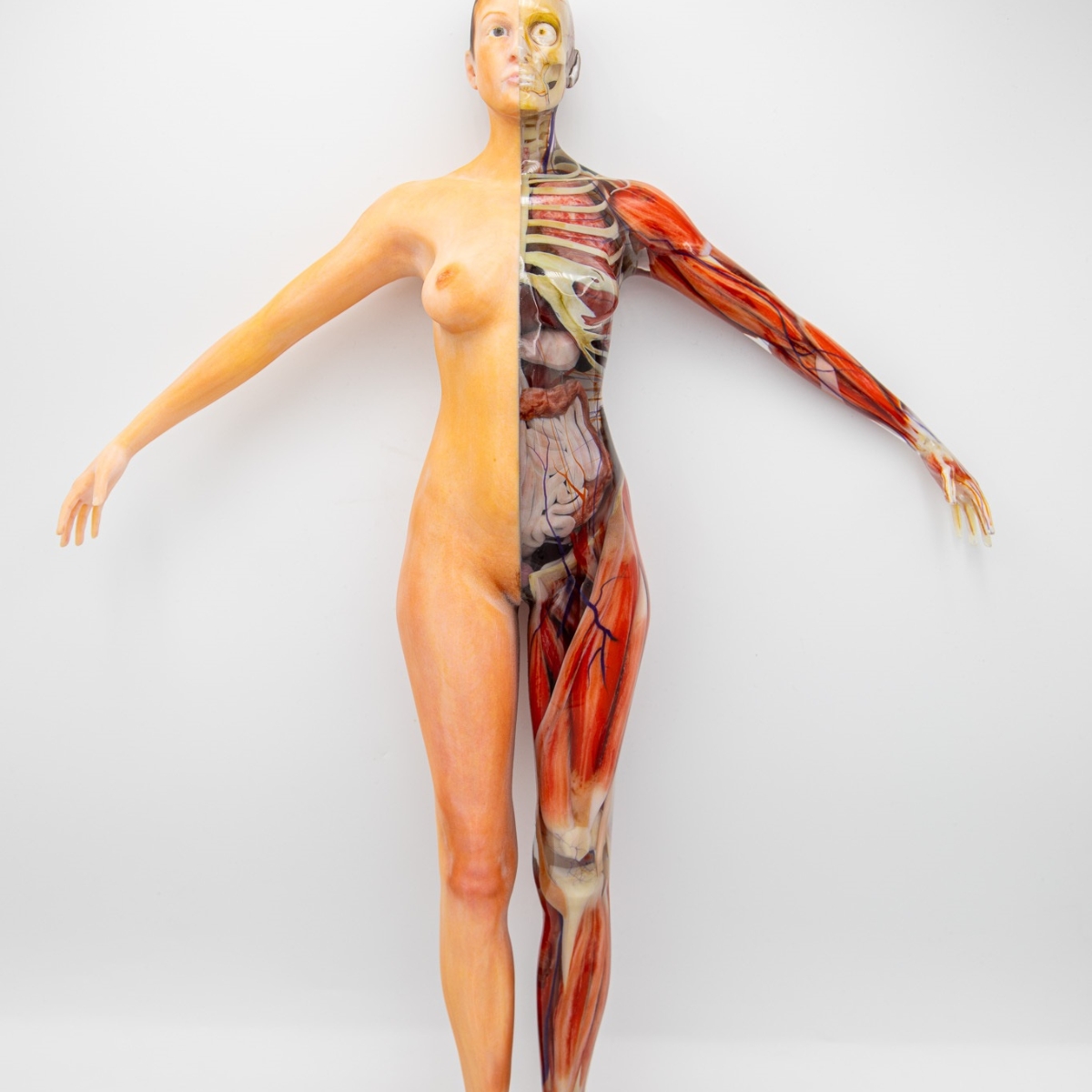