Safe journey to the operating theatre – how 3D printing is revolutionising preoperative planning
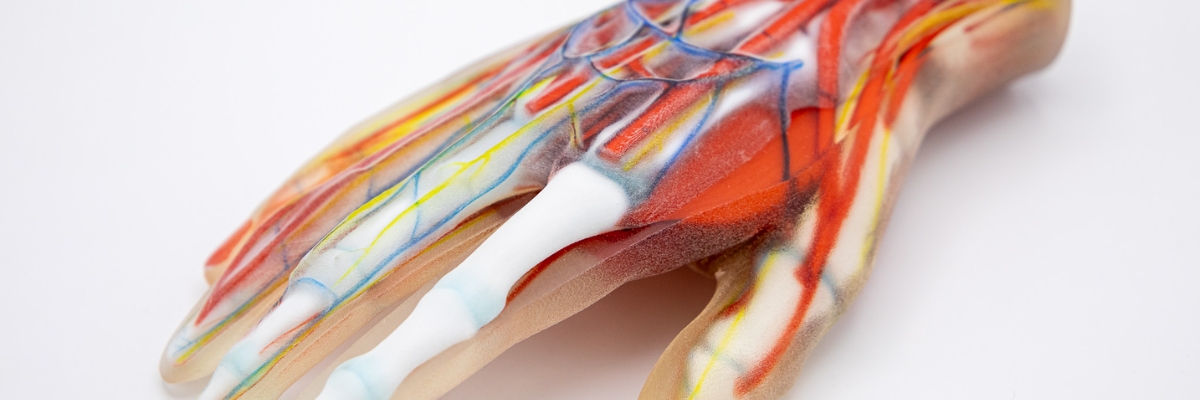
Surgical procedures are always nerve-wracking – but not only for the patient. Surgeons are also under great pressure during operations, of course. A single mistake or an unforeseen complication can be enough to turn even a routine procedure into a life-threatening situation.
To minimise this pressure, preoperative planning is essential. Surgeons can use this to both rehearse the actual operation and anticipate potential intraoperative complications, as well as develop strategies for managing them, thus creating more certainty for both sides.
This preoperative planning is done either digitally or with the help of anatomical models. The digital version is particularly popular because the digital model can be quickly modified, but of course it does not provide the tactile feedback that models can offer.
Traditionally manufactured models, often made using injection moulding, CNC or vacuum casting, provide the desired tactile feedback, but they come with their own set of problems. Production times, labour costs and a lack of customisation are among the most important of these.
Thanks to its unique properties, 3D printing can help. In this blog post, I would like to discuss the advantages of 3D printing for the production of medical models. I will limit myself to the most essential ones, although there are certainly many more.
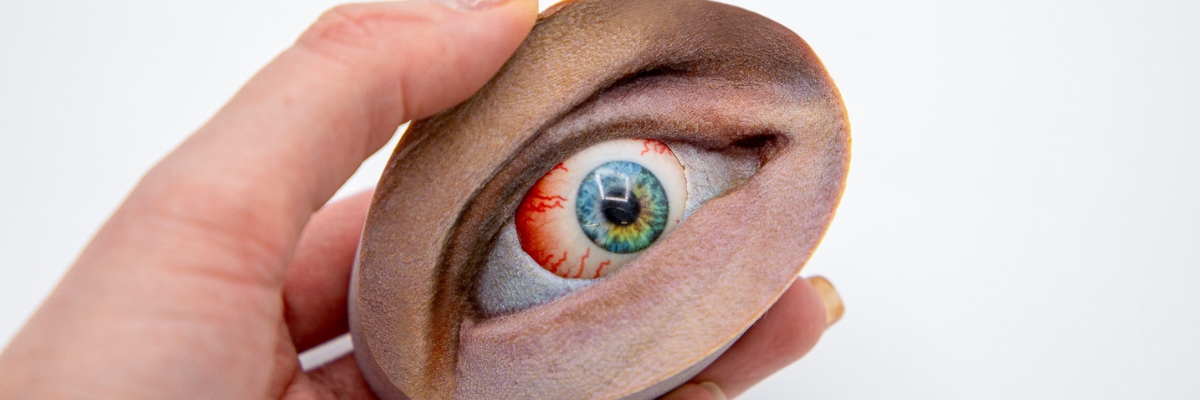
Personalisation
One of the biggest arguments in favour of using 3D printing to manufacture medical models is the ability to produce personalised models quickly and with very little effort.
While traditional methods would require planning for each individual model's lead and changeover times, additive manufacturing can usually produce unique pieces with no changeover time at all; at most, a material change may be necessary.
Instead of exchanging machine heads or producing new casting moulds, simply modifying the digital model is enough to get the 3D printer to implement the desired changes.
This is particularly relevant when it comes to complex surgical procedures or clinical pictures that rarely occur in practice. With customisation using 3D printing, surgeons have a highly detailed, practice-oriented and lifelike model for these cases too, enabling them to plan their operation thoroughly.

Production speed
When it comes to surgery, time is often of the essence. When urgency is compounded by complexity, surgeons face a difficult task. They need to prepare for the operation in the best possible way, but at the same time, they cannot afford to lose any time.
While conventional methods can take from several days to over a week to create a model, depending on its size and complexity, 3D printing can produce a highly detailed model in just a few hours to a day, once a high-quality DICOM data set has been created.
Of course, this speed is still not fast enough for emergency surgeries, but for such surgeries, no speed in the world would be sufficient to allow surgeons sufficient time to prepare for the operation.
However, for other urgent surgeries with at least a short time frame for planning, this speed advantage can make a significant difference, even if it is only a rudimentary preparation, which can already give surgeons a great deal more certainty.
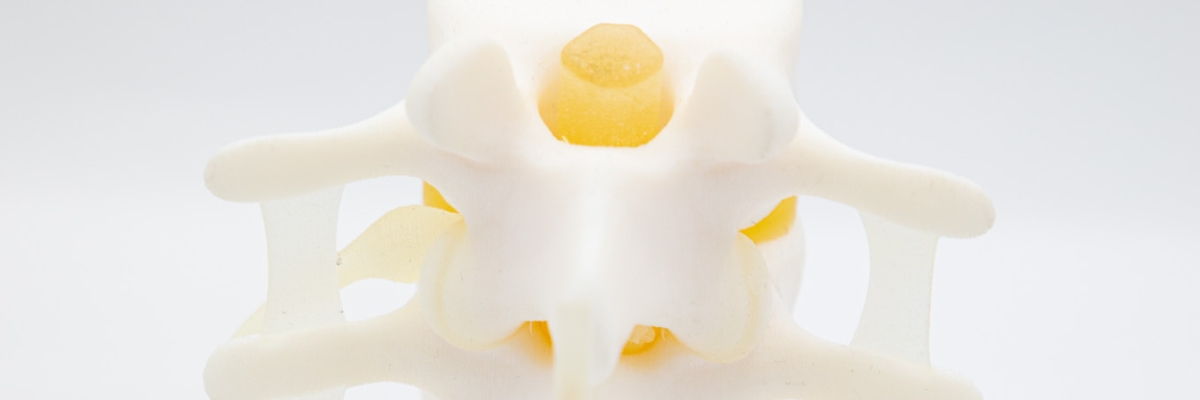
Cost efficiency
When it comes to simple, standardised medical models produced in very high quantities, conventional methods are undoubtedly the more cost-effective option. Additive manufacturing cannot compete with costs between 100 and 300 euros, which continue to fall as quantities increase.
However, when it comes to detailed individual pieces or small series, 3D printing comes out on top. The elimination of lead and changeover times massively reduces the manual labour required, and thus also the costs for this.
What's more, 3D printing stands out for its material efficiency. Whether conventional or additive manufacturing, materials specially designed for medical models are relatively costly compared to standard materials due to their unique properties, which are essential for perfect tactile feedback.
However, while conventional methods generate a lot of material waste, 3D printing is extremely material-efficient, which further reduces costs. These factors mean that even highly complex models that would cost several thousand euros using conventional methods can be produced by in-house 3D printing at a cost of just a few hundred euros.

Tactile feedback
The most important factor in why medical models are produced at all is the tactile feedback, thanks to which the surgeon can simulate the reaction of different types of tissue, bones, organs and more to his or her use of force and movements.
For a long time, 3D printing had the challenge of providing materials that could deliver realistic tactile feedback. As much as time and cost savings and personalisation are welcome, if the models do not react realistically, intensive preoperative planning becomes impossible.
However, this challenge has now been fully met. In particular, Stratasys® Digital Anatomy™ Printing (DAP) materials provide an unprecedented level of realism for 3D-printed medical models.
Not only can these materials be used to simulate soft tissue, bone and organs with patient-specific biomechanical accuracy, but by using PolyJet™ technology, a wide range of materials can be printed simultaneously, allowing properties such as degrees of hardness or elastic modulus to be individually customised for unique tactile feedback. A case study in which the use of these materials could massively simplify surgical preparation can be found here.

Conclusion
The advantages of 3D printing for preoperative planning listed here are just the tip of the iceberg. Among other things, the increased degree of personalisation also improves communication, both in interdisciplinary treatments and between doctor and patient, makes training and further education more realistic, and much more.
If you are already convinced by the advantages mentioned here or would like to learn more about the various possibilities of 3D printing, please feel free to contact our experts, who will be happy to advise you individually on your specific application.
Thank you for your attention – and see you in the next blog post!

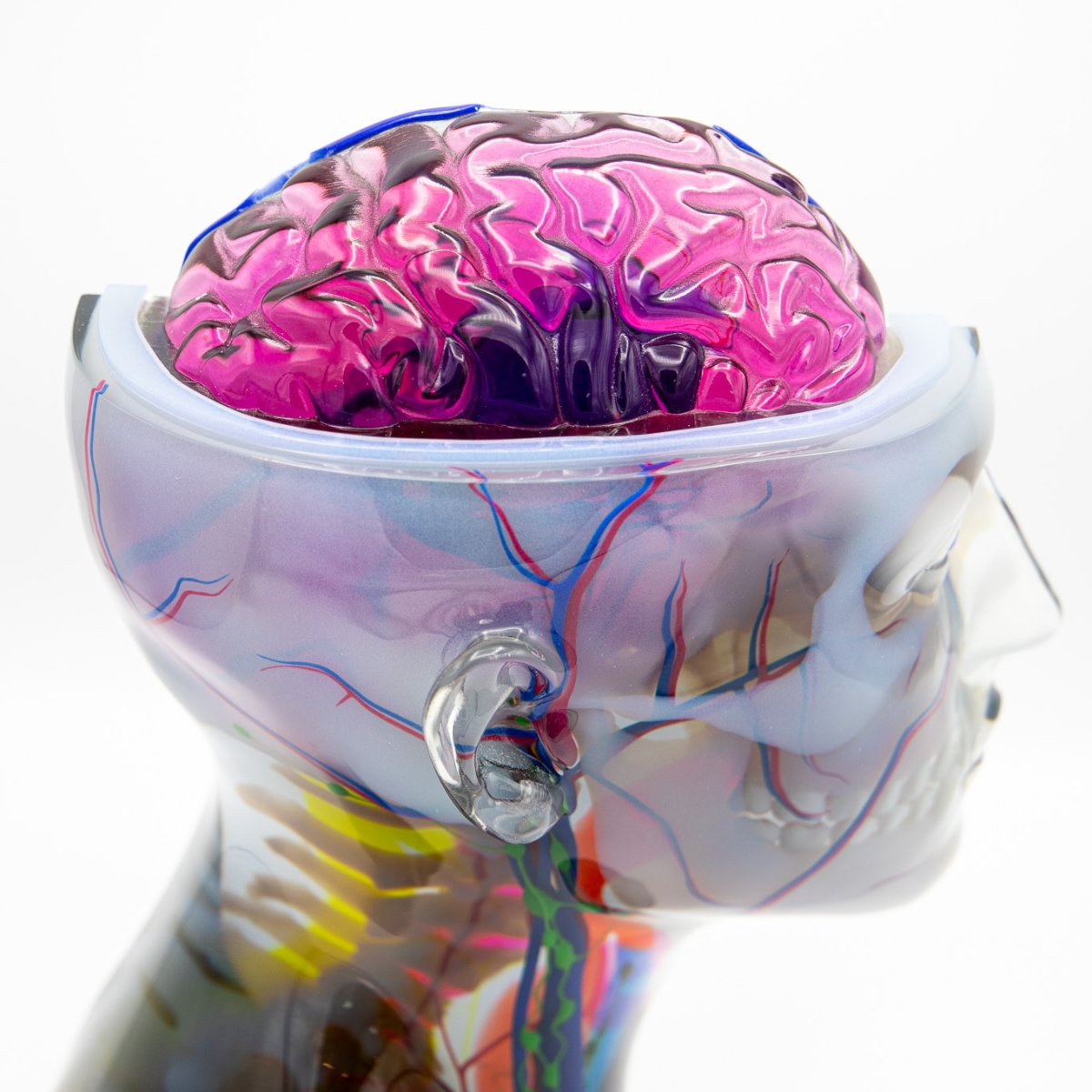

