What is model making in 3D printing?
Model making in 3D printing is the process of employing additive manufacturing technology to make physical representations of items, prototypes, or designs. It entails layer-by-layer converting digital 3D models, which are frequently developed using computer-aided design (CAD) software, into physical three-dimensional objects. This method enables the speedy and exact creation of models with fine details, complicated geometries, and variable degrees of customization across a wide range of industries, including architecture, product design, film, and art. 3D printing in model building has transformed the creative and prototyping processes, allowing for greater efficiency, flexibility, and the ability to create very precise duplicates.
What are the important characteristics to consider when model making?
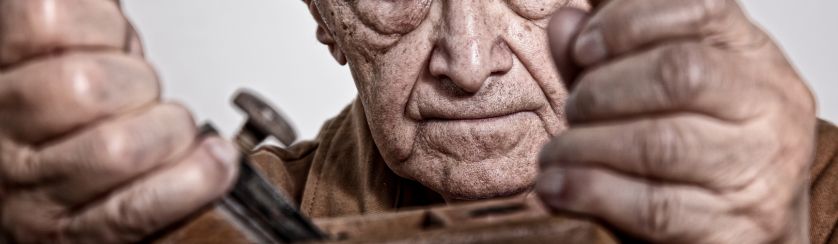
Craftsmanship and Skills
Traditional model making relies heavily on skilled craftsmanship, with artists shaping, carving, or assembling components by hand. The model maker's level of craftsmanship and expertise has a significant impact on the quality and complexity of the finished model.
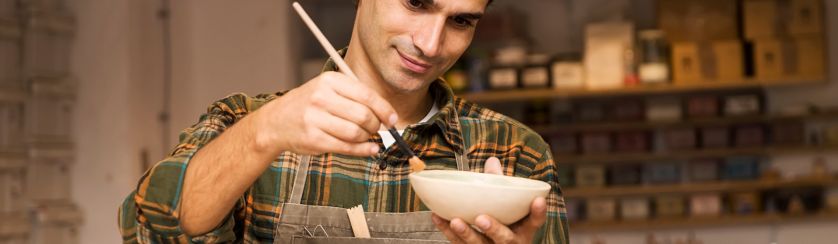
Material and Techniques
The use of appropriate materials and procedures is crucial in traditional model making. The choice of material, whether wood, metal, clay, or other, affects the model's beauty, durability, and functionality. Various techniques, including carving, sculpting, and moulding, add to the overall look.
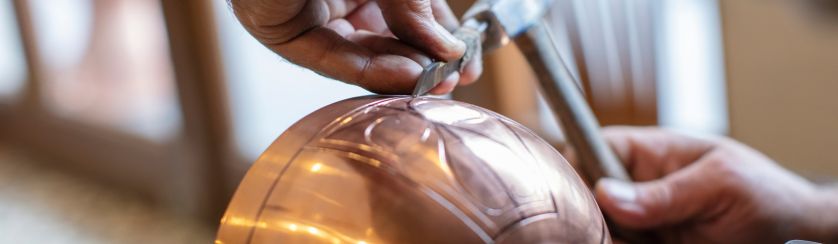
Detail and Finishing
Traditional model making is distinguished by its attention to exquisite detail and careful workmanship. Hand-painting, staining, and other surface treatments improve the model's visual appeal and realism.
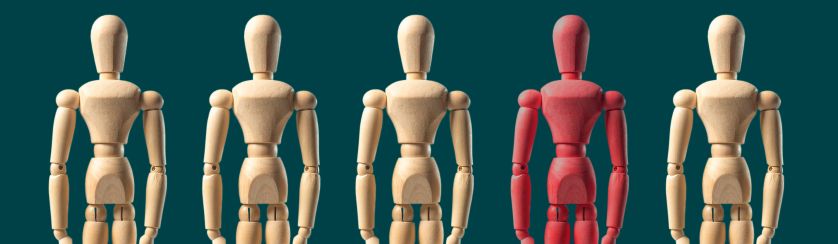
Scale Accuracy
Accurate scaling is critical for models designed to represent real-world items or structures. A faithful representation requires precise measurements and scaling algorithms.
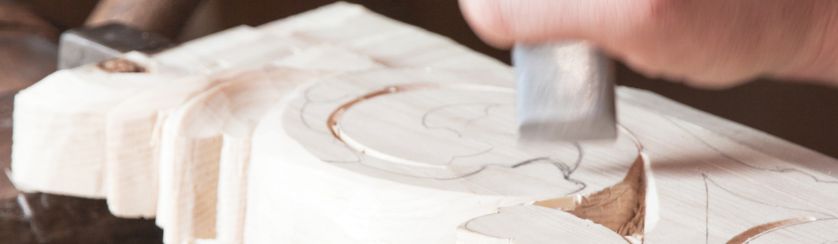
Time-consuming Process
Traditional model making can be time-consuming, especially when elaborate details or complicated patterns are present. The artisanal nature of the procedure frequently necessitates patience and meticulous attention to detail.
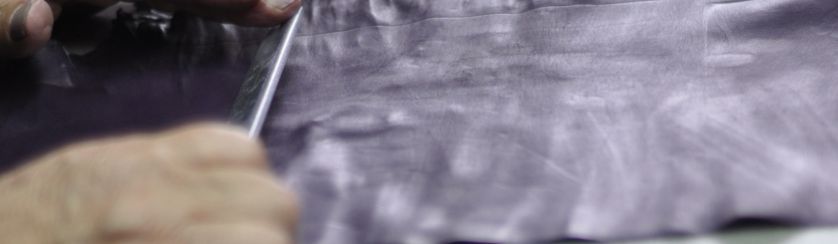
Limited Iteration and Material Constraints
Design iterations in traditional model creation can be difficult and time-consuming and has limited material options. Certain materials may be more difficult to work with or have limits in producing specific forms or details.
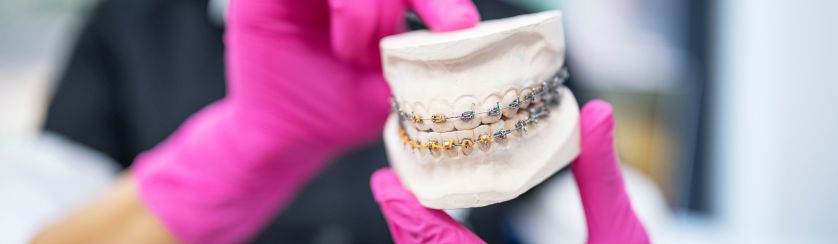
Cost of Materials and Labor
Traditional model making can be costly, both in terms of materials and skilled labour. The cost is determined by the complexity of the design, the techniques used, and the time spent on workmanship.
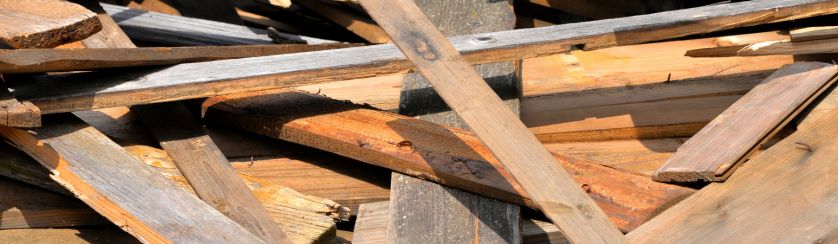
Environmental Impact
Some conventional model-making materials and techniques may have an impact on the environment, such as the usage of specific chemicals or waste disposal. Sustainability considerations are becoming increasingly important in assessing the environmental impact of old approaches.
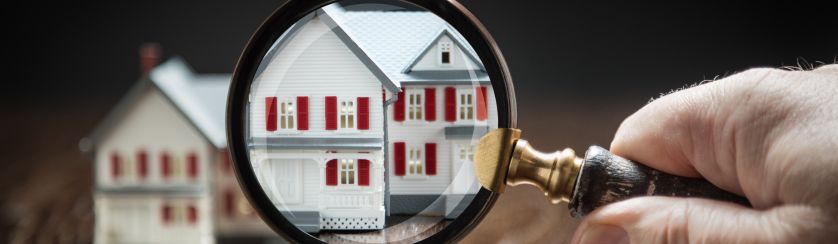
Post-processing Considerations
Sanding, painting, and varnishing are all necessary post-processing stages to get the desired final appearance. These processes may necessitate more time and expertise to carry out correctly.
What are the benefits of 3D printing models?
Precision and Detail
3D printing provides unprecedented precision and intricate detailing capabilities, allowing model makers to build very realistic copies with delicate details. The layer-by-layer additive method ensures that even the most complex geometries are correctly recreated, which improves model quality overall.
Rapid Prototyping
One of the key benefits of 3D printing for model manufacturing is the ability to quickly prototype designs. Traditional methods frequently require time-consuming hand craftsmanship, but 3D printing allows for rapid iterations and modifications. This agility speeds up the design and development phases, lowering time to market for creative ventures.
Material Variety
3D printing works with a wide variety of materials, including plastics and resins, metals, and even composites. This variety of material possibilities allows model makers to select the best material for the individual needs of each project, whether it is for architectural models, product prototypes, or creative works.
What are the applications of 3D printing models?
Architectural Models
Architects and urban planners use this technology to create detailed scale models that accurately reflect their concepts. The capacity to add complex details, geographical aspects, and structural elements improves communication of design concepts to customers and stakeholders.
Product Design and Prototyping
Product designers use 3D printing to prototype and test ideas before mass manufacturing. This enables a more cost-effective and efficient design validation procedure. 3D printing's quick prototype capabilities encourage iterative design cycles, allowing designers to enhance and perfect their products.
Film and Entertainment Industries
3D printing is widely used in the film and entertainment industries to create models for props, sets, and characters. From complex costume pieces to lifelike miniature sets, 3D printing adds to the visual splendour of films and television shows. The technology's ability to create unique and detailed components increases the realism of on-screen creations.
Healthcare and Dental Applications
Medical and dental model creation with 3D printing has become a transformative tool in the healthcare industry, providing novel solutions for surgical planning, training and patient education. Using patient-specific anatomical models created from medical imaging data, surgeons can precisely design complex surgeries, improving precision and lowering surgical risks. Furthermore, these 3D-printed models are essential educational aids, allowing medical personnel to visualise and effectively grasp complex anatomical components. Patient-specific models also help to improve communication with patients by providing a greater understanding of medical conditions and potential therapies.
What materials do we recommend for 3D printing models?
Somos® WaterShed® XC 11122 from Stratasys® - Printed on the Stratasys® Neo®800
Somos® WaterShed® XC 11122 is a popular resin among manufacturers due to its ABS and PBT-like qualities for stereolithography technology. Somos® WaterShed® provides detailed parts with high clarity and water resistance, making them ideal for tooling and moulds.
The robust, clear parts have the look and feel of manufactured plastic, with a smooth finish that speeds up testing.
The Stratasys® Neo®800 is ideal for those who need high-definition parts for their applications. Using the Neo®800 to print the Somos® WaterShed® XC 11122 allows you to quickly produce SD or HD tools and moulds with fine resolution and intricate, small details.
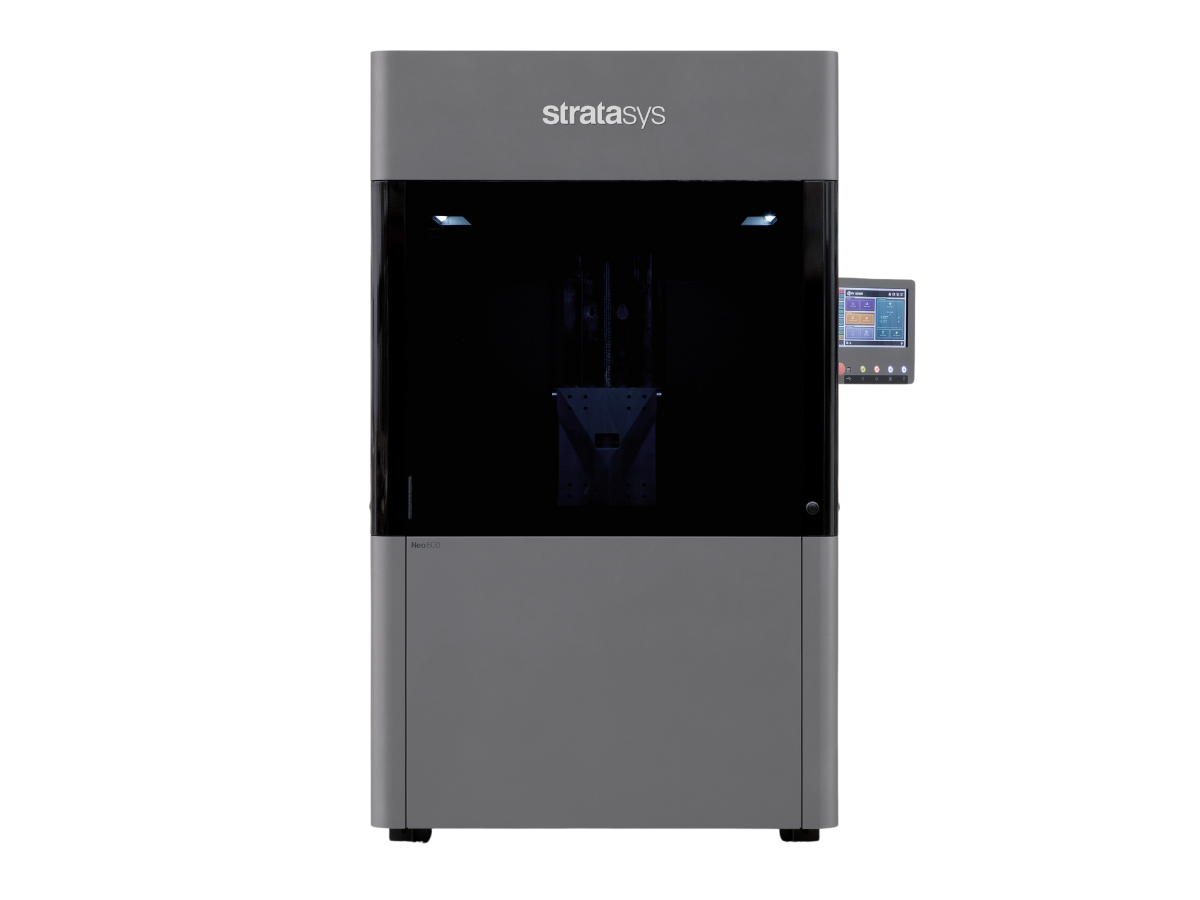
Neo®800
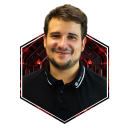
Have your components 3D printed now! Do you have any questions? Contact our experts!
Somos® WaterShed® Black from Stratasys® - Printed on the Stratasys® Neo®800
Somos® WaterShed® Black, a stereolithography resin, has identical qualities and processing to Somos® WaterShed® XC 11122. It produces hard, durable parts in a true black colour without painting.
Somos® WaterShed® Black's enhanced formulation allows for up to 50% faster processing than competing black SL materials, requiring less finishing and providing more uniform processing over time. Somos® WaterShed® Black also has excellent moisture and chemical resistance making it perfect for tools and moulds.
The Stratasys® Neo®800 is ideal for those who need large high-definition parts for their applications. Using such a machine to print the Somos® WaterShed® Black from Stratasys® allows you to quickly produce large-format SD and HD tools and moulds with fine resolution and intricate, small details.
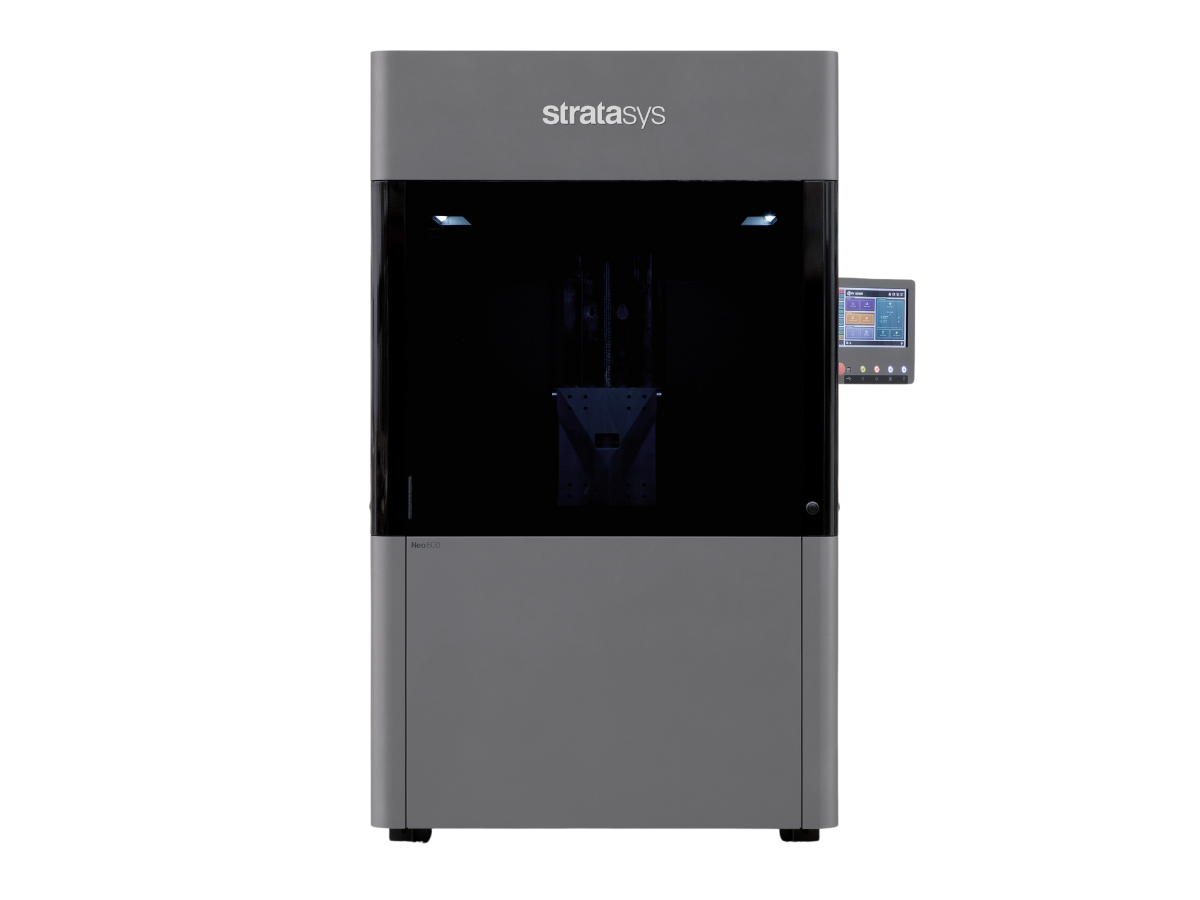
Neo®800
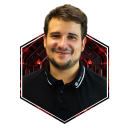
Have your components 3D printed now! Do you have any questions? Contact our experts!
PTG PA12 from ProductionToGo - Printed on the Nexa3D® QLS 820
PTG PA12 is a high-performance polymer with superior detail fineness and surface resolution. It also has excellent mechanical qualities and resistance to a variety of chemicals.
The PTG PA12 can be used for a wide range of tools and moulds and even for medical devices with temporary physical contact.
A variety of printers, including the powder 3D printers of Nexa3D® such as the QLS 230, QLS 236, QLS 260, QLS 820, and the Stratasys® H350, can print this material with precision without the use of supports, allowing you to design complicated structures.
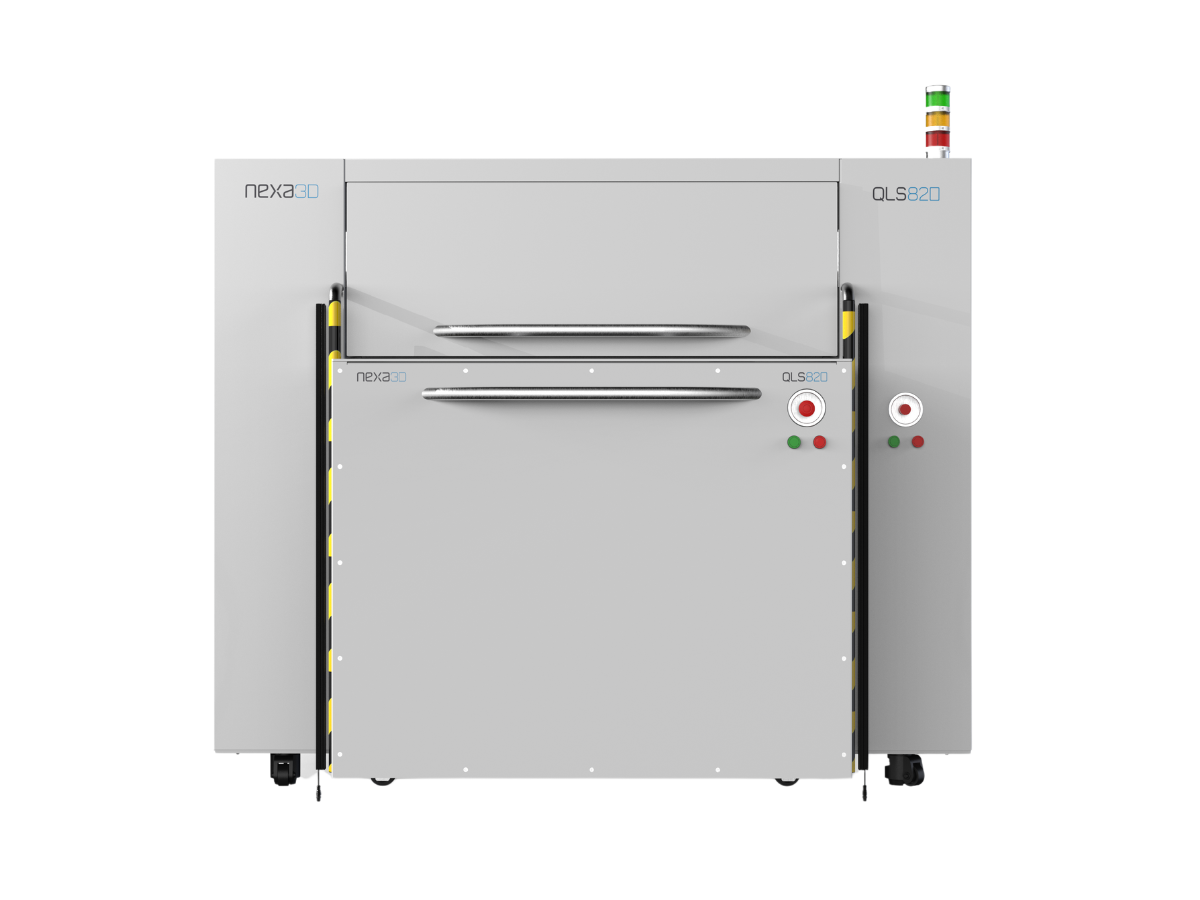
QLS 820
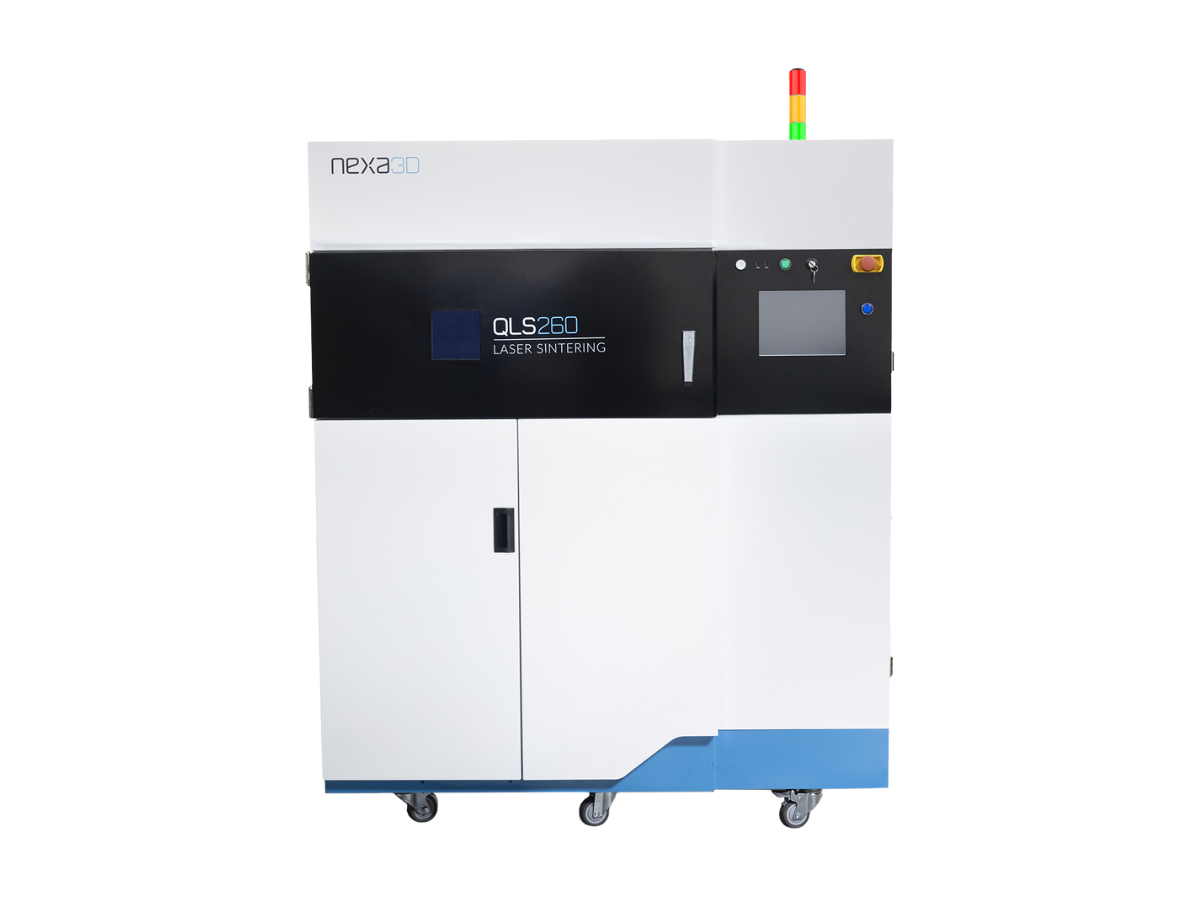
QLS 260
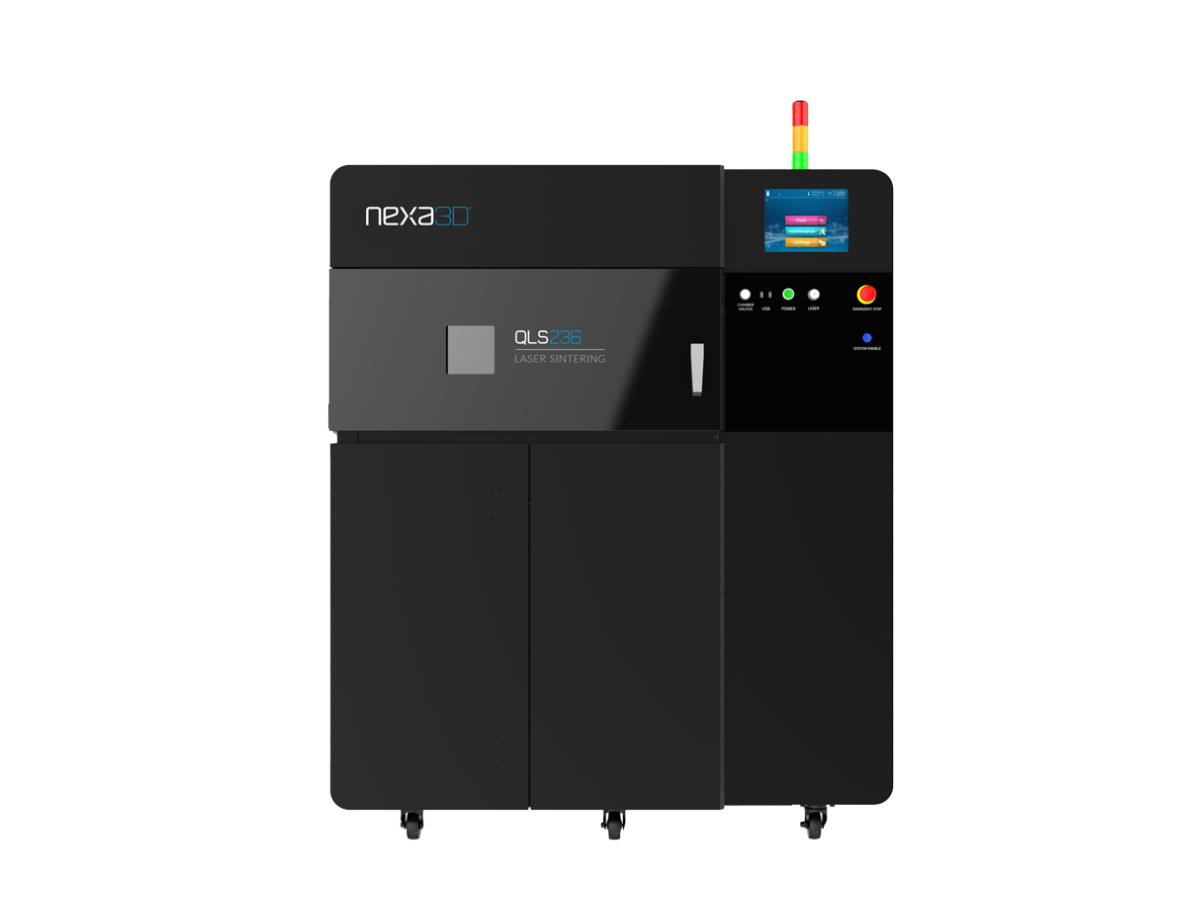
QLS 236
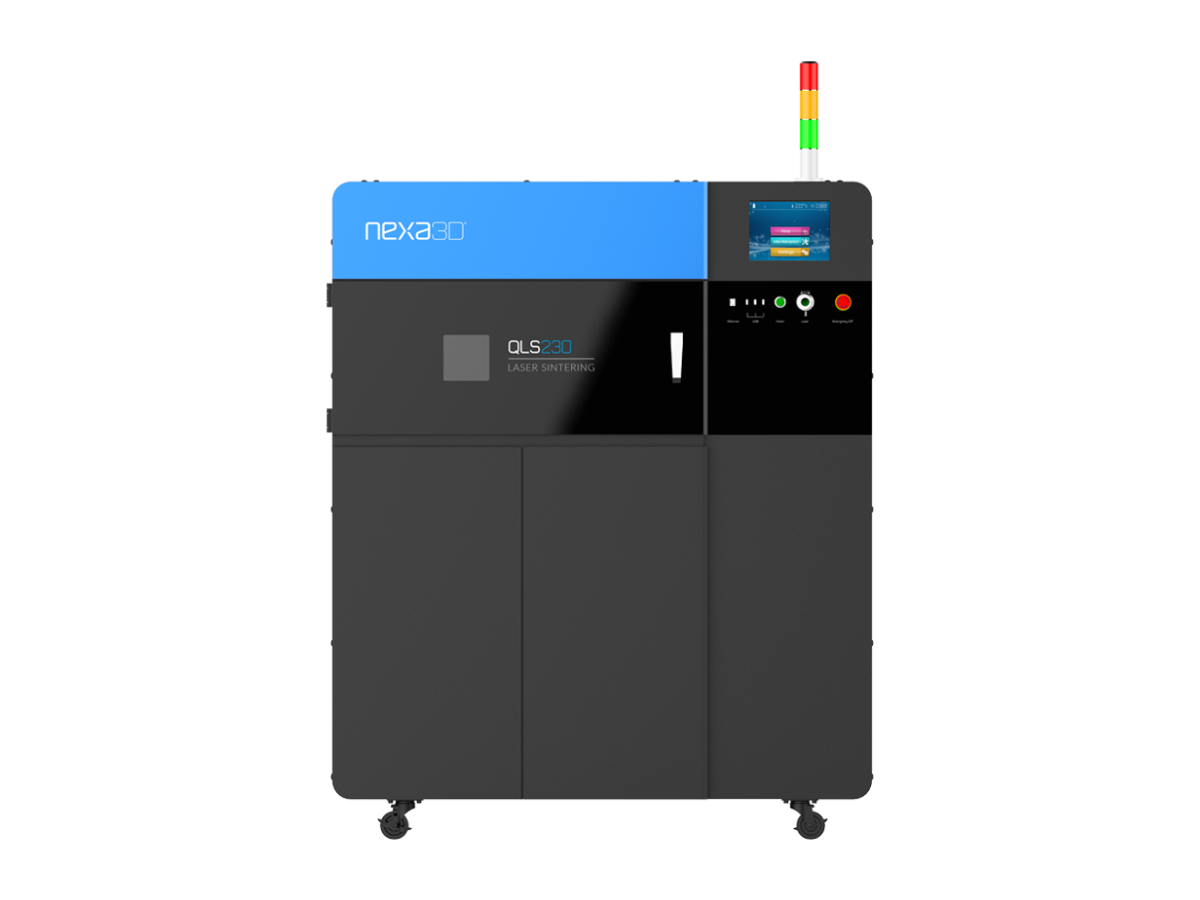
QLS 230
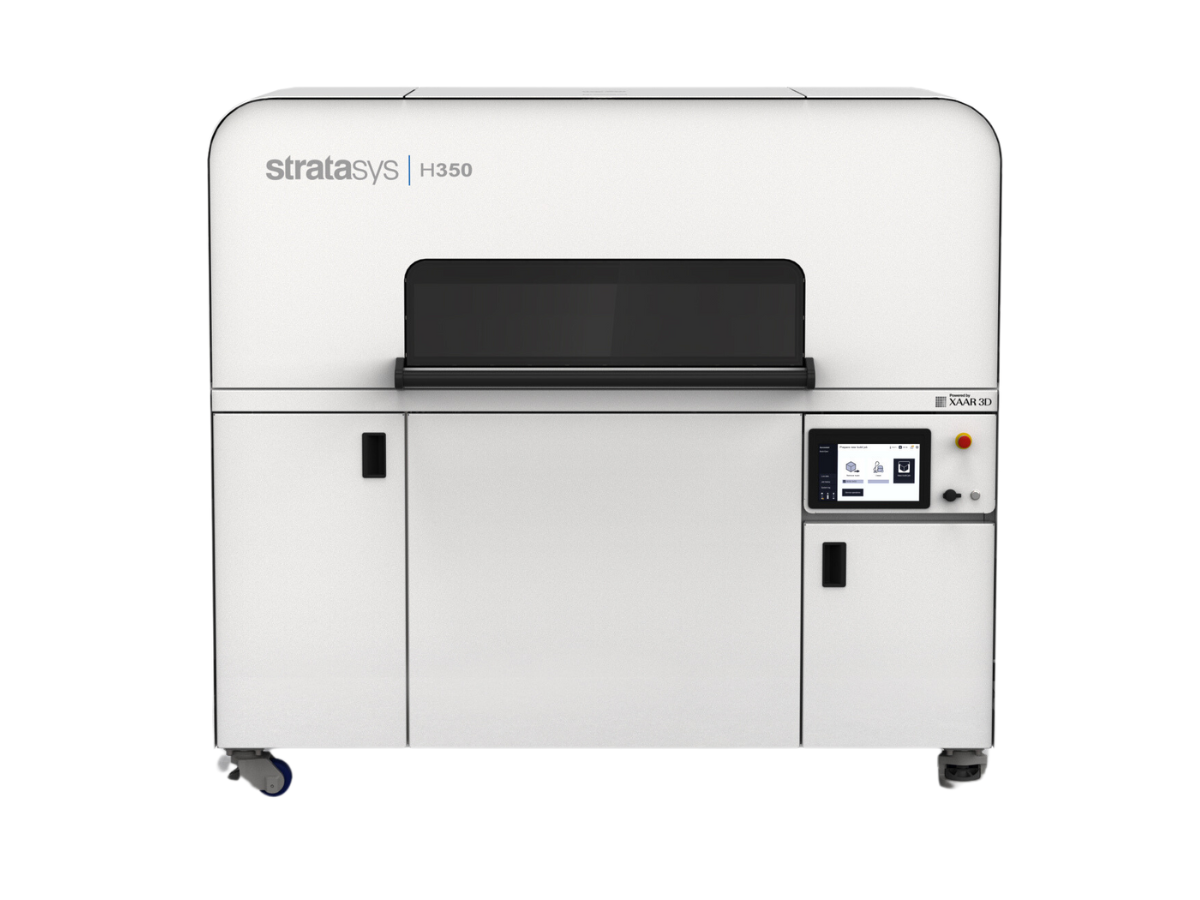
H350™
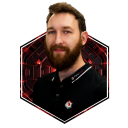
Have your components 3D printed now! Do you have any questions? Contact our experts!
INFINAM® RG 3101 L from Evonik - Printed on the Nexa3D® XiP Pro
INFINAM® RG 3101 L is a black, low-viscosity photopolymer that cures quickly and is very easy to process. The ready-to-use material combines excellent impact strength with high temperature resistance and exhibits long-lasting thermomechanical performance.
This photopolymer can be exposed to strong forces due to its high breaking strength. It can replace some of the engineering plastics produced by traditional processes and is perfect for creating tools and moulds.
The XiP Pro printer from Nexa3D® is one of the ultra-fast resin 3D printers that can utilise the INFINAM® RG 3101 L resin best. The unique LSPc® technology of Nexa3D® allows for the rapid manufacture of models with high resolution in a matter of hours.
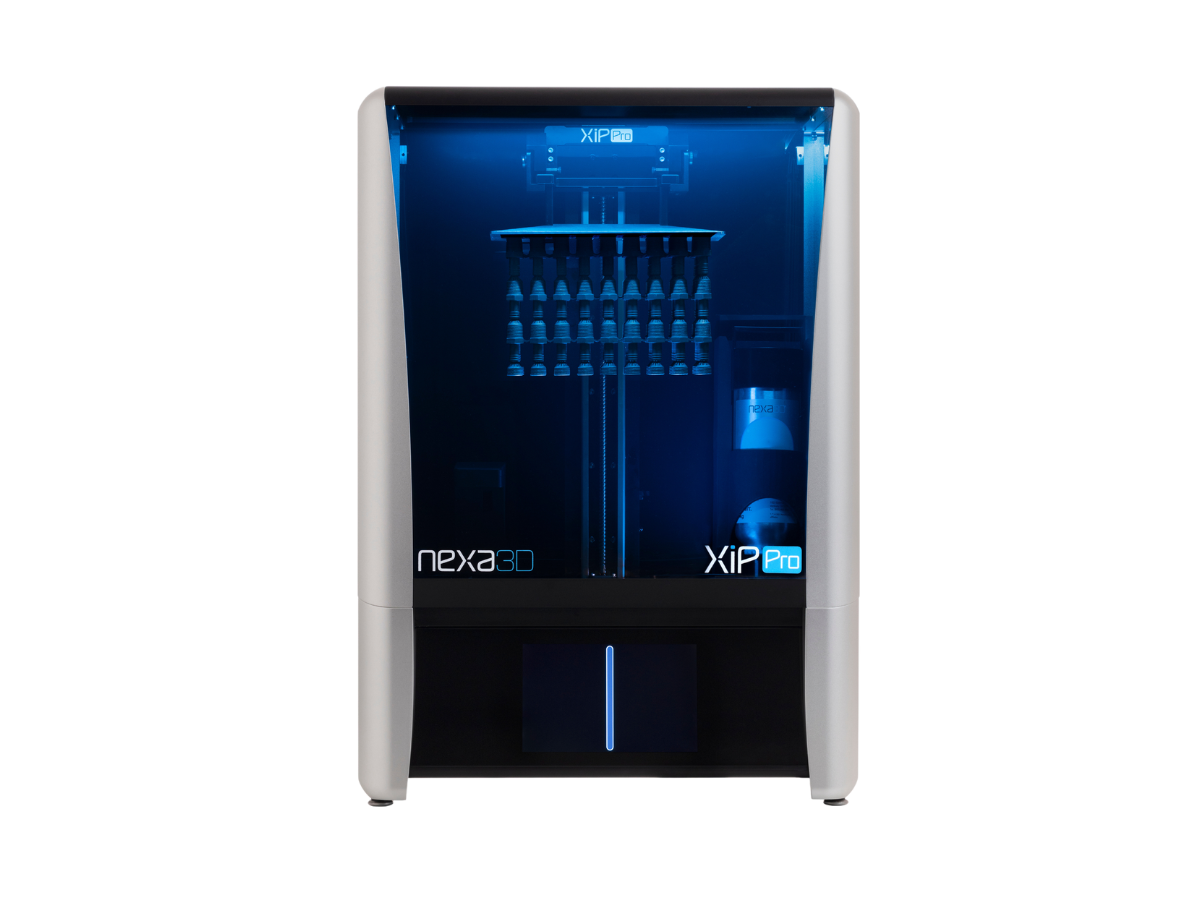
XiP Pro
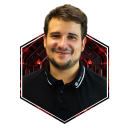
Have your components 3D printed now! Do you have any questions? Contact our experts!
INFINAM® TI 5400 L from Evonik - Printed on the Nexa3D® XiP Pro
Evonik's formulation addresses customer demand for a PVC-like resin for the rapidly expanding market of limited-edition designer toys.
The white material is perfect for things with a high level of detail and outstanding surface quality, which are difficult to distinguish from equivalent injection molded parts. The fully cured material has outstanding impact strength, high elongation at break, and long-lasting thermomechanical performance.
The XiP Pro printer from Nexa3D® is one of the ultra-fast resin 3D printers that can print the INFINAM® TI 5400 L photopolymer. The unique LSPc® technology of Nexa3D® allows for the rapid manufacture of figures and samples with high resolution in a matter of hours.
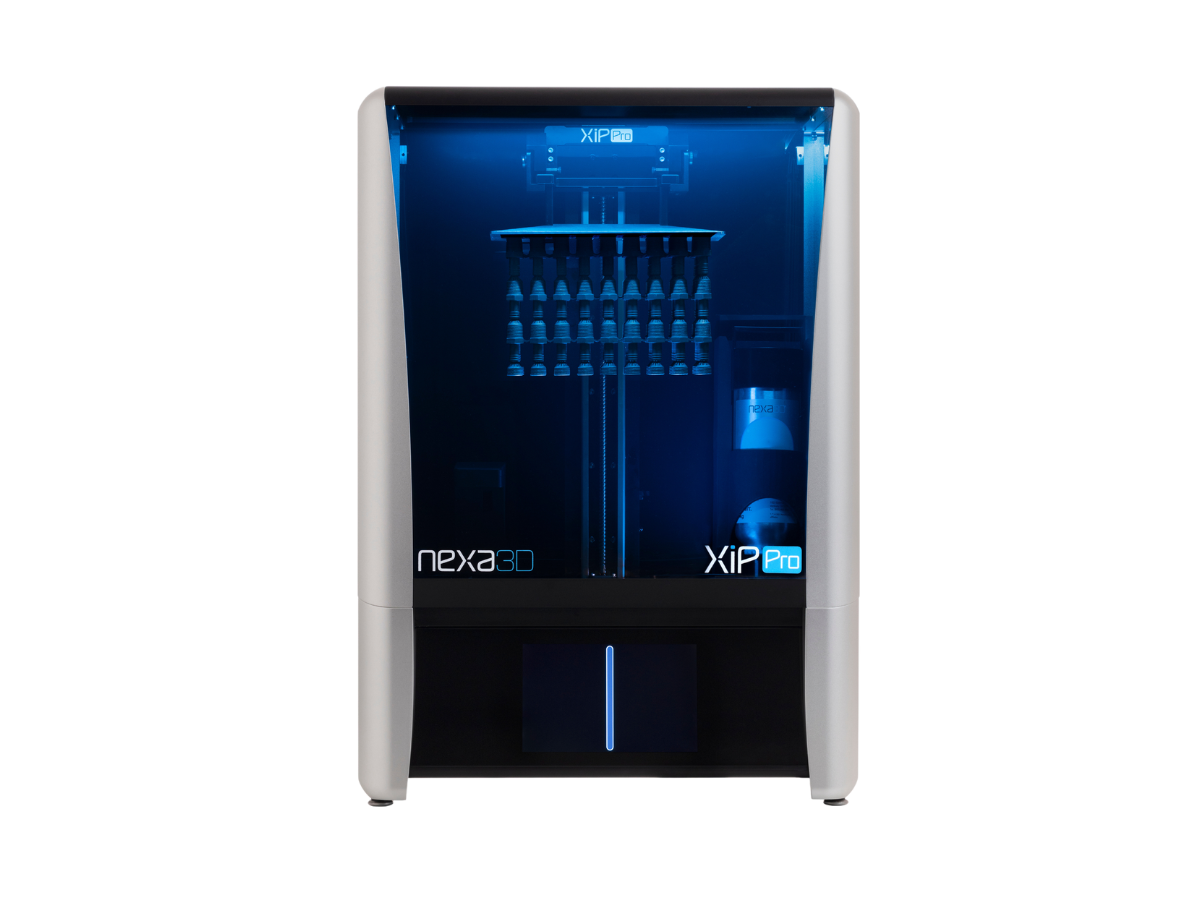
XiP Pro
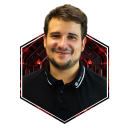