Shipping is one of the oldest industries in the world. At least 40,000 years ago, but most likely much earlier, people were already using the sea route for fishing, migration and trade, and over time a variety of new uses emerged, from warfare to goods transportation and the discovery of undeveloped land areas to passenger shipping.
To this day, this industry is also one of the largest in the world. Every year, around 11 billion tons of goods are transported by ship, there are over 100,000 different ships worldwide and in Germany alone there are almost 3,000 different shipping companies.
However, the production requirements for this gigantic and lucrative industry are extremely high. The components must withstand enormous forces, meet strict safety requirements, be resistant to weathering, corrosion and water - and all these properties must be achieved while the component distributes its weight ideally.
Combining these properties with the best possible weight optimization repeatedly presents traditional production methods with immense challenges. Until now, manufacturers have usually had to choose one of the two sides - but 3D printing makes the symbiosis of the two possible.
In this blog post, we will look at the various applications that 3D printing enables in the maritime industry and the unique benefits that can be achieved thanks to this technology. We will start with the different applications and I will divide them into three sub-areas - starting with military shipping.
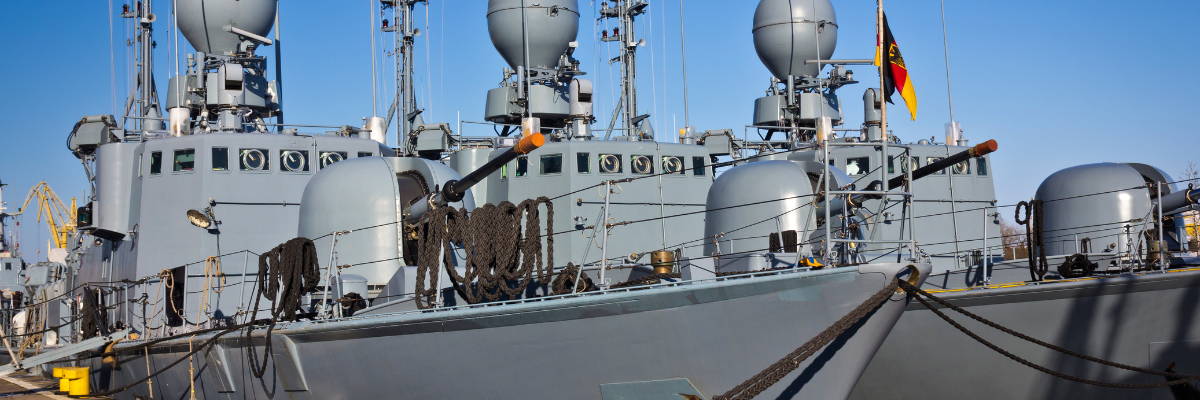
Applications in the military maritime industry
The navy has a military tradition of over 2,000 years and has never lost its importance. From the first recorded naval battle, the Battle of the Nile Delta between ancient Egypt and various maritime peoples, through the Viking Age and the late Middle Ages to modern times, the navy and naval supremacy have played an existential role in warfare.
One of the biggest problems, both in ancient and modern times, has always been the repair of ships damaged in battle - on the one hand in terms of repair capacity, but of course also because every missing ship in the fleet can lead to a loss of essential naval supremacy.
To increase the speed of repairs, the US Navy, for example, relies on additive manufacturing. Since 2022, several warships, including the amphibious assault ships USS Essex (LHD-2), USS Bataan (LHD-5) and USS Wasp (LHD-1), as well as the aircraft carrier USS John C. Stennis (CVN-74) and the submarine USS New Hampshire (SSN-778), have been equipped with their own 3D printers so that they no longer even have to go to port for potential repairs.
For example, in June 2023, the US Navy's USS Bataan was able to avoid a major repair mission due to a faulty air compressor thanks to the 3D printer on board. According to Rear Admiral Jason Lloyd, the procurement of this defective device would normally have taken up to a year and cost up to 400,000 US dollars - but thanks to 3D printers on board, not even a port had to be visited to replace the component.
However, it is not only the ships that benefit from 3D printers on board, but also the soldiers themselves. Several militaries around the world are already using additive manufacturing on the front line to quickly supply soldiers with personalized prostheses and similar indications - and thanks to an onboard 3D printer, the naval forces can also benefit from this in the future.
The US Navy is also relying more and more on 3D printing for the production of end-use parts. The massive 70% reduction in suppliers over the past forty years and the need to replace old ships while simultaneously expanding the navy have presented the Navy with major difficulties for several years.
These production difficulties are particularly noticeable in the case of submarines. Some submarines that have already been ordered are already more than a year behind the targeted completion date and an improvement in the tense situation is not expected until 2028 at the earliest.
In order to alleviate this situation more quickly, many within the US Navy are advocating the more extensive use of additive manufacturing. For example, Rear Admiral Jonathan Rucker, currently head of the Program Executive Office Attack Submarines, responded at a hearing of the Armed Services Subcommittee to the question of whether an expansion of additive manufacturing was necessary: "Absolutely yes, we need additive manufacturing (...) we can't meet the requirements for building the submarines we need and supporting maintenance if we don't move to additive manufacturing."
This statement is supported by the example of a sanitary system valve. The original manufacturer of this valve had to file for bankruptcy and the US Navy expected to wait two years using traditional manufacturing methods. Instead, one of these valves was scanned, 3D printed, subjected to intensive testing and finally installed - all in just six months.
Other examples of 3D printed end-use parts include a drain strainer nozzle on the USS Harry S. Truman aircraft carrier, which was the first 3D printed component ever on a military vessel, and an airflow cover on the USS Kentucky submarine.
These examples are just some of the many areas of application in which 3D printing is used in the navy. Furthermore, additive manufacturing is already being used extensively for prototyping and research applications within the Navy. If you would like a deeper insight into the possibilities of 3D printing across the military, you can find the relevant blog post here.
But another big beneficiary besides the military are private companies in the maritime industry - and we'll get to their applications now.
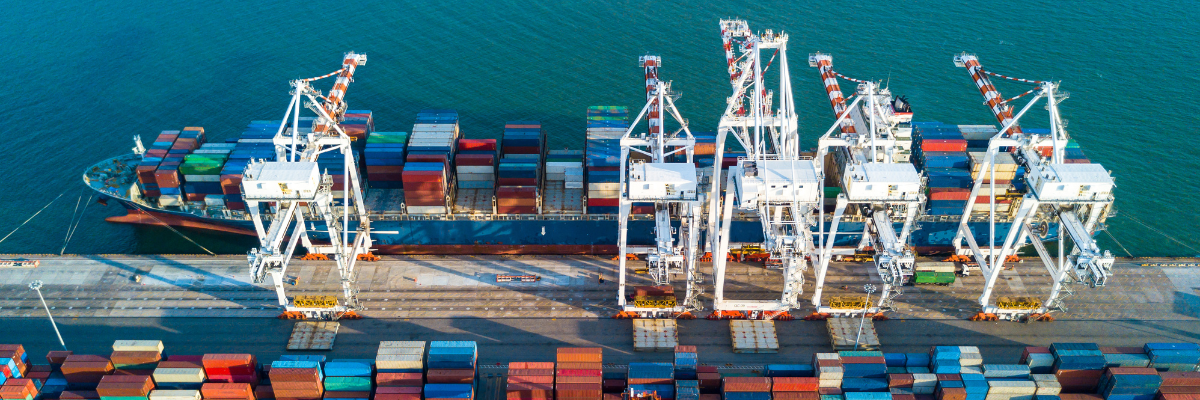
Applications in the commercial maritime industry
Even before shipping was used for military purposes, people had already recognized its value for commercial purposes, especially trade. The first trade routes were established by sea in the Arabian Sea as early as around 300 BC, and maritime trade has been indispensable since the Age of Discovery in the early modern era at the latest.
Even today, despite possibilities such as airplanes, trains, trucks and many others, around 80% of world trade takes place by sea. We were all reminded of this dependency once again in 2021, when the Ever Given blocked the Suez Canal for just over six days, triggering global supply delays and price increases.
However, commercial shipping undoubtedly faces major challenges. The biggest of these is the difficulty of making container ships more climate-friendly. Although the sea route is already far more environmentally friendly than the air trade route, efforts are nevertheless underway to improve the environmental footprint.
3D printing provides massive support for these efforts. An excellent example for the future is Thomas Dahmen's research for his doctoral thesis at the Technical University of Denmark (DTU). He discovered that injection nozzles allow fuel to flow more efficiently if they are curved and implemented these curved nozzles using 3D printing.
This increased efficiency in fuel injection improves the combustion of the fuel and therefore extends the service life of the engine on the one hand and reduces fuel consumption on the other, thereby killing two sustainability birds with one stone.
Additive manufacturing is also the perfect solution for optimizing the weight of ships, which has a major impact on emissions, thanks to the maximized design freedom and the ability to process composite materials with an extraordinary strength-to-weight ratio, for example.
For example, 3D printing makes it possible to print complex assemblies in one piece and minimize or maximize the weight at different points, depending on the weight required on a particular piece to ideally align the metacenter.
However, such weight optimizations not only help with ships, but also with underwater research equipment such as robots or autonomous underwater vehicles (AUVs). The British company ecoSUB, for example, uses 3D printing for its AUVs to produce components that are lightweight yet can withstand the high forces underwater.
And 3D printing as such is already being used commercially underwater. For example, the Norwegian company Kongsberg Ferrotech has equipped its "Nautilus" robot with 3D printing technology to carry out repairs to damaged metal structures at sea depths of up to 1,500 meters, particularly in the oil and gas industry.
Other areas of application for additive manufacturing in the commercial maritime industry once again include prototyping, but also the production of high-quality interior components for passenger ships, such as cruise ships or yachts.
As the last section in the application topic within this blog post, we now come to the private maritime sector, where 3D printing is used on both a large and small scale.
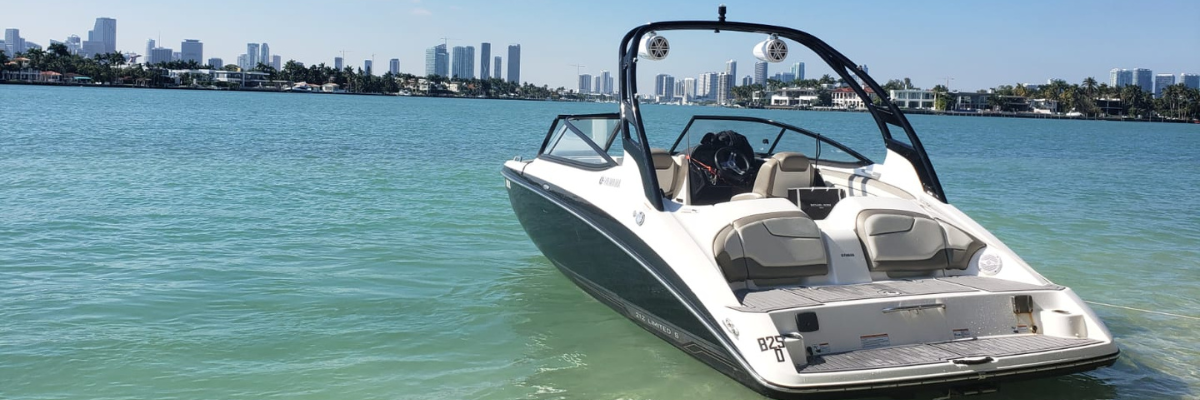
Applications in the private maritime industry
The private maritime industry, which includes yachts, small boats such as sailboats and water sports, is an immense industry. Sales in the small boat market alone amounted to USD 31.23 billion in 2023 and are expected to rise to USD 78.91 billion by 2032, according to Expert Market Research.
However, the current difficult economic conditions coupled with a continuing rise in production costs is also causing problems for this industry - especially for the production of personalized elements, which are becoming increasingly essential for customers worldwide.
Fortunately for this industry, however, additive manufacturing is a master for the fast, cost-effective and individualized production of components - and this has already been recognized by a large number of manufacturers in the private maritime industry.
For example, a number of different manufacturers, such as UK-based Silverlining Furniture, are 3D printing countless customizable types of decorations, furniture, dashboards and more.
But would you like to see larger examples of 3D printing in the private maritime industry? No problem, as the collaboration between Dutch companies KM Yachtbuilders and MX3D impressively demonstrates with a fully 3D-printed aluminum boat keel measuring 4 meters long and 8 meters thick.
Still not impressive enough? How about a fully 3D-printed boat? Dutch supplier Tanaruz, for example, offers its Ozare 6.5, a 6.5-metre-long and 2.1-metre-wide boat that is printed entirely from glass-fiber-reinforced polypropylene. However, the world record for the longest fully 3D-printed boat goes to the University of Maine with its 3Dirigo with a length of 7.6 meters.
Outside of this, additive manufacturing is once again playing a significant role in prototyping in the private sector. For example, the Swedish company Melker of Sweden had to adapt one of its kayaks to the American market, which would have taken tens of thousands of euros and up to two years to prototype. Thanks to 3D printing and recycled materials, however, this prototyping process could be made cheaper, faster - just six months instead of two years - and also more environmentally friendly.
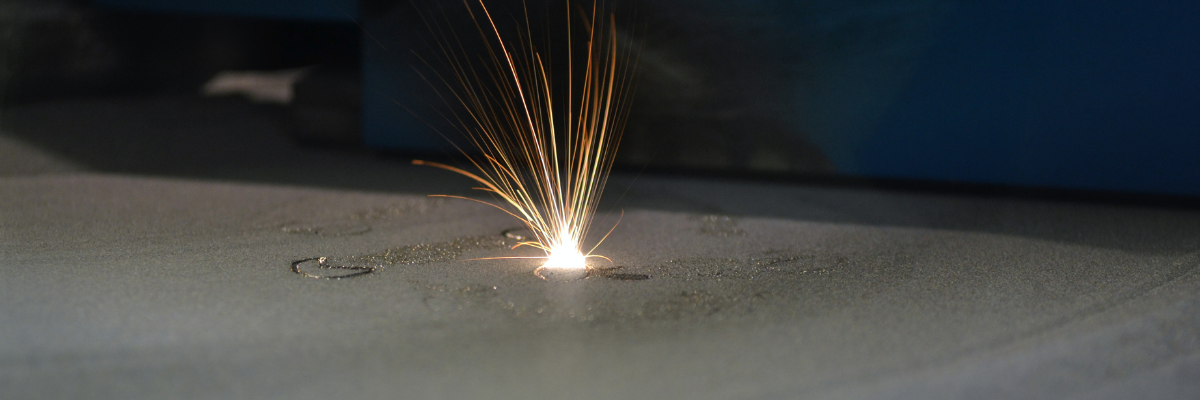
Advantages of 3D printing in the maritime industry
Now that I've outlined some of the exciting applications of 3D printing, let's look at why exactly all the different sub-sectors are relying on additive manufacturing as the tool of the present and future.
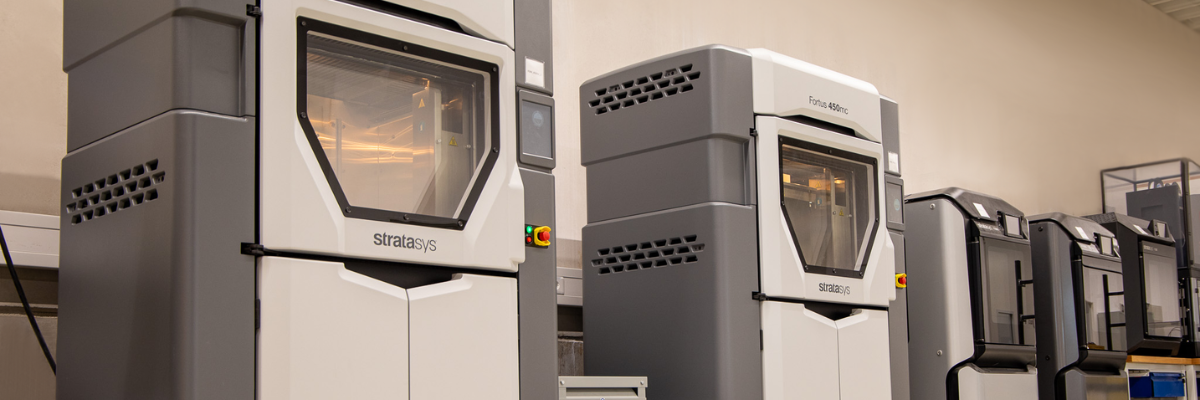
Greater independence
Delivery problems are no longer an exception in the "post-Covid world", but unfortunately the norm. Supply chains around the world are struggling with delays, capacity utilization and total failures - but additive manufacturing makes dependency on other suppliers obsolete.
Whether it's in-house production or using a trusted 3D printing service provider, centralizing the production of ship components gives companies more planning certainty and shorter time-to-market thanks to the ability to produce in-house prototypes and end-use parts.
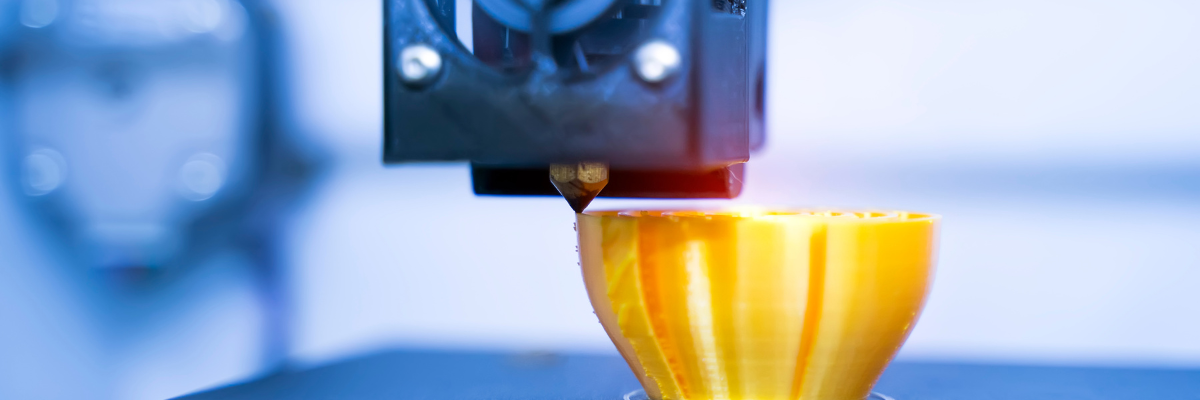
High production speeds
The high speeds that industrial 3D printers can achieve also ensure shorter time-to-market. Particularly in the case of prototypes, where even the smallest adjustments with traditional production methods can take a lot of time, additive manufacturing enables both the adjustment and production of prototypes at maximum speed.
However, the production speeds also provide numerous advantages for end-use parts. The greatest of these is the on-demand production of components, which has already been discussed several times in the areas of application - whether in production halls, ports or even directly on the high seas.
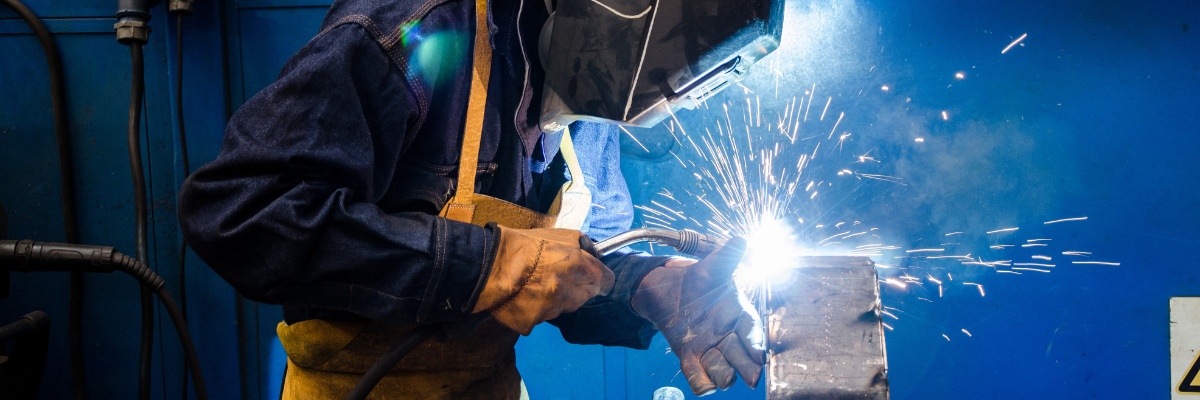
Reduced workload
The omnipresent shortage of skilled workers has not stopped at the maritime industry. Particularly in professions such as metalworkers, mechanics and mechanical engineers, companies are desperately looking for reinforcements - and 3D printing offers these reinforcements, albeit not in human form.
By using additive manufacturing, a variety of manual processes can be automated - or, in the case of using a trusted service provider, completely outsourced. Industrial printing systems are designed for maximum automation and enable continuous printing for up to over one hundred hours without any human interaction, saving massive amounts of labor and costs.
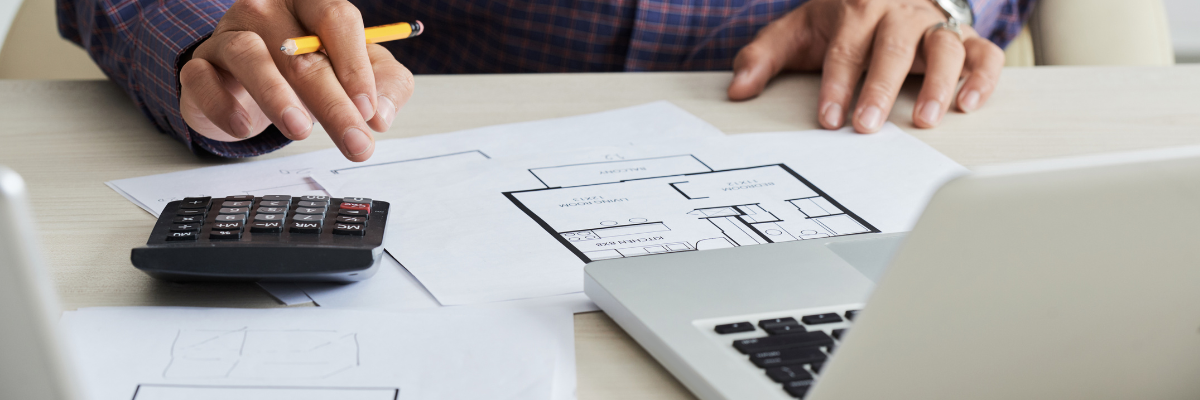
Lower production costs
3D printing can also reduce costs outside of the workforce. Particularly with large components, conventional subtractive manufacturing processes generate huge costs due to material wasted as scrap. However, this problem is minimized with additive manufacturing.
Thanks to the layered structure of components, 3D printing only processes the material that is actually needed for the component. The only waste produced is the thin support structures - and these can even be recycled in powder-based printing technologies to make work even more cost-efficient.
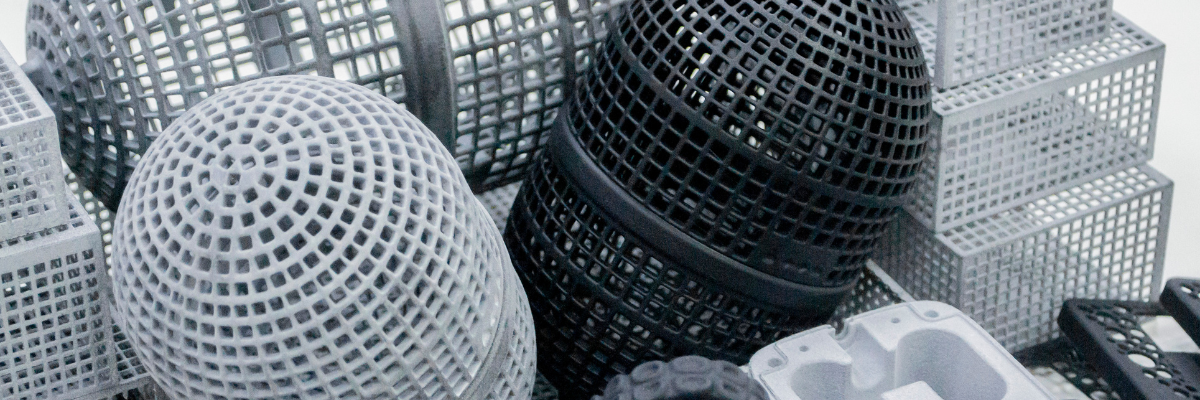
Maximized design freedom
Design freedom plays an essential role in the maritime industry. Whether for weight optimization, personalization, safety enhancement or much more, maximum performance is impossible without design freedom and traditional manufacturing methods can quickly reach their limits, especially with very complex designs.
Additive manufacturing, on the other hand, allows unique freedom in the design and production of even the most complex models. Honeycomb and internal structures, channels, cavities, lattice structures, free-form surfaces and much more become possible with ease thanks to the use of a 3D printer.
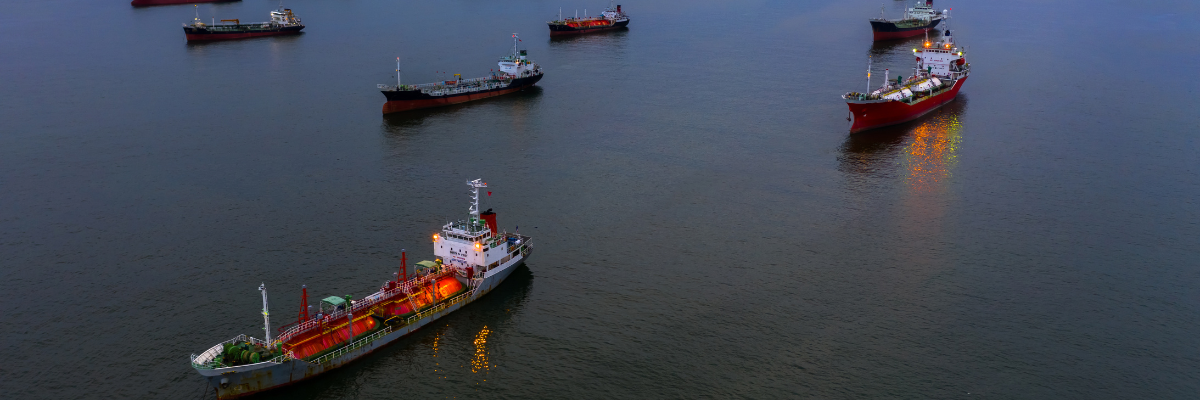
Greater uniformity
Two ships are never identical, even if they belong to the same class, for example. Differences in workmanship, assembly and sometimes high production tolerances in traditional manufacturing processes make every ship unique. What sounds nice at first can lead to major challenges, especially when it comes to repair or maintenance work, as spare parts have to be precisely adapted to these deviations.
In addition to exceptional precision and repeatability, additive manufacturing offers many other factors that can be used to increase uniformity in shipbuilding. From a reduction in the number of manufacturing steps required to a reduction in human interaction to integrated dimensional accuracy control in many industrial systems, 3D printing increases uniformity and thus minimizes many of the known difficulties of the maritime industry.
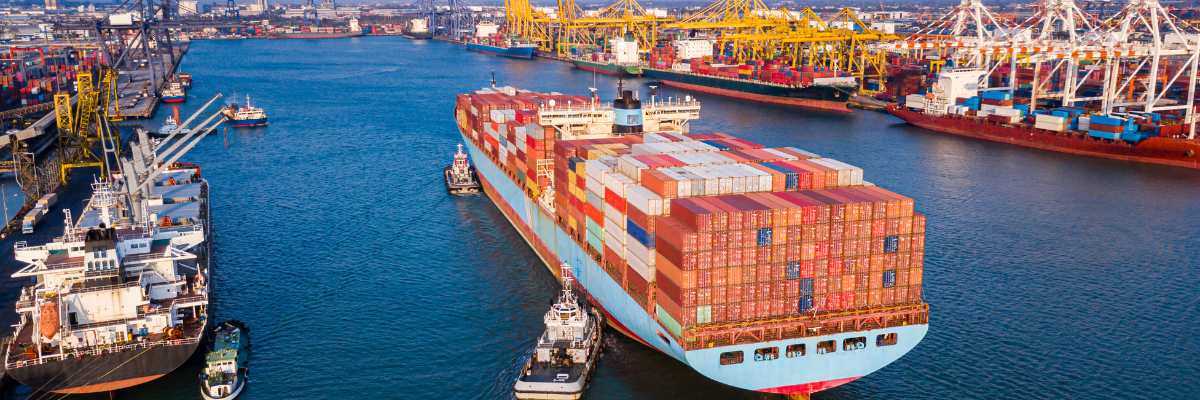
Conclusion
The applications and benefits presented in this blog post are just the tip of the iceberg, but are hopefully enough to show that additive manufacturing is not just beginning to revolutionize the maritime industry, but is already in the middle of the transformation process.
As one of the largest 3D printing service providers in Europe, we at PartsToGo are closely involved in this transformation process. With our expertise, several suitable printing solutions and materials that have passed the stringent IACS E10 tests for salt spray (test no. 12), cold (test no. 11) and flame retardancy (test no. 21), we are the perfect partner for the production of high-quality components for the maritime industry.
If you would like to benefit from us and turn your ideas into reality with maximum efficiency, you can contact us directly using the button below. We will get back to you as soon as possible and clarify all the individualities of your project so that it is implemented exactly according to your ideas!
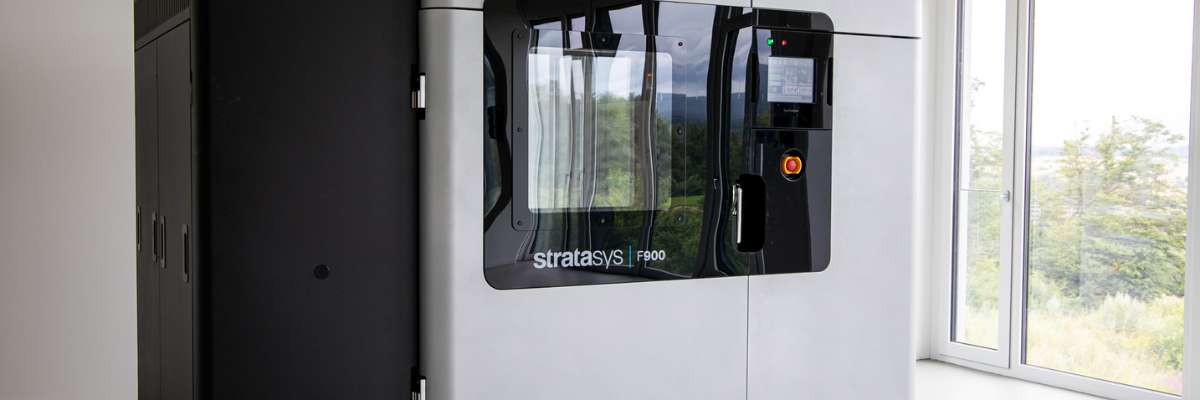
Our ideal solution for the maritime industry
Last but not least, we would like to highlight our ideal solution for the maritime industry, with which many of our projects in this sector are implemented. You can find a complete overview of our solutions and more information about our possibilities on our application page.
When it comes to components in the maritime industry, one of the most common requirements is an exceptional strength-to-weight ratio. There are a few materials available to meet this requirement, but none of them can simultaneously demonstrate IACS E10 certification for salt spray, cold and flame retardancy - except for Stratasys® ULTEM™ 9085 filament.
This filament can be used to print small and large components that can easily withstand the pressure of the sea and at the same time have an excellent heat resistance of up to 176.9 °C. This filament also plays in the Champions League when it comes to smoke development and toxicity.
Of course, such a high-performance thermoplastic also requires a high-performance printer that can process it. For this task, we use the F900 from Stratasys®, which boasts a large build volume, unrivaled consistency and outstanding isotropic properties, among other things.
That brings us to the end of this blog post. Thank you for your attention - and see you in the next blog post!
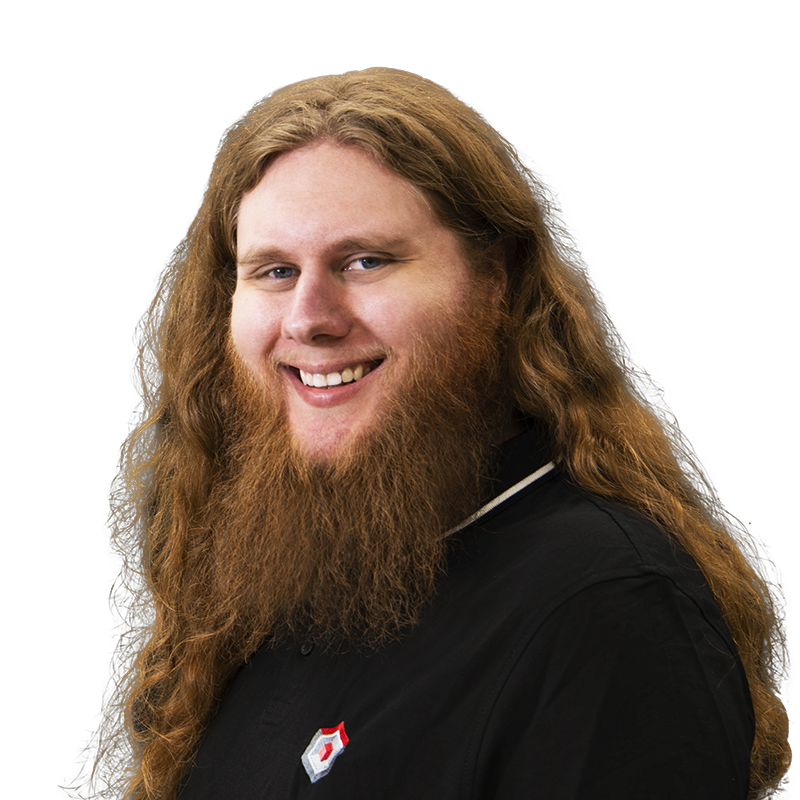