Since the first 3D printing process was filled for patent by Chuck Hull in 1984, this technology has made great progress. In the meantime, countless materials - from ABS and nylon to TPU - can be processed using additive manufacturing, and the areas of application for 3D printing have also multiplied in recent decades.
This expansion of possibilities has been closely linked to the development of new 3D printing processes. And even if this expansion naturally entails a multitude of advantages, it can be difficult to see through the fog of confusion, especially for newcomers to this technology.
It is precisely this fog that this blog post will now clear. Here you will get a brief insight into the most commonly used plastic 3D printing processes, including some advantages and disadvantages as well as a selection of manufacturers who produce 3D printers for this process. I will divide these processes according to the material used - and we will start this overview with the printing processes in resin 3D printing.
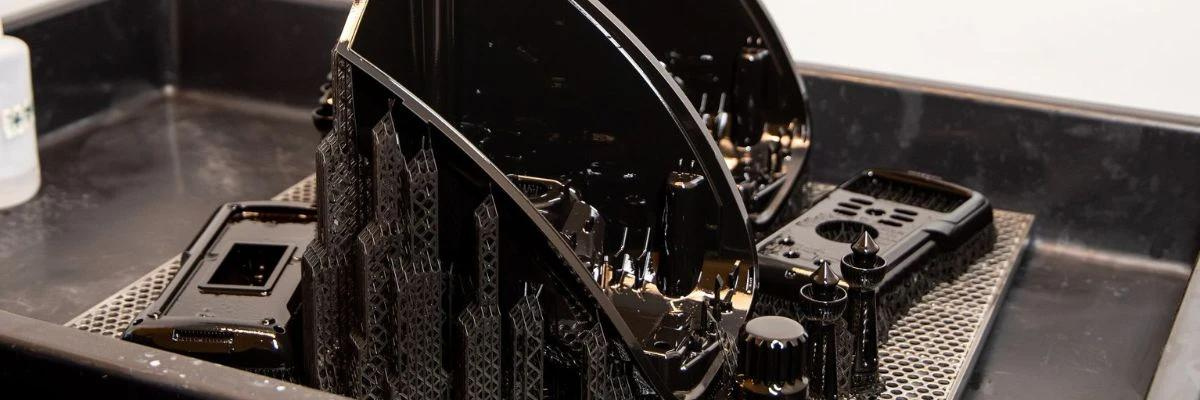
3D printing processes with resin
Some readers may wonder why I'm not starting with the most common type of 3D printing - filament 3D printing. Well, 3D printing with filaments is the best known, but not the oldest way of producing components using additive manufacturing.
This achievement goes to resin 3D printing, or more precisely to stereolithography, which we will discuss in more detail in a moment. But first, how resin 3D printing works in principle.
Liquid epoxy resin is used for 3D printing with resin. This resin hardens when exposed to UV light and is transformed into plastic. As with all types of 3D printing, the component is built up in layers - i.e. one layer is cured, liquid resin is applied to this layer and then also cured.
The vast majority of processes use a movable build plate, which is dipped into the resin and then moves vertically layer by layer. At the end of the printing process, the component must always be washed as there is excess resin on it and, if necessary, post-cured in order to achieve maximum mechanical performance.
As 3D printing with resin is the oldest printing technology, there are also many different processes for it. I will now discuss the most important of these individually - namely stereolithography, digital light processing, masked stereolithography and the PolyJet™ process.
Stereolithography (SLA)
As already mentioned, stereolithography, usually abbreviated as SLA, is the oldest patented 3D printing process. In this process, a tank is completely filled with resin and the build platform is then lowered almost completely to the bottom of the tank so that there is only one layer between the build platform and the bottom.
This layer is then cured using a UV laser that moves from point to point, tracing the geometry of the component. Once this layer is fully cured, the building platform is raised by the height of another layer so that this can also be cured by the laser. This process is then repeated until the entire component has been cured.
Despite its age, this process is still the most widely used type of resin 3D printing today. This is due in particular to the outstanding precision that this process offers. With an accuracy of up to ±0.05 mm, it is ideal for manufacturing assemblies and other applications that require maximum precision.
Another advantage is the exceptional transparency that can be achieved with SLA. The wide range of transparent materials with a variety of additional properties - from biocompatible to heat-resistant - enable maximum transparency for industries such as medical technology or photonics.
However, the comparatively slow printing speed must be mentioned as a disadvantage of this technology. As the laser hardens each dot individually, the process takes a good deal longer on average than with other 3D printing methods. In addition, the entry costs for this process are usually quite high, as there are no desktop printers with SLA processes.
However, there is a wide range of industrial printers from various providers. The best known of these are the Israeli-American company Stratasys® with its Neo® series, as well as the US company 3D Systems®, once founded by Chuck Hull, with the ProJet series, for example.
Digital Light Processing (DLP)
The DLP process actually describes not just a 3D printing process, but a projection technology that is also used in video projectors. This was developed in 1987 by Larry Hornbeck from the US company Texas Instruments.
In the late 1990s, experiments began with the use of this projection technology for additive manufacturing, which ultimately led to EnvisionTEC's Perfactory - the first commercially available DLP printer - in 2002.
In principle, the DLP process is very similar to the SLA process, the difference being the projection technology that gives it its name. Instead of a laser that moves from point to point, the entire resin layer is cured at once by UV light from the DLP projector.
The use of this projector results in a much higher speed than the SLA process. It is of course difficult to make general statements about the exact speed gain, but the DLP process is roughly between 30 and 50 % faster than stereolithography.
Another advantage is the much lower entry-level price of DLP printers. Most desktop resin 3D printers are based on the DLP process, which means that hobbyists can also use resin 3D printing for themselves.
One of the disadvantages of this process is the lower print resolution compared to other resin processes. This stands out with a slightly more pixelated appearance, but usually only when viewed very closely. DLP printers also do not offer oversized construction volumes, as the print resolution would drop significantly from a certain distance from the projector.
Nevertheless, there are of course some industrial DLP solutions and suppliers. The most well-known manufacturers include the French company Prodways with its ProMaker series, the German-American company EnvisionTEC mentioned above, for example with its Envision One, and again Stratasys® with its Origin® One.
Masked Stereolithografie (MSLA)
The MSLA process sits between the SLA and DLP processes and combines several features from both processes. Just like the DLP process, MSLA does not use a laser and, unlike DLP, does not use a projector, but rather an LED light that is selectively directed through an LCD screen onto the areas to be cured.
This process also cures the entire layer at once. However, the rest of the process, i.e. moving the build plate, washing off the component, etc., is identical to the SLA and DLP processes.
This process, developed at the beginning of the 2010s, combines the greatest advantages of the SLA and DLP processes - namely the speed of the DLP process combined with outstanding resolution thanks to the 8K resolution of the LCD screen.
In terms of price, it ranks in the middle of the two processes. As a high-resolution LCD screen is more expensive than a DLP projector, even the desktop versions cannot keep up with the low prices of DLP printers. However, industrial MSLA systems are usually still more affordable than SLA systems.
The only disadvantages that the MSLA process could not avoid in its symbiosis of SLA and DLP are, on the one hand, the still limited construction volumes due to the decreasing print resolution at long distances and, on the other hand, the still somewhat lower print resolution compared to the SLA process.
Even though MSLA is a comparatively new 3D printing process, there are also several providers of industrial printing systems. The best known of these are the US company Nexa3D® with its NXE 400Pro and XiP Pro and tangible engineering GmbH from Stuttgart with the Solidator 8K.
PolyJet™
While all three processes mentioned so far are very similar, the PolyJet™ process developed by the Israeli company Objet Geometries in 1998 stands out. Although it still works with UV light, it no longer uses a resin tank, but classic print heads.
Tiny droplets of resin are applied to the build plate from these print heads, which are immediately cured by the surrounding UV light. The print heads are usually stationary, while the round build platform rotates to enable faster and more consistent printing results.
The benefits of this unique process are many, but the most important is clearly the ability to print multiple materials and colors simultaneously. PolyJet™ machines have between three and eight material channels, allowing multi-material parts to be produced in a single print run rather than having to go through several different production stages.
Another advantage is the very smooth surface finish that can be achieved with PolyJet™. This eliminates potentially lengthy post-processing steps and therefore enables components to be completed more quickly.
To ensure component stability, the PolyJet™ process is unfortunately somewhat limited in terms of height - the maximum print height for currently available PolyJet™ machines is 200 mm. Another disadvantage is the higher acquisition costs, which are still lower than those of SLA machines, but a good deal higher than DLP or MSLA printers.
As PolyJet™ is a patented process from Objet Geometries, which merged with Stratasys® in 2011, there is only one manufacturer for this technology. However, Stratasys® offers machines for various applications, such as the J35™ Pro for prototyping, the DentaJet™ series for the dental industry, the J55 MediJet® for the medical industry and the J850™ Prime for end-use parts.
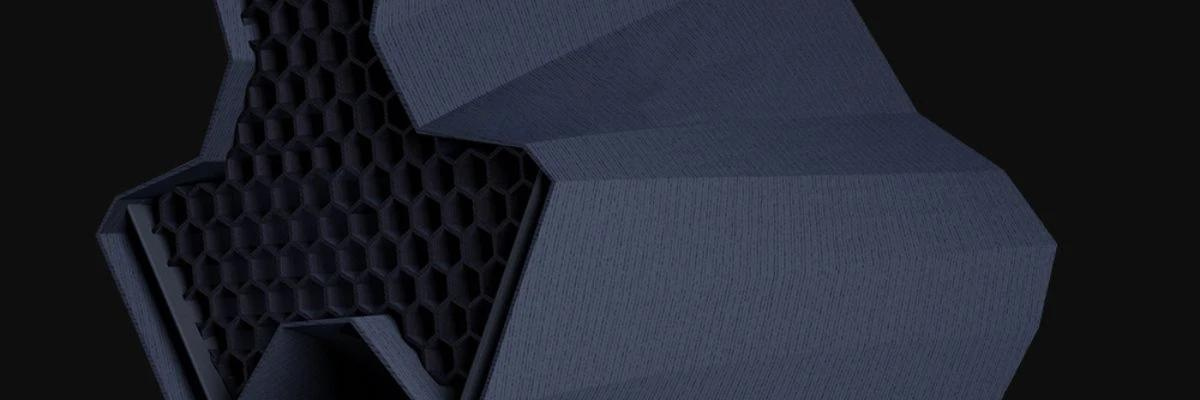
3D printing processes with filament
After the oldest technology within 3D printing, we come to what is clearly the best-known technology - 3D printing with filaments. However, filament 3D printing also has a few years under its belt - the FDM® process was patented in 1988 by Scott Crump, who founded Stratasys® a year later, and commercialized a year later.
Filament 3D printing is basically extrusion-based. This means that filaments are heated above the melting point in the printer and thus liquefied, after which a layer of filament is extruded onto the build plate. Due to the large temperature difference when it hits the build plate, the filament hardens quickly, whereupon the next layer is applied until the component is finished.
The only post-processing that is absolutely necessary with filament 3D printing is the removal of the support structures. Depending on the material, these can simply be removed by hand or with a flush cutter.
In contrast to resin 3D printing, 3D printing with filaments offers far fewer different processes for manufacturing components. The two most important of these are classic fused deposition modeling or fused filament fabrication and the newer fused granular fabrication.
Fused Depostion Modelling (FDM®) / Fused Filament Fabrication (FFF)
The only difference between the FDM® and FFF processes is the name. FDM® is the name patented by Stratasys®, which is why other manufacturers use the name FFF.
This process uses thin plastic threads, the filament that gives the process its name, which is made from classic plastic granulate. The entire process is exactly as described above, i.e. heating the filament, extruding, curing and finally removing the support.
The biggest advantage of this process is its low cost. The acquisition costs of FDM® and FFF printers are undoubtedly the cheapest in all of 3D printing and the material costs are also in the top league in terms of cost efficiency.
In terms of materials, another advantage is the very large selection of different and frequently used materials. From ABS and ASA to PEEK and TPU - FDM® or FFF 3D printing undoubtedly offers the greatest variety of materials.
However, this variety has not yet been able to solve the disadvantage of a rougher surface. For applications that require very smooth surfaces, the surface must always be reworked when using FDM® or FFF 3D printing, which in turn means time and effort. This process also lags behind others in terms of print resolution.
While the last process discussed had only one provider, the FDM® or FFF process is definitely the process with the most providers. Industrial systems are offered by Stratasys® with its F series, Markforged with the FX series and Roboze with the ARGO series, for example.
Fused Granular Fabrication (FGF)
In a more precise sense, the FGF process does not differ from FDM® and FFF in the process itself, but in the material used or the form of material used, because instead of using filament, the plastic granulate, often referred to as “pellets” in 3D printing, is used directly in this process.
These pellets are fed into the printer via a hopper system, where they are melted and then extruded onto the printing plate. Although the inside of the printer differs between the FGF and FDM®/FFF processes, both processes are basically exactly the same.
The first advantage of the FGF process is quickly recognized - namely the reduced material costs, as the pellets do not have to be transformed into filament first. On average, between 30 and 50 percent of material costs can be saved by using pellets.
Another advantage is the ability to print for longer without interruption. Thanks to the pellet form, the required amount of material can be fed directly into the printer, whereas with FDM® and FFF you are chained to the respective spool size and have to keep replacing it. FGF printing is therefore ideal for projects with large volumes in particular.
Unfortunately, however, the material shape also results in a loss of fineness of detail, as more material is extruded at once on average. In addition, the acquisition costs are naturally higher on average, as FGF printing is particularly effective for large-format components.
The variety of suppliers for FGF printing is much smaller than for the FDM®/FFF process due to its more specific field of application, but there are still several printing systems to choose from - including the EXT 1270 Titan Pellet from 3D Systems® and the ARGO 1000 from Roboze.
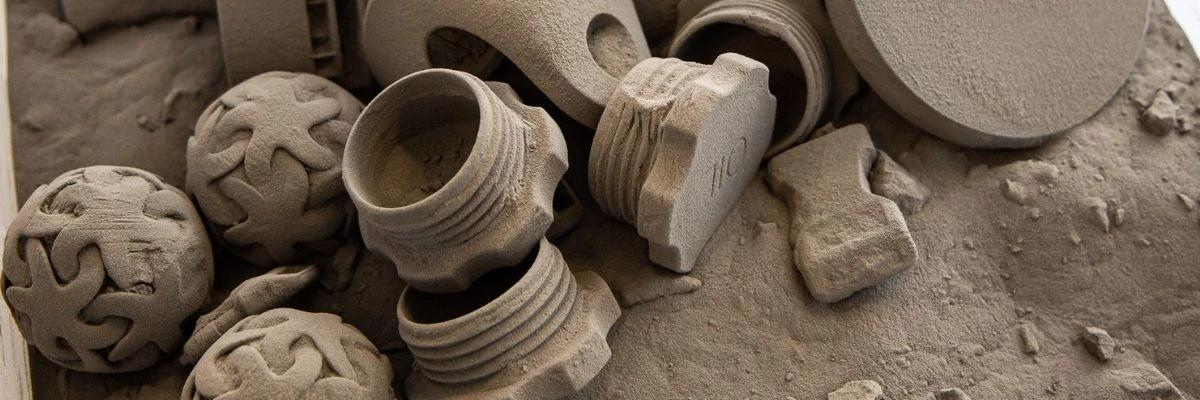
3D printing processes with powder
Last but not least, let's take a look at 3D printing with polymer powders. This process was also developed in the mid-1980s, in particular by Dr. Carl Deckard and Dr. Joe Beaman at the University of Texas, but it was not until 1992 that the first powder 3D printer became available.
In this type of 3D printing, polymer powder is applied layer by layer to a build plate, where it is then fused together in various ways before the next layer of powder is applied and the process continues until the part is complete.
A general advantage of all powder 3D printing processes is the lack of support structures. As the powder is not applied selectively but over the entire build platform, the powder that is not fused together also serves as a support structure. However, this excess powder must of course still be removed from the finished component, which is the only mandatory post-processing for this type of 3D printing.
The possibility of recycling this excess powder is also advantageous for all subsequent printing processes. After a short screening process, this powder can simply be reused with the addition of a certain percentage of new powder, which means that no material is wasted.
The main processes within this type of 3D printing are Selective Laser Sintering, which is the original powder-based 3D printing process, and Selective Absorption Fusion, developed by Stratasys®.
Selective laser sintering (SLS)
As the name suggests, the SLS process uses a laser to fuse the powder. A CO2 or infrared laser is usually used in order to have enough power to fuse the individual powder grains.
However, before this laser is used, the powder is heated to just below the melting point inside the printer. This heated powder is then scattered onto the build plate, whereupon the laser selectively melts together the areas required for the component.
As soon as the first layer has been sintered, the build plate is moved down the thickness of one layer, after which a new layer of powder is applied. As before, this process is repeated until the component is finished. The build plate is then removed, cooled, excess powder is removed from the component and, if necessary, further post-processing steps are added.
In addition to the general advantages of powder 3D printing mentioned above, the SLS process also offers its own advantages. These include the very large selection of materials. SLS powders come in a wide range of properties - from PP and TPU to a variety of polyamides such as PA6 or PA12, optionally also with glass bead or carbon fiber reinforcement.
Another advantage in contrast to the subsequent 3D printing processes is the entry-level price. SLS is now also available in a smaller format, with the Polish manufacturer Sinterit in particular offering several affordable desktop SLS printers.
However, SLS printing is also one of the slower variants of powder 3D printing. Similar to SLA, this is due to the laser, which has to move from point to point and therefore naturally requires much more time to fuse a layer. The surface, which is always somewhat rougher with powder components, also lags behind other powder processes with SLS.
The variety of suppliers for this process is quite high due to its age. For the industrial sector, 3D Systems® with its SLS 380, Nexa3D® with its QLS series and EOS GmbH with its P series, among others, offer ideal printing solutions.
Selective Absorption Fusion (SAF™)
The SAF™ process is based on the HSS process (High Speed Sintering), which was developed in the early 2000s but remained in the prototype phase for a long time, was further developed by Stratasys® into the SAF™ process in 2021 and was also launched on the market in 2022 with the H350.
This process does not use a laser, but melts the powder using a liquid and infrared heat. The liquid, known as High Absorption Fluid (HAF™), is applied to the powder, which, unlike the SLS process, is not heated, after which the heat source is applied. The HAF™ now absorbs far more of this heat and thus melts the surrounding powder evenly and precisely. The downstream process steps are identical to the SLS process.
Among other things, this process boasts a much improved printing speed. By fusing an entire layer at once, speed gains of up to 50% can be achieved compared to conventional SLS.
Another major advantage is the highest packing density on the market with the SAF™ process. On average, a packing density of up to 40% is possible, in certain cases even up to 50%, which massively increases the throughput of the 3D printer.
One disadvantage, however, is the very limited choice of materials. Stratasys® currently (June 2024) only offers two materials and the process is not designed for third-party materials. In addition, components printed with SAF™ always have a gray tint, which can be unsuitable for certain applications.
There is currently only one manufacturer for the SAF™ process, namely Stratasys®. There is also only one printer to date that uses this process, namely the H350, which means that the choice is clearly the smallest for this process. To be fair, however, the process is also clearly the most recent.
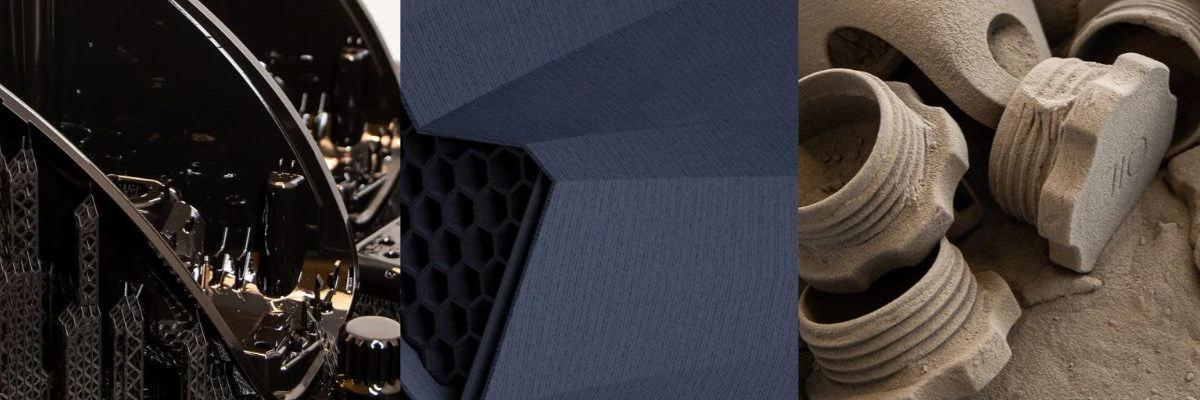
Conclusion
As has become clear in this blog post, the variety of 3D printing processes is enormous - even though I have only explained the most important processes here. Nevertheless, I hope that I have been able to shed some light on the subject with this blog post.
If you are explicitly interested in one of these processes, we at PartsToGo are the ideal contact for you. Thanks to our large printer portfolio and a large number of in-house experts, we can work with you to find the ideal solution for your requirements!
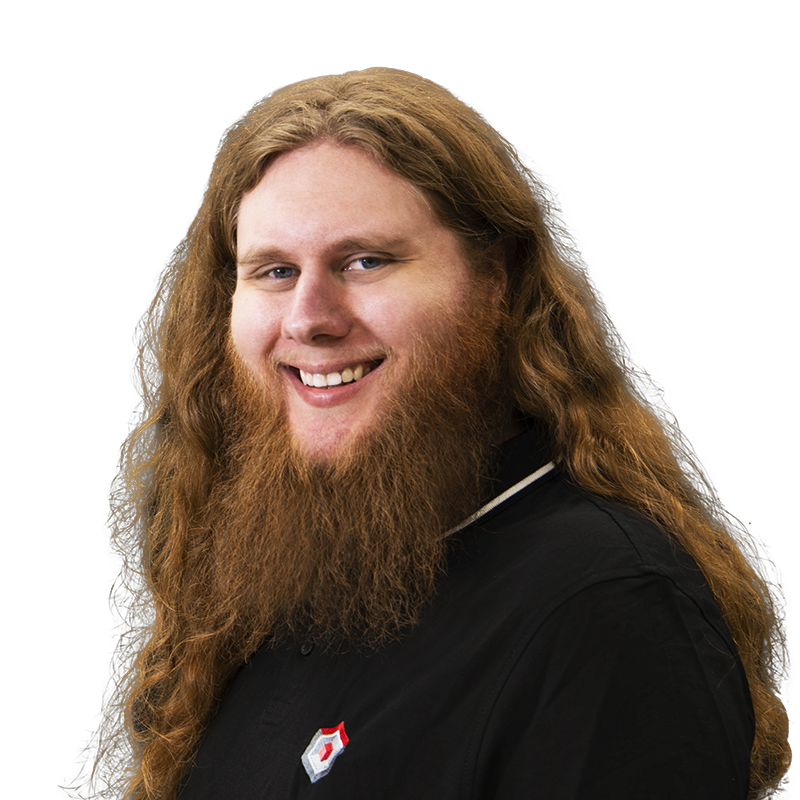