Even though SAF™ technology is one of the newest 3D printing technologies on the market and in our portfolio, it has undoubtedly already become one of the most widely used printing processes for our customers and partners.
There are many reasons for this. The most important of these are the excellent printing efficiency thanks to the market-leading nesting density, the material and thus cost savings achieved through the Big Wave™ powder management system, and exceptional precision and repeatability.
However, when it comes to many jobs, the question arises as to what the post-processing looks like with this technology. Are the steps more laborious than with other powder processes? Can the same or even better results be achieved than with other powder-based processes?
This blog post is intended to answer these and other questions. We will first discuss our post-processing procedure and the various options we offer our partners and customers, and finally compare the results with other powder-based processes, specifically Selective Laser Sintering (SLS).
Our process for reworking SAF™ components
The process for post-processing SAF™ components consists of several steps, some of which are optional. However, two of the steps are essential for every SAF™ component, regardless of its geometry and requirements, and we will cover these first.
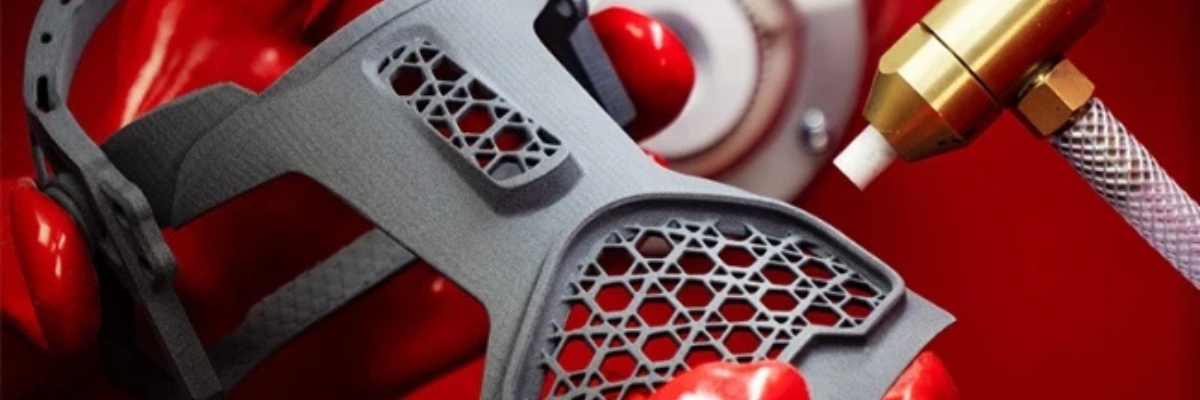
Depowdering / Air-blasting
A major advantage of all powder-based printing processes is that no supporting structures are required, since the unused powder automatically takes on the function of a support during the printing process. When the component comes out of the printer, it is therefore embedded in a block of powder – and the component must, of course, be freed from it.
This depowdering is often simply done manually, since most of the powder is not firmly attached to the component and is therefore easy to remove. However, this only works for very simple geometries. We, on the other hand, use a station specially designed for depowdering, which is equipped with a compressed air blasting system.
Air blasting not only removes the powder faster, more easily and with greater depth effect, but also allows complex structures to be gently freed of excess powder. Air blasting is particularly useful for cavities, holes or channels, as it can efficiently remove the powder from these structures.
The entire process of de-powdering or air-blasting takes between twenty and thirty minutes, depending on the size and geometry of the component. After this time, the majority of the component is free of excess powder, which is then processed in our recycling station and can be reused for another printing job.
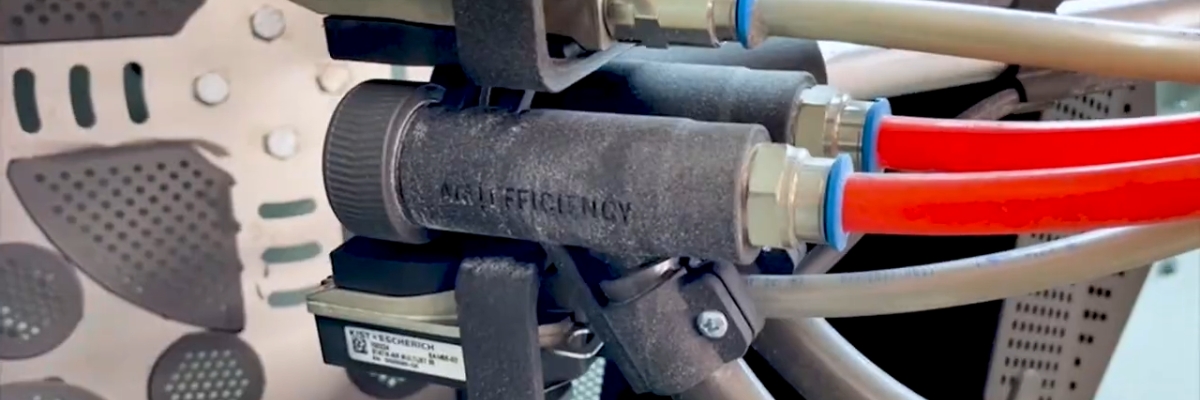
Sandblasting
In the second and theoretically final essential step, the focus is on removing excess powder, namely the last, often sticky residues, on the one hand, and on improving the surface quality, especially smoothing out unevenness, on the other.
This step is done by sandblasting. For this, we either use manual sandblasting in a sandblasting chamber specially designed for 3D printing or automated sandblasting using the CCP systems from AM Efficiency.
The decision between these two processes depends particularly on the complexity of the component. In particular, components with particularly thin structures could suffer damage during automated sandblasting, which is why we always prefer safety here.
But even when it comes to components with sharp edges, complex cavities, blind holes or deep bores, manual sandblasting is preferable, as it allows us to ensure that all excess powder is completely removed.
And last but not least, the number of components must also be taken into account when making this decision, since the automated option, in contrast to manual sandblasting, always takes the same time, between 30 and 60 minutes depending on the mode, for sandblasting.
However, we often combine both methods to automate the improvement of the surface quality and then manually remove any residual powder. We can offer a wide range of blasting media for surface smoothing to precisely meet our customers' requirements.
Now the components are completely free of excess powder and have a uniform surface. This concludes the mandatory post-processing steps, although one property is still changed in many cases – namely, the color.
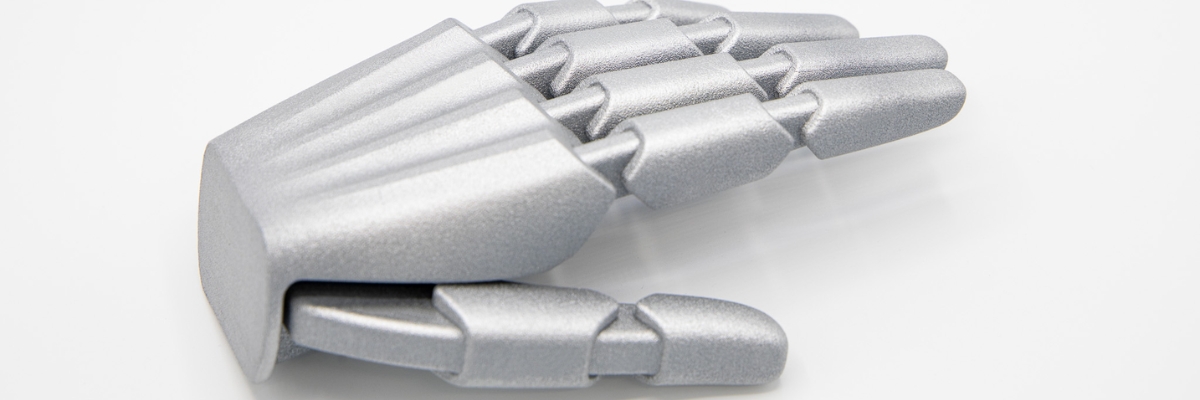
Coloring
SAF™ components are gray in color from the ground up. This is because only darker colors can be used for the printing process. This color scheme does not pose a problem for functional prototypes, but when it comes to end-user products, colors other than pure gray are usually desired.
However, the main advantage of the gray base color is that it can be dyed using a variety of methods. Both lighter and darker colors are possible, with dark colors in particular, such as black, looking particularly good on SAF™ components.
The various coloring options in our portfolio are far too diverse to list here. The specific decision depends once again on the complexity and required surface finish.
Due to the highly customized nature of this process, it is almost impossible to determine the time required in general. Depending on the complexity, size, process used and desired color, the process can take five minutes or several hours.
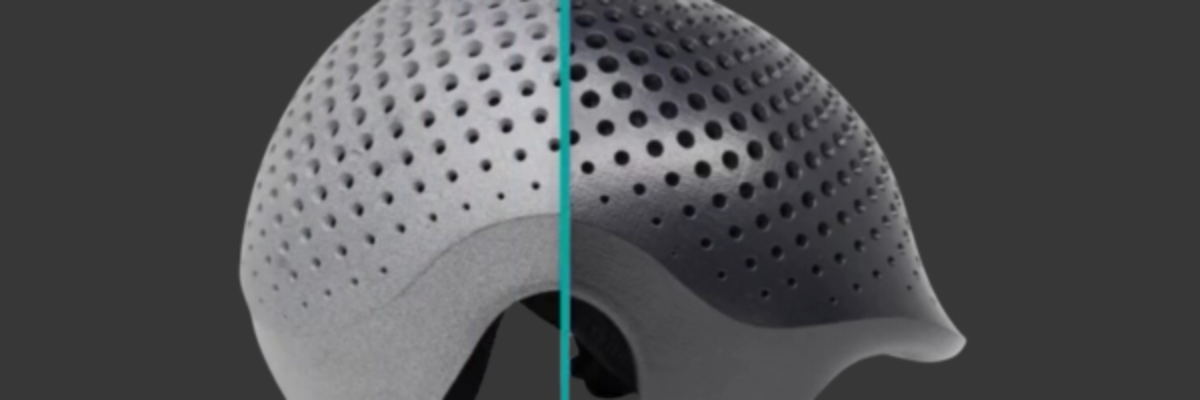
Chemical Smoothing
When customers require SAF™ components with an exceptionally smooth surface finish, chemical smoothing is always our method of choice.
In this process, the part comes into contact with a vaporized solvent specially formulated for PA, in an automated system from AMT in our case. This vaporized solvent softens the surface of the part, causing the layers to fuse more closely together and eliminating any unevenness.
This temporary softening of the surface also has the positive side effect of making the surface somewhat stronger and more cohesive after the process, thereby increasing the overall strength of the component. In addition, the sealing of tiny surface pores increases the component's watertightness and darkens its color slightly.
The chemical smoothing process takes between 15 and 30 minutes per batch. The end result is a very smooth, shiny surface. Component complexity is not a problem for this process, as the steam can also penetrate into cavities or delicate structures.
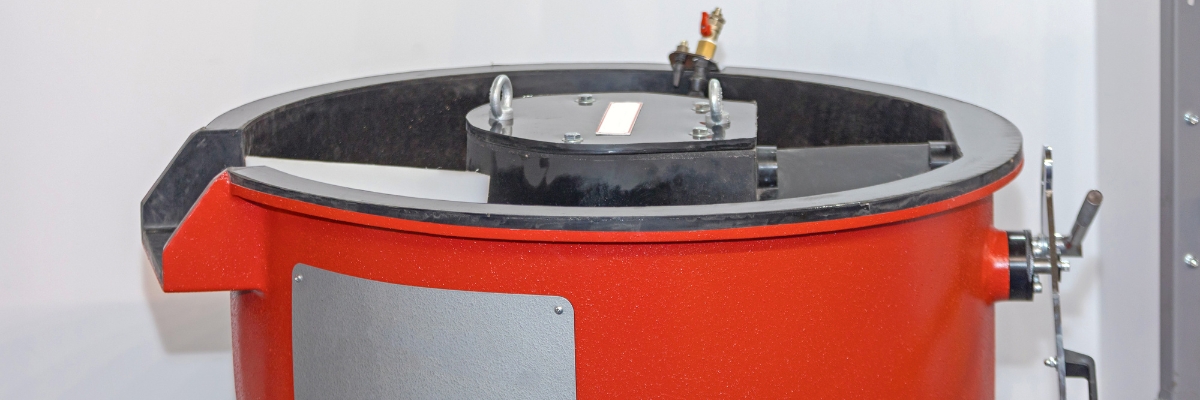
Vibratory Smoothing
Drum grinding is also used to achieve a smoother surface, but is particularly suitable for smaller components. In this process, the components are placed in a rotating drum together with an abrasive and a liquid, usually water. The abrasives can be selected individually, depending on the desired surface finish.
The rotation of the drum causes the components to rub against each other and against the abrasive, slowly and evenly removing rough edges, oxide layers and potential unevenness. The process simulates the natural erosion of stones, for example, only in a much faster form.
Depending on the desired surface finish, this process can also take place in several stages, with the abrasives being changed at each stage. The duration of this process is usually limited to a few hours, although a high-end finish can take several days due to the increased number of stages.
In contrast to chemical smoothing, this process gives the components not only a very smooth and deburred surface but also a matt or satin finish. However, with enough process steps, a high-gloss polish can also be achieved. Drum grinding is particularly suitable for small, robust components in large quantities.
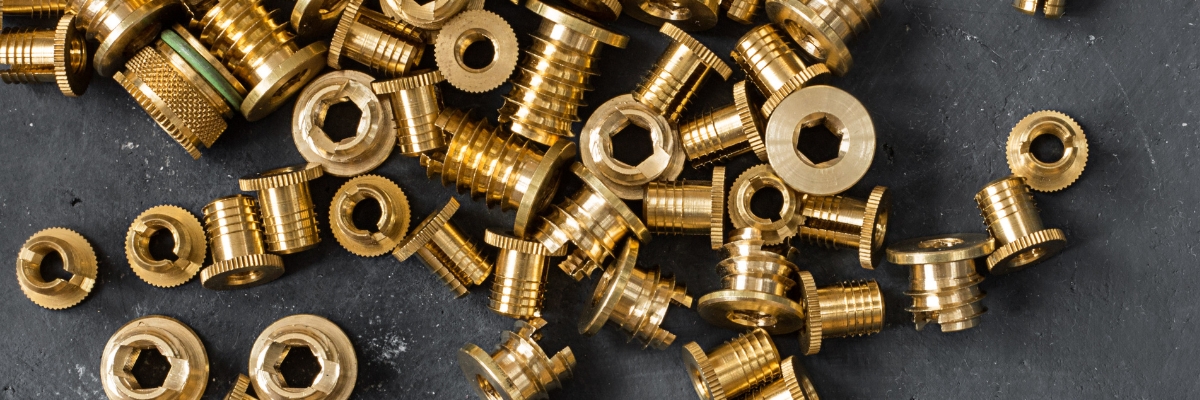
Threaded Inserts
Precisely fitting threaded inserts are essential in a wide range of industries to ensure that components can be quickly assembled and disassembled. While larger threaded holes, M8 and up, can simply be integrated into the digital model to be printed directly, very small printed threaded holes are often unable to permanently withstand strong forces.
However, since small threaded holes are in high demand, we rely on an automated solution for our production to manufacture and simultaneously insert the appropriate threads.
In this process, a heating element is used to bring the thread to a temperature at which the component melts when it comes into contact with the thread. This allows the thread to be inserted precisely and, due to the thermoplastic properties of the material, it solidifies around the insert, creating a strong connection.
By automating this process, it can be completed in less than a minute on average for each component. For larger threaded inserts and the associated pressure of the threaded holes, this process can even be completed in a few seconds for each component.
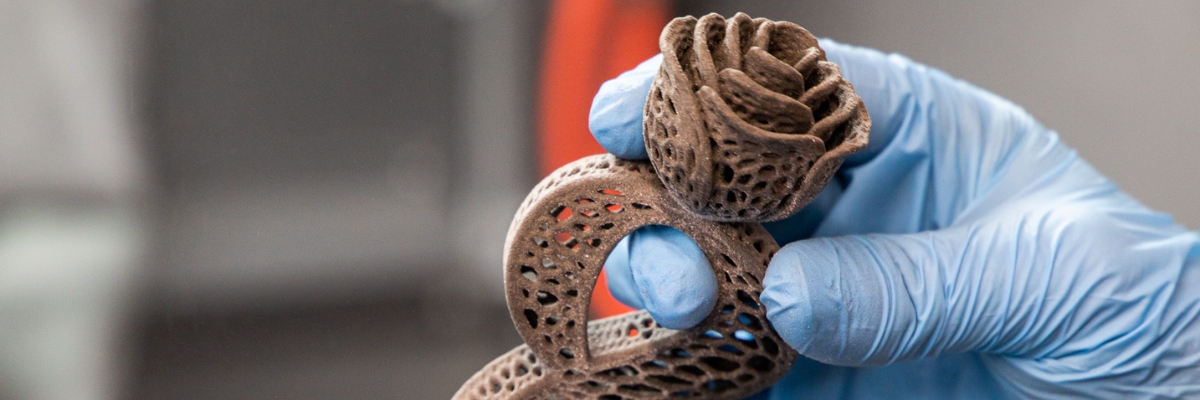
Differences to other powder-based processes
Now that we have explained the most important essential and optional post-processing steps for SAF™ components, we will now look at the differences to other powder-based processes, whereby I will refer specifically to the most widespread process, selective laser sintering (SLS).
First things first – the mandatory process steps are identical for both methods. The optional steps used in SAF™ printing can also be used in SLS printing. Nevertheless, there is a big gap between the post-processing steps for the two printing technologies, and these are specifically related to the part properties achieved by SAF™ printing.
When it comes to powder-based printing processes, SAF™ offers the best surface finishes, the tightest tolerances and excellent part density. In particular, these properties are undoubtedly superior to those of selective laser sintering and offer massive advantages not only in terms of use but also in terms of post-processing.
For example, depending on the application, parts printed using SAF™ can simply skip certain optional post-processing steps, since the surface quality, for example, is already more than sufficient, while SLS-printed parts would still need to be post-processed.
And even if certain post-processing steps are perhaps not entirely avoidable, they can be carried out much faster thanks to the improved properties. Especially when it comes to the steps of de-powdering and sandblasting, a tremendous amount of time can be saved because the powder adheres less strongly to the smoother surface. Steps such as chemical smoothing and barrel finishing also benefit from the improved initial surface.
The post-processing procedure also benefits from the increased process reliability of the SAF™ printing process. This increases the success rate, the uniformity of the component and the reproducibility, which in turn streamlines the post-processing procedure.
Last but not least, the use of the SAF™ process also has an impact on the costs associated with post-processing. The reduced amount of work involved in post-processing, especially in combination with better powder recovery and increased process reliability, can reduce the costs per component on average. These costs can be extremely significant, especially when it comes to series production.
But what about the results? At the end of the day, there is no question that SLS can also be used to produce excellent components. However, when it comes to top performance, SAF™ is the right choice for the vast majority of our project partners, as it can produce better results in less time and with exceptional durability.
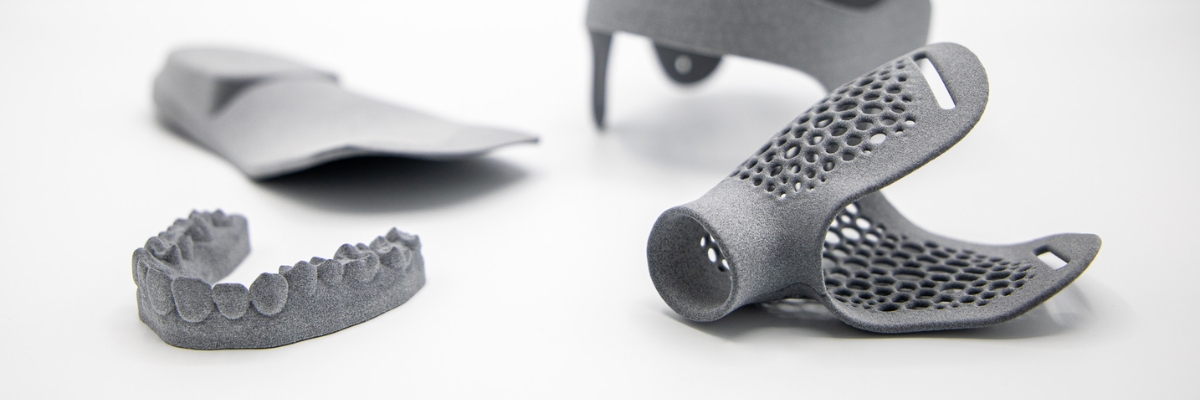
As mentioned at the beginning, SAF™ has now established itself as the preferred powder process for our project partners and customers. In addition to the excellent results, this is also due to the time saved in comparison to other powder processes, which is inevitably related to the post-processing.
If you want to take advantage of the many benefits of SAF™ parts without making a large investment, PartsToGo is the perfect partner for you. We print your parts with a specially trained team and a wide range of different finishing options to meet your exact requirements.
For in-depth advice on SAF™ parts, simply click here. If you already have a digital model and would like to order parts directly, you can do so here.
Thank you for reading – and see you in the next blog post!
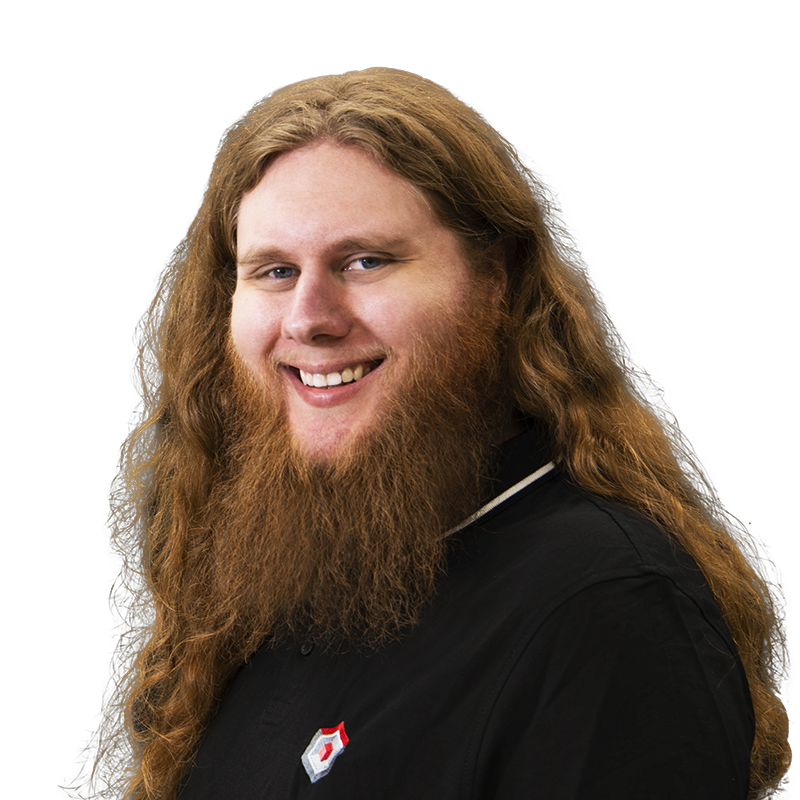