As a 3D printing service provider, we offer many options when it comes to the final finishing touches to components. Whether it's grinding, painting, trowalisation, thread inserts or much more, we always offer our customers the perfect option for their requirements.
When it comes to improving surface quality, one process in particular has become established in recent months – vapor smoothing.
In today's blog post, I would like to introduce you to this process. I will explain the process itself and the advantages that our customers receive when they use it for their components.
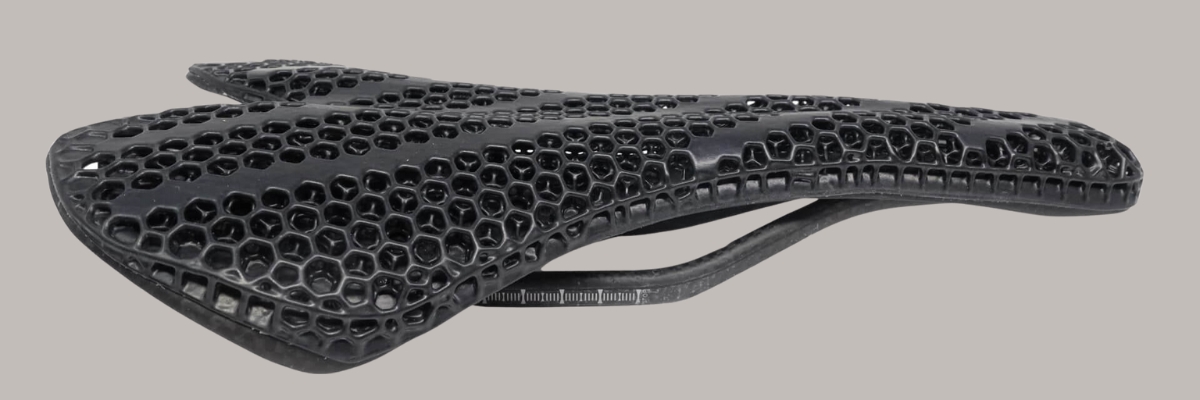
How vapor smoothing works
Vapor smoothing is always the final step in the post-processing. It is particularly essential that the component has been completely cleaned beforehand. This includes excess material, for example in the case of powder-based printed products, as well as support structures, for example in the case of filament-based components.
The fully cleaned component is placed in a sealed chamber in the first step – in our case, highly automated AMT systems specially designed for vapour smoothing are used.
This system is now filled with the appropriate solvent. It is essential to use different solvents for different materials, as many materials react differently to the respective solvents.
This solvent is then heated within the system until it evaporates. This vapour is then fed into the chamber, where the density of the vapour can be controlled to achieve different surface finishes.
As soon as the vapour comes into contact with the component, it condenses on the surface of the component due to the temperature difference. This process slowly softens the surface of the component until a micro-melting effect sets in.
This melting effect ensures that the viscosity of the outer layer is reduced without changing the mass of the component. The surface tension of the component now ensures that the softened polymer spreads evenly over the entire surface, thus eliminating raised layer lines and roughness.
Once the surface has been completely smoothed, the vapour is released from the chamber. As soon as the component is removed from the chamber, the solvent condensed on the surface also evaporates completely, whereupon the surface hardens again and thus permanently retains the smoothed surface.
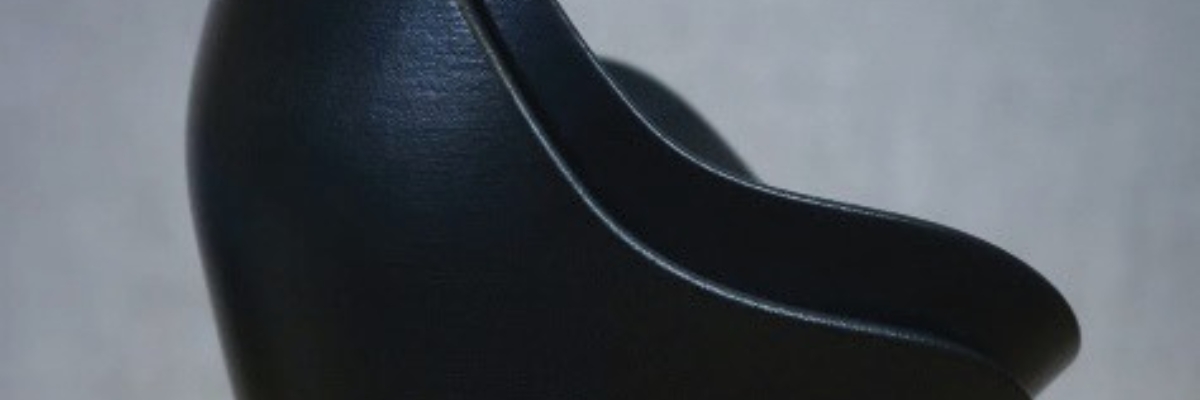
What advantages vapor smoothing offers
Now that we have examined the process in detail, let's take a look at the advantages of this post-processing method, which will also help us answer the question of why this particular method has become the preferred option for surface finishing among our customers.
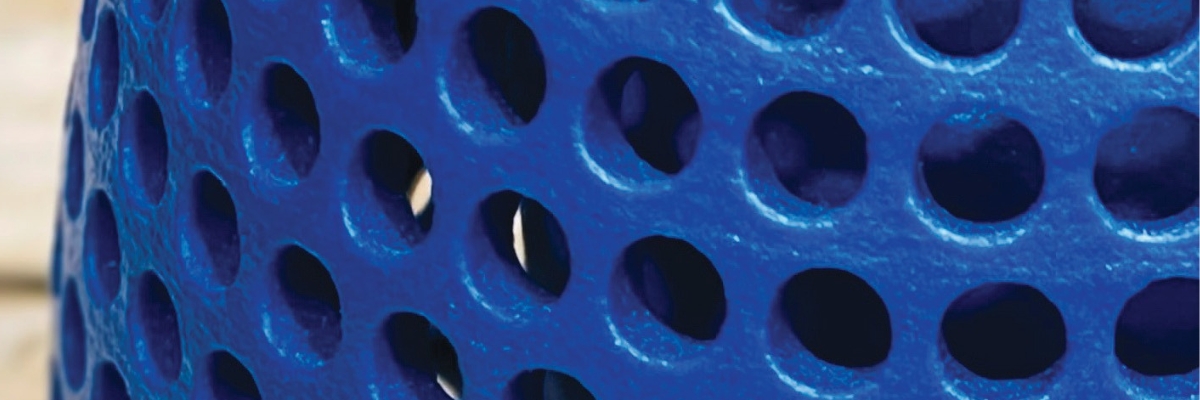
Non-abrasive process
Unlike mechanical grinding methods such as shot peening or trowalisation, vapor smoothing does not remove any material, but simply redistributes the existing material.
This ensures that the original geometry is fully retained. This is of the utmost importance, particularly for components or component groups with very tight tolerances.
In addition, the mass and weight of the component are not affected. This is an indispensable advantage when exacting weight requirements have to be met, as is often the case in the maritime and aerospace industries, in order to optimise weight distribution.
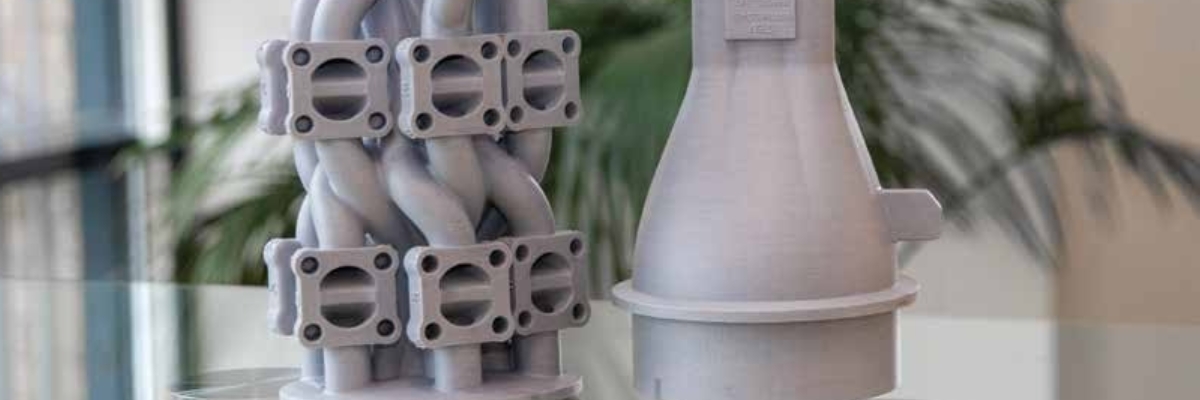
Processing complex geometriess
Traditional grinding methods quickly reach their limits when it comes to complex geometries. These methods often cannot reach all the necessary surfaces, especially when it comes to cavities or serpentine structures.
However, by using steam, even the most complex structures are no longer a problem. The steam easily penetrates into cavities and can effectively remove any unevenness from even the smallest channels.
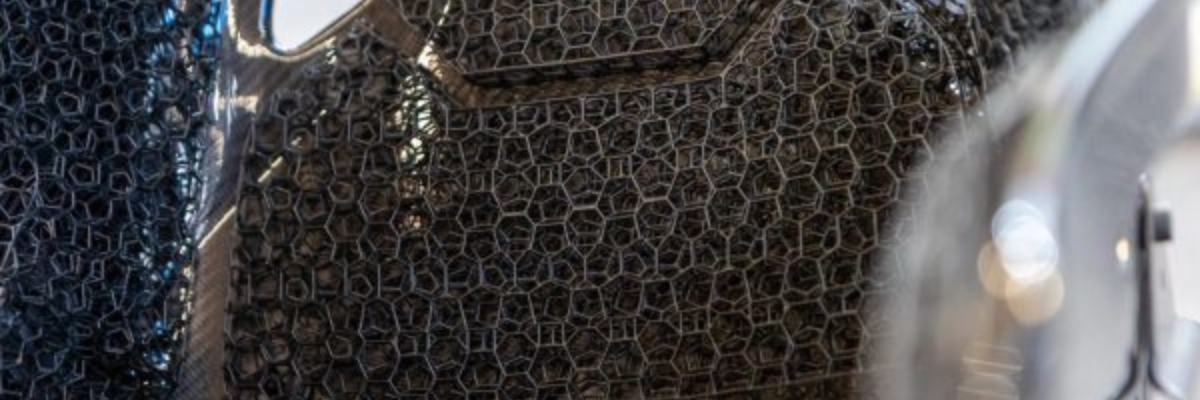
Improved mechanical properties
Unlike conventional methods, however, Vapor smoothing not only improves surface quality and eliminates unevenness, it also improves the mechanical properties of the component by closing microporosity.
The improved properties include, among other things, strength, elongation at break and durability, which is particularly ideal for components that are perpetually under high mechanical stress.
In addition, the sealing of microporosities also increases water resistance. Therefore, vapor smoothing is also a perfect choice for components that are used outdoors or under water.
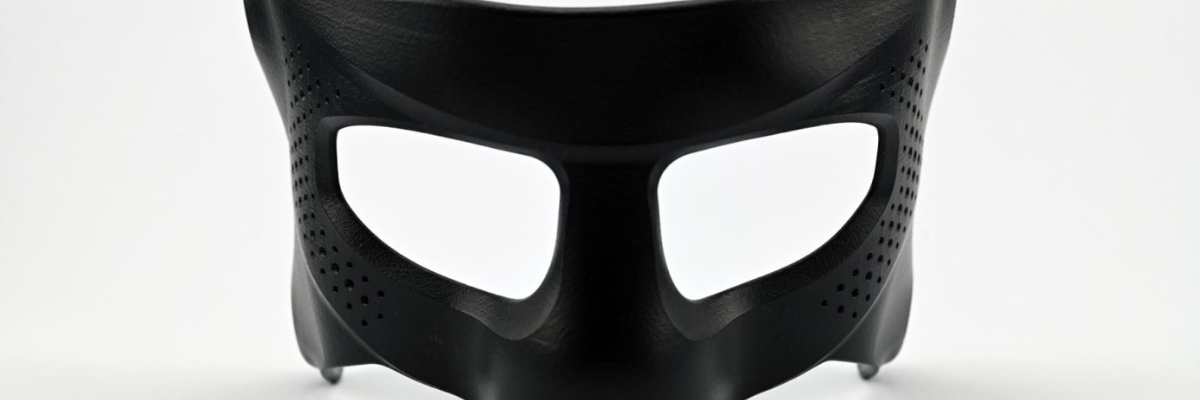
Time saving
Whether you are producing in-house or externally through a service provider, saving time is always an advantage – and our highly automated vapour-straightening solutions guarantee you will save time.
Depending on the complexity of the component and the material, we need only between 90 and 120 minutes per batch for Vapor smoothing with our AMT systems. With conventional methods, this would take up to a full working day for the same number of components – we can report this from our own experience.
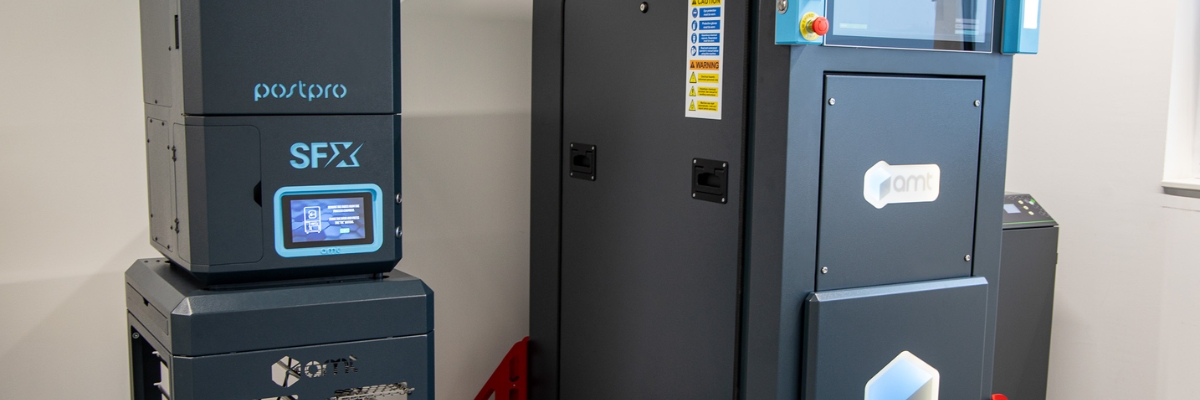
For which technologies vapor smoothing is suitable
To conclude this brief overview of chemical vapour smoothing, I would like to show you which technologies are compatible with chemical vapour smoothing.
Our AMT systems are designed for a very wide range of technologies. We can therefore offer this post-processing technology for all filament and powder 3D printing processes that we offer, including FDM®, FFF, SLS and SAF™.
These systems also offer versatility in terms of material compatibility. We can post-process polyamides and polypropylenes, as well as elastomers and even composites, using our systems to give them the perfect finishing touch.
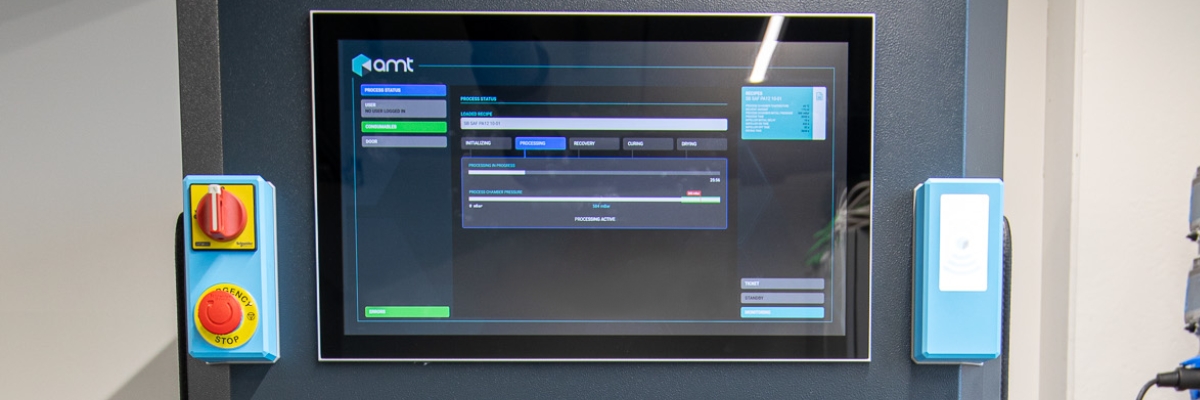
Conclusion
Vapor smoothing has become the finishing process of choice for many of our jobs. This is hardly surprising given the many advantages this process offers over conventional grinding methods.
If you would like to take advantage of Vapor Smoothing, you can access our ordering portal here. All you need to do is upload your digital model and specify the respective technologies – and you will receive the price for your project.
Thank you for your attention – and see you in the next blog post!