Masking tools, which are used for strategic masking in a variety of finishing steps, such as dyeing, painting or sandblasting, are of the utmost importance in a number of industries.
These masks are subject to very strict requirements, since they contribute to the rationalisation of production on a large scale and a faulty or even minimally imprecisely applied mask can render a component unusable, or in the case of highly automated production processes, even an entire batch of components.
There are various manufacturing methods for traditionally manufactured masking tools, from injection moulding, punching and thermoforming to manual cutting, but all of them are associated with long lead times and, for the most part, high costs, especially when it comes to small series production.
Another major disadvantage of the traditional production of these tools is the design limitations, whereby complex geometries do not allow the fit to be precisely adapted to the component. As a result, adhesive strips are then used to hold the mask in place, but this does not always lead to perfect results.
However, a long-ignored solution has recently emerged as the champion for this specific application – additive manufacturing, with its unique advantages that are particularly suitable for this application.
In this blog post, I will discuss the advantages of 3D printing for masking tools and the specific applications for which 3D-printed masks are suitable.
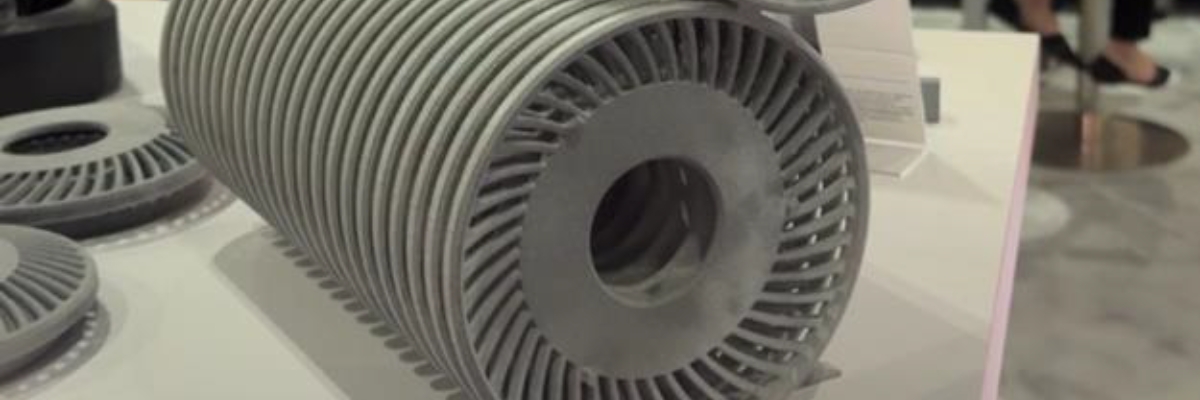
Faster, more precise and more cost-efficient with 3D printing
The reasons for the ever-increasing use of 3D printing for masking tools are manifold, so let's start with the advantages of 3D printing and how they are particularly noticeable in the production of masking tools.
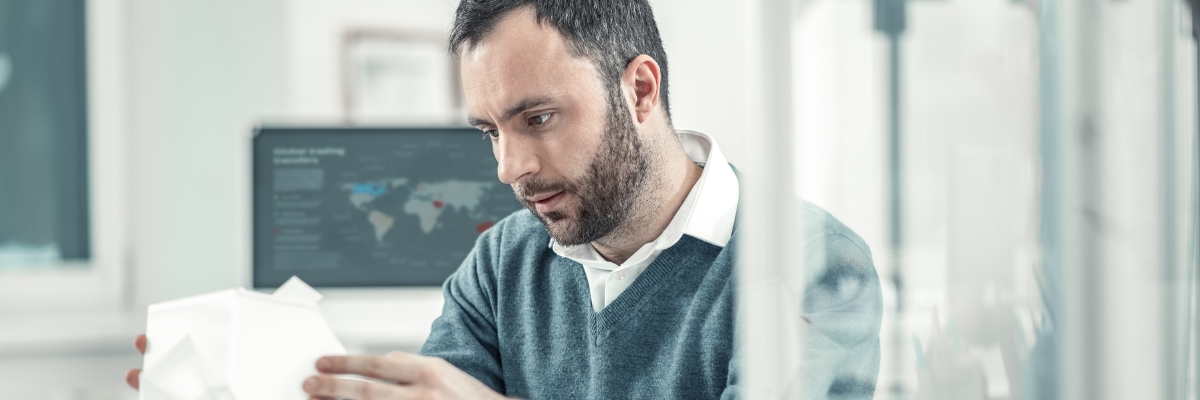
Freedom of design and precision
As mentioned in the introduction, the design restrictions are one of the biggest disadvantages of traditional manufacturing methods, which can have a significant negative impact on the undoubtedly most essential property of mask tools, precision.
3D printing excels in this regard for several reasons. One of these is the ability of additive manufacturing to produce even the most complex geometries and structures with outstanding precision. This means that masking areas can be designed highly individually, preventing potential precision issues even with very irregular or complex components.
Another factor is the ease of digitally creating the masking tool. Using a CAD program or other modelling software, the tools can be created quickly and if a digital model of the component to be masked already exists, the precise adaptation of the masking tool is even further simplified, since the digital model can simply be used as a basis for creating the tool in a 3D modelling program of choice.
The final factor in terms of design freedom and precision that 3D printing excels at is the ease with which the fit can be customised, without the need for any external aids to apply it. In addition to the precise fit to the component to be masked, holding tabs or fixing lugs, for example, can also be integrated directly into the design to ensure precision even under high mechanical loads.

Production speed and lead times
Conventional production methods for masking tools have to contend with lengthy lead times and sometimes low production speeds, which poses serious problems for volatile industries where trends change rapidly.
In this context, 3D printing has proven to be an excellent method for overcoming these challenges. The ability to produce on-demand, without the need for tools, and at excellent print speeds, means that rapid market changes can be turned to advantage by quickly implementing the latest consumer preferences.
Working with digitised models is particularly helpful here, as these can be modified with just a few clicks, depending on the complexity of the adaptation, so that the new masks can be produced and used in the shortest possible time.
And this advantage of additive manufacturing also provides massive support in the prototyping of masking tools. This means that different iterations can be produced in a much shorter time, leaving more time to test them in use and make changes if necessary.
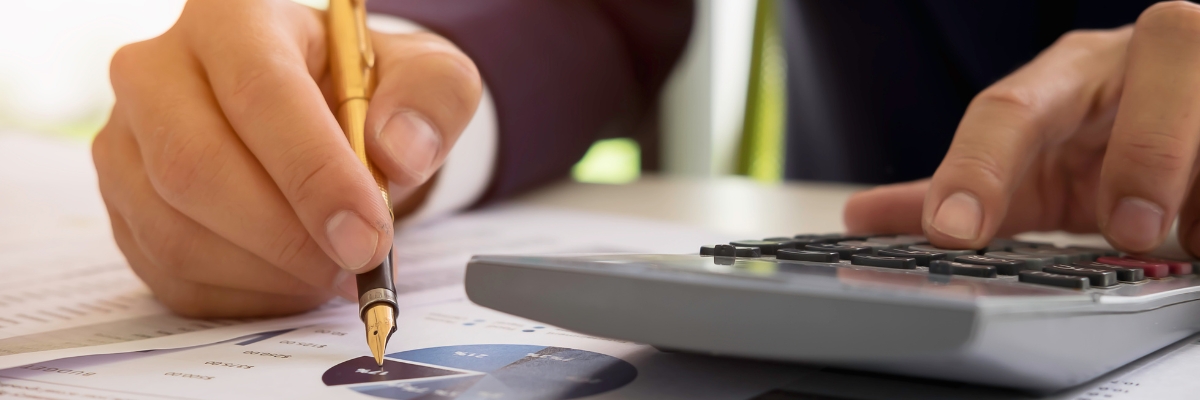
Cost efficiency
Masks are usually needed in small batches. This presents problems for many traditional manufacturing processes, especially injection moulding, as these are particularly cost-effective for large batches, whereas for individual pieces or small batches, the costs per piece are comparatively horrendous.
3D printing, on the other hand, is perfect for cost-effectively producing small series. By eliminating the need for expensive moulds and tools, which account for a large proportion of the costs in traditional production processes, the costs per component are massively reduced and production is accelerated at the same time.
But it is not only the elimination of production tools that enables costs to be saved. Another factor is the reduced material waste, since additive manufacturing only uses the material that is actually needed for the component, thus saving both production costs and the environment.
A final cost-saving point when using 3D printing, which is often overlooked, is the elimination of the need for large storage areas. Both the elimination of the need for production aids and the perfection of the on-demand production of the masking tools themselves can reduce storage costs and risks to a minimum, thus further contributing to a reduction in production costs.
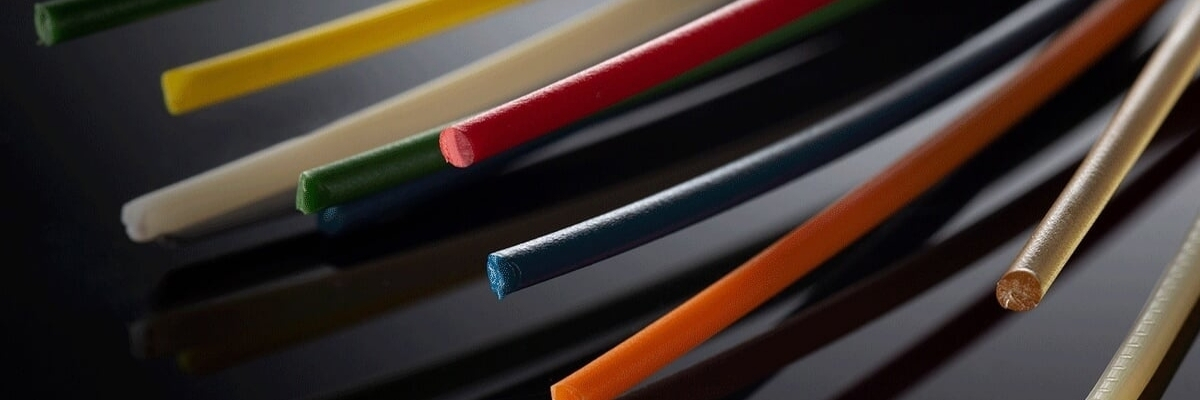
Material flexibility
All of the aforementioned advantages of additive manufacturing have been known for a while. So why has this technology only recently become established for this application? This is due to the final advantage, which has only emerged in recent years – the outstanding range of different materials.
Now, 3D printing can be used to produce a wide range of different properties needed for mask production, including, in particular, a high strength-to-weight ratio, high durability, heat and abrasion resistance.
High-performance thermoplastics, such as PEEK or ULTEM™, can now also be processed using additive manufacturing. This makes it possible to produce masks for high-performance applications, for example in the automotive or aerospace industries, that can easily withstand the high mechanical, thermal and chemical stresses of these applications.
The flexibility of the material should also be mentioned, as should the quick change between different materials in 3D printing. While long set-up times often have to be planned for conventional processes, 3D printing makes it easy to switch between different materials, allowing different mask tools to be produced one after the other without long downtimes.
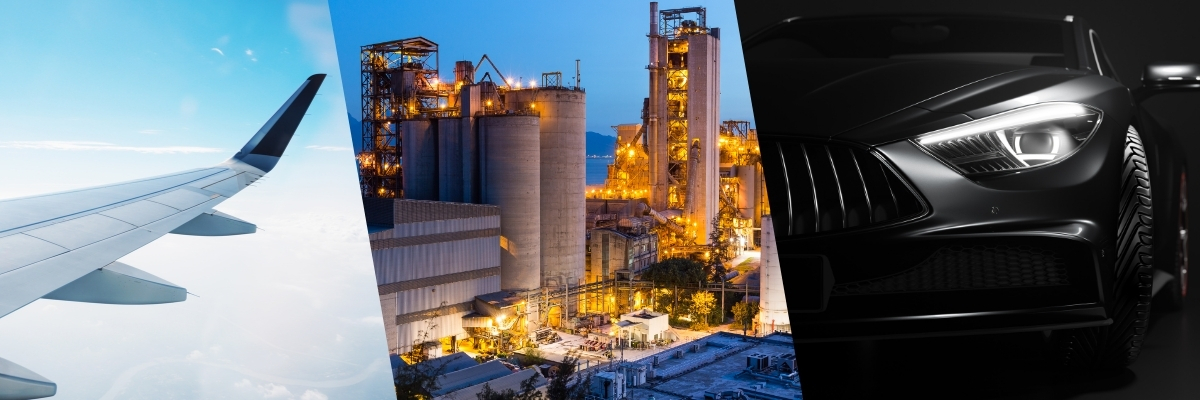
Suitable for use across all industries and applications
Now that we have explained the many advantages of using 3D printing for the production of masking tools in the first part, we will now look at the specific applications that are possible for these masks.
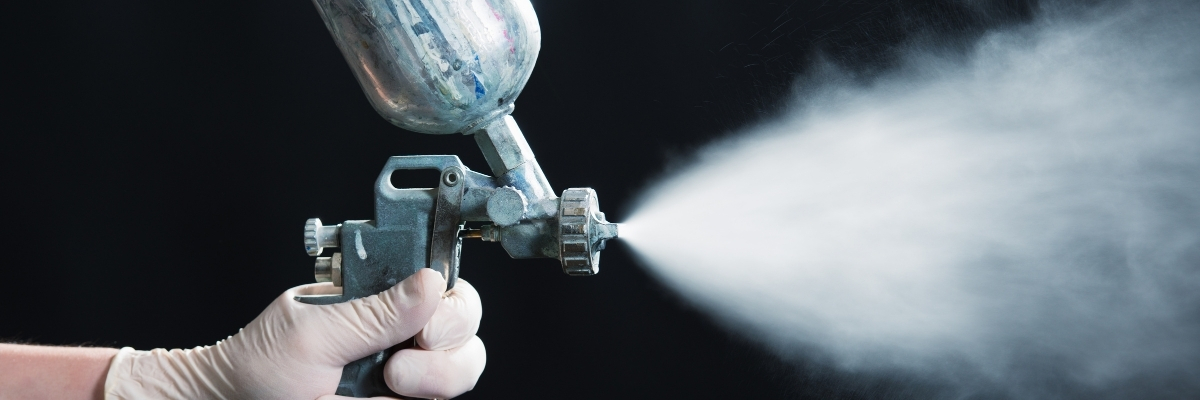
Varnishing and spray coating
When it comes to painting or spray coating components, masking tools require outstanding precision and fit to prevent overspray even on curved or angled surfaces and to ensure sharp edges between the coated and covered areas.
The ability to align the fit of the mask with the highest degree of precision on the component using the digital model or a 3D scanner means that even complex, uneven shapes can be precisely masked to ensure high-quality results.
Industries in which 3D-printed masks are used for this purpose are manifold, but they are particularly suitable for the automotive industry, for example for door handles, or for the consumer goods industry, for complex electronic housings.
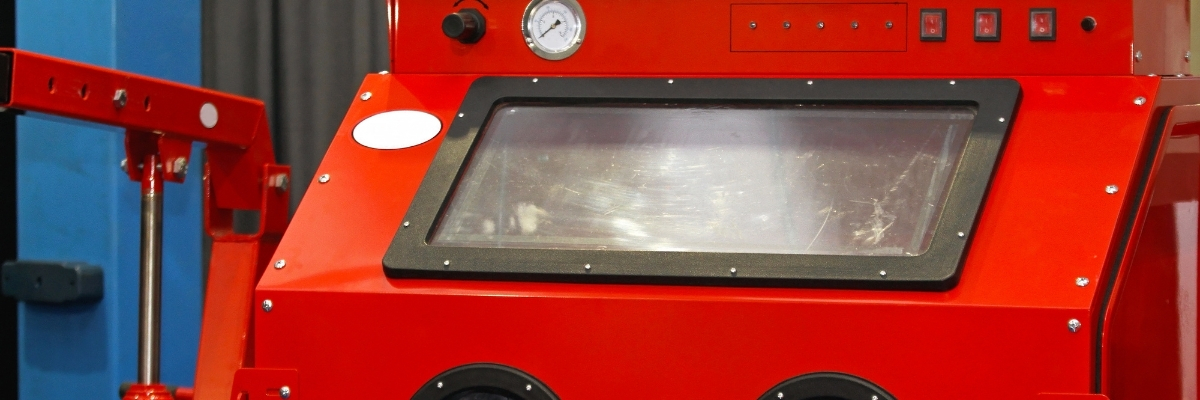
Sandblasting
When sandblasting components, masks are used that not only have to be extremely precise, which must also be guaranteed under the application of force, but also have increased abrasion resistance in order to withstand this force over a longer period of time.
Several 3D printing materials are suitable for providing excellent abrasion resistance, such as nylon or TPU, which ensures long-lasting usability and thus also reduced production costs.
Here, too, the range of industrial applications is broad. In mechanical engineering, in particular, where certain components only need to be partially processed using sandblasting, 3D-printed masking tools are ideal for enabling a safe and cost-effective process.

Powder coating
For powder coating and especially for the curing process in this method, masks are needed that can withstand high temperatures, as these masking tools have to be placed in the oven together with the workpiece to avoid accidental contamination of the uncoated areas with powder.
In particular, powder 3D printing uses a variety of materials that can withstand temperatures in the furnace of around 160 to 200 °C. In addition, this type of printing offers excellent detail reproduction, enabling even the smallest of shapes, such as threads or holes, to be accurately replicated.
The combination of powder coating and 3D-printed masks has already found some favour for vehicle parts with complex structures, such as wheel rims or chassis, or for metal furniture and household appliances, and is currently becoming more and more widespread, particularly thanks to the ideal properties, cost-effective production and reduced storage requirements.
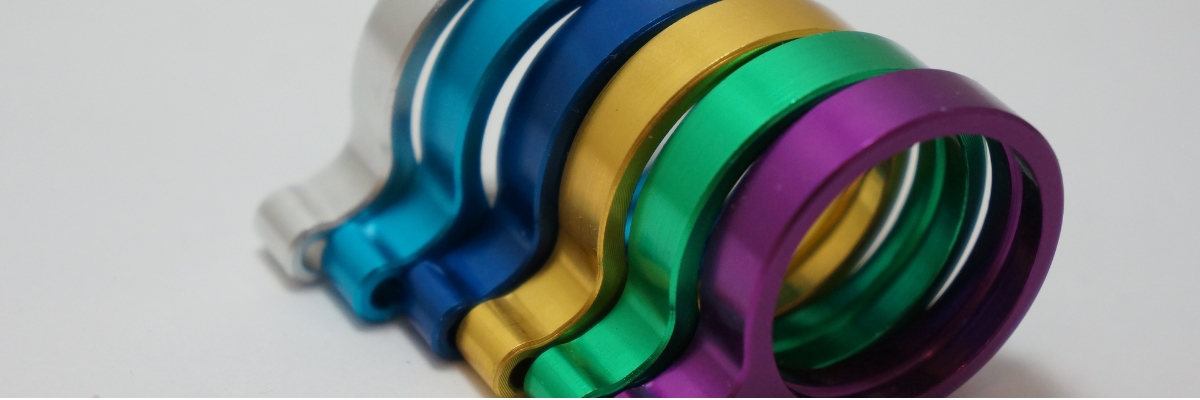
Anodising
During anodisation, the components are placed in a highly aggressive chemical bath in which electrolysis is then carried out to strengthen the oxidic layer on a metal. Masking tools in this process require maximum resistance to the acid used, for example sulphuric or chromic acid, as well as to electrolytes.
In the field of resin 3D printing in particular, several materials have now emerged that can precisely replicate these properties and at the same time possess the necessary precision to efficiently protect the components at the necessary points before anodisation.
The aviation industry frequently uses the anodising process to increase the corrosion resistance of components. However, the components are often relatively large and serve different functions, which is why certain areas, some of which are also large, have to be covered during anodising – and this is where 3D-printed masks are ideal, as they maintain their outstanding precision even in large formats.
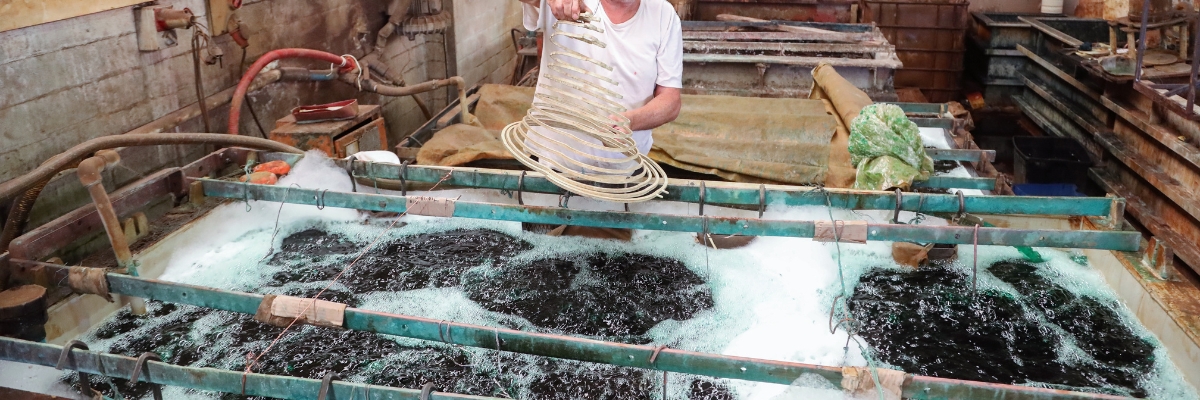
Galvanisation
Electroplating also requires masks that have excellent chemical resistance. In addition, however, the flow of electricity also plays a crucial role in this process, which is why masking tools must also be electrically insulating in order to protect specific areas of the workpiece from electroplating.
Both filament and resin 3D printing can impress with extraordinary materials that combine chemical resistance and insulating properties while also enabling excellent precision.
The advantage of design freedom is particularly advantageous in the electronics industry, where many different metals, such as copper, tin and aluminium, are electroplated, all of which require masking tools of different thicknesses. 3D printing also makes it possible to implement production changes at short notice without endangering the protection of the components.
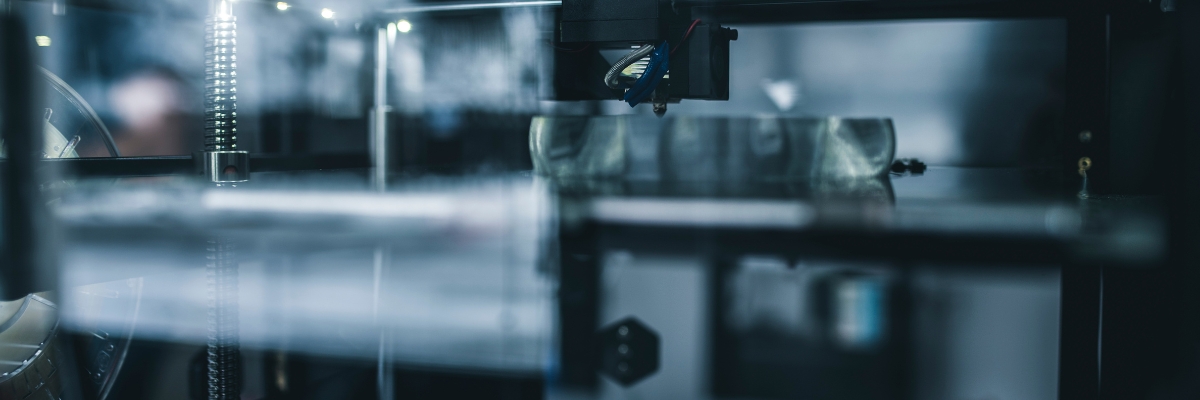
Conclusion
Even though masking tools are still a relatively new application within additive manufacturing, this blog post should have shown why this application is recently expanding into more and more industries and fields of application.
However, smaller companies in particular are often unable to take advantage of 3D printing because the cost of industrial machines is beyond their means. But we at PartsToGo have the ideal solution for this with our service!
Let us print your masking tools – simply send the digital model to info@parts-to-go.com and one of our experts will contact you shortly to discuss the final details.
Thank you for your attention – and see you in the next blog post!