While it was relatively easy to choose the right technology at the beginning of the development of 3D printing, as there simply wasn't much choice, things are different now. Due to the constant development and research within additive manufacturing, there are now countless different technologies, all with their own advantages and peculiarities, which can make choosing the right technology somewhat opaque.
This blog series aims to bring transparency to the process of choosing the right technology for your components. The aim is to compare two technologies, explain their advantages and disadvantages and finally present the ideal application for both technologies.
We will start this blog series with two powder-based technologies. On the one hand, Selective Absorption Fusion, or SAF™ for short, which was developed by the American-Israeli company Stratasys®, and on the other hand Multi Jet Fusion, or MJF for short, which was invented by the US company HP Inc, formerly Hewlett-Packard Company.
Functionality of the Technologies
Before we come to a direct comparison, however, we should first establish how exactly the technologies work to produce components from loose polymer powder.
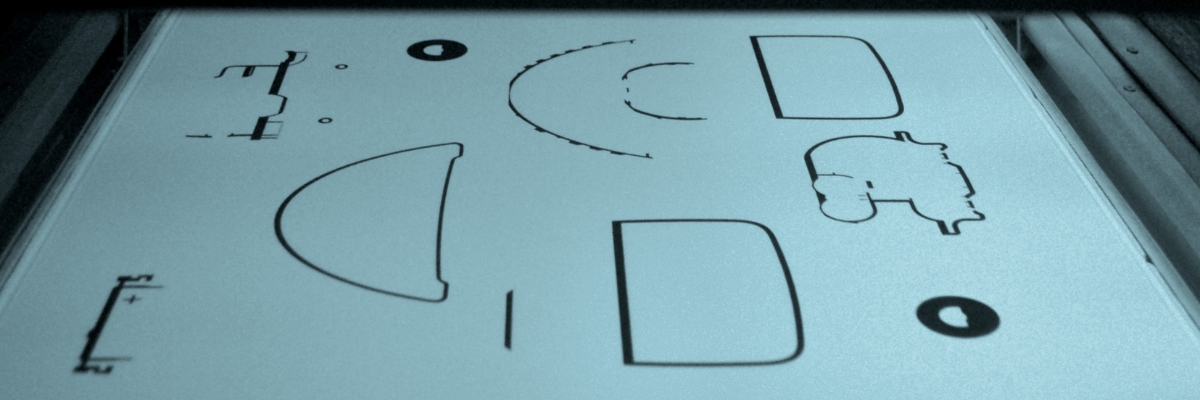
Multi Jet Fusion
In MJF, a thin, white layer of powder is first applied to the build plate and heated using infrared sources located on the print head. As soon as the required temperature has been reached, a heat-conducting liquid (fusion agent) is applied to the part of the loose powder that is to be printed.
In addition to this fusion agent, a heat-inhibiting agent (detailing agent) is also applied, but not to the area to be fused like the fusion agent, but around this area.
Once both agents have been applied, the heat source is removed some time later. Due to the black color of the Fusion Agent, it has absorbed more energy and now ensures that the white powder solidifies and melts. The detailing agent, on the other hand, acts as a kind of thermal insulator at this point, keeping the energy of the fusion agent in the designated areas.
Once the applied layer has completely melted, the entire process starts again - until the component is finished. The components must now be cooled down for between 48 and 72 hours, depending on the component, removed from the powder cake and cleaned of fused powder. Optional post-processing steps such as polishing, coloring or smoothing can then also be carried out.
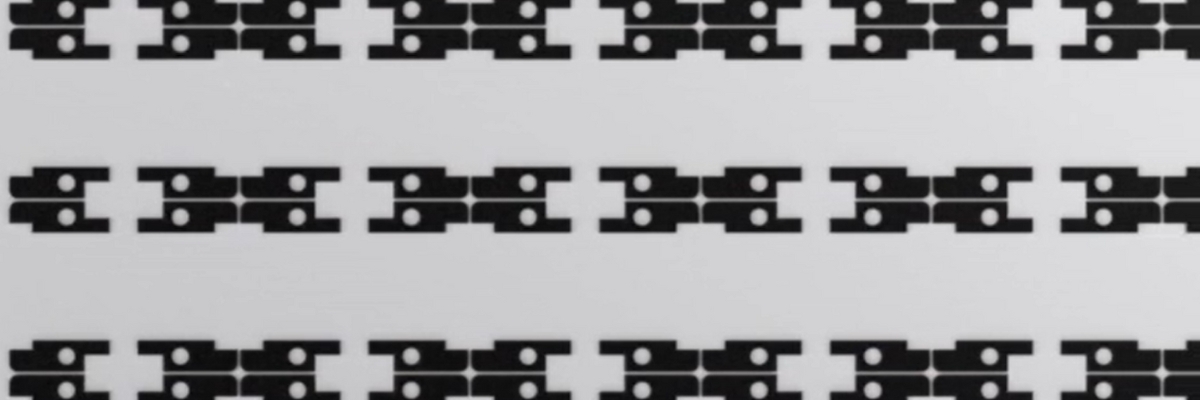
Selective Absorption Fusion
The SAF™ process, which to date can only be found in the H350 from Stratasys®, starts in the same way as MJF technology, namely with the application of a thin layer of powder to the build plate. However, instead of heating the powder directly, the so-called High Absorption Fluid (HAF™) is first applied to the areas that are to be fused together.
A second liquid is not required for this process. The HAF™ takes on the role of both fusion and detailing agent. As with the MJF, this liquid absorbs more of the infrared heat that is now applied, causing the surrounding powder to fuse together once the heat source has been removed.
The subsequent recoating process in the SAF™ process is supported by the patented Big Wave™ technology. This optimizes the feeding of the powder by ensuring, among other things, that the powder is always evenly distributed on the build plate and that overflowing powder is immediately returned.
Once the printing process is complete, the procedure is identical to the MJF process. Cooling, unpacking, cleaning and finally adding optional post-processing steps if required.
Would you like to discover the quality of SAF™ components for yourself? At the end of the blog post you will find a form with which you can secure a free SAF™ sample part!
Comparing the Technologies
The explanations of the technologies should have revealed that the two technologies are not dissimilar. The biggest differences are the fluids used during printing, the recoating process and that the powder coating and fluid application carriages move bidirectionally with MJF and unidirectionally with SAF™.
Nevertheless, both technologies offer different advantages and excel in different areas more than the other. We will now discuss the most important of these areas and compare the two technologies.
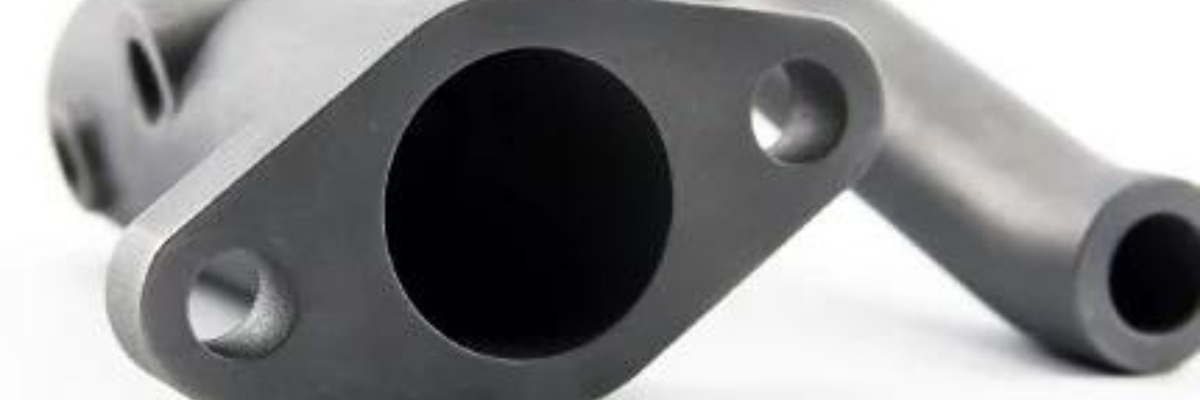
Surface Quality
As is usual with powder technologies, the surface quality is rougher with both technologies than with resin 3D printing, for example. Nevertheless, the surface quality is an important criterion, as depending on the quality, the post-processing time for components that are to be polished can be massively reduced.
In contrast to other powder-based printing processes, both technologies perform very well in this category, but SAF™ is slightly ahead. This is mainly due to the fact that SAF™ only uses one liquid and the slides move unidirectionally, which ensures better uniformity of thermal properties during printing.
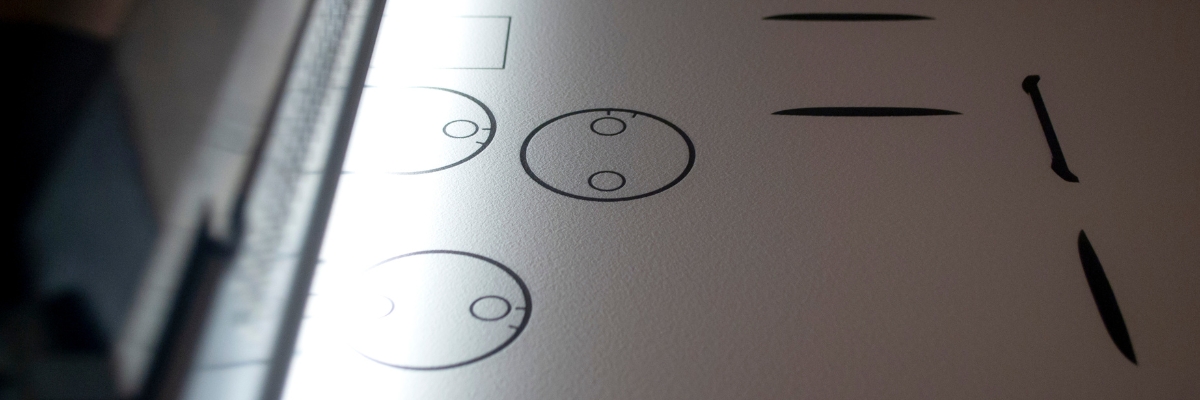
Printing Speed
In many industries, time is more than just money. Reputation, customer satisfaction and order commitments can all depend on a fast production time, which is why print speed is considered so important in many industries.
Here, the advantages given in the last point are reversed for the SAF™ process, giving MJF the edge. The bidirectional movement of the slides and the separation of the liquids ensure that the powder can fuse faster and the component is therefore completed more quickly.
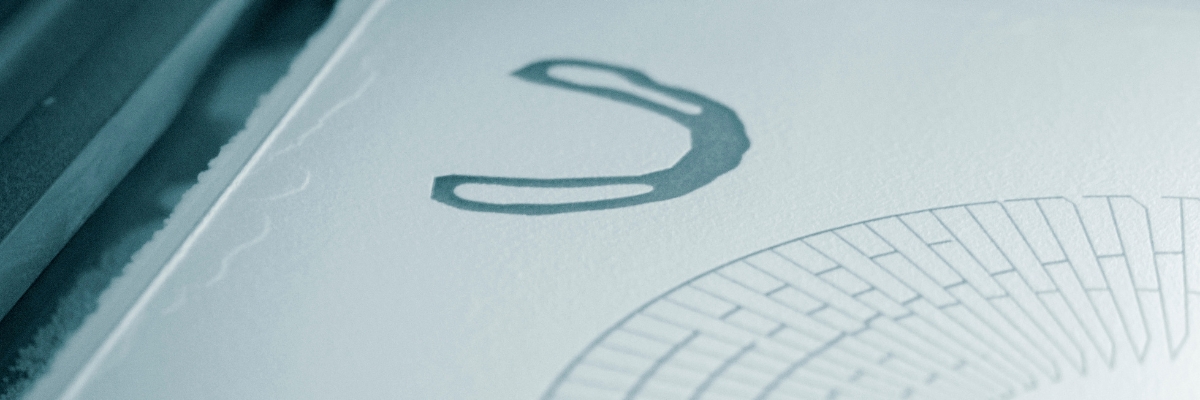
Accuracy
Implementing digital models as precisely as possible is a supreme discipline within additive manufacturing. Inaccurate production can be the death knell for a component, especially for customer-specific projects or individual parts of an assembly.
SAF™ technology has clearly set its sights on this supreme discipline. With its unidirectional inline architecture and the use of a thermal imaging camera that captures each layer with high-resolution thermal data in real time, SAF™ technology clearly outperforms its competitors.
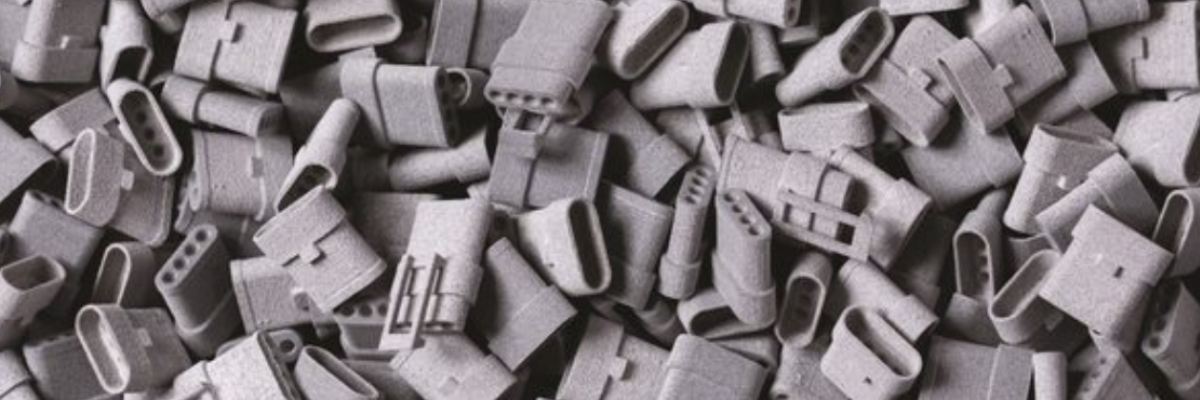
Repeatability
If components are to be produced in series, outstanding repeatability is an unavoidable factor - after all, the components in a series should not have different properties or differ in appearance.
Powder-based technologies generally demonstrate a high level of performance in this discipline - however, due to the higher precision of the SAF™ process just explained, it can also outperform the MJF here.
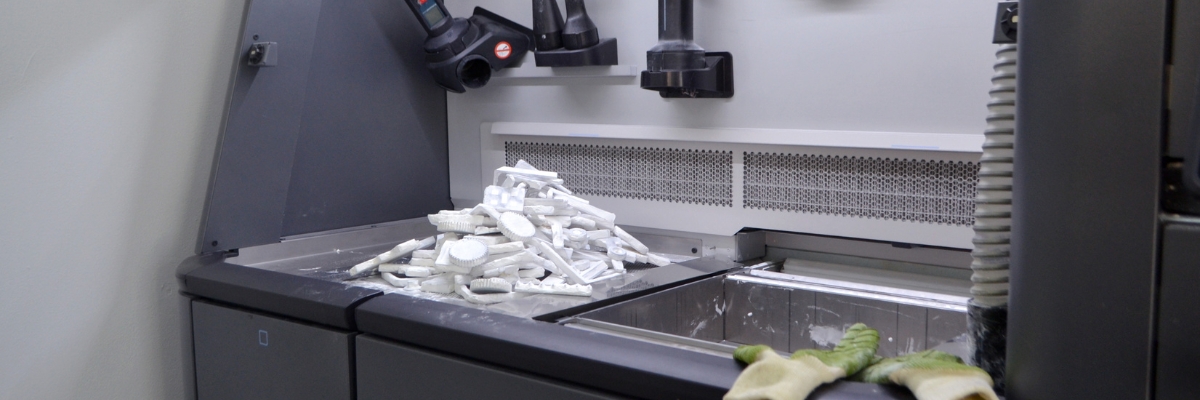
Post-Processing effort
The post-processing of powder components can take a considerable amount of time and requires a relatively large number of process steps. It is therefore essential for many applications to keep the time and effort involved as low as possible.
The detailing agent specially designed for this purpose in the MJF ensures less melted powder on average, which saves time and labor, especially in the sandblasting step. In the other mandatory post-processing steps, the two technologies are very comparable, meaning that the MJF process is ahead overall in this factor.
It is also important to note that the components always have a grey color after printing with both processes. The MJF process cannot even process dark-colored powders, as Fusion Agent gets its heat-conducting ability from its darker color. Ergo, in order to obtain colored components, a component must always be dyed in both processes.
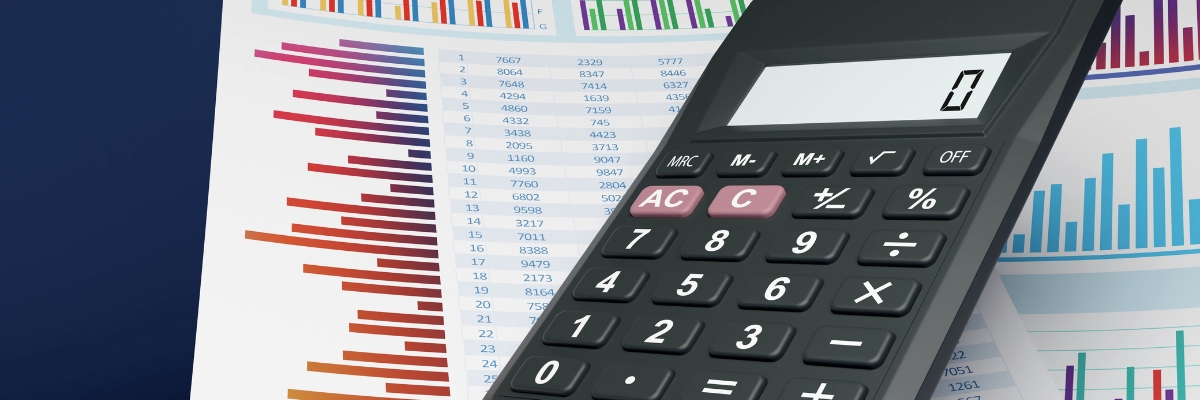
Cost Efficiency
Due to the ability to reuse unused powder after a print, 3D printing with powders always scores very well in terms of cost efficiency. Nevertheless, there is never too small a difference in terms of costs, which is why these two technologies should also be compared with each other.
However, acquisition costs and costs for electricity, for example, are rather difficult to compare in terms of technology, as there can be considerable differences between different machines - despite the same technology.
However, the SAF™ process has a fundamental advantage in terms of cost efficiency because it only uses one fluid in the printing process. This eliminates the need to purchase, deliver and store two fluids, which will reduce running costs in the long term.
SAF™ also scores with the highest nesting density of all powder technologies. This means that more parts can be produced in one print job, which pays off massively in the long term, especially in series production.
Ideal Applications of the Technologies
By directly comparing the two technologies, we have now highlighted the differences, despite the fundamental similarity of the printing process, and the advantages of each method. The final question that still needs to be answered is: for which applications is each technology ideally suited?
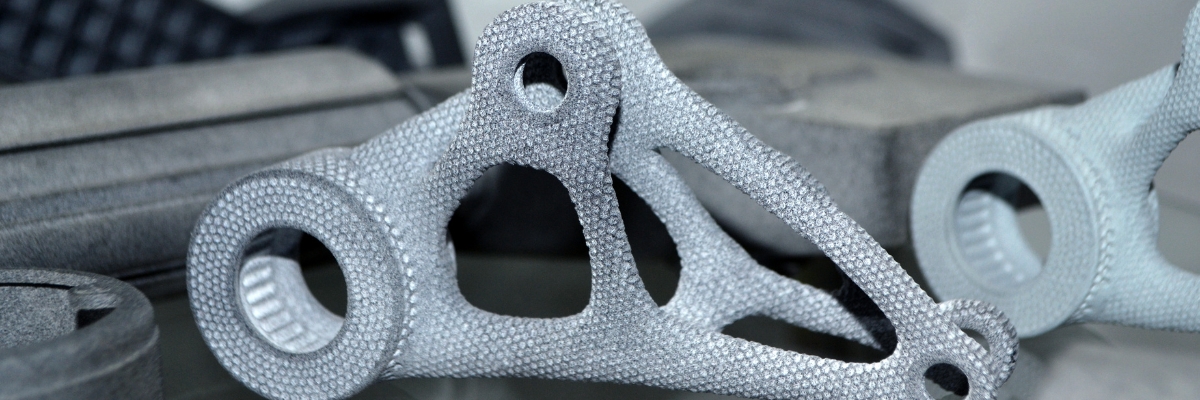
Multi Jet Fusion
MJF is virtually predestined for one of the most essential steps in product development - prototyping. The higher printing speed, the lower post-processing effort and the cost efficiency through recycling of the powder make fast iteration cycles possible at low cost.
Of course, this does not mean that MJF cannot be used for end-use parts - on the contrary. Especially when components are needed quickly, for example an emergency spare part, the use of MJF can be more than worthwhile.
Like powder-based printing technologies in general, MJF can be used across all industries. Whether for consumer goods, medical technology, defense or the automotive industry - MJF is ideal for rapid prototyping and the fast production of components.
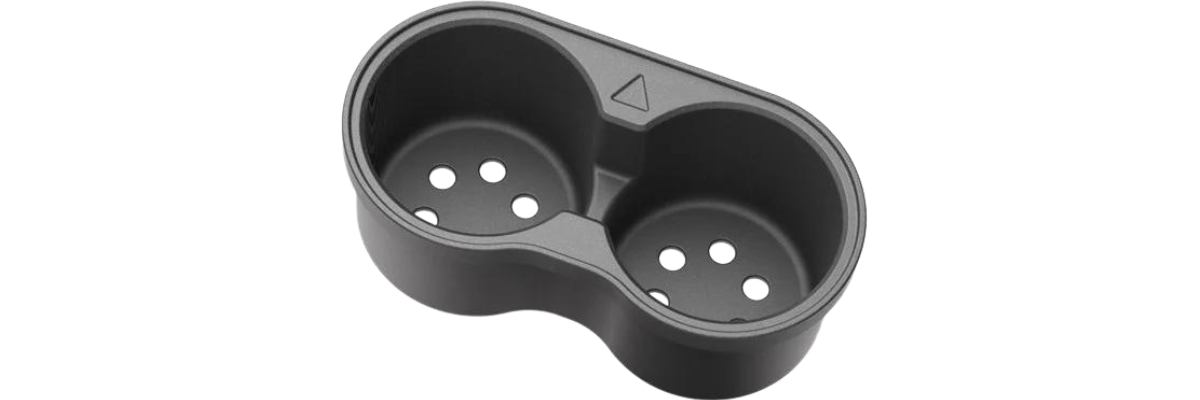
Selective Absorption Fusion
Quality over quantity - this could be seen as the mantra for the SAF™ process in this comparison. It really shines when it comes to individual, complex and detailed components and delivers the highest quality and surface finish within powder technologies - both for prototyping and for end-use parts.
Thanks to its extraordinary repeatability, SAF™ is not only suitable for the production of individual parts - series production in particular benefits massively from the unique precision of SAF™ technology.
The many advantages of the SAF™ process, from increased cost efficiency to exceptional quality, can also be used across all industries and consistently meet the highest requirements. If you would like to test whether the components from the SAF™ process also meet your requirements, you can get hold of a free sample part here.
Conclusion
It would certainly be inappropriate to declare one technology the clear winner of this comparison. Both processes have their areas of application in which they excel and are less likely to get in each other's way.
Nevertheless, it is not inappropriate to see SAF™ technology as a further development of MJF. A technology that was created specifically for rapid prototyping has, with a few modifications, become a technology that can easily meet industrial requirements for end-use parts.
If you are interested in seeing the quality of this further development with your own eyes and already have a project in mind that would be ideally suited to it, then you can get a quote here in no time at all. Have you not yet explored all the details or would you like to make direct use of the fantastic series production capabilities of SAF™ technology? Then contact us here!
I hope I have been able to present and compare both technologies adequately and hope that you will also read the next comparison of two technologies. Thank you for your attention!
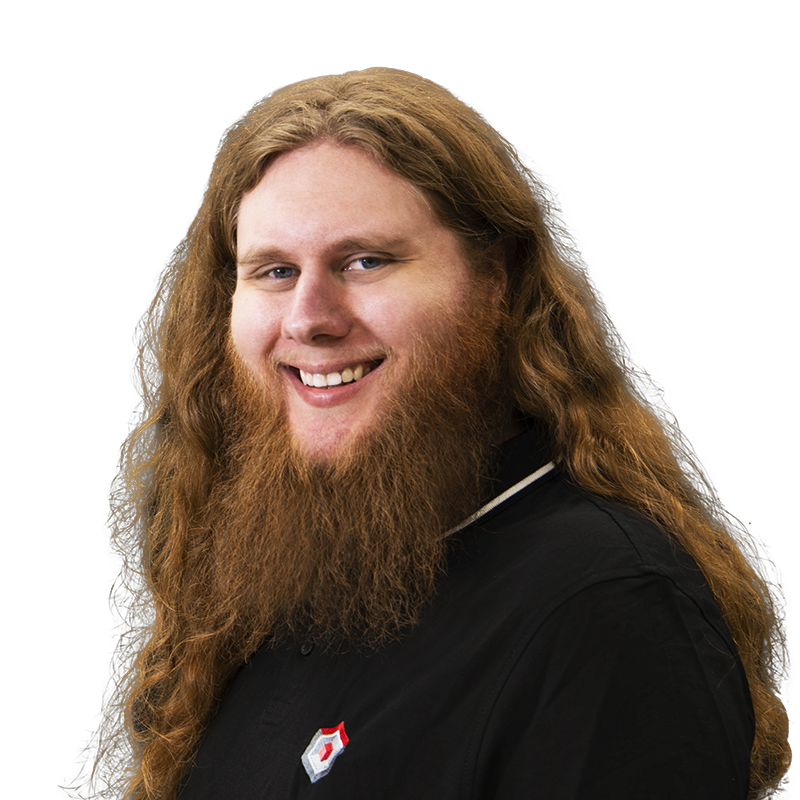