3D printers
High quality 3D printers
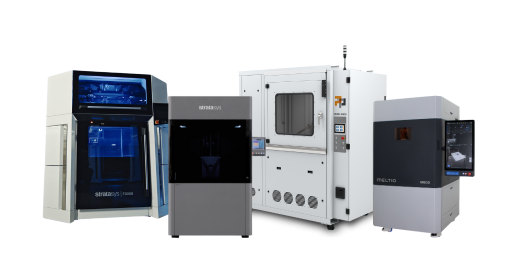
25% discount on your first order of 3D printed components!
SAVE SUMMER DISCOUNT NOW!The perfect symbiosis of quality and quantity!
Complex geometries with ideal properties!
High-resolution components with a wide variety of materials!
High-performance components with sustainable production!
A wide range of materials and ultra-fast production!
Ideal for a wide range of dental indications!
The process from simple component to product!
Fully automate your production!
Fast processing and successful management!
Sorry, there are no results for this combination of filters. Choose another combination of filters.
To ensure that all requests are handled promptly and completely, we ask that you submit all support requests through our support portal.
To the service portalDo you need assistance with your project, do you need advice or a sample part that we can send you?
Send EmailThe Stratasys® H350 is a manufacturing machine that integrates Selective Absorption Fusion, or SAF™ technology to produce functional, production-grade parts with unmatched consistency.
The H350™ powder-based 3D printer from Stratasys® is an additive manufacturing solution with smart controls that enable customers to deliver the consistency, accuracy and competitive costs that various markets demand.
Selective Absorption Technology, otherwise known as SAF™ technology powers the H350™ powder bed 3D printer. The H350™ functions by using HAF™ infrared absorption fluid to fuse powdered polymer particles together in layers to build parts. Industrial-grade piezo-electric print heads then jet this fluid onto the powder, which is then exposed to infrared energy that fuses the powder together to form each layer of the part.
Technical Specifications:
Effective build size (xyz): 315 x 208 x 293 mm
Effective build volume: 19.2 litres
Layer thickness: 100 μ
Time to a full build: 11.62 hrs
Two carriages are used in the architecture to print, fuse, and then recoat and heat the powder. It guarantees that all particles across the surface experience the same time and temperature profile regardless of where they are on the bed by printing and fusing, and then having the second carriage follow at the same pace ensuring functional parts with high print accuracy.
The thermal management system of the printer is made up of a high-resolution thermal camera that takes precise, high-resolution heat data specific to the bed position in real time, layer by layer. As a result, the temperature is constant from layer to layer throughout the construction as well as from one build to the next.
The Big Wave™ powder management system keeps a sizable, thermally stable wave of powder in place by making sure the required amount of powder is always spread throughout the entire print bed. Powder overflow is promptly recirculated to minimise temperature exposure and decrease powder ageing.
The industrial piezo printheads' ability to keep fluid temperature constant allows it to function safely in a high-temperature chamber, jet highly pigmented, viscous fluids that allows for high detail to be achieved even with a single HAF™ (High Absorption Fluid), avoids the abrupt cooling caused by cooling fluids (detailing agents), prevents the production of elephant skin and stabilises print quality and output.
Users can select the build preparation software platforms that best suit their business needs with the H350™ 3D printer. You can maintain quality control over your output with no forced firmware updates, no obligatory cloud connection, and the option to repurpose prior print settings.
The H350 printer was built to last with its long-lasting industrial print heads, low maintenance requirements, a small number of consumables and very few operating expenditures. To add, unfused powder can be reused – keeping material costs down and reducing cost per part.
While conventional powder bed fusion printers typically achieve a density of 6–10% in the build volume, the H350™'s SAF™ technology allows for part packing or nesting up to 12% in the build volume. Additionally, in real-world circumstances, Stratasys® has shown support for nesting densities of up to 23.5%. There is a clear correlation between nesting density and faster build times or more parts per build.
To simplify your workflow combine certain technologies such as the Stratasys® H350™ build removal box, build box transport trolley, powder retrieval stations and the Stratasys® H350 powder containers.
Call or email us and we will be happy to help you.
Products aimed at consumers that need to be finished to a high standard, like headphones, eyeglasses, clips, and consumer electronics cases.
Manifolds, jigs, adapters, brackets, mold tools, machine parts, and production aids.
Components that move, including snaps, gears, and hinges; electrical protection connectors; enhanced impact resistance; or components that are made of tough materials, like housings and shatter-proof trims.
Fill up the form below and we will send you the data sheet by e-mail.
Cookie settings
We use cookies to provide you with the best possible experience. They also allow us to analyze user behavior in order to constantly improve the website for you. Privacy Policy