3D-Drucker
Hochwertige 3D-Drucker
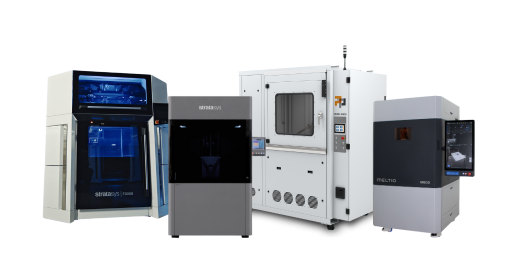
Durch den Einsatz modernster Blue-Laser-Technologie und Laserauftragschweißen zur Herstellung von Metallkomponenten mit beispielloser Geschwindigkeit und Effizienz integriert der Meltio M600 einen neuartigen Ansatz zur Energieversorgung und optimiert den Metalldruckprozess für eine verbesserte Produktivität und Materialausnutzung.
Der Meltio M600 ist ein fortschrittlicher industrieller 3D-Metalldrucker, der Probleme wie lange Vorlaufzeiten, hohe Lagerkosten und Schwachstellen in der Lieferkette behebt. Der M600 nutzt die fortschrittliche Blue-Laser-Technologie und das Laserauftragschweißen, um die Druckgeschwindigkeit zu erhöhen, den Energieverbrauch zu senken und die Effizienz bei einer Vielzahl von Metallmaterialien, einschließlich reflektierender Materialien wie Kupfer und Aluminium, zu verbessern. Das System verfügt über ein großes Bauvolumen (300 x 400 x 600 mm), eine vollständig inerte Kammer mit einem Sauerstoffgehalt von nur 10 ppm und eine umfassende Prozesssteuerung, um eine konstante Teilequalität zu gewährleisten.
Zu den Hauptmerkmalen des M600 gehören die Dual- und Quad-Wire-Funktionen, die das sequentielle Drucken mit bis zu vier verschiedenen Materialien in einem einzigen Auftrag ermöglichen, sowie eine Hot-Wire-Funktion, die das Material vorwärmt, um die Abscheidungsraten zu erhöhen. Die Maschine ist für die nahtlose Integration in bestehende Industrieanlagen konzipiert und erfordert nur minimale Bedienereingriffe für eine 24/7-Fertigung ohne Aufsicht. Mittels integriertem 3-Achs-Tastsensor können punktgenaue Reparaturarbeiten an Bauteilen und Formeinsätzen vorgenommen werden.
Der M600 bietet dank seiner benutzerfreundlichen Oberfläche, der Slicing-Software Meltio Horizon und der kompakten Lasereinheit, in der sämtliche optische Komponenten gekapselt integriert sind, eine kosteneffiziente Lösung für industrielle Anwendungen der additiven Metallfertigung durch reduzierte Rüstzeiten und geringeren Wartungsaufwand.
Technische Daten:
Druckbereich: 300 x 400 x 600 mm
Lasersystem: 9 Direktdiodenlaser mit insgesamt 1000 W
Laserwellenlänge: 450 nm (blau)
Die blauen Laser mit einer Wellenlänge von 450 nm bieten gegenüber herkömmlichen Nahinfrarotlasern und grünen Lasern mehrere bedeutende Vorteile. Erstens ermöglichen sie einen schnelleren Druck, wobei der M600 bis zu 60 % schneller druckt als der M450. Diese höhere Geschwindigkeit geht mit einem geringeren Energieverbrauch einher, der auf die höheren Absorptionsraten von Licht mit kürzerer Wellenlänge zurückzuführen ist. Blaue Laser sind besonders effektiv bei reflektierenden Materialien wie Kupfer und Aluminium, die für herkömmliche Lasersysteme normalerweise schwierig sind. Diese verbesserte Absorption ermöglicht eine effektivere Bearbeitung eines breiteren Spektrums an Metallmaterialien und erhöht so die Vielseitigkeit des Druckers. Der Laserkopf des M600 enthält neue und aktualisierte Sensoren für eine bessere Drucküberwachung.
Die Hot-Wire-Technologie von Meltio auf der M600 ist eine innovative Funktion, die die Leistung des Druckers erhöht. Durch eine konfigurierbare Stromquelle wird das Drahtmaterial aufgewärmt, bevor es das Schmelzbad erreicht, was zu einer schnelleren Auftragungsrate und optimierter Energieeffizienz führt. Die Hot-Wire-Technologie ermöglicht einen schnelleren Druck großer Teile, indem sie die Energie senkt, die Laser benötigen, um das Material vollständig zu schmelzen, und den Materialfluss optimiert, wodurch sich die mechanischen Eigenschaften der fertigen Komponenten verbessern. Dank der Programmierbarkeit können Kunden die Vorwärmparameter an spezifische Materialien und Bauteilbedürfnisse anpassen und so die Kompatibilität mit einer Vielzahl von Legierungen erhöhen.
Der M600 kann funktional abgestufte Komponenten aus bis zu vier Materialien herstellen. Dabei kann die Materialzusammensetzung im Bauteil graduell variiert werden, um die spezifischen Anforderungen zu verbessern. Ingenieure können Teile mit präzisen Materialeigenschaften an Funktionsflächen herstellen, was die Gesamtleistung und Funktionalität und Standzeit der Bauteile verbessert. Die Optionen „Dual Wire“ und „Quad Wire“ ermöglichen Kosteneinsparungen, indem kostspielige Materialien nur dann eingesetzt werden, wenn dies absolut notwendig ist, während Bauteilgeometrien, die einer geringeren mechanischen, abrasiven und thermischen Belastung ausgesetzt sind, mit kostengünstigeren Materialien gefertigt werden können. Diese Funktionalität erweitert den Anwendungsbereich des M600 und schafft neue Möglichkeiten in Bereichen wie der Luft- und Raumfahrt, der Automobilindustrie und der Medizin, in denen Teile aus mehreren Materialien erhebliche Vorteile bieten können.
Mit einem integrierten piezoelektronischen Tastsensor kann das System den Laserkopf exakt an der Oberfläche des zu bearbeitenden Werkstücks positionieren, um punktgenau an unterschiedliche Teilgeometrien Material aufzutragen. Diese Fähigkeit ist besonders nützlich, um an verschlissenen Bauteilen Reparaturen durchzuführen bzw. Bauteilgeometrien zu verstärken, da der Drucker so genau bestimmen kann, an welcher Stelle Material platziert werden muss. Der Tastsensor erkennt die genaue Position und Ausrichtung eines Werkstücks und stellt sicher, dass neue Merkmale an der richtigen Stelle und Ausrichtung angebracht werden. Bei Reparaturanwendungen kann es beschädigte Bereiche kartieren, sodass der M600 bestimmte Teile eines Teils wiederherstellen oder verstärken kann. Diese Funktion unterstützt auch eine Vielzahl von Werkstückhalterungsoptionen, sodass der M600 problemlos in bestehende Fertigungsabläufe integriert werden kann.
Der Meltio M600 verfügt über ein geschlossenes Atmosphärenkontrollsystem, das eine inerte Umgebung in der Baukammer aufrechterhält, was zu hervorragenden Druckbedingungen führt. Diese Methode liefert extrem niedrige Sauerstoffwerte von nur 10 ppm, was für die Verhinderung von Oxidation und den Schutz der Unversehrtheit empfindlicher Metalle während des Drucks von entscheidender Bedeutung ist. Darüber hinaus verfügt der M600 über ein Feuchtigkeitskontrollsystem und ein dreistufiges Partikel- und Chemiefiltersystem, das die regulierte Umgebung verbessert. Diese Eigenschaften machen den M600 besonders geeignet für die Arbeit mit reaktiven Materialien wie Titan-, Aluminium- und Kupferlegierungen, was letztendlich zu hochwertigen Metallteilen mit außergewöhnlichen mechanischen Eigenschaften und geringer Oxidation führt.
Die geschlossene Prozesssteuerung des Meltio M600 ist eine intelligente Funktion, die durch Echtzeitüberwachung und adaptive Anpassungen eine gleichbleibende Teilequalität gewährleistet. Drei Hochgeschwindigkeitskameras und Pyrometer überwachen kontinuierlich die Schweißnaht und Temperatur des Schmelzbades und liefern dem System wichtige Informationen. Der M600 passt, ähnlich wie der M450, die Laserleistung und die Materialzufuhrraten automatisch auf der Grundlage dieser Informationen an, um optimale Druckbedingungen zu gewährleisten. Diese adaptive Steuerungsmethode erkennt und korrigiert Anomalien während des Druckprozesses und senkt somit die Wahrscheinlichkeit von Fehlfunktionen. Die Prozesssteuerung mit geschlossenem Regelkreis verbessert die allgemeine Zuverlässigkeit und Qualität der gedruckten Objekte durch ständige Feinabstimmung der Druckparameter und macht den M600 zu einem hochpräzisen und effizienten Metall-3D-Drucksystem.
Das integrierte Nullpunktspannsystem stellt eine standardisierte Schnittstelle zwischen der Druckplatte und den Werkstückhalterungen her und ermöglicht so eine schnelle und präzise Positionierung und Klemmung der Komponenten. Dieses System ermöglicht Benutzern einen schnellen Wechsel zwischen Werkstücken oder Vorrichtungen bei einer Positionierungsgenauigkeit von weniger als 5 µm. Diese Funktionalität ist besonders nützlich in hybriden Fertigungssystemen, da sie einen reibungslosen Übergang zwischen dem M600 und anderen Fertigungsprozessen wie CNC-Bearbeitung oder Nachbearbeitung ermöglicht.
Die Meltio M600 verfügt über eine außergewöhnliche Materialkompatibilität, was sie zu einer ausgezeichneten Wahl für eine Vielzahl von Anwendungen in der additiven Metallfertigung macht. Das System kann eine Vielzahl von Metallen verarbeiten, darunter Edelstahl, Baustahl, Kohlenstoffstahl, Titanlegierungen, Nickellegierungen und sogar Kupfer und Aluminium. Diese Vielfalt ermöglicht es den Anwendern, das beste Material für ihre individuellen Projektanforderungen auszuwählen, wie z. B. Korrosionsbeständigkeit, hohe Festigkeit oder Hitzebeständigkeit. Die Fähigkeit des M600, mit Titanlegierungen zu arbeiten, eröffnet neue Möglichkeiten in der Luft- und Raumfahrt sowie in der Medizintechnik, wo leichte und stabile Materialien von entscheidender Bedeutung sind.
Der Meltio M600 ist so konzipiert, dass er sich nahtlos in bestehende Fertigungsumgebungen integrieren lässt, was ihn zu einer hervorragenden Ergänzung für moderne Maschinenwerkstätten und Produktionsanlagen macht. Seine Designphilosophie fördert die Interoperabilität mit CNC-Maschinenabläufen, sodass er neben traditionellen subtraktiven Fertigungstechniken eingesetzt werden kann. Der hohe Grad an Autonomie des M600 senkt den Bedarf an Bedienereingriffen und ermöglicht eine 24/7-Produktion ohne Aufsicht. Der werkseitig ausgerichtete Laserkopf der Maschine erhöht ihre autonome Effizienz, da keine manuelle Laserausrichtung erforderlich ist und der Wartungsaufwand drastisch reduziert wird. Die benutzerfreundliche Oberfläche des Systems und die schnelle Programmierung mit der Meltio Horizon-Software gestalten die Einrichtung und Bedienung selbst für Personen, die mit der additiven Fertigung noch nicht vertraut sind, effizient und schnell.
Der M600 ist ideal für die Herstellung komplizierter Leichtbaukomponenten für die Luft- und Raumfahrt sowie die Verteidigungsindustrie. Durch die Möglichkeit, mit Titanlegierungen und Inconel zu arbeiten, eignet er sich hervorragend für die Herstellung hochfester, hitzebeständiger Teile, einschließlich Motorkomponenten, Strukturelementen und maßgefertigten Halterungen. Die Präzision und Kapazität der Anlage, vollständig dichte Teile herzustellen, erfüllen die anspruchsvollen Qualitätsstandards dieser Branchen problemlos.
Für Anwendungen im Automobilbereich ermöglicht der M600 die schnelle Prototypenentwicklung und die Kleinserienfertigung von Spezialteilen. Dank seiner hohen Auftragungsrate und der Flexibilität, mit einer Vielzahl von Metallen zu arbeiten, eignet er sich ideal für die Herstellung von Motorkomponenten, Abgassystemen und Strukturelementen. Die Dual- und Quad-Wire-Funktion des Druckers ermöglicht die Herstellung von funktional spezifischen Materialien, was besonders bei Hochleistungsanwendungen im Automobilbereich von Vorteil sein kann.
Die Fähigkeiten des M600 sind für die Öl- und Gasindustrie von großem Nutzen. Die Fähigkeit der Maschine, mit korrosionsbeständigen Legierungen wie Inconel und Edelstahl umzugehen, ist für die Herstellung von Komponenten, die aggressiven Umgebungen standhalten, von entscheidender Bedeutung. Das große Bauvolumen ermöglicht die Herstellung großer Bauteile, während die Fähigkeit, vorhandene Komponenten zu reparieren und nachträglich mit fortschrittlichen Funktionen zu versehen, für die Wartung und Aktualisierung von Geräten in abgelegenen Gebieten äußerst nützlich sein kann, da dadurch Ausfallzeiten und Logistikkosten gesenkt werden.
Der M600 ist so konzipiert, dass er reibungslos mit bestehenden Maschinenwerkstätten zusammenarbeitet. Seine Interoperabilität mit CNC-Prozessen, der geringe Bedarf an Bedienereingriffen und die Fähigkeit, kontinuierlich zu arbeiten, machen ihn zu einer hervorragenden Ergänzung für herkömmliche Maschinenwerkstätten. Die Möglichkeit, ganze Teile herzustellen, vorhandene Komponenten mit Funktionen zu erweitern und Reparaturen durchzuführen – und das alles innerhalb eines einzigen Systems – bietet Maschinenwerkstätten neue Möglichkeiten und Umsatzchancen.