3D-Drucker
Hochwertige 3D-Drucker
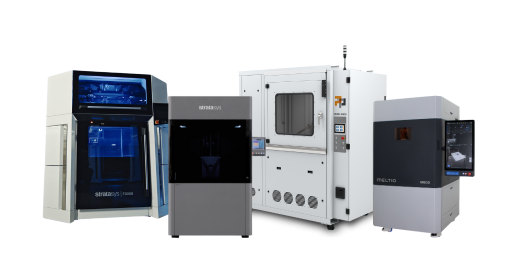
25 % Rabatt auf Ihre erste Bestellung von 3D-gedruckten Bauteilen!
SOMMER-RABATT JETZT SICHERN!Die perfekte Symbiose aus Qualität und Quantität!
Komplexeste Geometrien mit idealen Eigenschaften!
Hochauflösende Bauteile mit großer Materialvielfalt!
Leistungsstarke Bauteile mit nachhaltiger Fertigung!
Große Werkstoffauswahl und ultraschnelle Fertigung!
Ideal für verschiedenste Dentalindikationen!
Der Prozess vom simplen Bauteil zum Produkt!
Vollautomatisierung Ihrer Produktion!
Schnelle Verarbeitung und erfolgreiches Management!
Für diese Kombination der Filter gibt es leider keine Ergebnisse. Wählen Sie eine andere Filter-Kombination.
Um sicherzustellen, dass alle Anfragen zeitnah und vollständig bearbeitet werden, bitten wir Sie, alle Support-Anfragen über unser Support-Portal zu stellen.
Zum Service-PortalBrauchen Sie Unterstützung bei Ihrem Projekt, benötigen Sie eine Beratung oder ein Musterteile das wir Ihnen zusenden können?
Email sendenDer 3D-Druck läuft grundsätzlich in drei Prozessschritten ab: Druckjobvorbereitung, Druckprozess und Nachbearbeitung. Industrielle Druckanlagen können innerhalb dieser Prozessschritte gewisse Phasen autonom handhaben, bei anderen jedoch ist eine Automatisierung durch den Drucker selbst nicht möglich, wodurch insbesondere bei sehr hohen Stückzahlen Produktivität verloren geht.
Die Lösung für dieses Problem liefert Additive Automation, einst als hauseigenes Entwicklungsprojekt gestartet, doch inzwischen zu einem der größten Lösungsanbieter für vollautomatisierte Produktionszellen herangewachsen. Das Opus Magnum dieser Entwicklungsarbeit ist die Produktionszelle V1, mit der sich eine Vielzahl der eigentlich manuellen Prozesse automatisieren lassen, wodurch eine 24/7-Produktion möglich wird und somit die ideale Lösung für sehr hohe Stückzahlen ist.
Die Hauptkomponente der Produktionszelle ist selbstverständlich der Roboterarm, welcher den Großteil der Arbeit übernimmt.
Dieser sechsachsige Arm bietet eine Reichweite von 1.400 mm in alle Richtungen, kann bis zu 10 kg Gewicht tragen, brilliert mit herausragender Präzision sowie fortschrittlichen Sicherheitsfunktionen und erreicht Gelenkgeschwindigkeiten von bis zu 225 Grad pro Sekunde.
Eine Automation der Additiven Fertigung kann selbstverständlich nicht ohne die passenden Druckanlagen auskommen, wovon bis zu drei Stück in der Produktionszelle V1 Platz finden.
Die Druckanlagen bestechen dabei mit ultraschnellen Druckgeschwindigkeiten, einer hervorragenden Oberflächenqualität sowie einer großen Materialvielfalt, um eine Vielzahl von Eigenschaften zu ermöglichen.
Mit zwei Reinigungsstationen, einmal eine SVC-Anlage und einmal ein Ultraschallwasserbad, wird sichergestellt, dass auch komplexeste Bauteile gründlich gereinigt werden.
Die SVC-Lösung ist dabei für die Entfernung des überschüssigen Resins zuständig, wobei ein speziell für Resinbauteile formuliertes Lösungsmittel zum Einsatz kommt, während das Wasserbad mögliche Reste dieses Lösungsmittels entfernt.
Mit zwei Regalen gegenüber voneinander, von welchen eines als Eingangs- und eines als Ablageregal genutzt wird, bietet die Produktionszelle V1 genug Platz für die Produktion von bis zu 36 Bauplatten.
Zusätzlich sind diese beiden Regale mit Sensoren ausgestattet, welche dem Roboterarm mitteilen, aus welchen Regalen er leere Bauplatten entnehmen und in welche er volle Bauplatten legen kann.
Um ein Maximum an Sicherheit für den gesamten Prozess und für die Arbeitskräfte zu gewährleisten, ist in der Produktionszelle V1 sowohl eine Klimaanlage als auch ein Absaugsystem integriert.
Dadurch wird einerseits sichergestellt, dass die Temperatur für den Druckprozess und das Material immer perfekt ist, und andererseits werden die giftigen Dämpfe, die bei Druckprozess mit Resin entstehen können, aus der Zelle entfernt.
Die Produktionszelle wird von einer stabilen Plexiglaswand umringt, welche für eine Abgrenzung der umliegenden Produktion sorgt und die Sicherheit der Anwender und umliegenden Arbeitskräfte erhöht.
Durch diese Wand werden sowohl giftige Dämpfe in der Produktionszelle gehalten, aus welcher sie über das Absaugsystem entfernt werden, als auch die Temperaturkontrolle verbessert.
Das digitale Modell wird mit der passenden CAD- oder 3D-Modellierungssoftware für den Druck vorbereitet und daraufhin an die Druckanlage übertragen, um den Druckprozess zu beginnen.
Trotz dem außergewöhnlich hohen Automationsgrad mit der Produktionszelle, müssen einige Aspekte manuell vorbereitet werden. Diese Vorbereitung besteht jedoch nur aus dem Einlegen der leeren Bauplattformen in das Eingangsregal, dem Auffüllen des Lösungsmittels für die Reinigungsstation und das Stellen von Material in den Drucker, wobei die Befüllung jedoch automatisiert ist.
Nun beginnt der Roboterarm seine Arbeit. Er entnimmt eine der Bauplatten aus dem Eingangsregal, führt diese in den Drucker ein und ein Sensor im Drucker registriert die eingeführte Bauplattform, woraufhin der Druckjob automatisch gestartet wird. Nach dem Ende des Druckvorgangs entnimmt der Roboterarm selbstständig die Bauplattform und führt diese zum nächsten Schritt.
Nach einem kurzen Stopp auf der Umgreif-Halterung wird der Druckjob in die erste Waschstation gelegt. Bei diesem Waschvorgang, welcher sechs Minuten in Anspruch nimmt, werden Resinreste entfernt, woraufhin das Bauteil für ebenfalls sechs Minuten in die zweite Waschstation, ein Ultraschallwasserbad, gelegt wird, um potenzielle Reste des zuvor genutzten Lösungsmittels zu entfernen.
Zum Schluss legt der Roboterarm den Druckjob in das Ablageregal, welches Platz für bis zu 36 Bauplatten bietet. Daraufhin entnimmt der Roboterarm die nächste leere Bauplattform aus dem Eingangsregal und der Druck- und Waschprozess wird so lange wiederholt, bis das gesamte Ablageregal voll ist.
Nachdem der Druckzyklus vollständig beendet wurde, müssen die fertigen Druckjobs manuell entnommen werden und in eine Nachhärtungsstation der Wahl gelegt werden, um ein Maximum an mechanischen Eigenschaften zu erhalten. Daraufhin müssen nur noch die Supportstrukturen entfernt werden und schon ist das Bauteil fertig.
Gemeinsam automatisieren wir Ihre Fertigung. Reduzieren Sie Kosten und erhöhen Sie Ihren Fertigungsoutput. Ideal für Anwendungen mit kurzen Taktzeiten wie CNC Maschinen und 3D Drucker-Farmen.
Sie haben ein konkretes Projekt?Kontaktieren Sie uns!
Privatsphäre Einstellungen
Wir nutzen Cookies um Dir die bestmögliche Erfahrung zu bieten. Außerdem können wir damit das Verhalten der Benutzer analysieren um die Webseite stetig für Dich zu verbessern. Datenschutz