3D-Drucker
Hochwertige 3D-Drucker
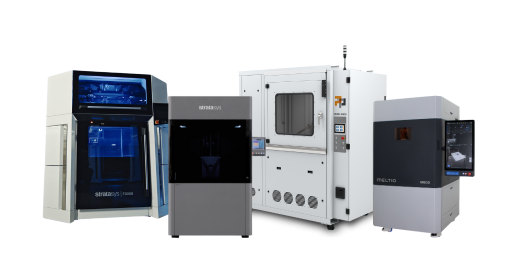
Die Nachbearbeitung von Resinbauteilen ist essenziell. Die Additive Fertigung mit Resin erfordert mehrere zwingend benötigte Nachbearbeitungsschritte, ohne die das Bauteil nicht funktionsfähig ist.
Diese zwingend benötigten Schritte sind einmal die Reinigung, einmal die Entfernung von Supportstrukturen und einmal die Nachhärtung. Im heutigen Blogpost möchte ich auf eben diese drei Schritte eingehen, diese erklären sowie mögliche Schwierigkeiten und Lösungsansätze für diese Schwierigkeiten aufzeigen.
Nachdem der Druckjob fertiggestellt und die Bauplatte aus dem Drucker entnommen wurde, müssen die hergestellten Komponenten stets einer Reinigung unterzogen werden. Diese Reinigung wird mit einem speziellen Lösungsmittel, zumeist Isopropanol, durchgeführt.
Klingt erst einmal einfach. Bei sehr simplen Strukturen, beispielsweise einem einfachen Würfel, ist es dies auch. Doch wenn wir uns zu komplexeren Strukturen begeben, ergo Komponenten mit Kleindetails, Hohlräumen, Löchern oder ähnlichem, kann aus dem Reinigungsprozess schnell eine Qual werden.
Überschüssiges Resin muss vollständig vom Bauteil entfernt werden, um die Qualität und mechanischen Eigenschaften des Bauteils zu maximieren. Und genau diese Vollständigkeit kann bei komplexeren Strukturen zur Schwierigkeit werden.
Die Reinigung von Resinbauteilen kann dabei mit verschiedenen Methoden durchgeführt werden. Die wichtigsten davon sind die händische Reinigung, die Reinigung mit speziell dafür vorgesehenen Waschstationen oder ein Ultraschallbad.
Die günstigste, aber auch arbeitsaufwendigste Methode, um Resinbauteile zu reinigen, ist per Hand. Das Bauteil wird dabei in eine Wanne mit Isopropanol getunkt und mit einem Pinsel, im besten Fall ein Hartborstenpinsel, vorsichtig von überschüssigem Resin befreit.
Der hohe Arbeitsaufwand dieser Methode wird leider nicht mit besserer Qualität belohnt – im Gegenteil. Selbst nach mehrmaligen Reinigungsdurchläufen können sich bei komplexeren Strukturen noch Resinreste auf dem Bauteil befinden.
Zu unserem Glück leben wir aber im 21. Jahrhundert und müssen uns daher nicht mehr auf händische Arbeit verlassen - Maschinen und Automation sei Dank!
Waschstationen sind die weitverbreitetste Methode, um Resinbauteile zu reinigen. Solche Waschstationen übernehmen quasi den vorher beschriebenen Teil der händischen Reinigung, indem das Reinigungsmittel in der Maschine „umhergewirbelt“ und dadurch das überschüssige Resin vom Bauteil entfernt wird.
Durch Waschstationen gereinigte Bauteile bieten, in den allermeisten Fällen, eine höhere Oberflächenqualität und benötigen, in eindeutig allen Fällen, weniger Zeitaufwand als händisch gereinigte Bauteile. Bei kleineren Komponenten können auch mehrere gleichzeitig von den Stationen bearbeitet werden, was weitere Zeit einspart.
Allerdings ist die Anschaffung einer Waschstation mit weitaus höheren Kosten verbunden als bei der händischen Reinigung jemals anfallen. Während kleine und hobbymäßige Waschstationen schon für einige hundert Euro zu bekommen sind, kosten professionelle und industrielle Waschstationen nicht selten einige tausend Euro.
Waschstationen sind daher nicht wirklich geeignet, wenn die Additive Fertigung nur „nebenher“ oder als Hobby betrieben wird. Im professionellen und industriellen Bereich werden Waschstationen hingegen unumgänglich, da die Zeit, welche für die händische Reinigung benötigt wird, in diesem Bereich nicht tragbar ist. Gleichzeitig werden die Anschaffungskosten durch den enormen Zeitgewinn aber auch rasch ausgeglichen.
Wie bereits erwähnt, bieten Waschstationen eine höhere Oberflächenqualität als die händische Reinigung. Wird jedoch eine exorbitante Oberflächengüte benötigt, muss auf eine andere Methode zurückgegriffen werden.
Ultraschallreiniger stellen die qualitativ hochwertigste, gleichzeitig aber auch die mit den höchsten Anschaffungskosten verbundene Möglichkeit Resinbauteile zu reinigen dar.
Bei diesem Verfahren wird die Reinigungsflüssigkeit, in diesem Fall kein Isopropanol, sondern TPM (Tripropylenglykolmonomethylether) oder DPM (Dipropylenglycolmethylether), durch eine Ultraschall-Schwingung zwischen 20 und 40 kHz angeregt. Dadurch entstehen mikroskopisch kleine Bläschen, welche kurze Zeit später wieder implodieren.
Durch dieses Implodieren der Bläschen, was auch als Kavitation bezeichnet wird, entsteht eine große Druck- und Sogwirkung am Bauteil, durch welche Resinreste geradezu abgesprengt werden und daraufhin vollständig zerbröseln.
Diese Art der Reinigung eignet sich, aufgrund der hohen Anschaffungskosten, vor allem für den industriellen Betrieb oder, wie vorhin bereits erwähnt, bei Komponenten, die eine außergewöhnliche Oberflächengüte benötigen, beispielsweise Schmuck.
Die größte Schwierigkeit bei diesem Schritt der Nachbearbeitung ist die Wichtigkeit der vollständigen Entfernung von übriggebliebenem, ungehärtetem Resin. Gerade bei der händischen Reinigung können mehrere Durchgänge erforderlich sein, um sämtliches überschüssiges Resin zu entfernen – und selbst dann besteht, besonders bei komplexen Komponenten, weiterhin die Gefahr, dass sich in einer Rille oder einem Hohlraum weiterhin Resin befindet.
Was ist aber nun das Problem daran, wenn sich noch ungehärtetes Resin auf dem Bauteil befindet? Und kann man es zur Not auch nachträglich entfernen?
Befindet sich ungehärtetes Resin auf der Oberfläche, leidet die Oberflächenqualität darunter. Da das Bauteil am Ende nachgehärtet werden muss, härtet das übriggebliebene Resin teilweise aus, wodurch Unebenheiten auf der Oberfläche entstehen.
Befindet sich das Resin wiederum in beispielsweise einem Hohlraum oder einem Kanal, kann dies die Funktionsweise des Bauteils vollständig zerstören. Muss nun eine andere Komponente mit dem Resinbauteil verbunden werden, ist dies nicht mehr möglich, weil das übriggebliebene Resin nun den Verzahnungspunkt verkleinert oder vollständig verschlossen hat.
Da das eigentlich ungehärtete Resin durch die Nachhärtung trotzdem ausgehärtet wird, ist auch eine nachträgliche Entfernung unmöglich. Ist die Oberflächenqualität oder Funktionalität des Bauteils also durch übriggebliebenes Resin eingeschränkt worden, ist es spätestens nach der Nachhärtung unter Umständen vollständig unbrauchbar.
Um unnötige Arbeit und Kosten zu sparen, sollte man lieber einmal zu oft das Bauteil auf Resinreste überprüfen. Auch wenn Waschstationen oder Ultraschallreiniger eingesetzt wurden! Nur weil solche Anlagen eine bessere Entfernung ermöglichen, sind sie noch lange nicht vollkommen frei von Fehlern.
Die Supportentfernung kann vor oder nach dem Nachhärten geschehen – vor der Nachhärtung ist die Entfernung jedoch einfacher, daher ordne ich es in diesem Blog als zweiten Schritt ein.
Bei der Supportentfernung geht es darum, wer hätte es geahnt, die Supportstützen, die bei der Additiven Fertigung mit Resin notwendig sind, zu entfernen. Warum diese Entfernung notwendig ist, muss ich wahrscheinlich niemandem erklären. Lieber erkläre ich, welche 3 Methoden es gibt, um diese Supportstützen zu entfernen, und welche Schwierigkeiten dabei auftreten können.
Natürlich gibt es auch hier die Möglichkeit, gute alte Handarbeit zu nutzen. Die Supportstrukturen lassen sich, aufgrund ihrer häufig länglichen Form, gut greifen und ohne allzu großen Kraftaufwand entfernen.
Diese Methode sollte bei Bauteilen mit kleineren Details allerdings auf keinen Fall angewendet werden. Dort könnte ein kräftiger Ruck ausreichen, um neben der Supportstruktur auch eines der kleineren Details in der Hand zu halten.
Bei der händischen Entfernung werden auch kleine bis mittelgroße Noppen am Bauteil zurückbleiben, welche jedoch mit ein wenig Sandpapier und etwas mehr Geduld entfernt werden können.
Bündigschneider stellen die sicherere Methode dar, um Supportstrukturen von Bauteilen zu entfernen. Gerade bei komplexeren Bauteilen ist diese Sicherheit unerlässlich, damit das Bauteil nicht beschädigt wird.
Der Bündigschneider wird so eng wie möglich an den Kanten der Supportstrukturen angesetzt und daraufhin schneidet man die Strukturen eine nach der anderen vom Bauteil weg. Diese Methode erfordert durch die höhere Genauigkeit allerdings auch mehr Zeit als die händische Entfernung.
Auch hier werden Noppen am Bauteil bleiben, jedoch mit ziemlicher Sicherheit weitaus kleinere als bei der händischen Entfernung. Dies sorgt für geringeren Zeitaufwand beim Schleifen, was die vorher mehr benötigte Zeit zur Entfernung der Supportstützen mindestens wieder ausgleicht.
Die letzte Möglichkeit, um Supportstrukturen zu entfernen, stellt wasserlösliches Resin dar. Mit diesem können die Supportstrukturen erzeugt werden, welche sich zeitgleich mit der Reinigung lösen.
Bei dieser Methode werden auch keinerlei Noppen übrigbleiben, wodurch das Schleifen mit Sandpapier vollständig wegfällt. Aus diesem Grund ist diese Methode ohne Zweifel die schnellste Art, um Supportstrukturen zu entfernen.
Das einzige Problem dabei ist, dass der genutzte 3D-Drucker die Möglichkeit haben muss, zwei Resine gleichzeitig zu verdrucken. Ein vollständig aus wasserlöslichem Resin gefertigtes Bauteil wäre schließlich nicht sonderlich zielführend.
Solche Drucker sind zumeist eher im professionellen oder industriellen Segment zu finden. Nur sehr wenige Hobby-3D-Drucker besitzen dieses Feature. Möchte man sich die Supportentfernung massiv erleichtern, ist es also ratsam, sich vor dem Kauf einer Druckanlage darüber zu informieren, ob diese mit mehreren Resinen drucken kann.
Sowohl Zeitaufwand als auch Schwierigkeit sind bei der Supportentfernung in den allermeisten Fällen geringer als bei der Reinigung des Resinbauteils. Eine große Schwierigkeit besitzt dieser Nachbearbeitungsschritt dennoch.
Diese Schwierigkeit liegt bei diesem Schritt jedoch mehr am Menschen als am Schritt selbst – nämlich an fehlender Achtsamkeit. Ein zu kraftvolles Ziehen oder ein unachtsames Schneiden kann schon ausreichen, um einem Bauteil schwerwiegende, im schlimmsten Fall irreparable Schäden zuzufügen.
Irreparabel ist hier aber auch das Stichwort – nur sehr wenige Schäden sind dies in diesem Schritt. Ein abgebrochenes Detail kann häufig neu ausgedruckt und mittels Nachhärtung an das eigentliche Bauteil angebracht werden. Die Gefahr eines vollständigen Verlusts des Bauteils ist dadurch in diesem Schritt der Nachbearbeitung weitaus geringer.
Nichtsdestotrotz bedeutet ein abgebrochenes Detail Ärger, Arbeit und Zeitaufwand. Daher ist in diesem Schritt vor allem eins geboten – Geduld und Vorsicht. Mit diesen zwei Eigenschaften können Supportstrukturen auch von komplexen Bauteilen ohne größere Probleme entfernt werden. Oder man setzt auf eine Druckanlage, welche zwei Resine gleichzeitig verdrucken kann und spart sich so die Notwendigkeit dieser zwei Eigenschaften – zumindest bei diesem Schritt.
Bei der Nachhärtung von Resinbauteilen wird die Temperatur des Bauteils erhöht, um mechanische Eigenschaften wie beispielsweise Hitzebeständigkeit, Festigkeit, UV-Beständigkeit und viele weitere zu verbessern.
Bevor wir zu den Methoden kommen, ist wichtig zu beachten, dass jedes Resin unterschiedlich lange Zeit bei der Nachhärtung benötigt. Daher muss vor diesem Schritt zwingend die Gebrauchsanweisung des Materialherstellers überprüft werden, um die benötigte Zeit einzuhalten – darauf kommen wir bei den Schwierigkeiten aber noch einmal genauer zu sprechen.
Die Nachhärtung kann durch viele verschiedene Methoden stattfinden. Die wichtigsten davon sind Sonneneinstrahlung sowie Nachhärtungsstationen verschiedenster Art.
Die „grüne Methode“ für die Nachhärtung von Resinbauteilen stellt ein simpler Aufenthalt an einem Ort mit dauerhafter und gleichmäßiger Sonneneinstrahlung dar. Ob ein Balkon, eine Terrasse oder ein Fenstersims - Hauptsache ein Ort mit viel Sonne!
Der Nachteil dieser Methode ist die weitaus höhere benötigte Zeit für diesen Nachbearbeitungsschritt. Während Nachhärtungsstationen ein paar Minuten für diesen Schritt benötigen, sind für die natürliche Methode mehrere Stunden nötig.
Auch das Aussehen der Oberfläche ist bei dieser Methode anders als bei den Nachhärtungsstationen. Während Nachhärtungsstationen eine glänzende Oberfläche produzieren, erhalten Bauteile, die durch Sonneneinstrahlung nachgehärtet wurden, eher eine matte, opake Oberfläche.
Diese Methode ist selbstverständlich nur für den Hobbygebrauch mit simplen Bauteilen geeignet. Und für Leute mit Zeit. Für Leute mit weniger Zeit (und mit mehr Geld), eignen sich Nachhärtungsstationen weitaus besser.
Nachhärtungsstationen sind speziell für die Nachhärtung von Resinbauteilen gefertigte Anlagen – zumindest meistens speziell dafür. Theoretisch lassen sich auch Nagellacktrockner, da diese mit UV-Licht arbeiten, als umgenutzte Nachhärtungsstation verwenden. Zeitlich benötigt dies natürlich länger als klassische Nachhärtungsstationen, aber die Ergebnisse können sich tatsächlich sehen lassen.
Nicht „nur sehen lassen“ benötigt dann aber professionelle Hilfe. Viele Anbieter von Resin 3D-Druckern bieten zusätzlich zu ihren Druckanlagen auch professionelle Nachhärtungsstationen, teilweise auch direkt in Kombination mit einer Waschstation, an. Diese gibt es in verschiedensten Größen, teilweise auch speziell für die händische Nutzung, um tiefsitzende Hohlräume präzise zu erreichen, und zu verschiedenen Preisen, von unter einhundert bis hin zu über zehntausend Euro.
In diese Nachhärtungsstationen wird das Bauteil, je nach Anbieter mit oder ohne Bauplatte, eingeführt und daraufhin von mehreren UV-Lampen gleichzeitig ausgehärtet. Die Zeit wird dabei manuell eingestellt, beträgt in den allermeisten Fällen aber unter 5 Minuten.
Diese professionelle Hilfe sorgt für die bestmöglichen Materialeigenschaften und ein gleichmäßig hochwertiges Oberflächenfinish. Für professionelle oder industrielle Produktion gibt es daher keine andere Wahl als solche Nachhärtungsstationen.
Werden nicht-professionelle Nachhärtungsmethoden verwendet, stellt die größte Herausforderung der gleichmäßige Nachhärtungsgrad dar. Einerseits um die mechanischen Eigenschaften durchgängig über das gesamte Bauteil zu haben, andererseits um ein einheitliches Oberflächenfinish zu gewährleisten.
Die einzige Möglichkeit, um dieser Schwierigkeit entgegenzuwirken, stellt die Kombination mit beispielsweise einem Turntable oder einem Schallplattenspieler dar. Dadurch wird das Bauteil in gleichmäßigem Tempo gedreht, wodurch das UV-Licht an alle Stellen im selben Maße hingelangt.
Auch die Zeit, die ein Bauteil nachhärten muss, ist bei nicht-professionellen Nachhärtungsmethoden etwas komplizierter als ein reines Ablesen der Zeit. Da die vom Hersteller vorgegebene Zeit zumeist auf professionelle Nachhärtungsstationen beruht, können diese auch nur dort angewandt werden.
Diese Schwierigkeit lässt sich nur mit einem entgegenwirken – Ausprobieren. Ein regelmäßiges Überprüfen des Bauteils, während es sich unter der UV-Lichtquelle befindet, sollte einem relativ bald Aufschluss darüber geben, wie lange das genutzte Resin mit der genutzten Nachhärtungsmethode benötigt, um den bestmöglichen Nachhärtungsgrad zu erreichen. Wird jedoch bei einem späteren Druck ein anderes Resin verwendet, muss dieses Ausprobieren erneut stattfinden.
Beide bisher genannten Schwierigkeiten beziehen sich auf die Nutzung von nicht-professionellen Nachhärtungsmethoden. Besitzen professionelle Nachhärtungsmethoden überhaupt Schwierigkeiten?
Kurz gesagt: Ja, aber keine allzu großen Schwierigkeiten. Der Nachhärtungsgrad wird durch die Einstrahlung aus mehreren UV-Lampen gleichzeitig auf allen Seiten kontinuierlich und die Aushärtungszeit lässt sich aus dem Materialleitfaden ablesen. Nichtsdestotrotz kann auch eine professionelle Nachhärtungsstation Fehler verursachen, gerade bei komplexen Bauteilen.
Sollte es bei einem Bauteil zu einem Fehler kommen, ist aber auch bei diesem Schritt selten ein irreparabler Schaden entstanden. Durch eine erneute Aushärtung lassen sich die allermeisten Fehler beheben – wenn auch, wie so oft, mit erhöhtem Zeitaufwand.
Die Nachbearbeitung von Resinbauteilen ist ein langwieriger Prozess. Die in diesem Blogpost behandelten Schritte beinhalten nur die Schritte, die unverzichtbar sind. Dazu könnte noch beispielsweise Lackieren, Einfärben, Polieren und viele weitere Schritte kommen, wenn sie benötigt oder gewollt sind.
Umso wichtiger ist es, dass die Nachbearbeitung gleich beim ersten Versuch funktioniert. Der sowieso schon hohe Zeitaufwand muss nicht noch durch Fehler und deren Ausbesserung weiter verlängert werden. Inzwischen bietet auch die Nachbearbeitung einige Automatisierungsmöglichkeiten, wodurch der Arbeitsaufwand und die Fehlerquote, und damit indirekt auch der Zeitaufwand, gesenkt werden kann.
Die Nachbearbeitung von Resinbauteilen steckt, ob nun mit oder ohne Automatisierungsmöglichkeiten, voller Tücken. Ich hoffe, ich konnte mit diesem Blogpost einige dieser Tücken aufdecken und adäquate Lösungswege vorlegen. Sollten Sie weitere Informationen über Nachbearbeitungslösungen für Resinbauteile benötigen, kann ich Ihnen dieses Webinar ans Herz legen.
Ansonsten wünsche ich viel Erfolg bei der Nachbearbeitung. Auf das all Ihre Bauteile ohne große Schwierigkeiten vollendet werden!