3D-Drucker
Hochwertige 3D-Drucker
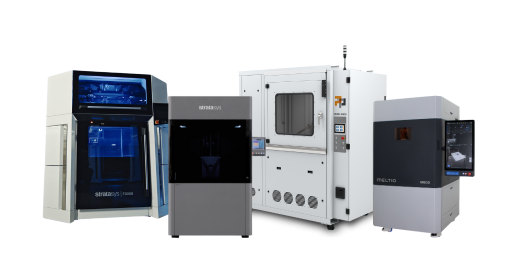
Die Digitalisierung des Fertigungsprozesses innerhalb der Metallverarbeitung begann einst in den frühen 1950er-Jahren. Mit der Entwicklung der ersten NC-Maschine von John T. Parsons in Kooperation mit dem Massachusetts Institute of Technology (MIT) wurde der Grundstein des Übergangs von manueller hin zur automatisierten, programmierbaren Steuerung für Maschinenabläufe gelegt.
Die Weiterentwicklung in CNC-Anlagen im Laufe der 70er war ein weiterer großer Sprung für die Rationalisierung der Fertigung. Nun konnten Maschinenabläufe nicht nur automatisiert, sondern auch schnell geändert sowie aus der Ferne überwacht werden.
In den späten 90ern kam schließlich die Additive Fertigung mit Metall auf den Markt und sorgte einmal mehr für Umdenken in der Produktion. Anstatt Bauteile subtraktiv und damit mit viel Materialausschuss und geringer Designfreiheit herzustellen, war es nun möglich, Bauteile quasi aus dem Nichts Schicht für Schicht aufzubauen.
Aufgrund der zeitlichen Abfolge sowie der Tatsache, dass die beiden Fertigungsmethoden im Grundsatz exakt gegensätzlich zueinander arbeiten, wird die Additive Fertigung bis zum heutigen Tage häufig als Konkurrenz, von manchen gar als vollumfänglicher Ersatz zu subtraktiven Herstellungsmethoden gesehen.
In diesem Blogpost möchte ich jedoch eine andere Sichtweise aufzeigen. Ich möchte die Vorzüge und Nachteile der beiden Fertigungsprozesse gegenüberstellen und somit eine einzigartige Symbiose präsentieren, welche durch die Verbindung der additiven und subtraktiven Fertigung ermöglicht werden.
Bei der subtraktiven Fertigung werde ich mich speziell CNC-Maschinen widmen, während die Additive Fertigung von laserbasierten Verfahren wie LMD (Laser Metal Deposition) repräsentiert wird. Sollten Sie bereits vollumfängliches Wissen zu beiden Arten der Fertigung besitzen, können Sie über den untenstehenden Button direkt zu den Einsatzgebieten der Symbiose springen.
Die subtraktive Fertigung ist eng mit der menschlichen Evolution verknüpft. Bereits vor Millionen von Jahren nutzten Urkulturen wie die Oldowan oder Lomekwi Steine und schlugen diese aneinander, um einfache Werkzeuge mit scharfen Kanten für die Jagd zu erhalten, und nutzten damit bereits das Grundprinzip der subtraktiven Fertigung.
Dieses Grundprinzip hat die Menschheit über ihre Existenz stetig weiterentwickelt, sodass wir heute nicht mehr Steine aneinanderschlagen, sondern programmierbare Anlagen besitzen, welche Metalle ohne menschlichen Eingriff präzise formen und gestalten können.
Dass die Vorteile dieser Fertigungsmethode vielfältig sind, ist allein daran zu erkennen, dass sie sämtliche Veränderungen in unserer Geschichte überdauert hat – von der Antike bis über die industrielle Revolution hinweg. Nichtsdestotrotz möchte ich hier die wichtigsten Vorteile kurz erläutern, um später die Symbiose mit der Additiven Fertigung zu untermauern.
Oberflächenqualität
Subtraktive Fertigungsmethoden erreichen herausragende Oberflächenqualität von bis zu 0,1 Ra/µm bei der Bearbeitung von Metall, vollständig ohne die Nutzung ausgiebiger Nachbearbeitungsprozesse – und selbst die Nachbearbeitungsprozesse, die potenziell anfallen können, können in CNC-Anlagen einfach direkt integriert sein, um menschlichen Aufwand zu minimieren.
Enge Toleranzen
Wenn es um Präzision geht, egal ob bei kleinen oder großen Bauteilen, ist die subtraktive Fertigung ungeschlagen. Selbst bei Standard-CNC-Anlagen sind Toleranzen von ±0,1 mm möglich und mit speziell auf Präzision ausgelegten Anlagen können sogar Toleranzen von ±0,0025 mm erreicht werden, was speziell in anspruchsvollen Industrien wie der Raumfahrt von höchster Wichtigkeit ist.
Skalierbarkeit für Serienproduktion
Als CNC-Anlagen in den 70er-Jahren die Metallverarbeitung im Sturm erobert haben, waren insbesondere die Kapazitäten für eine rationalisiertere Serienproduktion ein Segen für die Industrie. CNC-Anlagen vereinen eine Vielzahl von individualisierbaren Prozessschritten in einer einzelnen Umgebung, wodurch problemlos mehrere Bauteile zeitgleich produziert werden können.
Materialvielfalt
Materialeinschränkungen sind im Bereich der subtraktiven Fertigung ein Fremdwort. Egal ob hochfeste Legierungen, MMC (Metal Matrix Composites), Superlegierungen oder reflektierende Metalle – CNC-Anlagen können all diese Materialien und noch viele mehr problemlos verarbeiten.
Wie bei allem in der Welt, gibt es auch bei der subtraktiven Fertigung leider einige Nachteile, welche die Möglichkeiten einschränken – und um ein vollumfängliches Bild zu geben, werde ich auch hier die Wichtigsten nennen.
Materialausschuss
Einer der größten Nachteile bei der subtraktiven Fertigung ist der hohe Anteil an Materialausschuss. Selbst bei sehr simplen Bauteilen liegt die Ausschussrate häufig bei 50 %, welche bei komplexeren Bauteilen sogar auf bis zu 90 % ansteigen kann, was selbstverständlich zu weitaus höheren Kosten führt.
Individualisierung
CNC-Anlagen sind hochgradig anpassbar, keine Frage. Jedoch ist jede Anpassung und das damit einhergehende Umrüsten und Umprogrammieren mit einem Zeit- und Kostenaufwand verbunden, was kleine Produktionsläufe oder kurzfristige Änderungen wirtschaftlich sehr unrentabel macht.
Designeinschränkungen
Die subtraktive Fertigung brilliert zwar bei Großbauteilen, feinen Details und Serienproduktion, wenn es allerdings um sehr komplexe Designs geht, können CNC-Anlagen diese nicht umsetzen. Speziell bei innenliegenden Strukturen, Kanälen oder schlangenförmigen Geometrien kommen CNC-Anlagen rasch an ihre Grenzen.
Während die subtraktive Fertigung die Menschheit durch ihre Evolution begleitet hat, kam die Additive Fertigung erst in den frühen 1980ern zu Tage. Dr. Hideo Kodama vom Nagoya Municipal Industrial Research Institute in Japan meldete 1980 das erste Patent für einen additiven Fertigungsprozess an, wobei sein Projekt anhand fehlender finanzieller Mittel jedoch scheitern sollte.
1986 meldete Chuck Hull schließlich sein Patent zur Stereolithografie an, welches 1988 zum ersten Mal kommerzialisiert wurde. Es folgten eine Reihe an Entwicklungen und neuen Technologien, bis Mitte der 90er auch die Metallverarbeitung additiv möglich wurde – speziell dank Errungenschaften des Fraunhofer Institut ILT in Aachen und dem schwedischen Unternehmen Arcam.
Innerhalb der nunmehr 30 Jahre seit Erstentwicklung wurde innerhalb des Metall-3D-Drucks viel Fortschritt vorangebracht. Daher hat sich die Nutzung der additiven Metallverarbeitung stetig weiter ausgebreitet – und die Hauptgründe dieser Ausbreitung werde ich nun ausführen.
Ressourcenschonende Fertigung
Metalle können kostspielig sein, das muss ich wahrscheinlich keinem erklären. Daher ist es für metallverarbeitende Unternehmen unabdingbar, die Fertigung so ressourcenschonend wie möglich zu gestalten – und die Additive Fertigung ist ideal dafür. Durch den schichtweisen Aufbau werden nur sehr geringe Mengen an Metallpulver bzw. -draht verschwendet, was zu einem durchschnittlichen Ausschuss von nur 5 % führt.
Designfreiheit
Ein weiterer einzigartiger Vorteil der additiven Metallverarbeitung ist die unbeschränkte Designfreiheit. Ingenieure und Anwender können ihre Ideen nach Belieben umsetzen, ohne sich Gedanken machen zu müssen, ob die Anlage die jeweilige Geometrie auch abbilden kann. Innenliegende Wabenstrukturen, komplexe Formen, feine Details – mit der Additiven Fertigung lässt sich alles einfach und schnell umsetzen.
Individualisierung
Durch eine werkzeuglose Fertigung sind auch die Individualisierungsmöglichkeiten beim 3D-Druck grenzenlos. Das einzige „Umrüsten“, was potenziell erforderlich ist, um vollständig unterschiedliche Bauteile zu erstellen, ist ein Materialwechsel – und dieser ist, je nach Anlage, in einigen Sekunden bis einigen Minuten vollständig erledigt. Somit kann rasch zwischen Projekten gewechselt und auch eine rapide Anpassung auf sich ändernde Trends ist sofort möglich.
Leichtgewichtige Bauteile
Der finale Vorteil hängt zwar eng mit der Designfreiheit zusammen, muss aber im Bereich der Metallverarbeitung zweifellos auch einzeln genannt werden. Dank der Möglichkeit, Topologieoptimierungen ohne Designeinschränkungen umsetzen zu können, können für Industrien wie die Luft- und Raumfahrt oder die Automobilindustrie Komponenten erschaffen werden, die sehr geringes Gewicht aufweisen – ohne mechanische Leistungsfähigkeit und Festigkeit zu beeinflussen.
Wäre die Additive Fertigung völlig frei von Nachteilen, wäre sie wohl inzwischen in jeder einzelnen Industrie der Standard. Warum dies noch nicht der Fall ist, werde ich anhand der folgenden Nachzüge erläutern.
Nachbearbeitungsaufwand
Während der Druck selbst bei der Additiven Fertigung inzwischen sehr schnell vonstattengeht, müssen 3D-gedruckte Bauteile immer mindestens einen, wenn nicht sogar mehrere Nachbearbeitungsschritte, beispielsweise die Supportentfernung oder Reinigung, durchlaufen. Zwar lässt sich diese Nachbearbeitung inzwischen hochgradig automatisieren, nichtsdestotrotz ist dieser Prozess natürlich mit Zeit- und Kostenaufwand verbunden.
Oberflächengüte
Im Bereich des Kunststoff-3D-Drucks sind inzwischen herausragende Oberflächengüten möglich, speziell mit Verfahren wie SLA oder PolyJet™. Beim Metall-3D-Druck bleibt die Oberflächengüte jedoch weiterhin hinter der bei subtraktiven Fertigungsmethoden zurück. Speziell der „Treppeneffekt“, der bei steilen Winkeln auftritt, bei dem die Oberfläche durch den schichtweisen Aufbau nicht vollständig glatt ist, sondern eine treppenartige Struktur aufweist, kann die Oberflächenqualität stark trüben. Dieser Effekt lässt sich zwar mit Nachbearbeitung entfernen – aber wie zuvor bereits erwähnt, ist dies immer mit Zeit und Kosten verbunden.
Materialeinschränkungen
Die Materialvielfalt rund um Metall in der Additiven Fertigung hat sich in den vergangenen Jahren enorm erweitert und wird diesen Trend auch in Zukunft fortsetzen. Zum jetzigen Zeitpunkt sind einige weit verbreitete Materialien jedoch immer noch nicht einfach per 3D-Druck verarbeitbar – speziell reflektierende Metalle wie Bronze und Kupfer können den zumeist mit Laser arbeitenden 3D-Druckern Schwierigkeiten bereiten.
Wie bereits aus der Auflistung der Vor- und Nachteile ersichtlich wurde, decken sich die beiden Fertigungsmethoden beinahe perfekt gegenseitig ab. CNC brilliert bei Großserien mit simpleren Strukturen, Additive Fertigung bei Einzelstücken und Kleinserien mit komplexen Geometrien. CNC bietet hervorragende Oberflächen, verursacht jedoch viel Materialausschuss, währenddessen Additive Fertigung beim Ausschuss glänzt, bei der Oberflächengüte jedoch zurückstecken muss.
Diese beiden Prozesse sind meiner Meinung nach also keineswegs als Konkurrenz oder Ersatz zueinander anzusehen – vielmehr spielen sie perfekt ineinander, um die Nachteile des Anderen auszugleichen, ohne dabei ihre eigenen Vorteile zu minimieren.
Im letzten Abschnitt dieses Blogposts soll es nun darum gehen, wie ein hybrider Ansatz der Metallfertigung genau aussieht, welche verschiedenen Einsatzmöglichkeiten dafür existieren und wie er in verschiedensten Stufen des Produktentwicklungszyklus zum Einsatz kommen kann.
Prototyping
Als die Additive Fertigung einst entworfen wurde, damals noch mit einem alleinigen Fokus auf Kunststoffe, war sie vor allem als Werkzeug für Rapid Prototyping gedacht. Trotz der erweiterten Möglichkeiten, die mit dem 3D-Druck inzwischen möglich sind, ist Rapid Prototyping weiterhin ein ideales Einsatzgebiet dafür – und auch für die hybride Metallfertigung.
Der 3D-Druck dient hier als idealer Startpunkt für das Rapid Prototyping. Damit können sehr schnell die ersten Design- und Funktionsprototypen gedruckt werden, bei denen für Anpassungen nur das digitale Modell sowie gegebenenfalls das Material gewechselt werden muss.
Sobald der erste Validierungsprozess durch den 3D-gedruckten Prototyp abgeschlossen ist, kann nun die CNC-Anlage zum Einsatz kommen. Damit können Oberflächenfinish verbessert, Konturen verfeinert und mechanische Merkmale wie beispielsweise kleine Gewindeeinsätze präzise hinzugefügt werden.
Der nun fertiggestellte Prototyp wird daraufhin natürlich noch einmal auf Herz und Nieren überprüft. Im besten Fall besteht er alle Funktionstestungen, aber selbst wenn nicht, ist die Anpassung dank der Nutzung des 3D-Drucks so einfach und schnell wie nie zuvor.
Im Bereich der Prototyping profitiert die hybride Fertigung insbesondere von den beschleunigten Iterationszyklen mittels 3D-Druck, wodurch langwierige Umrüstzeiten, die bei CNC-Anlagen anfallen könnten, verhindert werden. Somit kann der Prototypingprozess massiv beschleunigt werden, wodurch Veränderungen im Markt- oder Nachfrageverhalten weitaus schneller umgesetzt werden können.
Komplexe Endverbrauchsteile
Egal ob Luft- und Raumfahrt, Automobilindustrie, Motorsport, Medizintechnik und viele weitere Industriezweige – viele Komponenten werden stetig komplexer, da beispielsweise mehr Energieeffizienz, Komfort oder Leistungsfähigkeit benötigt werden. Die hybride Fertigung hilft dabei, diese steigende Komplexität abzubilden, ohne Abstriche bei anderen Eigenschaften machen zu müssen.
Auch hier ist der 3D-Druck der Ausgangspunkt. Hiermit kann die Basis des Bauteils mit allen möglichen komplexen Strukturen und Geometrien innen sowie außen vollständig hergestellt werden. Werden komplexe Strukturen nur innenliegend benötigt, beispielsweise Kühlkanäle, kann der äußere Bereich auch einfach als Block gedruckt werden, der zum Schluss vollständig von der CNC-Anlage bearbeitet wird.
Egal, ob das Bauteil nun nur innen, nur außen oder sowohl als auch komplexe Strukturen aufweist, die CNC-Maschine übernimmt zumeist einen ähnlichen Schritt wie beim Prototyping – nämlich den finalen Schliff an Oberfläche, Konturen und gegebenenfalls auch das Hinzufügen mechanischer Merkmale.
Bei komplexen Endverbrauchsteilen wird der Vorteil des 3D-Drucks, unbegrenzte Designfreiheit zu bieten, direkt mit der herausragenden Oberflächengüte und Präzision der subtraktiven Fertigung zu kombiniert. Dadurch können einzigartige Designs umgesetzt werden, die beispielsweise dabei helfen, Komponenten leichter zu machen oder den Tragekomfort zu erhöhen.
Reparaturen
In vielen metallverarbeitenden Industrien sind Ausfallzeiten mit horrenden Kosten verbunden. Insbesondere in Branchen wie der Luftfahrt oder dem Motorsport sind schnelle Reaktionszeiten gefragt, wenn ein Bauteil Schäden erhalten hat – und mit der hybriden Fertigung kann diese Frage zweifellos beantwortet werden.
Welche der beiden Fertigungsmethoden hierbei beginnt, hängt eng mit dem jeweiligen Schaden zusammen. Bei Schäden aufgrund von Verformungen, Abrieb und Verschleiß kommt die CNC-Anlage zuerst zum Einsatz, damit die betroffene Stelle zunächst per Fräsen oder Schleifen auf eine einheitliche, bearbeitbare Ebene gebracht werden kann.
Daraufhin nimmt sich der 3D-Drucker der Sache an und beginnt die nun fehlende Struktur präzise direkt auf die jeweilige Stelle zu drucken. Sobald dieser Prozess fertig ist, wird das Bauteil einmal mehr in die CNC-Anlage gespannt, um dort, wenn nötig, die Oberfläche und Konturen zu verbessern.
Bei kleineren Schäden wie Rissen oder Brüchen beginnt der 3D-Druck direkt, indem er in die betroffenen Stellen Material einführt. Die CNC-Maschine ist danach einmal mehr dazu da, um die Oberfläche und Konturen zu finalisieren – wobei je nach Größe der Schäden auch alleine der 3D-Druck ausreichen kann.
Die Gegensätzlichkeit der beiden Fertigungsverfahren ist ideal, um Reparaturen schnell und kostengünstig zu erledigen. Kaum manueller Aufwand, geringer Materialverschleiß, hohe Geschwindigkeit – all diese Vorteile werden bei Reparaturen durch die Nutzung der hybriden Fertigung ermöglicht.
Oberflächenbeschichtungen
Oberflächenbeschichtungen sind in Hochleistungsanwendungen essenziell. Damit können unter anderem Bauteile hergestellt werden, bei denen kostenintensive Hochleistungsmaterialien nur dort eingesetzt werden, wo sie tatsächlich benötigt werden. Außerdem können natürlich auch ältere Bauteile mit einer neuen, leistungsfähigeren Oberfläche ausgestattet werden.
Für Oberflächenbeschichtungen gibt es eine Vielzahl an verschiedensten Verfahren, die jedoch alle zumeist entweder mit hohem Aufwand oder hohen Kosten einhergehen. Gewisse Verfahren müssen aufgrund der hohen Sicherheitsanforderungen auch häufig ausgelagert werden, was weitere Kosten und potenziell auch Lieferkettenschwierigkeiten nach sich zieht – doch mit Hilfe der hybriden Fertigung können präzise Beschichtungen einfach, kostengünstig und In-House stattfinden.
Der 3D-Druck übernimmt hier einmal mehr die Vorreiterrolle, indem er auf das jeweilige Bauteil Schicht für Schicht das jeweilige Material aufträgt. Durch die Nutzung von Technologien wie LMD (Laser Metal Deposition), bei der ein Schmelzbad zur Auftragung und Verbindung erzeugt wird, entsteht eine vollständig Dichte, neue Oberfläche aus dem neuen Material, die anderen herkömmlichen Verfahren in nichts nachsteht.
Die CNC-Maschine übernimmt hierbei einmal mehr die Stelle des finalen Schliffs ein, um die frische Oberfläche zu optimieren und somit sowohl Aussehen als auch Leistungsfähigkeit zu steigern.
Die Symbiose aus additiver und subtraktiver Fertigung schlägt in diesem Fall in eine sehr ähnliche Kerbe wie bei der Reparatur. Durch die gegensätzliche Art der Fertigung komplettieren sich diese beiden Fertigungsmethoden ideal, um den Prozess der Oberflächenbeschichtungen zu vereinfachen.
Werkzeug- und Formenbau
Zu guter Letzt muss bei den Profiteuren eines hybriden Fertigungsansatzes der Werkzeug- und Formenbau genannt werden. Speziell wenn es um Formen mit Kühlkanälen oder Spritzgussformen für komplexe Geometrien geht, kommt die subtraktive Fertigung alleine nur mit sehr viel Aufwand zum Ziel – die hybride Fertigung hingegen macht es so einfach wie nie zuvor.
Die Additive Fertigung mit Metall beginnt einmal mehr mit der Herstellung der Form. Dabei kommt der Designfreiheit einmal mehr eine essenzielle Rolle zu, aber auch die Fähigkeit, mehrere Materialien zeitgleich zu verarbeiten, die manche Metall-3D-Drucker besitzen, kann für verbesserte Ergebnisse genutzt werden.
Sobald das Werkzeug oder die Form fertig gedruckt ist, geht es beim CNC-Prozessschritt speziell um Präzisionsarbeit. Werkzeuge und Formen benötigen stets engste Toleranzen und mit der CNC-Maschine kann das 3D-gedruckte Bauteil verbessert werden, indem beispielsweise Trennlinien und Kern-Kavitäten-Schnittstellen bearbeitet werden.
Das Ergebnis sind außergewöhnliche Werkzeuge und Formen, die mit konturnahen Kühlkanälen, komplexen Kavitäten, internen Mustern, Multimaterialfähigkeit und vielem mehr glänzen können.
Speziell bei dieser Anwendung werden die Vorteile der beiden Fertigungsmethoden – die Designfreiheit beim 3D-Druck und die Präzision bei CNC-Anlagen – bis zum Anschlag ausgereizt. Die hybride Fertigung macht somit möglich, was zuvor unmöglich war, ohne dafür horrende Kosten in Kauf zu nehmen.
Die von mir genannten Anwendungsgebiete der hybriden Fertigung sind nur die Spitze des Eisbergs. Es gibt noch Dutzende weitere, spezifischere Anwendungsgebiete, in denen die Verknüpfung zwischen additiver und subtraktiver Fertigung Höchstleistungen ermöglicht.
Ich hoffe, ich konnte mit diesem Blogpost darlegen, dass die additive und subtraktive Fertigung keineswegs nur Konkurrenz zueinander sind, sondern auch ideal Zusammenarbeiten können, um die Vorteile beider Seiten zu bündeln.
Unsere Lösung für die hybride Fertigung stammt vom spanischen Unternehmen Meltio mit ihrer Engine CNC Integration. Damit wird ein Druckkopf einfach in eine bereits bestehende CNC-Anlage integriert und bietet somit eine kostengünstige Möglichkeit, nahtlos zur hybriden Fertigung überzugehen. Weitere Informationen zur Meltio Engine CNC Integration finden Sie hier.
Vielen Dank für Ihre Aufmerksamkeit – und bis zum nächsten Blogpost!