3D-Drucker
Hochwertige 3D-Drucker
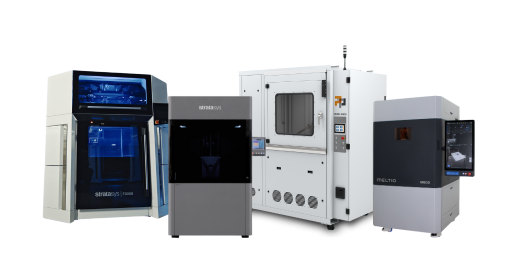
Im dritten Teil dieser Blogreihe rund um die Materialien der verschiedenen 3D-Druck-Technologien widmen wir uns heute den unterschiedlichen Arten von Polymer-Pulvern, deren Eigenschaften sowie deren Anwendungsgebieten.
Trotz der langen Verfügbarkeit dieser 3D-Druck-Technologie, allen voran das SLS-Verfahren, welches 1986 von Dr. Carl Deckard und Dr. Joe Beaman patentiert und 1992 mit der „Sinterstation 2000“ kommerzialisiert wurde, ist die Materialauswahl im Vergleich zum Filament- oder Resin-3D-Druck relativ gering.
Dies kommt vor allem daher, dass Polymer-Pulver für den 3D-Druck sehr genaue Spezifikationen erfüllen muss. Beispielsweise muss die Partikelgrößenverteilung sehr exakt sein, es muss spezielle Fließeigenschaften aufweisen und muss hohen Temperaturen standhalten können, um beim Druckprozess nicht seine Eigenschaften zu verlieren.
Nichtsdestotrotz konnte sich der Pulver-3D-Druck in vielen Industrien durchsetzen. Dies liegt unter anderem an dem sehr sparsamen Materialverbrauch dank Recyclingfähigkeit ungenutzten Pulvers, der grundsätzlich bei allen Pulvern hohen Hitzebeständigkeit und der herausragenden Druckgeschwindigkeit.
Aber es soll hier nicht um die Vorteile der Verfahren selbst gehen, sondern um die Vorteile der Materialien. Dafür werde ich die Materialien in drei Oberkategorien einteilen – einmal nylonbasierte Pulver, einmal Spezialpolymere und einmal Verbundwerkstoffe. Über den untenstehenden Button können Sie direkt zu den Spezialpolymeren oder den Verbundwerkstoffen springen, sollten Sie über nylonbasierte Pulver bereits ausgiebiges Wissen verfügen.
Seit der ersten Kommerzialisierung 1938 durch das US-amerikanische Unternehmen DuPont ist Nylon aus unser aller Leben nicht mehr wegzudenken. Ob bei Textilien, Haushaltsgeräten, industrieller Fertigung oder in der Medizin – Nylon ist so essenziell, dass es 1945 und 1946 sogar zu den sogenannten „Nylon Riots“ gekommen ist, als die Produktion von Nylontextilien nicht die extraordinäre Nachfrage stillen konnte.
Nylonbasierte Pulver, speziell PA12, waren auch die ersten Pulver, die für die Additive Fertigung verwendet wurden, weswegen wir uns diese hier zuerst anschauen. In dieser Kategorie werden wir uns PA6, PA11 und PA12 anschauen – begonnen mit dem mechanisch leistungsfähigsten Nylonmaterial.
PA6 ist ein halb-kristallines Polyamid, das aus der Polymerisation von Caprolactam hergestellt wird, welches das erste Mal 1938 vom deutschen Erfinder Paul Schlack synthetisiert wurde. Im 3D-Druck ist PA6 ein sehr leistungsfähiges, aber dennoch seltener als andere nylonbasierten Materialien genutztes Polymer-Pulver.
PA6 besticht dabei insbesondere mit seinen mechanischen Fähigkeiten. Das Material besitzt eine sehr hohe Festigkeit, Steifigkeit und Zähigkeit und ist außerdem sehr resistent gegen mechanische Belastungen, Verschleiß und Abrieb. Des Weiteren besitzt es eine hohe Hitzebeständigkeit von 220 bis 230 °C.
Zusätzliche positive Eigenschaften umfassen die Resistenz gegen eine große Anzahl von Chemikalien, Öle und Fette sowie der im Vergleich zu anderen nylonbasierten Materialien sehr niedrige Preis mit durchschnittlich 30 bis 60 Euro pro Kilogramm.
Warum aber wird PA6, trotz dieser Vorteile, seltener als andere nylonbasierte Pulver genutzt? Dies liegt vor allem an der hohen Verarbeitungsschwierigkeit. PA6 neigt zu Verzug, was eine exakte Kontrolle der Prozessparameter erfordert, besitzt eine hohe Hygroskopizität, was eine ordnungsgemäße Trocknung vor Verarbeitung voraussetzt, und ist auch in der Nachbearbeitung aufgrund der hohen Dichte und Härte eher störrisch. Zusätzlich hat PA6-Pulver die geringste Wiederverwendbarkeitsrate im Vergleich mit anderen nylonbasierten Pulvern.
Trotz dieser schwierigen Verarbeitung konnte sich PA6 aber zweifellos einen Namen in verschiedenen Industrien und Anwendungsgebieten machen. Speziell in der Maschinenbauindustrie haben die hervorragenden mechanischen und thermischen Eigenschaften die schwierige Verarbeitung überflügelt, wodurch inzwischen Zahnräder, Antriebskomponenten, Lagergehäuse aber auch Werkzeuge und Formen mit PA6-Pulver produziert werden.
Weitere Anwendungsgebiete von PA6-Pulver umfassen die Automobilindustrie, wo beispielsweise Luftansaugkanäle, Befestigungen und Abdeckungen mit PA6 additiv produziert werden, und das branchenübergreifende Rapid Prototyping für Prototypen, die mechanischen Belastungen standhalten müssen.
Wenn es um umweltfreundliche Produktion geht, ist PA11 ein wahres Wundermittel. Dieses Pulver wird aus regenerativem Rizinusöl hergestellt und ist somit weitaus umweltschonender als erdölbasierte Polymere.
Neben seiner Umweltfreundlichkeit trumpft PA11 vor allem mit seiner hohen Flexibilität und Duktilität auf. Es besitzt auch eine sehr gute Schlagzähigkeit und Bruchdehnung, wodurch mechanische Stöße und Schläge zum Kinderspiel werden – auch bei perpetuell wiederkehrenden Belastungen, dank hoher Langlebigkeit und sehr geringer Sprödigkeit.
Außerdem besitzt PA11 eine sehr gute Chemikalienresistenz, hohe Beständigkeit gegen UV-Strahlung und Witterungsbedingungen und ist im Gegensatz zu PA6 weitaus leichter zu verarbeiten dank geringerem Verzug und weniger Feuchtigkeitsempfindlichkeit.
Wo PA11 jedoch eindeutig den Kürzeren zieht ist beim Thema Hitzebeständigkeit. Mit einer Wärmeformbeständigkeit von bis zu 190 °C zwar weiterhin alles andere als niedrig, aber im Vergleich zu anderen Polymer-Pulvern dennoch im niedrigeren Bereich. Zusätzlich ist PA11 mit einem Preis von 70 bis 120 Euro pro Kilogramm das preisintensivste nylonbasierte Pulver und die Nachbearbeitung kann sich aufgrund der Flexibilität ebenfalls als schwierig gestalten.
Durch die Kombination aus Flexibilität und Schlagzähigkeit konnte sich PA11 unter anderem in der Luft- und Raumfahrt behaupten. Dabei kann es für eine Vielzahl von nicht-strukturellen Bauteilen verwendet werden, beispielsweise Kabelkanäle, Schutzabdeckungen, Dichtungen und viele weitere.
Ebenfalls kommt PA11 häufig in der Medizintechnik zum Einsatz, da es biokompatibel und mehrfach sterilisierbar ist. Dabei kann es sowohl für medizinische Instrumente als auch für Indikationen wie Prothesen oder Orthesen verwendet werden. Auch bei Outdoor-Anwendungen ist PA11 aufgrund seiner sehr hohen Witterungsbeständigkeit sehr beliebt.
PA12 wird aus der Polymerisation von Laurinlactam gewonnen und ist ein teilkristallines Polyamid. PA12 war zur Entwicklung des Pulver-3D-Drucks das Material schlechthin und hat sich bis heute in einer breiten Palette von Anwendungen behaupten können.
Der Hauptgrund für die frühe Nutzung dieses Materials liegt in der sehr einfachen Verarbeitbarkeit von PA12. Das Material gilt als das am einfachsten zu druckende Polymer-Pulver, da es kaum Verzug, eine herausragende Prozessstabilität und eine sehr geringe Feuchtigkeitsaufnahme besitzt. Auch die Nachbearbeitung ist außergewöhnlich simpel, wodurch PA12-Bauteile sehr leicht geschliffen, gebohrt oder lackiert werden können.
Eine einfache Verarbeitbarkeit allein hätte jedoch nicht ausgereicht, um sich durchgängig zu behaupten. Dafür hat PA12 seine mechanischen Eigenschaften, die eine sehr gute Balance aus Steifigkeit und Flexibilität liefern. Zusätzlich besitzt PA12 eine gute Schlagzähigkeit sowie eine hohe Beständigkeit gegen Chemikalien, UV-Strahlung und Witterung.
PA12 ist jedoch nur bedingt gegen Brüche bei dauerhaften mechanischen Belastungen geschützt. Auch hohe Temperaturen machen PA12 zu schaffen, da es eine Wärmeformbeständigkeit von maximal 182 °C besitzt. Außerdem ist PA12 mit einem Preis von 60 bis 100 Euro im Mittelfeld anzusiedeln, wobei PA12 hervorragend recyclebar ist, wodurch es insbesondere bei großen Produktionsvolumina trotz der höheren Einstiegspreise zu Kosteneinsparungen kommt.
Durch seine ausgewogenen Eigenschaften und sehr einfache Verarbeitung kommt PA12 bevorzugt beim Prototyping zum Einsatz. Über alle Industrien hinweg können mit PA12 Funktions- und Designprototypen schnell erstellt und auch schnell abgeändert werden. Speziell beim Massenprototyping in der Automobilindustrie oder Luftfahrt hat sich PA12 bewährt.
Des Weiteren findet PA12 auch häufig bei Konsumgütern, speziell im Außenbereich, Verwendung, beispielsweise für Brillengestelle, Elektronikgehäuse oder auch bei Haushaltsgeräten. Außerdem wird es auch gerne für Halterungen, Werkzeuge und andere Fertigungshilfsmittel genutzt, bei denen ein gewisses Maß an Flexibilität nötig ist.
Eine kurze Erwähnung sollte hier ebenfalls glasfaserverstärktes PA12, zumeist als PA12 GF abgekürzt, finden, da sich dieses immer größerer Beliebtheit erfreut. Durch die Kombination mit den Glasfasern wird nämlich die Festigkeit massiv erhöht, ohne dabei jedoch das Bauteil schwerer zu machen, weswegen es insbesondere in der Automobilindustrie und der Luftfahrt für leichtgewichtige und dennoch feste Bauteile genutzt wird.
Während nylonbasierte Pulver sehr weitflächig eingesetzt werden können, sind nachfolgende Materialien eher auf spezifischere Anwendungsgebiete zugeschnitten und besitzen zumeist einzigartige Eigenschaften, in welchen sie brillieren.
In dieser Kategorie werden wir uns ebenfalls drei verschiedene Pulverarten anschauen – TPE / TPU, PP und PEEK, begonnen mit dem Material der Wahl für Elastizität!
TPE, oder thermoplastische Elastomere, ist ein Überbegriff für mehrere Materialien, inkludierend TPA, TPC und TPU. Da im Bereich der Polymer-Pulver zumeist TPU, ergo thermoplastisches Polyurethan, genutzt wird, werden wir uns auch auf dieses Material fokussieren.
TPU besticht allen voran mit seiner außergewöhnlichen Elastizität. Diese, in Kombination mit der hervorragenden Rückstellkraft und Abriebfestigkeit, sorgt dafür, dass Komponenten sich bei mechanischen Belastungen sehr weit dehnen können, ohne zu brechen oder auf Dauer ihre mechanischen Eigenschaften zu verlieren, und daraufhin eigenständig wieder in ihre originäre Position zurückspringen.
Zusätzlich ist TPU beständig gegen sehr viele Öle, Fette und Lösungsmittel, bietet mit einer Wärmeformbeständigkeit von bis zu 220 °C sehr gute Voraussetzungen für den Einsatz bei Hochtemperaturanwendungen und ist dank Beständigkeit gegen UV-Strahlung auch für gewisse Außenanwendungen geeignet.
TPU-Pulver ist dafür jedoch schwierig zu verarbeiten, sogar schwerer als PA6. Durch die Elastizität neigt das Material zu Verzug und auch die Schichtadhäsion kann Probleme verursachen, weswegen ein exakt auf dieses Material angepasster Prozess von Nöten ist. Auch die Nachbearbeitung ist durch die Flexibilität relativ aufwendig und der Preis ist mit 60 bis 120 Euro pro Kilogramm im oberen Mittelfeld.
Dank seiner Elastizität und Rückstellkraft bietet sich TPU-Pulver industrieübergreifend besonders gut für Stoßdämpfer an. Ob in der Luftfahrt, der Automobilindustrie oder für Schutzausrüstung im Leistungssport – TPU macht langlebig elastische Bauteile möglich.
Weitere Anwendungsgebiete umfassen die Konsumgüterbranche, in der mit TPU-Pulver unter anderem Schutzhüllen, Schuhsohlen oder flexible Kleidungsaccessoires hergestellt werden können, und die Robotik, wo TPU ideal für flexible Greifer oder Gelenkmanschetten geeignet ist.
Polypropylen ist einer der am weitverbreitetsten Kunststoffe weltweit und ist insbesondere in der Verpackungsindustrie nicht mehr wegzudenken und auch in die Welt der Additiven Fertigung hat PP inzwischen seinen Fußabdruck setzen können.
Dieser Fußabdruck ist vor allem der sehr geringen Dichte von PP zu verdanken, die bei durchschnittlich 0,9 g/cm³ liegt. Dadurch ermöglicht PP die Herstellung sehr leichter und dennoch mechanisch belastungsfähiger Bauteile, dank einer hohen Zähigkeit und Schlagfestigkeit.
Zusätzlich nimmt PP so gut wie gar keine Feuchtigkeit auf, was die mechanischen Eigenschaften und die Dimensionsstabilität auch unter Feuchtigkeit auf einem hohen Niveau hält, und ist außergewöhnlich beständig gegen Chemikalien, einschließlich Säuren, Basen, Lösungsmitteln und Fetten. PP ist außerdem mit einem Preis von 30 bis 60 Euro pro Kilogramm und guten Recyclingeigenschaften sehr kosteneffizient.
Wo PP jedoch schwächelt ist in puncto Steifigkeit, wo es nur moderate Werte erreicht, ohne dabei eine extraordinäre Flexibilität zu besitzen. Mit einer Wärmeformbeständigkeit von unter 170 °C ist es zusätzlich nicht für Anwendungen unter sehr hohen Temperaturen geeignet und die Verarbeitung von PP ist dank hoher Neigung zu Verzug und Schrumpfung relativ schwierig.
Genau wie bei der traditionellen Fertigung hat PP im 3D-Druck seine Hauptfunktion in der Verpackungsindustrie gefunden. Egal ob recyclebare Behälter und Flaschen, Schutzverpackungen oder flexible Verpackungen, mit PP in der Additiven Fertigung wird umweltfreundliche Herstellung und leistungsfähige Anwendung ermöglicht.
PP kommt ebenfalls häufig für Fluidbehälter, beispielsweise in der Automobilindustrie als Wischwasser- oder Kühlmittelbehälter, zum Einsatz dank seiner Beständigkeit gegen Feuchtigkeit und Chemikalien und auch in der Landwirtschaft wird PP unter anderem für Bewässerungssystemkomponenten und Schutzfolien verwendet.
PEEK ist eines der neuesten Materialien innerhalb der Additiven Fertigung und hat seinen Weg bis dato vor allem in den Filament-3D-Druck gefunden – aber auch bei Polymer-Pulvern gibt es inzwischen die Möglichkeit, PEEK zu verarbeiten.
Dieses Material brilliert dabei mit einzigartigen mechanischen und thermischen Fähigkeiten. Mit einer beispiellosen mechanischen Festigkeit, Steifigkeit und Verschleißbeständigkeit sowie einer Wärmeformbeständigkeit von bis zu 280 °C ist es für Hochleistungsanwendungen die perfekte Wahl.
Ebenfalls besticht PEEK mit einer hervorragenden Beständigkeit gegen eine Vielzahl von Chemikalien und Gamma-Strahlung. Außerdem ist PEEK inhärent flammhemmend, wodurch es selbst strengste Brandschutzvorschriften ohne Probleme erfüllt, und ist biokompatibel.
Während bereits TPU oder PP als schwierig zu verarbeiten beschrieben wurden, setzt PEEK dieser Beschreibung die Krone auf. Mit Schmelztemperaturen von über 340 °C werden sehr spezielle Druckanlagen benötigt, um das Material überhaupt verarbeiten zu können. Zusätzlich ist PEEK mit einem Preis von 300 bis 600 Euro pro Kilogramm zweifellos das kostenintensivste Polymer-Pulver auf dem Markt.
PEEK bietet die einzigartige Möglichkeit, funktionelle Bauteile für die Raumfahrt zu produzieren. Dank den herausragenden mechanischen, thermischen und chemischen Eigenschaften bieten PEEK-Bauteile die nötige Stabilität und Sicherheit, um in diesem Anwendungsgebiet Bauteile wie Dichtungen, Ventile und Strukturbauteile herzustellen.
Ein weiterer großer Einsatzbereich bietet PEEK in der Medizintechnik. Dank seiner Biokompatibilität kann es sowohl für Instrumente als auch für Implantate eingesetzt werden. Außerdem lässt sich PEEK auch sehr gut in der Luftfahrt, der Automobilindustrie und der Elektronikbranche nutzen.
Bei Verbundwerkstoffen wird ein Matrixmaterial, beispielsweise ein PA11-Pulver, mit einem anderen Material verbunden, um gewisse Eigenschaften zu verbessern. Die nachfolgenden Verbundwerkstoffe sind mit beinahe allen der vorangegangenen Pulver kompatibel, mit Ausnahme von der Kombination von Carbonfasern und TPU-Pulver.
In dieser Kategorie werden wir uns ein weiteres Mal drei Materialarten anschauen – carbonfaserverstärkte Pulver, flammhemmende Pulver und ESD-sichere Pulver, begonnen mit dem Verbundwerkstoff, der auf maximale mechanische Eigenschaften ausgelegt ist.
Bei der Verbindung mit Carbonfasern werden millimeterkleine, zerhackte Carbonfasern gleichmäßig mit dem Matrixpulver vermischt, zumeist mit einem Massenanteil zwischen 10 und 20 %, um die mechanischen Eigenschaften des Matrixpulvers massiv zu verbessern, ohne dabei das Gewicht zu erhöhen.
Diese Kombination führt zum größten Vorteil von carbonfaserverstärkten Pulvern – einem außergewöhnlichen Festigkeits-Gewichts-Verhältnis, mit der strukturell hochstabile und Bauteile mit geringem Gewicht möglich sind. Auch die Steifigkeit wird durch die Verbindung mit den Carbonfasern erhöht.
Des Weiteren wird auch die Hitzebeständigkeit dank den Carbonfasern verbessert. Die exakte Wärmeformbeständigkeit hängt natürlich eng mit dem Matrixmaterial zusammen, aber im Vergleich zwischen verstärktem und unverstärktem Pulver schneiden die verstärkten Pulver immer besser ab. Dasselbe gilt auch für die chemische Resistenz.
Carbonfaserverstärkte Pulver besitzen jedoch eine rauere Oberfläche als unverstärkte Pulver und sind auch um bis zu 150 % teurer. Ebenfalls ist die Verarbeitungsschwierigkeit erhöht, da ein stärkerer Laser oder spezielle, auf Carbonfasern ausgelegte Düsen benötigt werden – je nach spezifischen Druckverfahren.
Das außergewöhnliche Festigkeits-Gewichts-Verhältnis ist besonders in der Luftfahrt von großem Vorteil. Durch mögliche Gewichtseinsparungen bei Strukturbauteilen wie Tragflächen, Ruder und Halterungen von bis zu 30 % können hierbei massive Mengen an Treibstoff gespart werden.
Weitere Anwendungsgebiete umfassen den Industrie- und Maschinenbau, in dem Werkzeuge, Formen, Zahnräder, Gehäuse und mehr gedruckt werden können, und die Automobilbranche, in der das verringerte Gewicht bei Struktur- und Performanceteilen ebenfalls zu Treibstoffeinsparungen führt.
Um Pulver, die nicht inhärent flammhemmend sind, mit dieser Eigenschaft auszustatten, werden die Pulver mit bestimmten Additiven, beispielsweise Halogen- oder Phosphorverbindungen, zugesetzt. Je nach Abstimmung werden dabei verschiedene Flammhemmungsstufen erreicht.
Der größte Vorteil dieser Pulver ist offensichtlich – die Flammhemmung. Dadurch wird gewährleistet, dass die Bauteile einen erhöhten Entzündungswiderstand, begrenzte Wärmeabgabe und selbstverlöschende Eigenschaften besitzen, wodurch eine Flamme, nach Entfernung der Zündquelle, innerhalb von 10 bis 30 Sekunden erlischt.
Zusätzlich bieten flammhemmende Polymer-Pulver eine verringerte Toxizität und Rauchbildung bei einem potenziellen Brand und verringern die Flammausbreitung, um umliegende Komponenten vor Hitze- oder Flammschäden zu schützen.
Durch die Zugabe der Flammschutzmittel wird allerdings manchmal die Resistenz gegenüber Chemikalien negativ beeinflusst. Auch das Fließverhalten und die Druckqualität können beeinflusst werden, was spezielle Druckparameter voraussetzt. Zu guter Letzt ist auch der Preis durch die Zugabe der Additive erhöht, durchschnittlich zwischen 50 und 100 % im Vergleich zum reinen Matrixmaterial.
Bei Anwendungen mit hohem Sicherheitsbedürfnis, beispielsweise der Öl- und Gasindustrie, sind flammhemmende Eigenschaften ein Muss, um potenzielle Schäden an Mensch und Maschine zu verhindern. Dabei eignen sich flammhemmende Polymer-Pulver sowohl für Maschinen in Form von Zahnrädern, Lagern und mehr sowie für Menschen in Form von Schutzausrüstung.
Dieses Sicherheitsbedürfnis erfüllen flammhemmende Pulver außerdem für Industrien wie der Automobilbranche, der Luftfahrt, der Verpackungsindustrie und der Elektronikindustrie.
ESD, oder elektrostatische Ableitungen, stellen insbesondere in der Elektronikindustrie ein großes Problem dar. Es wird geschätzt, dass alleine innerhalb dieser Branche jedes Jahr mehrere Milliarden US-Dollar an Schäden durch ESD entstehen.
ESD-sichere Pulver stellen für eine Vielzahl von Anwendungen innerhalb dieser Industrie die Lösung dar. Diese zumeist mit Kohlenstoffröhrchen zugesetzten Pulver liefern ableitende oder antistatische Eigenschaften, mit denen ESD-Schäden an Bauteilen und Menschen verhindert werden.
Diese Art von Pulvern zeichnet sich außerdem damit aus, dass sie die mechanischen, chemischen, physischen und thermischen Eigenschaften des Matrixmaterials zumeist gar nicht und wenn dann nur minimal beeinträchtigen. Das bedeutet für Unternehmen, dass sie relativ einfach auf ESD-sichere Pulver wechseln und alteingediente Eigenschaften ohne Schwierigkeiten beibehalten können.
Die Verarbeitungsschwierigkeit wird jedoch auch bei ESD-sicheren Pulvern etwas erhöht, wenn auch nicht so sehr wie bei anderen Verbundwerkstoffen. Ein stärkerer Laser oder spezielle Düsen sind nichtsdestotrotz notwendig für die korrekte Verarbeitung. Auch die Preise erhöhen sich, jedoch ebenfalls weniger als bei anderen Verbundwerkstoffen – durchschnittlich zwischen 20 und 50 %.
Selbstverständlich liegt der Hauptnutzen solcher Pulver in der Elektronikindustrie. Diese ermöglichen die Herstellung von ESD-sicheren Gehäusen, Isolatoren, Halterungen, Abdeckungen und Steckverbindungen, aber auch für Werkzeuge und andere Fertigungshilfsmittel.
Weitere Nutznießer dieser Pulver umfassen die Luftfahrt, die Automobilindustrie und auch der Konsumgütersektor, in denen ebenfalls Gehäuse und Abdeckungen produziert werden können, um auch hier für ein Maximum an Sicherheit zu sorgen.
Trotz der geringeren Materialauswahl als bei anderen 3D-Druck-Technologien bietet der Polymer-Pulver-Druck immer noch eine breite Palette an verschiedenen Pulvern, die mit unterschiedlichen Eigenschaften branchenübergreifend glänzen können.
Ich hoffe, dass ich einen schnellen Überblick zu diesen unterschiedlichen Eigenschaften geben konnte und Sie nun mit gestärktem Wissensschatz an die Auswahl Ihrer Pulvermaterialien gehen können.
In einem der nächsten Blogposts werden wir uns dann die verschiedenen Arten von Metallen im 3D-Druck anschauen, um auch dort einen idealen Überblick zu geben.
Vielen Dank für die Aufmerksamkeit – und bis zum nächsten Blogpost!