3D printers
High quality 3D printers
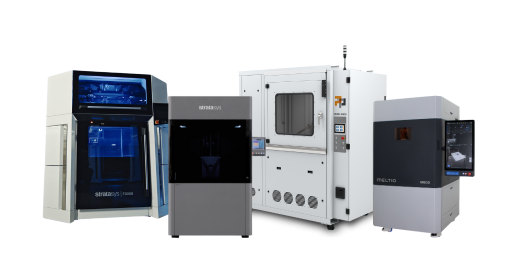
In the third part of this blog series on the materials used in various 3D printing technologies, we will be looking at the different types of polymer powders, their properties and their applications.
Despite the long-standing availability of this 3D printing technology, above all the SLS process, which was patented in 1986 by Dr. Carl Deckard and Dr. Joe Beaman and commercialised in 1992 with the ‘Sinterstation 2000’, the choice of materials is relatively limited compared to filament or resin 3D printing.
This is mainly due to the fact that polymer powder for 3D printing must meet very precise specifications. For example, the particle size distribution must be very exact, it must have special flow properties and it must be able to withstand high temperatures in order not to lose its properties during the printing process.
Nevertheless, powder 3D printing has become established in many industries. This is due, among other things, to the very economical use of material thanks to the recyclability of unused powder, the high heat resistance of all powders and the outstanding printing speed.
But this article is not about the advantages of the processes themselves, but about the advantages of the materials. For this purpose, I will divide the materials into three main categories – nylon-based powders, special polymers and composite materials. If you already have extensive knowledge of nylon-based powders, you can use the button below to jump directly to the special polymers or the composite materials.
Since its first commercialisation in 1938 by the US company DuPont, nylon has become an indispensable part of all our lives. Whether in textiles, household appliances, industrial manufacturing or medicine – nylon is so essential that it even led to the so-called ‘Nylon Riots’ in 1945 and 1946, when the production of nylon textiles could not meet the extraordinary demand.
Nylon-based powders, especially PA12, were also the first powders to be used for additive manufacturing, which is why we will look at them first here. In this category, we will look at PA6, PA11 and PA12, starting with the mechanically strongest nylon material.
PA6 is a semi-crystalline polyamide made from the polymerisation of caprolactam, which was first synthesised in 1938 by the German inventor Paul Schlack. In 3D printing, PA6 is a very high-performance polymer powder that is, however, used less frequently than other nylon-based materials.
PA6 is particularly impressive for its mechanical properties. The material has a very high strength, rigidity and toughness and is also very resistant to mechanical loads, wear and abrasion. Furthermore, it has a high heat resistance of 220 to 230 °C.
Additional positive properties include resistance to a large number of chemicals, oils and fats, as well as a very low price compared to other nylon-based materials, with an average of 30 to 60 euros per kilogram.
But why is PA6, despite these advantages, used less frequently than other nylon-based powders? This is mainly due to the high processing difficulty. PA6 tends to warp, which requires precise control of the process parameters, has a high hygroscopicity, which requires proper drying before processing, and is also rather stubborn in post-processing due to its high density and hardness. In addition, PA6 powder has the lowest reusability rate compared to other nylon-based powders.
Despite these processing difficulties, PA6 has undoubtedly made a name for itself in various industries and fields of application. Particularly in the mechanical engineering industry, the excellent mechanical and thermal properties have outweighed the difficult processing, with the result that gears, drive components, bearing housings, tools and moulds are now being produced with PA6 powder.
Other areas of application for PA6 powder include the automotive industry, where, for example, air intake ducts, fastenings and covers are produced with PA6 additive, and cross-industry rapid prototyping for prototypes that have to withstand mechanical loads.
When it comes to environmentally friendly production, PA11 is a real miracle cure. This powder is made from regenerative castor oil and is therefore much more environmentally friendly than petroleum-based polymers.
In addition to its environmental friendliness, PA11 stands out above all for its high flexibility and ductility. It also has very good impact strength and elongation at break, making it a breeze to withstand mechanical shocks and impacts – even with perpetually recurring loads, thanks to its high durability and very low brittleness.
In addition, PA11 has very good chemical resistance, high resistance to UV radiation and weather conditions and, in contrast to PA6, is much easier to process thanks to less warping and less sensitivity to moisture.
However, where PA11 clearly draws the short straw is in terms of heat resistance. With a heat deflection temperature of up to 190 °C, it is still anything but low, but compared to other polymer powders, it is still in the lower range. In addition, with a price of 70 to 120 euros per kilogram, PA11 is the most expensive nylon-based powder, and post-processing can also be difficult due to its flexibility.
Thanks to its combination of flexibility and impact resistance, PA11 has established itself in the aerospace industry, among others. It can be used for a variety of non-structural components, such as cable ducts, protective covers, seals and many more.
PA11 is also frequently used in medical technology because it is biocompatible and can be sterilised multiple times. It can be used for both medical instruments and indications such as prostheses or orthoses. PA11 is also very popular for outdoor applications due to its very high weather resistance.
PA12 is obtained from the polymerisation of laurolactam and is a semi-crystalline polyamide. PA12 was the material of choice when 3D printing was first developed and is still used today in a wide range of applications.
The main reason for the early use of this material lies in the very easy processability of PA12. The material is considered to be the easiest polymer powder to print because it has hardly any warpage, outstanding process stability and very low moisture absorption. Post-processing is also exceptionally simple, making PA12 components very easy to grind, drill or paint.
However, easy processing alone would not have been enough to maintain its position consistently. To do that, PA12 has its mechanical properties, which provide a very good balance of rigidity and flexibility. In addition, PA12 has good impact resistance and high resistance to chemicals, UV radiation and weathering.
However, PA12 is only partially protected against fractures under permanent mechanical loads. High temperatures also affect PA12, as it has a maximum heat resistance of 182°C. Furthermore, with a price of 60 to 100 euros, PA12 is in the mid-range, although it is highly recyclable, which means that despite the higher initial prices, there are cost savings, especially for large production volumes.
Thanks to its well-balanced properties and very easy processing, PA12 is the preferred choice for prototyping. Across all industries, PA12 can be used to quickly create and modify functional and design prototypes. It has proven particularly useful for mass prototyping in the automotive and aerospace industries.
Furthermore, PA12 is also frequently used in consumer goods, especially for outdoor use, for example for spectacle frames, electronic housings or even household appliances. It is also popular for brackets, tools and other production aids where a certain degree of flexibility is required.
Glass-fibre-reinforced PA12, usually abbreviated to PA12 GF, should also be briefly mentioned here, as it is becoming increasingly popular. The combination with glass fibres massively increases strength without making the component heavier, which is why it is used in particular in the automotive and aerospace industries for lightweight yet strong components.
While nylon-based powders can be used for a wide range of applications, the following materials are more tailored to more specific applications and usually have unique properties that make them stand out.
In this category, we will also look at three different types of powder – TPE / TPU, PP and PEEK, starting with the material of choice for elasticity!
TPE, or thermoplastic elastomers, is an umbrella term for several materials, including TPA, TPC and TPU. Since TPU, or thermoplastic polyurethane, is mostly used in the field of polymer powders, we will also focus on this material.
TPU is characterised by its extraordinary elasticity. This, in combination with its excellent resilience and abrasion resistance, ensures that components can stretch a long way under mechanical stress without breaking or permanently losing their mechanical properties, and then spring back into their original position on their own.
In addition, TPU is resistant to many oils, greases and solvents, offers very good conditions for use in high-temperature applications with a heat resistance of up to 220°C and is also suitable for certain outdoor applications thanks to its resistance to UV radiation.
However, TPU powder is difficult to process, even more so than PA6. Due to its elasticity, the material tends to warp and layer adhesion can also cause problems, which is why a process precisely adapted to this material is necessary. Post-processing is also relatively expensive due to the flexibility, and the price is in the upper mid-range at 60 to 120 euros per kilogram.
Thanks to its elasticity and resilience, TPU powder is particularly suitable for shock absorbers across all industries. Whether in aviation, the automotive industry or for protective equipment in competitive sports – TPU makes durable elastic components possible.
Other areas of application include the consumer goods industry, where TPU powder can be used to manufacture protective covers, shoe soles or flexible clothing accessories, and robotics, where TPU is ideal for flexible grippers or joint sleeves.
Polypropylene is one of the most widely used plastics worldwide and is particularly indispensable in the packaging industry. It has also been able to make its mark in the world of additive manufacturing.
This is mainly due to the very low density of PP, which averages 0.9 g/cm³. This makes it possible to produce very light yet mechanically strong components thanks to its high toughness and impact strength.
In addition, PP absorbs virtually no moisture, which maintains its mechanical properties and dimensional stability at a high level even when exposed to moisture, and is exceptionally resistant to chemicals, including acids, bases, solvents and fats. PP is also very cost-effective with a price of 30 to 60 euros per kilogram and good recycling properties.
However, where PP struggles is in terms of rigidity, where it only achieves moderate values, without having extraordinary flexibility. With a heat deflection temperature below 170 °C, it is also not suitable for applications at very high temperatures, and PP is relatively difficult to process due to its high tendency to warp and shrink.
Just as in traditional manufacturing, PP has found its main function in the packaging industry when it comes to 3D printing. Whether recyclable containers and bottles, protective packaging or flexible packaging, PP in additive manufacturing enables environmentally friendly production and high-performance applications.
PP is also frequently used for fluid containers, for example in the automotive industry as containers for washer fluid or coolant, thanks to its resistance to moisture and chemicals. In agriculture, PP is used for components in irrigation systems and protective films, among other things.
PEEK is one of the newest materials in the field of additive manufacturing and has so far mainly found its way into filament 3D printing – but it is now also possible to process PEEK in polymer powders.
This material excels with unique mechanical and thermal properties. With unparalleled mechanical strength, rigidity and wear resistance, as well as a heat deflection temperature of up to 280°C, it is the perfect choice for high-performance applications.
PEEK also offers outstanding resistance to a wide range of chemicals and gamma radiation. In addition, PEEK is inherently flame retardant, which means that it easily meets even the strictest fire safety regulations, and is biocompatible.
While TPU or PP have already been described as difficult to process, PEEK takes the biscuit. With melting temperatures of over 340°C, very specialised printing equipment is needed to process the material at all. In addition, at a price of €300–600 per kilogram, PEEK is undoubtedly the most expensive polymer powder on the market.
PEEK offers the unique possibility of producing functional components for aerospace. Thanks to their outstanding mechanical, thermal and chemical properties, PEEK components provide the necessary stability and safety for manufacturing components such as seals, valves and structural components in this field of application.
PEEK is also widely used in medical technology. Thanks to its biocompatibility, it can be used for both instruments and implants. PEEK is also very useful in the aerospace, automotive and electronics industries.
In composites, a matrix material, for example a PA11 powder, is combined with another material to improve certain properties. The following composites are compatible with almost all of the powders listed above, with the exception of the combination of carbon fibres and TPU powder.
In this category, we will once again look at three types of materials – carbon fibre-reinforced powders, flame-retardant powders and ESD-safe powders, starting with the composite material designed for maximum mechanical properties.
In the case of carbon fibres, chopped carbon fibres just a few millimetres in size are mixed evenly with the matrix powder, usually in a mass fraction between 10 and 20%, to massively improve the mechanical properties of the matrix powder without increasing the weight.
This combination results in the greatest advantage of carbon fibre-reinforced powders – an exceptional strength-to-weight ratio, which makes it possible to create structurally highly stable components with a low weight. The stiffness is also increased by the combination with the carbon fibres.
Furthermore, heat resistance is also improved thanks to the carbon fibres. The exact heat deflection temperature is of course closely related to the matrix material, but when comparing reinforced and unreinforced powder, the reinforced powder always performs better. The same applies to chemical resistance.
However, carbon fibre-reinforced powders have a rougher surface than unreinforced powders and are also up to 150% more expensive. They are also more difficult to process, as a more powerful laser or special nozzles designed for carbon fibres are required, depending on the specific printing process.
The exceptional strength-to-weight ratio is particularly advantageous in aviation. The potential for weight savings of up to 30% in structural components such as wings, rudders and brackets can result in massive fuel savings.
Other areas of application include industrial and mechanical engineering, where tools, moulds, gears, housings and more can be printed, and the automotive industry, where the reduced weight of structural and performance parts also leads to fuel savings.
To provide powders that are not inherently flame retardant with this property, certain additives, such as halogen or phosphorus compounds, are added to the powders. Depending on the composition, different levels of flame retardancy are achieved.
The greatest advantage of these powders is obvious – their flame retardancy. This ensures that the components have increased ignition resistance, limited heat emission and self-extinguishing properties, whereby a flame extinguishes within 10 to 30 seconds after removal of the ignition source.
In addition, flame-retardant polymer powders offer reduced toxicity and smoke formation in the event of a potential fire and reduce the spread of flames to protect surrounding components from heat or flame damage.
However, the addition of flame retardants sometimes has a negative impact on resistance to chemicals. Flow behaviour and print quality can also be affected, which means that special printing parameters are required. Finally, the price is also higher due to the addition of additives, on average between 50 and 100% higher than for the pure matrix material.
In applications with high safety requirements, for example in the oil and gas industry, flame-retardant properties are a must to prevent potential damage to people and machines. Flame-retardant polymer powders are suitable for both machines in the form of gears, bearings and more, and for people in the form of protective equipment.
Flame-retardant powders also fulfil this safety requirement for industries such as the automotive, aviation, packaging and electronics industries.
ESD, or electrostatic discharge, is a major problem in the electronics industry in particular. It is estimated that billions of dollars in damages occur due to ESD in this industry alone each year.
ESD-safe powders are the solution for a variety of applications within this industry. These powders, which are usually added with carbon tubes, provide dissipative or antistatic properties that prevent ESD damage to components and people.
These powders are also characterised by the fact that they usually have no or only a minimal effect on the mechanical, chemical, physical and thermal properties of the matrix material. This means that companies can easily switch to ESD-safe powders and retain their tried and tested properties without difficulty.
However, the processing difficulty is also increased somewhat for ESD-safe powders, although not as much as for other composite materials. A stronger laser or special nozzles are nonetheless necessary for proper processing. Prices also increase, but less than for other composite materials – on average between 20 and 50%.
Of course, the main use of such powders is in the electronics industry. These enable the production of ESD-safe housings, insulators, brackets, covers and plug connections, as well as tools and other manufacturing aids.
Other beneficiaries of these powders include the aerospace, automotive and consumer goods industries, where housings and covers can also be produced to ensure maximum safety.
Despite the smaller selection of materials than with other 3D printing technologies, polymer powder printing still offers a wide range of different powders that can impress with different properties across a range of industries.
I hope that I have been able to give you a quick overview of these different properties and that you can now go about choosing your powder materials with a greater knowledge.
In one of the next blog posts, we will take a look at the different types of metals used in 3D printing to provide you with an ideal overview of these as well.
Thank you for reading – and see you in the next blog post!