3D-Drucker
Hochwertige 3D-Drucker
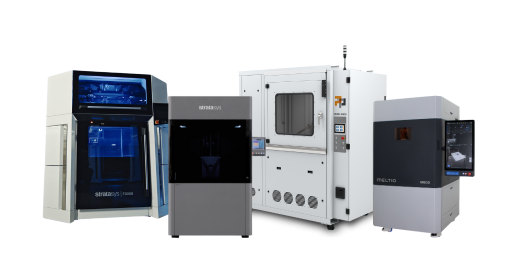
25 % Rabatt auf Ihre erste Bestellung von 3D-gedruckten Bauteilen!
SOMMER-RABATT JETZT SICHERN!Die perfekte Symbiose aus Qualität und Quantität!
Komplexeste Geometrien mit idealen Eigenschaften!
Hochauflösende Bauteile mit großer Materialvielfalt!
Leistungsstarke Bauteile mit nachhaltiger Fertigung!
Große Werkstoffauswahl und ultraschnelle Fertigung!
Ideal für verschiedenste Dentalindikationen!
Der Prozess vom simplen Bauteil zum Produkt!
Vollautomatisierung Ihrer Produktion!
Schnelle Verarbeitung und erfolgreiches Management!
Für diese Kombination der Filter gibt es leider keine Ergebnisse. Wählen Sie eine andere Filter-Kombination.
Um sicherzustellen, dass alle Anfragen zeitnah und vollständig bearbeitet werden, bitten wir Sie, alle Support-Anfragen über unser Support-Portal zu stellen.
Zum Service-PortalBrauchen Sie Unterstützung bei Ihrem Projekt, benötigen Sie eine Beratung oder ein Musterteile das wir Ihnen zusenden können?
Email sendenExpandierendes Polypropylen (EPP) hat sich seit seiner Entwicklung in den frühen 1980er-Jahren in Japan zu einem Grundpfeiler in vielen Hochleistungsindustrien entwickelt. Ob Automobilindustrie, Luft- und Raumfahrt, Baubranche oder viele weitere, für Bauteile, die herausragende Schlagzähigkeit und Energieabsorption und zeitgleich ein geringes Gewicht erfordern, ist EPP inzwischen zweifellos das Material der Wahl.
Dabei hat sich EPP für diese Hochleistungsanwendungen insbesondere gegen EPS, expandierendes Polystyrol, besser bekannt unter dem Handelsnamen Styropor®, durchsetzen können. Durch verbesserte Schlagzähigkeit, Recyclingfähigkeit und Designflexibilität kann EPP gegenüber EPS immer weitere Anwendungsfelder erschließen, was durch die Vorhersage einer durchschnittlichen Wachstumsrate des EPP-Markts von 7,21 % bis zum Jahr 2029 untermauert wird.
Die Formung von EPP wird dabei traditionell mit Metallformen, beispielsweise aus Werkzeugstahl oder Aluminium, durchgeführt. Diese herkömmlichen Formen gehen allerdings mit einigen Nachteilen einher, die die Kosten und die Produktionszeit erhöhen.
Inzwischen bietet der Filament-3D-Druck, auch bekannt als FDM- oder FFF-3D-Druck, jedoch die Möglichkeit, diese Nachteile in Vergessenheit geraten zu lassen. In diesem Blogpost möchte ich den Prozess der EPP-Formung vorstellen, auf die Vorteile des 3D-Drucks für die Formherstellung eingehen und die idealen Materialien und Druckanlagen für diesen Prozess aufzeigen.
Das EPP kommt in Form von sehr kleinen Perlen, welche zunächst für einige Stunden in einer Dampfkammer oder mit einem Treibmittel „vorexpandiert“ werden, woraufhin die nun etwas größeren Perlen zwischen 12 und 48 Stunden ruhen gelassen werden. Dieser Prozess legt die Zellstruktur der Perlen fest und gibt EPP seine charakteristischen Eigenschaften.
Im nächsten Schritt kommt die Form zum Einsatz. Diese besteht aus zwei Formhälften, einer männlichen und einer weiblichen, deren Kavität die Form des Endprodukts abbildet. In diese Formkavität werden die EPP-Perlen nun überführt und auf die beiden Formhälften wird Spannkraft ausgeübt, um die Hälften durchgängig gleichmäßig aneinanderzuhalten.
Als Nächstes wird Wasserdampf mit einer Temperatur zwischen 100 und 150 °C in die Formkavität eingelassen. Dieser Dampf sorgt nun einerseits für eine Erweichung der Perlenoberflächen und andererseits erleichtert er die weitere Expansion des Materials.
Um eine gleichmäßige Verteilung des Dampfes innerhalb der Form sowie eine kontrollierte Zufuhr von Luft und Ableitung von Dampf zu gewährleisten, sind die Formen an bestimmten Stellen mit porösen Strukturen ausgestattet, die eine ideale Zirkulation gewährleisten.
Nach einiger Zeit unter Dampfeinwirkung sind die Oberflächen der Perlen so weich, dass sie mit den Oberflächen der umliegenden Perlen verschmelzen. Dadurch bildet sich, während das Material zeitgleich weiter expandiert, eine kontinuierliche, monolithische Schaumstoffstruktur, während die Zellstruktur des Materials und damit auch die charakteristischen Eigenschaften beibehalten werden.
Sobald das EPP in der durch die Kavität vorgegebenen Form ausgehärtet ist, wird die Spannkraft noch kurze Zeit auf den beiden Formhälften gehalten, während der Schaumstoff langsam abkühlt. Sobald dieser vollständig abgekühlt ist, wird die Spannkraft entfernt und das fertige Teil aus den beiden Formhälften entnommen. Der Prozess des Formens selbst, Abkühlungszeit exkludiert, dauert dabei nur einige Minuten.
Nun kann der Schaumstoff bei Bedarf noch mit verschiedenen Nachbearbeitungsmethoden vollendet werden. Von Zuschneiden über Oberflächenveredelung bis hin zu Einfärbung – die Möglichkeiten der Nachbearbeitung sind schier grenzenlos.
Die Form steht beim Prozess der EPP-Formung, allgemein auch als Dampfkammerformung bekannt, natürlich im Fokus. Für die Herstellung dieser Formen ist der 3D-Druck geradezu prädestiniert, da er viele der Engpässe, die mit der Herstellung aus Metall einhergehen, löst.
Zunächst einmal zu einem der Hauptaugenmerke für jede Produktion – Kosten. Da die EPP-Form spezielle Eigenschaften benötigt, beispielsweise eine hohe Wärmeformbeständigkeit, bieten sich innerhalb des 3D-Drucks nur spezielle Hochleistungsmaterialien an. Die reinen Materialkosten sind dadurch erst einmal höher als bei einem traditionellen Metallhalbzeug – dieses Kostenmanko wird durch die Verarbeitungskosten jedoch nicht nur ausgeglichen, sondern sogar überkompensiert, sodass sich insgesamt eine signifikante Reduktion der Gesamtproduktionskosten ergibt, welche durchschnittlich 40 % beträgt.
Dies liegt insbesondere daran, dass die porösen Strukturen, die in der Form benötigt werden, nicht aufwändig gefräst oder gelasert werden müssen, sondern einfach im digitalen Modell in das Design integriert werden können, wodurch der 3D-Drucker die fertige Form direkt mit der porösen Struktur druckt. Mit der passenden Software kann die Struktur sogar feingenau angepasst werden, um die Oberflächendichte des späteren EPP-Teils abzuändern. Zusätzlich wird durch die direkte Integration dieser porösen Strukturen Materialausschuss vermieden, was sowohl Kosten als auch Umwelt schont.
Ein weiteres Hauptaugenmerk für jede Produktion ist Zeit – und auch hier können 3D-gedruckte EPP-Formen ihr traditionelles Pendant übertreffen. Da die Formen stark in ihrer Größe variieren können, ist ein exakter Vergleich kaum möglich, durchschnittlich kann per 3D-Druck allerdings ca. 60 % an Produktionszeit eingespart werden.
Aber nicht nur bei der Produktionszeit, sondern auch beim Formprozess sparen 3D-gedruckte Formen Zeit. Da die für diese Anwendung geeigneten Materialien allesamt herausragende Isolationseigenschaften besitzen, geht keinerlei Hitze beim Formungsprozess verloren, wodurch die Zykluszeit um bis zu 34 % reduziert werden kann. Außerdem wird dadurch viel weniger Dampf benötigt, ca. 65 %, was einmal mehr die Kosten nach unten drückt.
Der finale große Vorteil von 3D-gedruckten Formen ist die Texturqualität des EPP-Teils. Trotz der Verschmelzung der einzelnen EPP-Perlen besitzt das endgültige Teil weiterhin eine „perlenartige“ Oberflächentextur – jeder, der bereits einmal Styropor® in der Hand hatte, kennt diese Struktur. Während diese Struktur bei Anwendungen wie Verpackungsmaterial irrelevant ist, gibt es viele Anwendungen, bei denen die Schaumstoffoberfläche ansprechender aussehen muss, was mit herkömmlichen Formen nur durch Nachbearbeitung erreicht werden kann.
Per 3D-Druck können die Formen jedoch direkt mit einer Textur gedruckt werden, die während des Formgebungsprozesses auf das EPP-Teil übertragen werden. Außerdem können kleine Merkmale, beispielsweise Schriftzüge oder Logos, mit hohem Detailgrad und geringem Aufwand in das digitale Modell integriert werden, damit diese ebenfalls direkt auf den Schaumstoff übertragen werden.
Nachdem wir nun die vielfältigen Vorteile der Additiven Fertigung bei EPP-Formen besprochen haben, müssen wir natürlich auch die Schattenseite beleuchten – es gibt schließlich nie vielerlei Vorzüge ohne mindestens einen Nachteil.
Dieser eine Nachteil ist bei 3D-gedruckten EPP-Formen die Lebensdauer, welche hinter der von herkömmlichen Metall-Formen zurückbleibt. Eine genaue Lebensdauer hängt selbstverständlich von den Prozessumständen ab, aber durchschnittlich lassen sich mit einer Form mindestens 2.000 Bauteile herstellen, bevor die Form die Qualität des EPP-Teils beeinträchtigt.
Diese Zahl kann jedoch mit einigen Prozessänderungen erhöht werden. Einerseits sollte der Vorteil, dass weniger Dampf benötigt wird, auch tatsächlich genutzt werden, da eine höhere Dampfkonzentration auf Dauer die Form schädigt, andererseits sollte darauf geachtet werden, dass die Spannkraft so niedrig wie möglich gehalten wird, um das Bauteil nicht unnötig zu strapazieren.
Wenn diese Punkte beachtet werden, kann die Anzahl der produzierten EPP-Teile mit einer einzigen Form auf über 5.000 ansteigen. Diese Zahl bleibt weiterhin hinter denen von Metallformen zurück, welche von 10.000 mit Aluminium auf bis zu 1.000.000 mit Werkzeugstählen andauern können – wobei die Material- und Herstellungskosten bei Werkzeugstählen natürlich noch einmal höher liegen als bei Aluminium.
Daher bietet sich der 3D-Druck bei Produktionen mit sehr hohen Stückzahlen trotz seiner vielfältigen Vorteile nicht an. Für Industrien, die jedoch eher kleine bis mittelgroße Serien herstellen, oder die eine häufige Anpassung der Form benötigen, ist der 3D-Druck dafür jedoch umso idealer.
Wie bereits zuvor erwähnt, benötigen die genutzten Materialien spezielle Eigenschaften, darunter insbesondere eine hohe Wärmeformbeständigkeit, einen geringen Wärmeausdehnungskoeffizient und eine herausragende Korrosionsbeständigkeit. Auch Biokompatibilität kann von Vorteil sein, wenn der Schaumstoff später mit Medikamenten oder Nahrungsmitteln in Kontakt kommen könnte. Dadurch fallen Standardmaterialien, beispielsweise PLA oder ABS, natürlich sofort aus dem Auswahlprozess.
Unsere favorisierten Optionen für die Herstellung von EPP-Formen sind Verbundwerkstoffe, beispielsweise das Nylon12CF von Stratasys®, oder PEI, besser bekannt unter seinem Handelsnamen ULTEM™.
Wir setzen dabei speziell auf das ULTEM™ 1010 als unser Zugpferd bei 3D-gedruckten EPP-Formen. Mit einer Wärmeformbeständigkeit von 214 °C, einer hervorragenden Korrosionsbeständigkeit, Biokompatibilität und Zugfestigkeit ist dieses Material herausragend geeignet für die additive Fertigung von EPP-Formen.
Da dieses Material eine hohe Verarbeitungstemperatur benötigt, werden hochindustrielle Anlagen benötigt, um dieses Material präzise verarbeiten zu können. Unsere Wahl fällt dabei auf den F900™ von Stratasys®.
Diese Druckanlage glänzt nicht nur mit der problemlosen Verarbeitung von ULTEM™ 1010, sondern auch mit einer führenden Präzision und Wiederholbarkeit sowie der Möglichkeit, nahezu isotrope Bauteile herzustellen. So können eine maximale Lebensdauer der Formen sowie die problemlose Neuproduktion sichergestellt werden.
Die Additive Fertigung ist wahrlich keine neue Technologie mehr. Seit ihrer Konzeption in den 1980er-Jahren werden jedoch stets neue Industrien und Anwendungsgebiete erschlossen – so auch nun mit der Herstellung von EPP-Formen, welche vor allem dank den Fortschritten in Sachen Materialeigenschaften möglich wurde.
Diese noch vergleichsweise junge Anwendung hat dabei bereits einen großflächigen Fußabdruck hinterlassen. Bereits jetzt haben mehrere große Hersteller von Schaumstoffen auf den 3D-Druck gesetzt und ich hoffe, dass ich mit diesem Blogpost dazu beitragen kann, dass sich die Vorteile der Additiven Fertigung auch weiter in dieser Industrie durchsetzen können.
Wenn Sie weiterführende Fragen rund um diese Anwendung haben, kontaktieren Sie gerne unsere Experten. Wir helfen Ihnen gerne weiter, um die passende Lösung zur Integration der Additiven Fertigung in Ihre Produktion zu finden – ob direkt mit einer eigenen Anlage oder per Produktion als Dienstleister.
Vielen Dank für Ihre Aufmerksamkeit – und bis zum nächsten Blogpost!
Privatsphäre Einstellungen
Wir nutzen Cookies um Dir die bestmögliche Erfahrung zu bieten. Außerdem können wir damit das Verhalten der Benutzer analysieren um die Webseite stetig für Dich zu verbessern. Datenschutz