3D-Drucker
Hochwertige 3D-Drucker
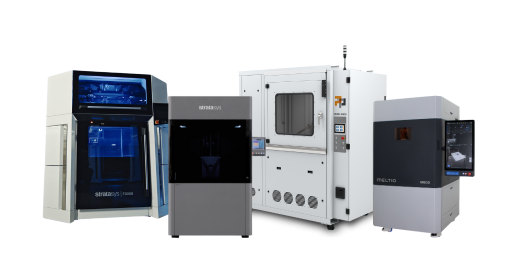
Der 3D-Druck von Metallbauteilen breitet sich innerhalb von verschiedenen Industriezweigen immer weiter aus. Ob Automobilbranche, Werkzeughersteller, Luft- und Raumfahrtindustrie oder gar Medizintechnik – die Anwendungsgebiete der Additiven Fertigung von Metallkomponenten werden immer diverser. Einen genaueren Einblick in die Vorteile und Anwendungsgebiete des Metall-3D-Drucks können Sie hier erhalten.
Die Entscheidungen rund um die Additive Fertigung mit Metall werden aber ebenfalls immer diverser – und damit auch schwieriger. Immer mehr Drucker, Technologien, Hersteller und Materialien kommen auf den Markt und ermöglichen somit individuellere Möglichkeiten, verursachen jedoch auch längere Entscheidungsprozesse.
Eine Entscheidung, welche allerdings bereits vor der Additiven Fertigung sehr vielfältig war, ist die der Oberflächenveredelung von Metallbauteilen. Es gab bereits in den 70ern unzählige Verfahren, mit welchen Metallkomponenten veredelt werden können – und die Additive Fertigung hat zu diesen noch weitere hinzugefügt.
Im heutigen Blogpost soll es um genau diese unzählbaren Verfahren gehen. Selbstverständlich muss ich mich in diesem Blog auf die wichtigsten Verfahren beschränken, da weder mir als Schreiber noch Ihnen als Leser eine Unendlichkeit an Zeit zur Verfügung steht, aber diese Verfahren werden nachfolgend intensiv beleuchtet sowie deren Vor- und Nachteile präsentiert.
Beginnen wir diesen Blogpost mit einigen der klassischen Techniken zur Veredlung von Metalloberflächen, welche bereits lange vor der Additiven Fertigung existiert haben, jedoch ohne Probleme auch Metallbauteile, die mit dieser hergestellt wurden, veredeln können.
Der Klassiker schlechthin für die optische Oberflächenveredelung von Metallen ist das händische Schleifen. Dieses kann beim fertigen, ergo bereits gesinterten, Bauteil geschehen, aber auch davor, während sich das Bauteil noch im Grünteilzustand befindet.
Bei beiden Versionen ist der größte Vorteil eindeutig die geringen Kosten. Es werden keine Maschinen oder andere Gerätschaften benötigt, welche gegebenenfalls teuer akquiriert werden müssen, sondern ausschließlich Sandpapier oder ein Handpad, Zeit und Kraft.
Auch das Ergebnis bei Bauteilen mit simplen Geometrien kann sich nach dem Schleifen sehen lassen, insbesondere wenn bereits das Grünteil geschliffen wird – hierbei sind bis zu fünfmal feinere Oberflächen als ohne Schleifen möglich. Bei dieser Variante des Schleifens ist die Kraft jedoch mit Bedacht einzusetzen, da das Bauteil nur durch das Polymerbindemittel zusammengehalten wird.
Der größte Nachteil dieser Oberflächenveredelungsvariante ist offensichtlich – der Aufwand. Selbst das Schleifen eines kleineren Bauteils kann einiges an Zeit in Anspruch nehmen.
Auch die Einheitlichkeit kann beim klassischen Schleifen zu Problemen führen. Umso komplexer die Geometrien werden, desto schwieriger wird es mit händischem Schleifen eine einheitliche Feinheit der Oberfläche zu erreichen.
Ab einem gewissen Grad an Komplexität ist ein händisches Schleifen auch gar nicht mehr möglich. Insbesondere bei inneren Strukturen oder bei feinsten Details wird ein Schleifer, sei er noch so gut, nicht weit kommen.
Das Schleifen der Bauteile hat trotz alledem eindeutig weiterhin seinen Platz in der Welt der Oberflächenveredelung. Für sehr kleine Betriebe, bei wenigen Komponenten und bei sehr simplen Geometrien sind die Anschaffungskosten einer Gerätschaft speziell für die Oberflächenveredelung von Metallbauteilen eher weniger lohnenswert, weswegen sich hier die gute, alte Handarbeit auch zukünftig lohnt.
Die Galvanotechnik ist das älteste chemische Oberflächenveredelungsverfahren, welches heutzutage noch genutzt wird, um Metallbauteile optisch und funktionell zu verändern. Das Ende des 18. und Anfang 19. Jahrhunderts in Italien entwickelte Verfahren konnte durch die vergleichsweise marginale Toxizität beim Aufbringen metallischer Überzüge die bis dahin mit Quecksilber arbeitenden Prozeduren wie beispielsweise die Feuervergoldung ersetzen und ist seitdem ein unverzichtbarer Bestandteil für viele metallverarbeitende Unternehmen.
Bei diesem Verfahren wird Gleichstrom durch ein elektrolytisches Bad geleitet, an dessen Anode sich ein Metall befindet. Dieses wird durch die chemische Reaktion stückweise zersetzt, woraufhin sich die positiv geladenen Metallionen zum Werkstück, welches durch eine elektrische Verbindung zur Kathode wird, bewegen und sich auf diesem ablagern.
Die Vorteile dieses Verfahrens sind vielfältig, der wichtigste ist allerdings die hohe Vielfalt, die die Galvanotechnik bietet. So lassen sich vielfältige Materialien galvanisieren, von Gold bis Zink, und diese geben ihre Eigenschaften durch die Ablagerung auf dem Bauteil natürlich an dieses weiter. Dadurch sind den Merkmalen der 3D-gedruckten Metallbauteile quasi keine Grenzen mehr gesetzt.
Ein weiterer Vorteil ist der fantastische Korrosionsschutz, welcher durch die Galvanotechnik erreicht wird. Galvanik macht Bauteile grundsätzlich immer langlebiger und widerstandsfähiger, was insbesondere bei Applikationen mit hoher Krafteinwirkung von hoher Bedeutung ist.
Selbstverständlich kommt jedoch auch dieses Verfahren nicht ohne Nachteile einher. Einerseits ist die Schichtdicke, die durch das Galvanisieren erreicht wird, in den seltensten Fällen wirklich gleichmäßig. Sollte Gleichmäßigkeit benötigt werden, muss zusätzlich also ein weiteres Verfahren, z. B. das vorher präsentierte Schleifen, genutzt werden.
Ein weiterer Nachteil ist die Nutzung einer Vielzahl von Chemikalien. Auch wenn einige Abschnitte zuvor die geringere Toxizität dieses Verfahrens im Vergleich zu noch älteren Verfahren genannt wurde, werden nichtsdestotrotz giftige Dämpfe abgegeben. Dadurch sind gesonderte Sicherheitsmaßnahmen nötig, um dieses Verfahren zu nutzen, wodurch es insbesondere für kleine Unternehmen zumeist ausscheidet.
Die Galvanotechnik bietet sich durch ihren hohen Automationsgrad besonders für Unternehmen an, die größere Mengen oder größere Bauteile produzieren. Durch gewisse Eigenschaften, welche die Galvanisierung immer mit sich bringt, wie eine Verbesserung der Korrosionsbeständigkeit, ist die Galvanik für gewisse Industrien wie z. B. die Luft- und Raumfahrt unumgänglich, um ihre produzierten Teile noch leistungsfähiger zu machen.
Druckluftstrahlen, teilweise auch Sandstrahlen genannt, ist ein weiterer Klassiker in der Oberflächenveredelung, welches sowohl die optischen als auch funktionellen Eigenschaften eines Metallbauteils ändern kann. Bereits 1870 meldete der US-amerikanische Erfinder Benjamin Chew Tilghman das Patent des Druckluftstrahlverfahrens an, welches in den kommenden Jahrzehnten weiter verfeinert und auf eine Vielzahl von Materialien, darunter auch Metalle, ausgeweitet wurde.
Wurde traditionell Sand verwendet, welches durch Druckluft auf das jeweilige Bauteil gestrahlt wurde, existiert inzwischen eine Vielzahl von verschiedenen Strahlmitteln. Von Glas- und Keramikperlen über Schlacke und Korund bis hin zu Glas- und Nussschalengranulat – die Liste der möglichen Strahlmittel könnte noch eine ganze Weile so weiter gehen.
Diese Vielfalt an Strahlmitteln führt uns auch zum ersten, großen Vorteil des Druckluftstrahlens. Jedes Strahlmittel sorgt nämlich für unterschiedliche Merkmale beim Bauteil. So können rauere Oberflächen beispielsweise mit Korund oder Granatsand erreicht werden, während glattere Oberflächen durch Nutzung von Glasperlen oder Nussschalengranulat erzielt werden können.
Ein weiterer Vorteil sind die eher geringen Anschaffungs- und Materialkosten. Ein mobiles Druckluftstrahlgerät erhält man bereits für wenige hundert und eine Druckluftstrahlkabine bereits ab eintausend Euro. Die Strahlmittel können ebenfalls sehr günstig sein, z. B. Schlacke oder Granatsand.
Nachteilig ist die hohe Staubentwicklung, welche beim Druckluftstrahlen auftritt. Diese sorgt einerseits dafür, dass das Tragen von PSA bei offenen Druckluftstrahlgeräten Pflicht wird, andererseits muss der ganze Staub natürlich irgendwie entfernt werden, was einiges an Zeit kosten kann.
Beachtet werden muss auch, dass die Oberfläche des bestrahlten Bauteils warm wird. Bei den allermeisten additiv produzierten Metallbauteilen ist diese entstehende Wärme kein Problem, aber bei Komponenten mit sehr dünnen Wänden kann es nichtsdestotrotz zu Komplikationen führen.
Durch die hohe Qualität, die das Druckluftstrahlen erzielt, und die geringen Kosten hat sich diese Veredelungstechnik für viele kleinere und mittelständische Betriebe als absoluter Allrounder durchgesetzt. Insbesondere, wenn mehrere Materialien in einem Betrieb zum Einsatz kommen, lohnt sich Druckluftstrahlen durch seine Vielseitigkeit ohne jeden Zweifel.
Das Gleitspanen, welches auch als Gleitschleifen oder Trowalisieren, ein Neologismus, der auf die Walther Trowal GmbH & Co. KG zurückzuführen ist, welche dieses Verfahren als erstes industriell in einer Trommel nutzte, bekannt ist, ist das letzte der klassischen Veredelungsverfahren, welches wir uns heute anschauen werden.
Bei diesem Verfahren wird das Metallbauteil zusammen mit den Schleifkörpern und einem flüssigen Zusatzmittel in einem Behälter gegeben, welcher sich daraufhin oszillierend oder rotierend in Bewegung setzt und somit zu einer Relativbewegung zwischen Werkstück und Schleifkörper führt, wodurch die Oberfläche des Bauteils zumeist geschliffen, seltener poliert oder geläppt, wird.
Einen Vorteil, welches das Gleitspanen mit dem Druckluftstrahlen gemeinsam hat, ist, dass es für verschiedene Ziele verschiedene Schleifmittel gibt. Diese können aus Keramik, Kunststoff, Naturprodukten und mehr bestehen und liefern unterschiedliche Merkmale, um das Bauteil ideal auf die jeweiligen Anforderungen abzustimmen.
Im Gegensatz zum Druckluftstrahlen ist die menschliche Interaktion bei diesem Prozess aber kaum vorhanden. Sobald die benötigten Materialien in den Behälter geschüttet wurden und die Maschine angeschaltet ist, ist der Prozess vollständig automatisiert und man muss nur warten, bis das Bauteil fertig ist und es aus dem Behälter holen.
Durch diesen hohen Automationsgrad sind Gleitspanmaschinen allerdings auch alles andere als günstig in der Akquisition. Die Preise beginnen bei wenigen zehntausend Euro, können jedoch bei größeren Maschinen schnell über hunderttausend Euro betragen.
Trotz der grundsätzlich hohen Qualität und gründlichen Natur der Oberflächenbearbeitung beim Gleitspanen ist auch dieses Verfahren nicht für hochkomplexe Komponenten geeignet. Auch bei sehr feinen Details ist dieses Verfahren nicht ideal geeignet, da es die Oberfläche für solche zumeist zu rabiat behandelt.
Das Gleitspanen eignet sich ideal für Unternehmen, welche sehr viele, dafür aber eher kleinere, simplere Metallbauteile produzieren und diese schnell und ohne viel Zeitverlust nachbearbeiten wollen. Umso höher die Produktionskapazitäten, desto schneller wird der Return on Investment dank der eingesparten Zeit erreicht.
Nach einigen Klassikern kommen wir nun zu den Verfahren, welche spezifisch für die Oberflächenveredelung von 3D-gedruckten Metallbauteilen vorgesehen wurden. Da diese Verfahren allesamt noch relativ jung sind und die Auswahl daher geringer als bei den klassischen Verfahren ist, werden wir uns hierbei auf die drei wichtigsten Technologien beschränken.
Im Jahr 2016 wurde die DryLyte®-Technologie vom spanischen Unternehmen GPAINNOVA veröffentlicht und stellt das erste trockene Elektropoliturverfahren weltweit dar.
Die klassische Elektropolitur funktioniert quasi gegensätzlich zur Galvanotechnik, ergo ein Werkstück bildet hierbei die Anode und die Kombination aus Gleichstrom und elektrolytisches Bad trägt Stücke des Bauteils ab, wodurch es glatter wird. Die DryLyte®-Technologie ersetzt hierbei das elektrolytische Bad mit festen Elektrolytpartikeln in Kugelform, was mehrere Vorteile mit sich bringt.
Einer dieser Vorteile ist, dass die DryLyte®-Technologie die Metallbauteile nicht nur glatter macht, sondern gleichzeitig auch poliert. Insbesondere bei Anschauungsmodellen, bei welchen eine glänzende Oberfläche von größter Wichtigkeit sein kann, kann dadurch ein eigentlich eigener und aufwendiger Arbeitsschritt vollständig in Nichtigkeit verschwinden.
Ein weiterer großer Vorteil ist die sehr geringe Toxizität, die bei dieser Variante der Elektropolitur entsteht. Die Elektrolytpartikel besitzen eine nur sehr geringe Säurekonzentration, welche eine Lagerung, Handhabung und Entfernung ohne zusätzliche Sicherheitsmaßnahmen möglich macht – ganz im Gegensatz zur klassischen Elektropolitur oder der Galvanotechnik.
Als Nachteil muss jedoch die überdurchschnittlich lange Prozesskette genannt werden. Die Bauteile können nicht einfach direkt aus dem Drucker in die Politur gehen, sondern müssen erst gereinigt und entfettet werden und auch danach müssen Reinigungsarbeiten vorgenommen werden, um das Bauteil vollumfänglich nutzbar zu machen.
Des Weiteren ist Rauheitsreduktion bei der Elektropolitur zu einem gewissen Grad begrenzt. Zwar schneidet die DryLyte®-Technologie hierbei besser als die klassische Elektropolitur ab, jedoch bleibt sie anderen Technologien wie beispielsweise dem Druckluftstrahlen oder dem Gleitspanen weiterhin unterlegen.
Unternehmen, die eine große Anzahl kleiner Komponenten mit geringer bis mittlerer Komplexität produzieren, profitieren von der DryLyte®-Technologie am meisten. Durch die Zeitersparnis dank Schleifen und Polieren gleichzeitig, kann auch das Rapid Prototyping einen massiven Nutzen in dieser Technologie finden.
Die Technologie der Suspended Rotational Force (SRF) wurde vom US-amerikanischen Unternehmen PostProcess Technologies® im Jahr 2019 auf den Markt gebracht und baut auf dem klassischen Verfahren des Gleitspanens auf.
Die SRF-Technologie kombiniert diese Technologie jedoch mit dem Einsatz von speziell für die Additive Fertigung entwickelten Schleifmitteln. Außerdem arbeitet SRF mit einer Software, welche die Gleichmäßigkeit der mechanischen Kraft im Behälter erhöht.
Die Vorteile dieser Technologie beziehen sich vor allem auf die exakte Abstimmung auf die Additive Fertigung. PostProcess Technologies® nimmt ein bereits zertifiziertes Verfahren und münzt dieses noch exakter auf die Anforderungen der Additiven Fertigung – z. B. durch die bereits erwähnten Schleifmittel.
Durch die Softwareunterstützung und die erhöhte Einheitlichkeit der mechanischen Kraft werden auch Metallkomponenten mit sehr feinen Details schonend veredelt, wodurch die Anwendungsbereiche dieser Technologie über die des klassischen Gleitspanens herausgehen.
Genau wie beim Gleitspanen sind die Anschaffungskosten einer der größten Nachteile. Zwar liegt der Preis der Maschine mit der SRF-Technologie, der sogenannte RADOR™, im mittleren Preissegment im Vergleich zu anderen Gleitspananlagen, ist damit aber immer noch teurer als viele andere Oberflächenveredelungsgerätschaften.
Ein weiterer Nachteil ist die Bindung an PostProcess Technologies®, was die Verbrauchsmaterialien angeht. Inzwischen bietet PostProcess Technologies® zwar eine Menge verschiedener Schleifmedien, aber sollte man ganz spezifische Anforderungen haben, könnte es sein, dass kein passendes Schleifmedium verfügbar ist.
Die SRF-Technologie brilliert besonders bei der Massen- und Serienproduktion von Metallkomponenten. Im Gegensatz zum Gleitspanen kann es auch feine Details veredeln und eignet sich somit ideal für eine Vielzahl von industriellen Applikationen. Zusätzlich lassen sich mit der SRF-Technologie auch mit anderen Technologien 3D-gedruckte Komponenten veredeln, z. B. FFF, SLA, MJF und einige mehr.
Unser letztes Verfahren für die Oberflächenveredelung von 3D-gedruckten Metallkomponenten kommt einmal mehr von PostProcess Technologies®. Thermal Atomized Fusillade, oder kurz TAF, wurde 2022 in Form der DECI Duo™ Oberflächenveredelungsmaschine präsentiert und ist im Gegensatz zur SRF an kein klassisches Verfahren angelehnt, sondern eine vollständig eigene Technologie.
Diese arbeitet mit zwei senkrechten und einem waagrechten Strahlstrom, welche eine Mischung aus Druckluft, Reinigungsmittel und Schwebstoffen in schnellen Salven auf das Bauteil abgeben. Das Bauteil steht dabei auf einem Drehteller, damit die einachsigen Strahlströme das gesamte Bauteil bearbeiten können.
Der größte Vorteil dieser neuen Technologie ist, dass selbst komplexeste Bauteile damit veredelt werden können. Kleine Details, Waben und selbst innere Kanäle können mit dieser Technologie bearbeitet werden – und das vollständig automatisiert.
Ein weiterer Vorteil ist, dass durch diese Technologie nicht nur Oberflächen veredelt, sondern auch Stützstrukturen entfernt werden können. Auch hinsichtlich Technologien ist dieses Verfahren sehr vielseitig. Sie wurde zwar spezifisch für Metallkomponenten entwickelt, kann aber durch angepasste Parameter ohne Probleme auch FFF-, PolyJet-, SLA-, MJF- und viele weitere Bauteile bearbeiten.
Die Nachteile dieser Technologie decken sich mit denen der SRF-Technologie. Die Anschaffungskosten liegen dabei aber noch einmal über denen der SRF-Technologie und durch die Nutzung mehrerer Verbrauchsmaterialien ist die Abhängigkeit noch einmal schwerwiegender.
Rund um die Verbrauchsmaterialien muss auch die Auswahl zum derzeitigen Stand (Mai 2024) als Nachteil gewertet werden. Bis dato sind nur wenige verschiedene Materialien verfügbar, was die Anwendungsvielfalt natürlich verringert.
Nichtsdestotrotz ist die TAF-Technologie ein absolutes Zugpferd in Sachen Oberflächenveredelung von additiv gefertigten Metallbauteilen. Durch den maximalen Automationsgrad und die Möglichkeit, komplexeste Strukturen zu veredeln, ist diese Technologie für Unternehmen, welche höchste Qualität mit geringem Aufwand benötigen unumgänglich.
Wie in diesem Blogpost hoffentlich ersichtlich wurde, sind die Möglichkeiten der Oberflächenveredelung von Metallkomponenten mehr als vielfältig – und dabei wurden hier nicht einmal alle Möglichkeiten genannt.
Welche Variante der Oberflächenveredelung für die eigene Produktion am passendsten ist, hängt stark von den Anwendungen, die das Bauteil am Ende erfüllen muss, ab.
Ich hoffe, dass dieser Blogpost dabei helfen konnte, die vielen verschiedenen Möglichkeiten der Oberflächenveredelung von Metallkomponenten besser zu sortieren und dass Sie Ihre passende Variante gefunden haben.
Vielen Dank für Ihre Aufmerksamkeit – und bis zum nächsten Blogpost!