3D printers
High quality 3D printers
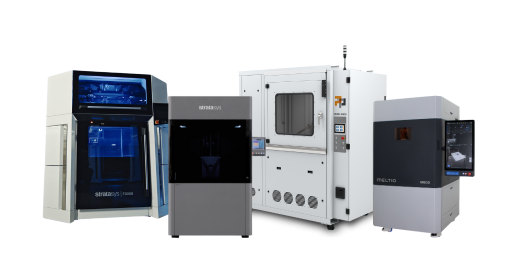
The 3D printing of metal components is becoming increasingly widespread within various branches of industry. Whether it's the automotive industry, tool manufacturers, the aerospace industry or even medical technology - the areas of application for additive manufacturing of metal components are becoming increasingly diverse. You can gain a more detailed insight into the advantages and areas of application of metal 3D printing here.
However, the decisions surrounding additive manufacturing with metal are also becoming increasingly diverse - and therefore more difficult. More and more printers, technologies, manufacturers and materials are coming onto the market, enabling more individualized options, but also causing longer decision-making processes.
However, one decision that was already very diverse before additive manufacturing was the surface finishing of metal components. Back in the 1970s, there were already countless processes that could be used to finish metal components - and additive manufacturing has added even more to these.
Today's blog post is about precisely these countless processes. Of course, I have to limit myself to the most important processes in this blog, as neither I as a writer nor you as a reader have an infinite amount of time available, but these processes will be examined in detail below and their advantages and disadvantages presented.
Let's start this blog post with some of the classic techniques for finishing metal surfaces that existed long before additive manufacturing, but which can also easily be used to finish metal components produced with it.
The classic method for the optical surface finishing of metals is manual polishing. This can be done on the finished, i.e. already sintered, component, but also beforehand, while the component is still in the green part state.
The biggest advantage of both versions is clearly the low cost. No machines or other equipment are required, which may have to be acquired at great expense, but only sandpaper or a hand pad, time and energy.
The results for components with simple geometries are also impressive after sanding, especially if the green part is already sanded - up to five times finer surfaces are possible than without sanding. With this type of sanding, however, the force must be used with caution, as the component is only held together by the polymer binder.
The biggest disadvantage of this surface finishing variant is obvious - the effort involved. Even sanding a smaller component can take quite some time.
Uniformity can also lead to problems with classic grinding. The more complex the geometries become, the more difficult it is to achieve a uniform surface finish with manual grinding.
Above a certain level of complexity, manual sanding is even no longer possible. A sander, however good it may be, will not get very far, especially with internal structures or the finest details.
Despite all this, sanding components clearly still has its place in the world of surface finishing. For very small companies, with few components and very simple geometries, the acquisition costs of equipment specifically for the surface finishing of metal components tend to be less worthwhile, which is why good old-fashioned manual work will continue to pay off in the future.
Electroplating is the oldest chemical surface finishing process that is still used today to visually and functionally modify metal components. Developed in Italy at the end of the 18th and beginning of the 19th century, the comparatively marginal toxicity of the process when applying metallic coatings meant that it was able to replace procedures that had previously used mercury, such as fire gilding, and has since become an indispensable component for many metalworking companies.
In this process, direct current is passed through an electrolytic bath with a metal at the anode. This is broken down piece by piece by the chemical reaction, whereupon the positively charged metal ions move to the workpiece, which becomes the cathode through an electrical connection, and are deposited on it.
The advantages of this process are many, but the most important is the great variety offered by electroplating. A wide variety of materials can be electroplated, from gold to zinc, and these naturally pass on their properties to the component through deposition on the component. As a result, there are virtually no limits to the characteristics of 3D-printed metal components.
Another advantage is the fantastic corrosion protection achieved by electroplating. Electroplating always makes components more durable and resistant, which is particularly important for applications involving high forces.
Of course, this process is not without its disadvantages. On the one hand, the layer thickness achieved by electroplating is rarely really uniform. If uniformity is required, a further process, e.g. the grinding described above, must also be used.
Another disadvantage is the use of a large number of chemicals. Even though the lower toxicity of this process compared to even older processes was mentioned a few paragraphs earlier, toxic vapors are nevertheless emitted. As a result, special safety measures are required to use this process, which means that it is usually not suitable for small companies in particular.
Due to its high degree of automation, electroplating is particularly suitable for companies that produce larger quantities or larger components. Due to certain properties that electroplating always brings with it, such as an improvement in corrosion resistance, electroplating is essential for certain industries, such as aerospace, in order to make the parts they produce even more efficient.
Sandblasting is another classic surface finishing process that can change both the visual and functional properties of a metal component. The US inventor Benjamin Chew Tilghman filed a patent for the sandblasting process back in 1870, which was further refined over the following decades and extended to a variety of materials, including metals.
While sand was traditionally used, which was blasted onto the respective component using compressed air, there is now a wide range of different blasting media. From glass and ceramic beads, slag and corundum to glass and nutshell granulate - the list of possible blasting media could go on for quite some time.
This variety of blasting media also leads us to the first major advantage of sandblasting. Each blasting medium provides different characteristics for the component. For example, rougher surfaces can be achieved with corundum or garnet sand, while smoother surfaces can be achieved by using glass beads or nutshell granulate.
Another advantage is the relatively low purchase and material costs. A mobile sandblasting unit can be purchased for just a few hundred euros and an air blast cabinet for as little as one thousand euros. The blasting media can also be very inexpensive, e.g. slag or garnet sand.
A disadvantage is the high level of dust that is generated during sandblasting. On the one hand, this ensures that PPE must be worn when using open compressed air blasting machines, and on the other hand, all the dust must of course be removed somehow, which can take a lot of time.
It should also be noted that the surface of the blasted component becomes hot. For the vast majority of additively manufactured metal components, this heat is not a problem, but for components with very thin walls, it can nevertheless lead to complications.
Due to the high quality that sandblasting achieves and the low costs, this finishing technique has established itself as an absolute all-rounder for many small and medium-sized companies. Especially when several materials are used in a company, sandblasting is undoubtedly worthwhile due to its versatility.
Vibratory finishing, also known as vibratory grinding, is the last of the classic finishing processes that we will look at today.
In this process, the metal component is placed in a container together with the abrasive media and a liquid additive, which then starts to oscillate or rotate, resulting in a relative movement between the workpiece and the abrasive media, whereby the surface of the component is usually ground, or more rarely polished or lapped.
One advantage that vibratory finishing has in common with sandblasting is that there are different abrasives for different targets. These can be made of ceramic, plastic, natural products and more and provide different characteristics to ideally match the component to the respective requirements.
However, unlike sandblasting, there is very little human interaction involved in this process. Once the required materials have been poured into the container and the machine is switched on, the process is fully automated and all you have to do is wait until the component is ready and remove it from the container.
However, this high degree of automation means that vibratory finishing machines are anything but cheap to purchase. Prices start at a few tens of thousands of euros, but can quickly reach over a hundred thousand euros for larger machines.
Despite the fundamentally high quality and thorough nature of the surface treatment in vibratory finishing, this process is also not suitable for highly complex components. This process is also not ideal for very fine details, as it usually treats the surface too roughly for these.
Vibratory finishing is ideal for companies that produce a large number of smaller, simpler metal components and want to rework them quickly and without losing too much time. The higher the production capacity, the faster the return on investment is achieved thanks to the time saved.
After some classics, we now come to the processes that have been specifically designed for the surface finishing of 3D-printed metal components. As these processes are all still relatively new and the selection is therefore smaller than for the classic processes, we will limit ourselves to the three most important technologies.
In 2016, the DryLyte® technology was released by the Spanish company GPAINNOVA and is the first dry electropolishing process in the world.
Classic electropolishing works in the opposite way to electroplating, i.e. a workpiece forms the anode and the combination of direct current and electrolytic bath removes pieces of the component, making it smoother. DryLyte® technology replaces the electrolytic bath with solid electrolyte particles in spherical form, which has several advantages.
One of these advantages is that DryLyte® technology not only makes the metal components smoother, but also polishes them at the same time. Particularly in the case of demonstration models, where a shiny surface can be of the utmost importance, this can completely eliminate a separate and time-consuming work step.
Another major advantage is the very low level of toxicity caused by this type of electropolishing. The electrolyte particles have a very low acid concentration, which makes storage, handling and removal possible without additional safety measures - in stark contrast to classic electropolishing or electroplating.
However, the above-average length of the process chain must be mentioned as a disadvantage. The components cannot simply go straight from the printer into the polishing process, but must first be cleaned and degreased, and cleaning work must also be carried out afterwards in order to make the component fully usable.
Furthermore, roughness reduction during electropolishing is limited to a certain degree. Although DryLyte® technology performs better than classic electropolishing, it is still inferior to other technologies such as sandblasting or vibratory finishing.
Companies that produce a large number of small components with low to medium complexity benefit most from DryLyte® technology. Due to the time saved by grinding and polishing at the same time, rapid prototyping can also find massive benefits in this technology.
The Suspended Rotational Force (SRF) technology was launched on the market by US company PostProcess Technologies® in 2019 and is based on the classic vibratory finishing removal process.
However, SRF technology combines this technology with the use of abrasives specially developed for additive manufacturing. SRF also works with software that increases the uniformity of the mechanical force in the container.
The advantages of this technology relate primarily to its precise adaptation to additive manufacturing. PostProcess Technologies® takes an already certified process and adapts it even more precisely to the requirements of additive manufacturing - e.g. through the aforementioned abrasives.
Thanks to the software support and the increased uniformity of the mechanical force, even metal components with very fine details can be gently finished, which means that the areas of application for this technology go beyond those of classic vibratory finishing.
As with vibratory finishing, the acquisition costs are one of the biggest disadvantages. Although the price of the machine with SRF technology, the so-called RADOR™, is in the middle price segment compared to other vibratory finishing machines, it is still more expensive than many other surface finishing machines.
Another disadvantage is that it is tied to PostProcess Technologies® in terms of consumables. Although PostProcess Technologies® now offers a wide range of different abrasive media, if you have very specific requirements, it may be that no suitable abrasive media is available.
SRF technology excels in the mass and serial production of metal components. In contrast to vibratory finishing, it can also refine fine details and is therefore ideal for a wide range of industrial applications. In addition, SRF technology can also be used to finish 3D-printed components using other technologies, e.g. FFF, SLA, MJF and many more.
Our latest process for the surface finishing of 3D printed metal components once again comes from PostProcess Technologies®. Thermal Atomized Fusillade, or TAF for short, was presented in 2022 in the form of the DECI Duo™ surface finishing machine and, unlike SRF, is not based on a classic process, but is a completely proprietary technology.
This works with two vertical and one horizontal jet stream, which emit a mixture of compressed air, cleaning agent and suspended particles onto the component in rapid bursts. The component is placed on a turntable so that the uniaxial jet streams can process the entire component.
The biggest advantage of this new technology is that it can be used to finish even the most complex components. Small details, honeycombs and even internal channels can be processed with this technology - and completely automatically.
Another advantage is that this technology not only refines surfaces, but can also remove support structures. This process is also very versatile in terms of technologies. Although it was developed specifically for metal components, it can also process FFF, PolyJet, SLA, MJF and many other components without any problems thanks to adapted parameters.
The disadvantages of this technology are the same as those of SRF technology. However, the acquisition costs are even higher than those of SRF technology and the dependency is even greater due to the use of multiple consumables.
In terms of consumables, the current selection (May 2024) must also be seen as a disadvantage. To date, only a few different materials are available, which naturally reduces the variety of applications.
Nevertheless, TAF technology is an absolute driving force when it comes to surface finishing of additively manufactured metal components. Thanks to the maximum degree of automation and the ability to finish the most complex structures, this technology is indispensable for companies that require the highest quality with minimal effort.
As this blog post has hopefully made clear, the options for surface finishing metal components are more than diverse - and not all of the options have even been mentioned here.
Which surface finishing option is most suitable for your own production depends heavily on the applications that the component ultimately has to fulfill.
I hope that this blog post has helped you to better sort through the many different surface finishing options for metal components and that you have found the right option for you.
Thank you for your attention - and see you in the next blog post!