3D-Drucker
Hochwertige 3D-Drucker
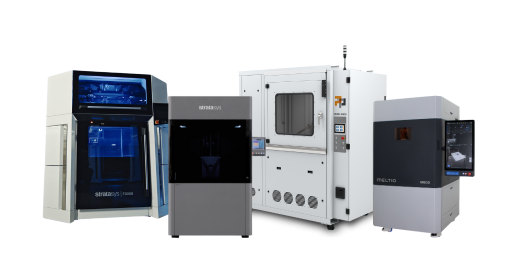
Die Automobilbranche ist seit jeher ein Garant für Fortschritt. Sei es Henry Ford, der 1913 das erste mechanisierte Fließband für die Herstellung des Modell T entwickelte und somit das Automobil der breiten Masse zugänglich machte, oder Ôno Taiichi, der in den 1950ern das „Toyota seisan hôshiki“, eingedeutscht Toyota-Produktionssystem, erfand und damit den Grundstein für das heute industrieübergreifende System der Just-in-Time-Fertigung legte.
Dieser Garant des Fortschritts kam jedoch insbesondere in den letzten Jahren etwas ins Straucheln. Wachsender Druck von Regulatoren und Verbrauchern rund um Energieeffizienz sowie schwächelnde Lieferketten bringen die Automobilbranche in Verzug, einmal mehr ihre Produktionsprozesse zu revolutionieren – und hierbei spielt die Additive Fertigung eine außergewöhnlich wichtige Rolle.
In diesem Blogpost wird es zunächst um die Geschichte der Additiven Fertigung innerhalb der Automobilindustrie gehen. Daraufhin widmen wir uns den Vorteilen, die diese bietet, und zu guter Letzt schauen wir uns einige Anwendungen an, bei welchen der 3D-Druck herkömmliche Produktionsmethoden bereits ersetzen konnte.
Nicht wenige denken beim 3D-Druck an eine sehr neue Technologie, jedoch ist dies ein Irrglaube. Bereits in den frühen 80ern begann die Entwicklung von 3D-Druck-Verfahren, namentlich das SLA- und SLS-Verfahren, und 1988 konnte schließlich der erste 3D-Drucker auf dem Markt erworben werden.
Das Potenzial dieser Technologie haben mehrere Automobilhersteller früh erkannt. Ford kaufte 1988 tatsächlich sogar die dritte 3D-Druckanlage weltweit, um diese Technologie schnellstmöglich für ihre Zwecke validieren zu können. Drei Jahre später sollte BMW folgen und Mitte der 90er auch Volkswagen und Porsche.
Zu dieser Zeit wurde der 3D-Druck ausschließlich für Rapid Prototyping genutzt. Die schnellen Produktionsgeschwindigkeiten und die simplifizierten Abänderungen von Modellen eigneten sich ideal, um Iterationszeiten zu verkürzen und Testverfahren intensiver durchzuführen.
Für Endverbrauchsteile war die Additive Fertigung zu diesem Zeitpunkt jedoch noch nicht geeignet. Und während der 3D-Druck bereits damals die Kosten und den Zeitaufwand für Prototypingprozesse massiv reduzieren konnte, so wurden viele Automobilhersteller von den hohen Anschaffungskosten abgeschreckt.
Zu Beginn der 2010er-Jahre begann schließlich der erste „Hype“ um 3D-Druckanlagen. Neue Hersteller schossen quasi aus dem Nichts hervor, die Materialauswahl wurde massiv erweitert und durch die Entwicklung von Desktop-3D-Druckanlagen konnten auch die Anschaffungskosten minimiert werden.
Eine Vielzahl Automobilhersteller sprang auf den umgangssprachlichen „Hype Train“ auf. Toyota, Fiat, Kia, Chevrolet, Bugatti und viele Weitere hatten den 3D-Druck nun ins Auge gefasst. Zunächst ebenfalls beinahe ausschließlich zum Prototyping, aber durch die massive Verbreiterung der Materialauswahl wurden schnell auch neue Anwendungsgebiete für 3D-gedruckte Teile offengelegt – von Ersatzteilen über „Legacy-Parts“ bis hin zu Endverbrauchsteilen.
Nun ist solch ein Hype Train jedoch selten von langer Dauer. Ob ein Produkt oder eine Technologie diesen Hype wert war, lässt sich am besten daran erkennen, ob es auch nach dem Abflachen dieses weiterhin in Nutzung bleibt. Konnte der 3D-Druck den Hype innerhalb der Automobilindustrie also rechtfertigen?
Die Antwort ließ sich eigentlich bereits aus meinem Vorwort herauslesen und ist ein klares Ja. Alleine in den letzten fünf Jahren wurden die 3D-Druck-Ressourcen bei verschiedenen Automobilherstellern massiv ausgeweitet.
So hat BMW beispielsweise 2020 ihren „Additive Manufacturing Campus“ in Oberschleißheim, unweit von München, eröffnet. Alleine hier sind etwa 50 verschiedene 3D-Druckanlagen im Betrieb mit dem Ziel, die Additive Serienfertigung zu perfektionieren. Jährlich druckt BMW weltweit bereits über 300.000 Komponenten verschiedener Art und zur Eröffnung des AM-Campus sprach Milan Nedeljković, Mitglied des Vorstands der BMW AG, davon, dass die Additive Fertigung „schon jetzt ein integraler Bestandteil“ des Produktionsprozesses bei BMW ist.
Auch Volkswagen spielt weiterhin in der obersten Liga, wenn es um den 3D-Druck von Automobilkomponenten geht. So wurde 2021 die Technologie des Binder Jettings im Stammwerk in Wolfsburg integriert und auch in der Volkswagen Academy in Emden werden Auszubildende inzwischen intensiv in die Nutzung von 3D-Druckern betraut – ein eindeutiger Beweis, dass VW den 3D-Druck als zukunftsweisende Technologie betrachtet.
Aus Zeitgründen lässt sich in diesem Blogpost natürlich nicht jedwede neue Entwicklung und Ausweitung des 3D-Drucks präsentieren, aber einen kleinen Ausblick in die Zukunft möchte ich noch geben. So schätzt das renommierte Marktforschungsinstitut Mordor Intelligence™ die jährliche Wachstumsrate des 3D-Drucks innerhalb der Automobilindustrie auf 21,74 % – von bereits 1,21 Milliarden US-Dollar auf 3,86 Milliarden US-Dollar – und zeigt damit die große Wachstumschance des 3D-Drucks in diesem Sektor auf.
Dass sich die Additive Fertigung in der Automobilindustrie etablieren konnte, lässt darauf schließen, dass sie einige Vorteile mit sich bringen muss, die bei herkömmlichen Fertigungsmethoden nicht gegeben sind – und um exakt diese soll es nun gehen.
Der erste Vorteil ist auch gleichzeitig der, der damals Ford und später auch BMW und Volkswagen zu Frühanwendern des 3D-Drucks gemacht hat. Die außergewöhnlich schnelle Produktionsgeschwindigkeit, die der 3D-Druck ermöglicht, ist insbesondere für das Prototyping, aber auch die Produktion von Ersatzteilen, unerlässlich geworden.
Beim Prototyping erlaubt diese erhöhte Geschwindigkeit Designern und Entwicklern ihre Ideen direkt in die Tat umzusetzen. Dadurch können Designs schneller optimiert, Eigenschaften schneller getestet und potenzielle Fehler schneller ausgemerzt werden. Dieser verringerte Zeitaufwand bei der Produktion sorgen außerdem für eine höhere Sicherheit, da die jeweiligen Entwürfe intensiver getestet werden können.
Im Hinblick auf die Ersatzteile ermöglicht die Additive Fertigung die Perfektionierung des Just-in-Time-Verfahrens. Es werden keine prall gefüllten Lagerhallen benötigt, wenn innerhalb schnellster Zeit neue Bauteile produziert werden können. Somit können einerseits Lagerkosten, durch den verringerten Lagerplatz, als auch das Lagerrisiko gesenkt werden.
Und natürlich ist auch bei Endverbrauchsteilen eine hohe Produktionsgeschwindigkeit nie verkehrt. Eine schnellere Markteinführungszeit sowie eine schnellere Reaktionszeit auf Markt- oder Regulationsänderungen sind nur zwei der vielen Möglichkeiten, die der 3D-Druck für Endverbrauchsteile liefert.
Ein weiterer Vorteil für die Automobilproduktion ist die beinahe uneingeschränkte Designfreiheit, die der 3D-Druck bietet. Dank diesem können komplexeste Merkmale wie Hohlräume, schlangen- und wabenförmige Strukturen oder auch kleinste Details präzise hergestellt und jederzeit repliziert werden.
Diese Designfreiheit hilft einerseits Designern dabei, ihre Ideen uneingeschränkt umzusetzen. In Kombination mit der schnellen Druckgeschwindigkeit und dem geringen Materialverbrauch des 3D-Drucks werden somit auch Experimente neuartiger Formen und Strukturen ermöglicht, durch welche Leistung oder Energieeffizienz erhöht werden können.
Aber nicht nur in der Produktion selbst, sondern auch der Designphase hilft der 3D-Druck beim Thema Energieeffizienz. Durch Topologieoptimierungen, generativem Design und gegebenenfalls dem Einsatz von Gitterstrukturen lassen sich Gewichtsoptimierungen von bis zu 70 % im Gegensatz zu herkömmlichen Fertigungsmethoden erreichen.
Durch diese Gewichtsoptimierung benötigt ein Fahrzeug natürlich weniger Energie, um sich fortzubewegen. Dadurch wird sowohl der Geldbeutel der Nutzer als auch die Umwelt geschützt. Zusätzlich wird durch diese Optimierung der Materialverbrauch reduziert, was sich ebenfalls positiv auf Kosten und Umwelt auswirkt – und uns auch zu unserem nächsten großen Vorteil bringt.
Geringere Emissionswerte sind selbstverständlich mehr als wünschenswert für Kraftfahrzeuge, aber auch was die Produktion angeht, existiert ein großer Drang in Richtung Umweltschutz und Kreislaufwirtschaft – und der 3D-Druck vermag diesen Drang zu stillen.
Während herkömmliche Verfahren subtraktiv arbeiten, produziert der 3D-Druck Bauteile, indem sie Schicht für Schicht aufgebaut werden. Dadurch wird nur das Material benutzt, was für das Bauteil benötigt wird. Der einzige Materialausschuss, der beim 3D-Druck entsteht, sind die Supportstrukturen und im Falle des Resin- und Pulver-3D-Drucks noch etwas überschüssiges Material.
Gerade dieser Pulver-3D-Druck eignet sich jedoch ideal, um den Materialausschuss noch weiter zu minimieren. Denn das überschüssige Material, welches beim Pulver-3D-Druck zeitgleich als Stützstruktur dient, kann problemlos recycelt werden. Rund um den Prozess des Polymer-Pulver-Recyclings finden Sie hier einen passenden Blogpost.
Alles in allem bietet der 3D-Druck also die ideale Möglichkeit, industrielle Produktion umweltfreundlicher zu gestalten und zeitgleich Kosten einzusparen, da ein verringerter Materialausschuss natürlich auch zu geringeren Materialkosten führt.
Bereits unter der hohen Produktionsgeschwindigkeit wurde die Perfektionierung des Just-in-Time-Verfahrens erwähnt. Diese gilt jedoch ebenfalls nicht nur für 3D-gedruckte Automobilkomponenten, sondern für den gesamten Produktionsprozess.
Ein 3D-Drucker kann nämlich auch ideal mit anderen Fertigungsmethoden kooperieren, um die Produktion unabhängiger von potenziellen Lieferkettenschwierigkeiten zu machen, insbesondere durch die Möglichkeit, hauseigene Fertigungshilfsmittel auf Knopfdruck zu produzieren.
Ob Werkzeuge, Halterungen, Vorrichtungen oder Formen aller Art, von Spritzguss- bis Tiefziehformen, der 3D-Druck ermöglicht die individuelle Anpassung dieser Fertigungshilfsmittel an die jeweilige Applikation sowie den schnellen Druck dieser.
Aufgrund der sehr breiten Materialauswahl lassen sich inzwischen auch alle potenziell nötigen Materialeigenschaften für Fertigungshilfsmittel finden – von hitzebeständig und flammhemmend bis flexibel und chemikalienresistent. Dadurch erlaubt der 3D-Druck für alle Prozesse innerhalb der Automobilherstellung eine maximale Unabhängigkeit.
Im letzten Abschnitt dieses Blogposts möchte ich auf einige der verschiedenen Anwendungsbereiche des 3D-Drucks innerhalb der Automobilbranche eingehen. Dabei werde ich die jeweiligen Anwendungen erst einmal grundsätzlich erläutern und zum Schluss ein spezifisches Beispiel nennen, um einen genaueren Einblick in die Möglichkeiten der Additiven Fertigung zu geben.
Da die Vorteile rund um Rapid Prototyping bereits in diesem Blogpost erwähnt wurden, werde ich bei diesen auf eine grundsätzliche Erklärung verzichten und lieber zwei spezifische Beispiele nennen.
Zunächst wäre da Audi, welche inzwischen eine Vielzahl verschiedener Prototypen per 3D-Druck herstellt, beispielsweise Rücklichtabdeckungen mit den Vollfarb-PolyJet™-Druckern von Stratasys®. Diese Vollfarbfähigkeit ermöglicht eine neue Stufe an Realismus bei Prototypen, wodurch der Prototypingprozess noch einmal beschleunigt werden kann.
Ein weiteres, sehr spannendes Beispiel kommt vom Reifenhersteller Michelin®. 2019 haben diese den ersten Prototypen für ihren neuen Reifen mit dem Namen Uptis (Unique Puncture-Proof Tire System) vorgestellt. Dieser 3D-gedruckte Prototypreifen ist vollständig luftlos und verringert somit die Gefahren von Reifenpannen massiv. 2021 wurden auf diesem Reifen die ersten Kilometer gefahren und im Laufe dieses Jahres soll der Reifen auf dem Markt verfügbar sein.
Über eine Vielzahl von Industrien hinweg wünschen sich potenzielle Kunden immer mehr Personalisierung in ihren Produkten und in vielen dieser Industrien wird der 3D-Druck bereits eingesetzt, um diesen Wunsch zu erfüllen – so auch in der Automobilbranche.
Der 3D-Druck kann diesen Wunsch so effizient erfüllen, da die Anpassung des digitalen Modells einfach und schnell erfolgen kann. Im Gegensatz zu vielen herkömmlichen Produktionsmethoden ist auch kein Umrüsten erforderlich – einfach das veränderte Modell zum Druckauftrag hinzufügen und einige Stunden später das modifizierte Bauteil erhalten.
Ein praktisches Beispiel hierfür liefert der Sportwagenhersteller Lamborghini mit seinem Sián Roadster. Die Luftauslässe am Heck des Fahrzeugs, welche mit einem Carbonfaserverbundwerkstoff 3D-gedruckt werden, lassen sich beispielsweise mit Initialien oder kleinen Logos individualisieren, wodurch jeder einzige Sián Roadster zu einem Unikat wird.
Unter Legacy-Teilen versteht man gewisse Komponenten von Fahrzeugen, deren Produktion bereits vor langer Zeit eingestellt wurde. Wird solch ein Legacy-Teil dann benötigt, beispielsweise zur Reparatur, sind die Anschaffungskosten enorm hoch.
Der 3D-Druck kann dieses Problem sehr einfach lösen. Alles, was benötigt wird, ist ein digitales Modell des jeweiligen Teils oder, falls kein digitales Modell vorhanden ist, einen 3D-Scanner, um das alte Bauteil in ein digitales Modell zu verwandeln. Durch bereits vorher genannte Designoptimierungen kann das Legacy-Teil sogar noch verbessert werden. So kann Langlebigkeit, Gewicht, Materialverbrauch und vieles mehr mit dem digitalen Modell angepasst werden.
Diese Vorteile nutzt zum Beispiel der Kleinunternehmer Shane Drake aus Maine. Dieser nutzt 3D-Drucker von Raise3D, um Komponenten für japanische Oldtimer nachzufertigen. Die Kombination aus 3D-Drucker und Handwerkskunst von Shane ermöglichen die ideale Reproduktion dieser Legacy-Teile.
Motorkomponenten zählen zu den teuersten Bauteilen innerhalb der Automobilindustrie. Sie müssen eine außergewöhnliche Haltbarkeit, Hitzebeständigkeit und Widerstandsfähigkeit besitzen, wodurch nur Hochleistungsmaterialien in Frage kommen, und zusätzlich müssen diese Komponenten mit äußerster Präzision hergestellt werden.
Beide diese Voraussetzungen kann der 3D-Druck erfüllen – und zeitgleich noch die Kosten senken. Die bereits erwähnte Materialsparsamkeit kommt hier einmal mehr zum Tragen und sorgt dafür, dass Automobilhersteller massiv Kosten einsparen können.
Aber auch von der hohen Designfreiheit profitieren Motorkomponenten massiv. Dadurch lassen sich beispielsweise komplexe Kühlkanäle produzieren, die das Wärmemanagement verbessern und somit die Effizienz und Lebensdauer von Motoren erhöhen.
Porsche ist einer der Vorreiter für 3D-gedruckte Motorkomponenten. Ein Beispiel beinhaltet 3D-gedruckte Motorkolben im Porsche 911 GT2 RS, die nicht nur 10 % leichter sind, sondern auch integrierte Kühlkanäle besitzen, wodurch eine Leistungssteigerung um 30 PS erreicht werden konnte.
Zum Ende dieses Blogposts stellt sich natürlich die Frage, ob inzwischen sogar vollständig oder zumindest beinahe vollständig 3D-gedruckte Kraftfahrzeuge existieren. Auf wirklich vollständig 3D-gedruckte Autos müssen wir zwar wahrscheinlich noch etwas warten, aber größtenteils 3D-gedruckte Fahrzeuge gibt es sogar mehrere.
Das erste beinahe vollständig 3D-gedruckte Auto wurde tatsächlich bereits 2014 produziert. Den sogenannten „Strati“ stellte Local Motors in Zusammenarbeit mit Cincinnati Incorporated und dem Oak Ridge National Laboratory auf der International Manufacturing Technology Show 2014 in Chicago vor, wobei der Druckprozess nur 44 Stunden andauerte. Die einzelnen Komponenten mussten daraufhin jedoch noch drei Tage gefräst und zusammengebaut werden. Nur die Batterie, Reifen und einige kleinere Komponenten wurden bei diesem Fahrzeug noch mit herkömmlichen Fertigungsmethoden produziert.
Ein weiteres Beispiel ist der Czinger 21C. Bei diesem hybriden Sportwagen wurde beinahe das gesamte Chassis, das Aufhängungssystem sowie die Auspuffkomponenten per Additiver Fertigung produziert. Der Czinger 21C wurde 2020 in London präsentiert, soll jedoch nur auf 80 Modelle limitiert erworben werden können.
Das erste größtenteils 3D-gedruckte Fahrzeug, welches inzwischen auf die Massenproduktion erreicht hat, ist der XEV Yoyo des Start-ups XEV aus Hong Kong. Dieses elektrische Stadtfahrzeug wurde mit Ausnahme der Fenster, dem Chassis und den Sitzen vollständig 3D-gedruckt. Das Fahrzeug befindet sich seit 2021 in der Produktion und erfreut sich dank konkurrenzfähigem Preis und schlankem Design hoher Beliebtheit in Großstädten.
Der 3D-Druck hat sich innerhalb der Automobilbranche innerhalb der letzten Jahre eindeutig etablieren können. Vom Prototypingwerkzeug hat er sich zu einem Garanten für schnelle und hochqualitative Produktion einer Vielzahl verschiedener Automobilkomponenten entwickelt.
Dabei ist die Entwicklung jedoch noch lange nicht am Ende angekommen. Ob Stadtfahrzeug, Sport- oder Rennwagen – eine Vielzahl von Herstellern arbeitet unaufhörlich an neuen Entwicklungen und Fortschritten, um die Vorteile der Additiven Fertigung wirklich für alle Automobilkomponenten zu erschließen.
Wenn Sie immer auf dem neuesten Stand sein wollen, was den 3D-Druck innerhalb der Automobilbranche angeht, dann schauen Sie gerne häufiger auf diesem Blog vorbei – denn wenn es neue Entwicklungen gibt, erfahren Sie sie hier schnellstmöglich!
Vielen Dank für Ihre Aufmerksamkeit – und bis zum nächsten Blogpost!