3D printers
High quality 3D printers
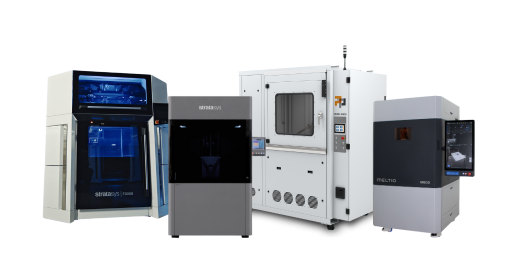
The automotive industry has always been a guarantor of progress. Be it Henry Ford, who developed the first mechanized assembly line for the production of the Model T in 1913 and thus made the automobile accessible to the masses, or Ôno Taiichi, who invented the “Toyota seisan hôshiki”, or Toyota production system, in the 1950s and thus laid the foundation for today's cross-industry system of just-in-time production.
However, this guarantor of progress has been somewhat stumbling in recent years. Growing pressure from regulators and consumers regarding energy efficiency as well as weakening supply chains have put the automotive industry under pressure to revolutionize its production processes once again - and additive manufacturing plays an exceptionally important role in this.
In this blog post, we will first look at the history of additive manufacturing within the automotive industry. We will then look at the benefits it offers and finally, we will look at some applications where 3D printing has already replaced conventional production methods.
Quite a few people think of 3D printing as a very new technology, but this is a misconception. The development of 3D printing processes, namely the SLA and SLS processes, began back in the early 1980s and the first 3D printer was finally available on the market in 1988.
Several car manufacturers recognized the potential of this technology early on. In 1988, Ford actually purchased the third 3D printing system worldwide in order to validate this technology for its purposes as quickly as possible. Three years later, BMW followed suit, and Volkswagen and Porsche in the mid-1990s.
At this time, 3D printing was used exclusively for rapid prototyping. The fast production speeds and simplified modifications of models were ideal for shortening iteration times and carrying out test procedures more intensively.
However, Additive Manufacturing was not yet suitable for end-use parts at that time. And while 3D printing was already able to massively reduce the costs and time required for prototyping processes back then, many car manufacturers were put off by the high acquisition costs.
The first “hype” around 3D printing systems finally began in the early 2010s. New manufacturers emerged virtually out of nowhere, the choice of materials was massively expanded and the development of desktop 3D printing systems also minimized acquisition costs.
A large number of car manufacturers jumped on the colloquial “hype train”. Toyota, Fiat, Kia, Chevrolet, Bugatti and many others had now set their sights on 3D printing. Initially, this was also almost exclusively for prototyping, but the massive expansion of the range of materials quickly opened up new areas of application for 3D-printed parts - from spare parts to “legacy parts” and end-use parts.
However, such a hype train rarely lasts long. The best way to tell whether a product or technology was worth the hype is whether it remains in use even after the hype has died down. So was 3D printing able to justify the hype within the automotive industry?
The answer was already clear from my foreword and is a resounding yes. In the last five years alone, 3D printing resources have been massively expanded at various car manufacturers.
In 2020, for example, BMW opened its “Additive Manufacturing Campus” in Oberschleissheim, not far from Munich. Around 50 different 3D printing systems are in operation here alone with the aim of perfecting additive series production. BMW already prints over 300,000 components of various types worldwide every year, and at the opening of the AM Campus Milan Nedeljković, member of the Board of Management of BMW AG, said that additive manufacturing is “already an integral part” of the production process at BMW.
Volkswagen also continues to play in the top league when it comes to the 3D printing of automotive components.
In 2021, binder jetting technology was integrated into the main plant in Wolfsburg and trainees at the Volkswagen Academy in Emden are now also being intensively trained in the use of 3D printers - clear proof that VW sees 3D printing as a pioneering technology.
Due to time constraints, it is of course not possible to present every new development and expansion of 3D printing in this blog post, but I would like to give a small glimpse into the future. The renowned market research institute Mordor Intelligence™ estimates the annual growth rate of 3D printing within the automotive industry at 21.74% - from 1.21 billion US dollars to 3.86 billion US dollars - and thus shows the great growth opportunity of 3D printing in this sector.
The fact that Additive Manufacturing has been able to establish itself in the automotive industry suggests that it must offer a number of advantages that are not available with conventional manufacturing methods - and this is exactly what we will now be looking at.
The first advantage is also the one that made Ford, and later BMW and Volkswagen, early adopters of 3D printing. The exceptionally fast production speed made possible by 3D printing has become essential for prototyping in particular, but also for the production of spare parts.
In prototyping, this increased speed allows designers and developers to put their ideas directly into practice. As a result, designs can be optimized more quickly, properties can be tested faster and potential errors can be eliminated more quickly. This reduced time required for production also ensures greater safety, as the respective designs can be tested more intensively.
With regard to spare parts, Additive Manufacturing enables the just-in-time process to be perfected. No bulging warehouses are required if new components can be produced in the shortest possible time. This means that storage costs can be reduced due to the reduced storage space, as well as the storage risk.
And of course, a high production speed is never a bad thing, even for end-use parts. A faster time to market and a faster response time to market or regulatory changes are just two of the many possibilities that 3D printing offers for end-use parts.
Another advantage for automotive production is the almost unlimited freedom of design that 3D printing offers. Thanks to this, the most complex features such as cavities, serpentine and honeycomb structures or even the smallest details can be precisely produced and replicated at any time.
On the one hand, this design freedom helps designers to realize their ideas without restrictions. In combination with the fast printing speed and low material consumption of 3D printing, it also enables experimentation with new shapes and structures that can increase performance or energy efficiency.
However, 3D printing not only helps with energy efficiency in the production itself, but also in the design phase. Through topology optimization, generative design and, if necessary, the use of lattice structures, weight optimizations of up to 70% can be achieved compared to conventional manufacturing methods.
As a result of this weight optimization, a vehicle naturally requires less energy to move. This protects both the user's wallet and the environment. In addition, this optimization reduces material consumption, which also has a positive effect on costs and the environment - and also brings us to our next big advantage.
Lower emission values are of course more than desirable for motor vehicles, but there is also a great urge towards environmental protection and a circular economy when it comes to production - and 3D printing is able to satisfy this urge.
While conventional processes work subtractively, 3D printing produces components by building them up layer by layer. This means that only the material that is needed for the component is used. The only material waste generated by 3D printing is the support structures and, in the case of resin and powder 3D printing, some excess material.
However, powder 3D printing in particular is ideal for minimizing material waste even further. This is because the excess material, which also serves as a support structure in powder 3D printing, can be easily recycled. You can find a suitable blog post about the process of polymer powder recycling here.
All in all, 3D printing offers the ideal opportunity to make industrial production more environmentally friendly and save costs at the same time, as reduced material waste naturally also leads to lower material costs.
The perfection of the just-in-time process has already been mentioned under high production speed. However, this also applies not only to 3D-printed automotive components, but to the entire production process.
A 3D printer can also ideally cooperate with other manufacturing methods to make production less dependent on potential supply chain difficulties, particularly through the ability to produce in-house manufacturing aids at the touch of a button.
Whether tools, brackets, fixtures or molds of all kinds, from injection molds to deep-drawing molds, 3D printing enables these production aids to be individually adapted to the respective application and printed quickly.
Thanks to the very wide selection of materials, it is now also possible to find all potentially necessary material properties for production aids - from heat-resistant and flame-retardant to flexible and chemical-resistant. As a result, 3D printing allows maximum independence for all processes within automotive manufacturing.
In the last section of this blog post, I would like to look at some of the different areas of application for 3D printing within the automotive industry. I will first explain the respective applications in principle and then give a specific example to provide a more detailed insight into the possibilities of additive manufacturing.
As the advantages of rapid prototyping have already been mentioned in this blog post, I will refrain from giving a general explanation and instead give two specific examples.
Firstly, there is Audi, which now produces a variety of different prototypes using 3D printing, such as rear light covers using Stratasys® full-color PolyJet™ printers. This full-color capability enables a new level of realism in prototypes, which can further accelerate the prototyping process.
Another very exciting example comes from tire manufacturer Michelin®. In 2019, they presented the first prototype for their new tire called Uptis (Unique Puncture-Proof Tire System). This 3D-printed prototype tire is completely airless and thus massively reduces the risk of punctures. The first kilometers were driven on this tire in 2021 and the tire should be available on the market later this year.
Across a variety of industries, potential customers want more and more personalization in their products and in many of these industries, 3D printing is already being used to fulfill this desire - including the automotive industry.
3D printing can fulfill this desire so efficiently as the customization of the digital model can be done easily and quickly. In contrast to many conventional production methods, no retooling is required - simply add the modified model to the print job and receive the modified component a few hours later.
A practical example of this is provided by the sports car manufacturer Lamborghini with its Sián Roadster. The air outlets at the rear of the vehicle, which are 3D printed using a carbon fibre composite material, can be customized with initials or small logos, for example, making every single Sián Roadster unique.
Legacy parts are certain vehicle components whose production was discontinued a long time ago. If such a legacy part is then needed, for example for repairs, the acquisition costs are extremely high.
3D printing can solve this problem very easily. All that is needed is a digital model of the part in question or, if no digital model is available, a 3D scanner to convert the old part into a digital model. The legacy part can even be improved through the aforementioned design optimizations.
Durability, weight, material consumption and much more can be adjusted with the digital model.
Small business owner Shane Drake from Maine, for example, makes use of these advantages. He uses 3D printers from Raise3D to reproduce components for vintage Japanese cars. The combination of 3D printers and Shane's craftsmanship allow for the ideal reproduction of these legacy parts.
Engine components are among the most expensive parts in the automotive industry. They must have exceptional durability, heat resistance and resilience, which means that only high-performance materials can be used, and these components must also be manufactured with extreme precision.
3D printing can fulfill both of these requirements - and reduce costs at the same time. The aforementioned material economy comes into play here once again and ensures that car manufacturers can make massive cost savings.
However, engine components also benefit massively from the high degree of design freedom. This makes it possible, for example, to produce complex cooling channels that improve heat management and thus increase the efficiency and service life of engines.
Porsche is one of the pioneers of 3D-printed engine components. One example includes 3D-printed engine pistons in the Porsche 911 GT2 RS, which are not only 10% lighter, but also have integrated cooling channels, resulting in a 30 hp increase in performance.
At the end of this blog post, the question naturally arises as to whether fully or at least almost fully 3D-printed cars now exist. We will probably have to wait a little longer for truly fully 3D-printed cars, but there are several vehicles that are mostly 3D-printed.
The first almost fully 3D-printed car was actually produced back in 2014. The so-called “Strati” was presented by Local Motors in collaboration with Cincinnati Incorporated and the Oak Ridge National Laboratory at the 2014 International Manufacturing Technology Show in Chicago, with the printing process taking just 44 hours. However, the individual components then had to be milled and assembled over a further three days. Only the battery, tires and some smaller components of this vehicle were still produced using conventional manufacturing methods.
Another example is the Czinger 21C. Almost the entire chassis, suspension system and exhaust components of this hybrid sports car were produced using additive manufacturing. The Czinger 21C was presented in London in 2020, but only 80 models will be available for purchase.
The first largely 3D-printed vehicle to reach mass production is the XEV Yoyo from Hong Kong start-up XEV. This electric city vehicle was completely 3D printed with the exception of the windows, chassis and seats. The vehicle has been in production since 2021 and is very popular in large cities thanks to its competitive price and sleek design.
3D printing has clearly established itself within the automotive industry in recent years. From a prototyping tool, it has developed into a guarantor for fast and high-quality production of a variety of different automotive components.
However, this development is far from over. Whether city cars, sports cars or racing cars - a large number of manufacturers are constantly working on new developments and advances to really make the benefits of additive manufacturing available for all automotive components.
If you want to keep up to date with the latest developments in 3D printing within the automotive industry, then please check this blog often - because if there are any new developments, you will find them here as soon as possible!
Thank you for your attention - and until the next blog post!