3D printers
High quality 3D printers
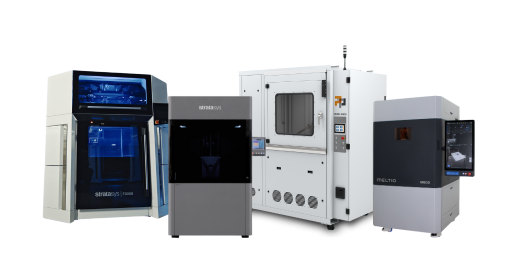
High-quality 3D printing solutions for demanding projects
Order Parts now!The perfect symbiosis of quality and quantity!
Complex geometries with ideal properties!
High-resolution components with a wide variety of materials!
High-performance components with sustainable production!
A wide range of materials and ultra-fast production!
Ideal for a wide range of dental indications!
The process from simple component to product!
Fully automate your production!
Fast processing and successful management!
Sorry, there are no results for this combination of filters. Choose another combination of filters.
To ensure that all requests are handled promptly and completely, we ask that you submit all support requests through our support portal.
To the service portalDo you need assistance with your project, do you need advice or a sample part that we can send you?
Send EmailWith its Live Sinter™ software, Desktop Metal® offers the ideal solution for compensating for shrinkage and deformation during the sintering process. Using complex algorithms, the software calculates how the component will be deformed during the sintering process before the printing process and automatically compensates for this by creating an adapted offset model.
Traditionally, sacrificial structures are used to prevent sintering shrinkage and distortion. However, these are not only costly in the long term, but can also lead to other problems such as cracks or fractures in the component because they fight against shrinkage and distortion. With Desktop Metal® Live Sinter™ and the automatically created offset model, however, these dangers are eliminated because the natural process of shrinkage and warpage is no longer fought against, but instead exploited to obtain a perfect component at the end.
To create an ideal off-set model, the Live Sinter™ software uses an advanced sintering simulation that is customized for each component to simulate non-linear shrinkage, friction, elastic and plastic deformations, and density variations. These simulations are designed to be interactive, allowing users to see exactly how the off-set model was created.
Desktop Metal®'s Live Sinter™ software offers the option of automatically generating support structures. These are optimally designed for the respective component, reducing material consumption and integrating distortion compensation.
To minimize tolerances even further, Desktop Metal® Live Sinter™ offers the option of optimization using scan data. This helps to prevent even complex distortion effects in future parts. The scan-based adjustment affects the entire volume of the part, ensuring that thin walls and hidden interior areas move in unison with the exterior areas.
Cookie settings
We use cookies to provide you with the best possible experience. They also allow us to analyze user behavior in order to constantly improve the website for you. Privacy Policy