3D printers
High quality 3D printers
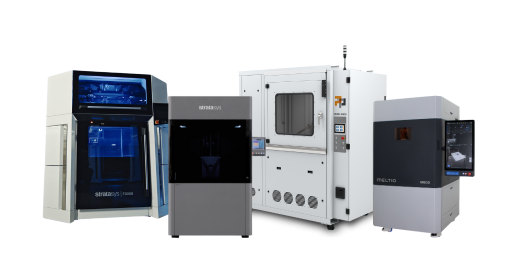
The Meltio Engine CNC Integration is a unique hybrid manufacturing technology that enables the smooth integration of additive and subtractive manufacturing processes.
The Meltio Engine CNC Integration is a novel hybrid manufacturing technology that converts existing CNC machines into multi-purpose metal 3D printing platforms. This system easily connects Meltio's innovative wire-laser deposition technology with standard CNC machining capabilities, allowing manufacturers to mix additive and subtractive processes in one workflow. The Meltio Engine has a compact deposition head with six low-power lasers capable of processing metal welding wire, and it can be simply retrofitted to practically any CNC machine with no size limitations.
This integration provides considerable benefits for near-net shape manufacturing, part repair, and feature enhancements or addition to existing components. The method enables the fabrication of complex shapes with machining tolerances in the same process. The Meltio Engine CNC Integration, with its user-friendly interface and dedicated software for toolpath development and process control, allows machine shops and manufacturers to increase their capabilities at a low cost. It can handle a wide range of materials, including stainless steel, mild steel, titanium, and Inconel, making it suited for industries such as aerospace, automotive, and general machining. This method marks a significant step forward in hybrid manufacturing technology by combining the geometric freedom of additive manufacturing with the precision of subtractive procedures.
Technical Specifications:
Print Envelope: Depends on the Integration
Laser System: 9 diode lasers with a total of 1000 watts
Laser Wavelength: 450 nm (blue)
By integrating the Meltio Engine into current CNC machines, users may integrate additive and subtractive manufacturing processes in a single workflow. This enables the fabrication of highly complicated items with machining tolerances in the same process. The method allows for metal 3D printing and machining of sophisticated geometries in a single step, considerably increasing the range of items that may be created and the efficiency with which they are manufactured.
By utilizing the M600 print head, the Blue Laser technology is also utilized in the Meltio Engine CNC Integration. These 450nm wavelength blue lasers significantly increase speed – an amazing 60% when comparing the M450 to the M600 print head – when compared to traditional near infrared and green lasers. In addition, these blue lasers reduce energy consumption because light with a shorter wavelength has higher absorption rates. This also increases the range of materials, making the Meltio Engine CNC Integration highly effective with reflective materials such as copper and aluminum.
The Meltio Engine is an affordable solution to add metal 3D printing capabilities to existing CNC machines. This retrofitting strategy enables machine shops to increase their services and capabilities without making major investments in separate, dedicated additive manufacturing systems. Companies that leverage existing equipment can enter the field of metal additive manufacturing with cheaper starting costs and a faster return on investment.
Scalability is one of the most significant advantages of the Meltio Engine CNC Integration. There are no inherent size limits because the working envelope is only restricted by the size of the CNC machine's motion system. This enables the manufacture of large-scale parts that would be unfeasible or prohibitive using standalone 3D printers. Furthermore, the system's versatility in terms of material compatibility, including stainless steel, mild steel, titanium, and Inconel, makes it appropriate for a wide range of industrial applications.
The Dual Wire option further expands the Meltio Engine CNC Integration's versatility by allowing users to combine different metals such as stainless steel, carbon steel, titanium alloys, and Inconel in a single print job. This feature gives new opportunities for developing parts with optimised performance characteristics, as different regions of a component can be printed using materials that are best suited to their unique needs. The Meltio Engine CNC Integration's rapid material switching boosts production by eliminating downtime while also allowing for more efficient use of expensive materials. Furthermore, it increases design flexibility, allowing engineers to develop complicated parts with varied material properties throughout their structure.
The Meltio Engine CNC Integration continuously checks and adjusts important printing settings in real time, ensuring that part quality remains consistent throughout the process. Laser modulation provides fine control over the energy input, adjusting to changes in material properties or geometry to maintain ideal melting conditions. Simultaneously, the wire modulation system adjusts the feed rate and location of the metal wire, enabling precise material deposition. This synergistic management of laser and wire allows the system to respond dynamically to variables in the printing process, such as changes in heat accumulation or component geometry. This control system's closed-loop design allows it to automatically compensate for any deviations from the planned parameters, lowering the likelihood of faults and improving overall part quality.
This system uses CNC machining precision in conjunction with Meltio's sophisticated wire-laser deposition technology to repair broken parts, add new features to existing components, or enhance portions with various materials. The process starts with employing the CNC capability to remove damaged regions or prepare surfaces for material addition. The Meltio Engine's additive manufacturing capabilities are then utilised, depositing material with great accuracy to rebuild worn portions, add new geometries, or enhance existing parts with changing material qualities. This hybrid technique enables previously unachievable or economically impracticable repairs, increasing the useful life of critical components and decreasing the need for complete part replacement.
The Meltio Engine CNC Integration has exceptional material compatibility, making it an excellent choice for a variety of metal additive manufacturing applications. The system can handle a wide variety of metals, including stainless steel, mild steel, carbon steel, titanium alloys, nickel alloys and even copper and aluminium. This diversity enables users to choose the best material for their unique project needs, such as corrosion resistance, high strength, or heat tolerance. The Meltio Engine CNC Integration's ability to work with titanium alloys is also important, since it offers new opportunities in the aerospace and medical industries, where lightweight, strong materials are critical.
The Meltio Engine's hybrid manufacturing capabilities enable the fabrication of complex geometries with tight machining tolerances, which is critical for aircraft components. The system's capacity to fix and add features to existing parts is very useful in this industry, since component modification and maintenance are frequently necessary. The connection with CNC machines enables wide-scale manufacturing capabilities, making it appropriate for producing big aircraft components at a low cost.
Its ability to produce big parts fast and work with a wide range of metals, including lightweight alloys, makes it excellent for designing custom components, prototypes, and small-batch production parts. The hybrid manufacturing process enables the fabrication of complex geometries with accurate finishing, which is critical for maximising performance in automotive applications. The system's capacity to handle materials such as aluminium and titanium is especially useful for producing lightweight, high-strength components, which are required in modern car design and racing applications.
The system's ability to deal with corrosion-resistant alloys such as stainless steel and Inconel is critical for creating components that can withstand extreme conditions. The enormous build volume enables for the production of big parts, and the ability to repair and add features to existing components is extremely useful for maintaining and updating equipment in remote areas. This skill can drastically cut downtime and logistics costs in the energy industry. The hybrid manufacturing approach also enables the creation of complex parts with internal channels or distinct geometries, which are frequently required in energy applications.
The system's ability to produce entire parts, add features to existing components, and perform repairs all in one configuration allows machine shops to generate new revenue streams and boost their competitiveness. Because of their capacity to work with a variety of materials and make parts with complex geometries, these shops can take on more diversified and challenging projects.