3D printers
High quality 3D printers
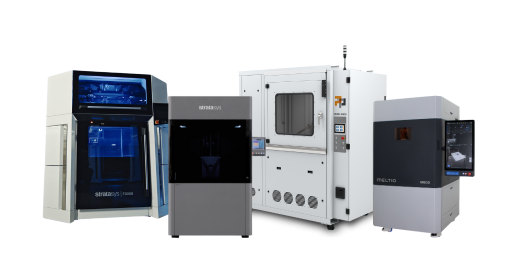
25% discount on your first order of 3D printed components!
SAVE SUMMER DISCOUNT NOW!The perfect symbiosis of quality and quantity!
Complex geometries with ideal properties!
High-resolution components with a wide variety of materials!
High-performance components with sustainable production!
A wide range of materials and ultra-fast production!
Ideal for a wide range of dental indications!
The process from simple component to product!
Fully automate your production!
Fast processing and successful management!
Sorry, there are no results for this combination of filters. Choose another combination of filters.
To ensure that all requests are handled promptly and completely, we ask that you submit all support requests through our support portal.
To the service portalDo you need assistance with your project, do you need advice or a sample part that we can send you?
Send EmailThe SAF™ PowderEase™ T1 leverages precision powder management technology to optimize material recovery and dosing, enabling highly accurate powder recycling that minimizes waste while maintaining consistent part quality and manufacturing performance.
Stratasys® and Rösler AM Solutions collaborated to develop the SAF™ PowderEase™ T1, a 3-in-1 post-processing solution for the Stratasys® H350 SAF™ powder bed printer. This groundbreaking technology integrates and automates three important processes: powder breakout, retrieval, and dosing, considerably lowering manual labor and expediting additive manufacturing workflows. The PowderEase™ T1 is intended to manage the output of up to six H350 printers at once, providing outstanding scalability and efficiency.
One of the PowderEase™ T1's main advantages is its capacity to save time and reduce waste in the post-processing step. According to tests and comparisons, the system can save up to 50 minutes per build over manual operations. Furthermore, it encourages efficient powder use, reduces waste, and ensures traceability and hygiene.
Technical Specifications:
Platform Size: 500 x 400 mm
Loading Capacity: 2 full builds without refilling
Operating Temperature Range: 15 - 30 °C
Extraction Rate: 150 m³/h
The PowderEase™ T1 combines and automates three important post-processing operations: powder breakout, retrieval, and dosing, into a single, integrated system.
The powder breakout process entails removing extra powder from printed parts, which is often a time-consuming manual activity. The PowderEase™ T1 automates this process by applying innovative vibration and air flow techniques to efficiently extract loose powder from the pieces while preserving the printed structures.
The retrieval phase focuses on collecting the removed powder for possible reuse. The device collects loose powder using a sophisticated suction mechanism and accurate filtration to minimize contamination in order to preserve powder quality and minimize material waste.
The dosing operation is crucial for ensuring consistent print quality. The PowderEase™ T1 includes high-precision dosing mechanisms that use a combination of gravimetric and volumetric approaches to assure proper powder distribution for future print jobs. This precise control over powder quantities and combination ratios is critical for producing consistent outcomes in additive manufacturing.
The PowderEase™ T1's scalable efficiency is a key characteristic that dramatically improves additive manufacturing operations. This scalability translates into optimal resource use. Manufacturers can considerably reduce their equipment footprint and expenses by centralizing post-processing for many printers. Instead of requiring separate post-processing devices for each printer, a single PowderEase™ T1 can handle the output from up to six machines, making better use of manufacturing floor space.
The PowderEase™ T1's capacity to save up to 50 minutes of time each build compared to manual techniques is a significant step forward in additive manufacturing efficiency. This reduction in time is achieved by automating three important post-processing operations: powder breakout, retrieval, and dosing. Manufacturers can enhance throughput without extending their equipment footprint or manpower by using shorter turnaround times. This increased efficiency enables more responsive production cycles and potentially shorter lead times for clients.
The PowderEase™ T1 system exhibits superior powder management capabilities, which considerably improve the productivity and sustainability of additive manufacturing processes. The system's enclosed design and integrated extraction system (with a rate of 150m³/h) contribute to a clean workspace and operator safety by reducing powder exposure. The PowderEase™ T1 has an automated sieving system with a 300 mm screen and a mesh width of 250 μm². This fine sieving process is necessary to remove any impurities or agglomerated particles from the recovered powder, ensuring that only high-quality powder is returned to the manufacturing process. It uses sophisticated mechanisms to ensure accurate dosing (mixing of used and virgin powders) and constant powder dispersion, which are critical for sustaining part quality and process reliability.
The PowderEase™ T1 is compliant with various significant certifications and standards, including:
- ISO 8573-1 Class 2:4:2 for compressed air quality.
- REACH (Registration, Evaluation, Authorization, and Restrictions of Chemicals)
- RoHS (Restricted Hazardous Substances)
- WEEE (Waste Electric and Electronic Equipment)
- Modern Slavery Act
- Conflict Minerals Regulation
The PowderEase™ T1 complies with these standards and has features that assure traceability and cleanliness, providing manufacturers with a solution that not only enhances efficiency but also meets the demanding criteria of regulated industries. These certifications show Stratasys®' dedication to environmental responsibility, ethical sourcing, and product safety.
Call or email us and we will be happy to help you.
Fill up the form below and we will send you the data sheet by e-mail.
Cookie settings
We use cookies to provide you with the best possible experience. They also allow us to analyze user behavior in order to constantly improve the website for you. Privacy Policy