3D printers
High quality 3D printers
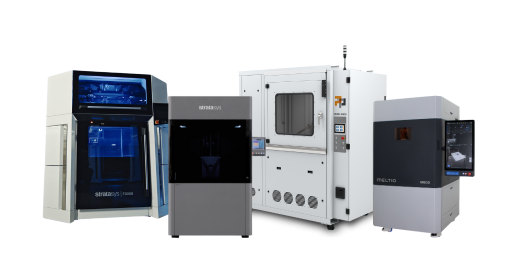
25% discount on your first order of 3D printed components!
SAVE SUMMER DISCOUNT NOW!The perfect symbiosis of quality and quantity!
Complex geometries with ideal properties!
High-resolution components with a wide variety of materials!
High-performance components with sustainable production!
A wide range of materials and ultra-fast production!
Ideal for a wide range of dental indications!
The process from simple component to product!
Fully automate your production!
Fast processing and successful management!
Sorry, there are no results for this combination of filters. Choose another combination of filters.
To ensure that all requests are handled promptly and completely, we ask that you submit all support requests through our support portal.
To the service portalDo you need assistance with your project, do you need advice or a sample part that we can send you?
Send EmailThe PostPro DPX is a compact depowdering system with ATEX certification and a powerful filtration system that is designed to efficiently post-process 3D printed parts, significantly reducing manual labor while improving batch-to-batch consistency.
The PostPro DPX is an efficient depowdering system designed to speed up the post-processing of 3D printed items, particularly those created with powder bed fusion methods such as SLS, SAF and MJF. The DPX, with its ample 10-liter basket capacity, can accommodate a wide range of part sizes, allowing for high-volume throughput while assuring complete cleaning. This technology automates the removal of surplus powder with high-pressure compressed air and specifically designed abrasive media, which not only increases production but also protects the printed components. By reducing manual work and improving batch-to-batch uniformity, the PostPro DPX improves operational efficiency in additive manufacturing settings.
The PostPro DPX has a user-friendly touchscreen HMI (Human-Machine Interface), an ionization unit that effectively reduces static build-up during the cleaning process, is ATEX certified, ensuring compliance with safety regulations for environments containing combustible dust, and a powerful filtration system that efficiently captures airborne dust particles generated during depowdering.
Technical specifications:
Basket Size: Ø450 x 210 mm
Basket Volume: 10 liters
Basket Loading Weight: 10 kg
Blast Gun: Single with Ø6 mm nozzle
Air Consumption: 700l/min at 4 bar
The PostPro DPX has a decent 10-liter basket capacity, which accommodates a variety of part sizes while providing complete cleaning during the depowdering process. This decent-sized volume enables the simultaneous processing of several components, which boosts productivity in areas where fast throughput is critical. The basket has a soft plastic liner that prevents components from injury while cleaning and allows for optimal mixing and rotation of parts within the basket, ensuring that all surfaces are thoroughly cleaned of superfluous powder.
The PostPro DPX is equipped with a user-friendly touchscreen HMI (Human-Machine Interface) that simplifies parameter modifications and operational control. This user-friendly interface enables operators to easily select cleaning recipes, monitor the depowdering process in real time, and make any changes on the fly. The touchscreen interface streamlines the user experience, reducing training time for new operators and increasing overall operational efficiency, making it accessible to users of diverse technical competence.
The PostPro DPX's integrated ionization unit reduces static build-up during the depowdering process. Static electricity can draw small powder particles back to cleaned surfaces, reducing the quality of the completed items. The technology uses ionized air to effectively neutralize static charges, ensuring that components remain dust-free after cleaning and reducing the need for further post-processing operations. This function is very useful for maintaining high-quality standards in businesses like dental and jewelry production.
The PostPro DPX was designed with space efficiency in mind, and its compact form factor makes it ideal for small workshops and laboratories. Despite its compactness, the system does not sacrifice performance or safety; it is ATEX certified to Class II 3/-D T125°C, assuring compliance with high safety criteria for situations containing flammable dust. This certification makes it an excellent alternative for enterprises working in industries that demand the safe handling of potentially hazardous products while maximizing workspace usage.
The PostPro DPX comes with a strong filtration system that effectively separates dust particles produced during the depowdering process. This technology not only keeps the workspace clean, but it also provides a good view of the blasting area, which improves operator safety and comfort. By effectively catching airborne dust particles, the filtering system promotes a healthier working environment and aids in compliance with workplace safety laws. Overall, this functionality demonstrates AMT's dedication to providing comprehensive solutions that prioritize operational efficiency and user safety in additive manufacturing processes.
The PostPro DPX works with all standard engineering abrasive materials, including glass and ceramics. This versatility enables customers to choose the best medium for their unique depowdering requirements, ensuring successful removal of surplus powder from 3D printed items made with technologies such as SLS, SAF™ and MJF. The technology automates the cleaning process by combining high-pressure compressed air with the abrasive medium of choice, improving efficiency and consistency in post-processing.
Fill up the form below and we will send you the data sheet by e-mail.
Cookie settings
We use cookies to provide you with the best possible experience. They also allow us to analyze user behavior in order to constantly improve the website for you. Privacy Policy