3D printers
High quality 3D printers
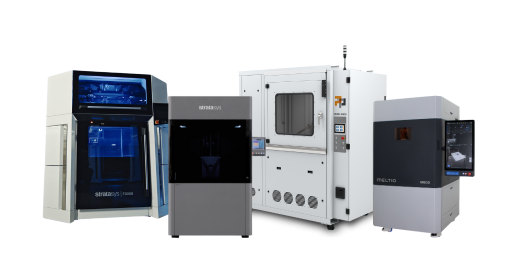
25% discount on your first order of 3D printed components!
SAVE SUMMER DISCOUNT NOW!The perfect symbiosis of quality and quantity!
Complex geometries with ideal properties!
High-resolution components with a wide variety of materials!
High-performance components with sustainable production!
A wide range of materials and ultra-fast production!
Ideal for a wide range of dental indications!
The process from simple component to product!
Fully automate your production!
Fast processing and successful management!
Sorry, there are no results for this combination of filters. Choose another combination of filters.
To ensure that all requests are handled promptly and completely, we ask that you submit all support requests through our support portal.
To the service portalDo you need assistance with your project, do you need advice or a sample part that we can send you?
Send EmailThe PostPro DP MAX is a highly automated depowdering and shot blasting machine designed for high productivity in large-scale manufacturing, with continuous tumble belt technology and a 63-liter processing volume.
The PostPro DP MAX is a fully automated 2-in-1 depowdering and shot blasting equipment that maximizes throughput when post-processing 3D printed products. Using continuous tumble belt technology, the system has a generous 63-liter processing volume, making it ideal for large component and batch production runs. This revolutionary design enables effective cleaning and surface finishing of parts while minimal operator involvement, hence optimizing the whole operation. The PostPro DP MAX considerably improves productivity by combining depowdering and shot blasting capabilities, allowing manufacturers to process many components fast and efficiently.
The PostPro DP MAX's user-friendly interface, driven by a Siemens S7-1200 PLC, allows for smooth interaction with external Manufacturing Execution Systems (MES). The system's ergonomic front-loading design allows operators to readily access and load parts from a comfortable working height, increasing usability. Furthermore, the reversible belt controls allow for autonomous loading and unloading of components from shipping containers, increasing operational efficiency and reducing downtime between batches. The PostPro DP MAX also has advanced technologies such as an ionization unit and a cyclone dust separation system.
Technical specifications:
Processing Belt Dimensions: Ø590 x 770 mm
Processing Belt Volume: 63 liters
Processing Belt Maximum Load: 30 kg
Blast Guns:Triple Ø8 mm nozzle
The PostPro DP MAX uses continuous tumble belt technology, which is critical for improving the cleaning and finishing of 3D printed components. This revolutionary design enables components to be processed in a dynamic, rolling motion, ensuring that every surface is evenly exposed to the cleaning material. The system's enormous 63-liter processing volume allows producers to handle several items simultaneously without sacrificing productivity. This continual movement not only improves the thoroughness of the depowdering process, but also greatly reduces cycle times when compared to static systems. As a result, producers may achieve faster throughput rates, making the PostPro DP MAX ideal for high-volume manufacturing applications where time and efficiency are important.
The PostPro DP MAX's ergonomic front-loading design is specifically engineered to improve operator comfort and production efficiency. By allowing users to load and unload parts at a comfortable working height, this feature reduces physical strain and tiredness during operation. The design features convenient access ports for speedy component loading, which is critical in fast-paced manufacturing environments. Additionally, the reversible belt controls allow for automatic loading and unloading from transport containers, considerably saving manual handling time. This user-centric approach not only boosts productivity by speeding up the entire process, but it also promotes a safer work environment by lowering the risk of damage from repetitive lifting and awkward postures.
Static electricity can present considerable issues in post-processing, particularly when cleaning 3D printed parts. The PostPro DP MAX tackles this issue through its enhanced ionization unit, which produces ionized air throughout the cleaning cycle. This method successfully neutralizes static charges that can attract small powder particles back to cleaned surfaces, guaranteeing that the parts are completely dust-free. By eliminating static buildup, the ionization unit removes the need for further cleaning procedures after depowdering, optimizing the whole operation. This capability is especially significant in industries like aerospace and medical devices, where surface integrity and cleanliness are critical to guaranteeing product performance and regulatory compliance.
The incorporation of a Siemens S7-1200 PLC in the PostPro DP MAX improves operational capabilities by allowing for smooth communication with external Manufacturing Execution Systems (MES). This programmable logic controller enables operators to monitor and regulate manufacturing processes in real time, providing useful information about operational efficiency. Users can design, update, and save programmable cleaning recipes directly from an easy touchscreen interface, allowing for rapid alterations based on unique material needs or component geometries. This level of digital connectivity allows manufacturers to make data-driven decisions and optimize their workflows for optimal efficiency. The PostPro DP MAX maintains consistent quality over several production runs by allowing you fine control over the cleaning process.
The PostPro DP MAX's effective dust management system comprises a powerful cyclone dust separation mechanism, which is critical for keeping a clean working environment. This technology successfully filters away blast media and dust generated during operation, reducing collection within the chamber and ensuring maximum visibility for workers. The high extraction rate ventilator improves air quality by reducing airborne particles that may represent a health concern or interfere with production activities. This feature, which prioritizes cleanliness and safety, not only contributes to a more productive workplace but also adheres to best practices for health and safety compliance in manufacturing environments.
The PostPro DP MAX includes a quick-clean sealed dust bin for optimum waste management during operation. This convenient design enables operators to effortlessly dispose of gathered dust and powder without causing a mess or being exposed to potentially harmful chemicals. The dust bin's sealed design ensures that contaminants are safely confined, creating a safer working environment by lowering the danger of airborne dust exposure. Furthermore, this feature makes maintenance easier by enabling for the rapid removal and replacement of waste materials without disrupting production flow. The quick-clean sealed dust container improves waste management procedures, increasing overall operational efficiency while also enabling compliance with health and safety laws in production environments.
Fill up the form below and we will send you the data sheet by e-mail.
Cookie settings
We use cookies to provide you with the best possible experience. They also allow us to analyze user behavior in order to constantly improve the website for you. Privacy Policy