3D printers
High quality 3D printers
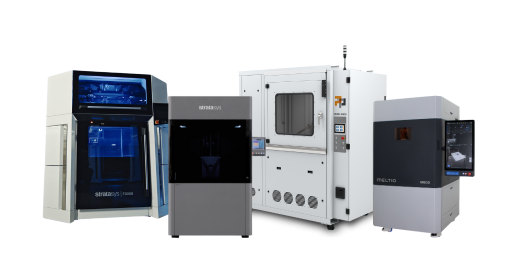
25% discount on your first order of 3D printed components!
SAVE SUMMER DISCOUNT NOW!The perfect symbiosis of quality and quantity!
Complex geometries with ideal properties!
High-resolution components with a wide variety of materials!
High-performance components with sustainable production!
A wide range of materials and ultra-fast production!
Ideal for a wide range of dental indications!
The process from simple component to product!
Fully automate your production!
Fast processing and successful management!
Sorry, there are no results for this combination of filters. Choose another combination of filters.
To ensure that all requests are handled promptly and completely, we ask that you submit all support requests through our support portal.
To the service portalDo you need assistance with your project, do you need advice or a sample part that we can send you?
Send EmailWelcome to a new era of custom manufacturing. Use the 3D printer to create large-format components with a positioning accuracy of 10 µm with reliable repeatability.
The Argo 1000 is a high-temperature industrial 3D printer from Italian manufacturer Roboze. With its extruder capable of reaching 450°C and build envelope that heats up to 180°C, the ARGO 1000 is compatible with superpolymers and composites such as PEEK, Carbon Peek, Helios PEEK 2005, Carbon PA and Ultem AM9085F, as well as polymers such as PC LEXAN EXL AMHI240F, FUNCTIONAL-NYLON, ABS-ESD, PP, FLEX-TPU, STRONG-ABS and ULTRA-PLA.
Technical data:
Construction volume: 1000 x 1000 x 1000 mm
Accuracy: XY:10µm ; Z:25µm
High-definition profile: 0.225 mm
Standard profile: 0.300 mm
The construction material can be printed with a water-soluble support when the extrusion head is equipped with two extruders. Alternatively, the printing process can be used in IDEX (Independent Dual Extruder) mode, which enables printing to be duplicated in a single cycle, boosting productivity and efficiency.
Based on the utilization of pellets as a raw material, hypermelt technology represents a new paradigm in the additive production of high performance polymers. Large format items made of a variety of advanced materials, such as super polymers like PEKK and ULTEM 9085, composites like PA and PEEK filled with carbon fiber, elastomers, recycled materials, and bio-based polymers, can actually be produced thanks to this creative method. Produce parts with a production speed 10 times higher (with an extrusion rate of up to 2 kg/h) and costs reduced by up to 60% compared to filament methods and maintaining a high deposition accuracy.
Roboze has a beltless system, with a patented direct mechatronic movement of the X and Y axis through a gear rail. The system guarantees high mechanical precision and unparalleled positionability for a constant production process.
The ARGO 1000's innovative extrusion mechanism, called the HVP extruder, enables the printing of superpolymers and composites. 3D printing takes place at up to 450 °C and with different extruders adapted to the filament.
The Roboze Argo 1000 has the largest ARGO series build volume, with a 1000 x 1000 x 1000 mm (39.37 3x 39.37 x 39.37 in).
The production process of the Roboze ARGO 1000 is optimized to print parts with the best performing characteristics, offering fast and flexible production.
The Roboze ARGO 1000 features an industrial automation system that integrates seamlessly into your production workflow. This system allows you to schedule the production of parts, analyze data, and quickly detect and resolve downtime, increasing efficiency and reducing the likelihood of print failures.
The Roboze ARGO 1000 is equipped with remote maintenance modules that help detect malfunctions and reduce the likelihood of downtime for the benefit of production. The Roboze ARGO 1000 can evolve over time to incorporate new features, parameters and data as the remote management function automatically provides software updates.
To achieve excellent mechanical properties and maintain dimensional tolerances on the generated object, a 3D printing process, from superpolymers and composites, requires a homogeneously heated chamber. Years of research and development of all elements involved led to the Roboze heating chamber technology. The culmination of this technology is the Roboze ARGO 1000.
The superpolymers and composites produced by Roboze are already available on the market and can be used instead of metal alloys when high temperatures, strong chemical resistance and mechanical properties are required. Hundreds of companies, with the support of Roboze and thanks to the commercial partnership with Solvay, have transformed their production processes and replaced metals. As a result, time and costs have been optimized.
Using ULTEM AM9085F, Roboze technology has been able to produce cup holders that save up to 71% of costs.
By using carbon PA instead of metal, a centering device was developed that reduced the number of parts in the bearing by 92%.
By using PEEK, Roboze technology, 39% of costs could be saved in the production of bus bar holders.
By using carbon PEEK instead of specially alloyed brass, gears could be produced and their weight reduced by 84%.
Fill up the form below and we will send you the data sheet by e-mail.
Cookie settings
We use cookies to provide you with the best possible experience. They also allow us to analyze user behavior in order to constantly improve the website for you. Privacy Policy