3D printers
High quality 3D printers
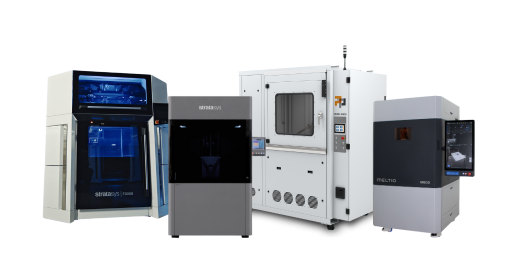
25% discount on your first order of 3D printed components!
SAVE SUMMER DISCOUNT NOW!The perfect symbiosis of quality and quantity!
Complex geometries with ideal properties!
High-resolution components with a wide variety of materials!
High-performance components with sustainable production!
A wide range of materials and ultra-fast production!
Ideal for a wide range of dental indications!
The process from simple component to product!
Fully automate your production!
Fast processing and successful management!
Sorry, there are no results for this combination of filters. Choose another combination of filters.
To ensure that all requests are handled promptly and completely, we ask that you submit all support requests through our support portal.
To the service portalDo you need assistance with your project, do you need advice or a sample part that we can send you?
Send EmailThe QLS 236 from Nexa3D® uses Selective Laser Sintering (SLS) technology to produce components with excellent mechanical and thermal properties. With this system, even highly complex components can be manufactured without any support structures.
The QLS 236 is the ideal system for all users who require high quality components at low prices. The Nexa3D® SLS system offers high speed and access to BASF's most powerful SLS materials as well as an open material platform. The industrial SLS system impresses with a powerful CO² laser and a large installation space.
Features:
Technology: SLS (selective laser sintering).
Usable build volume: 230 x 230 x 250 mm
Laser power: 60W CO2
Max. Printing speed: up to 22 mm/hour
A print speed of up to 22 mm per hour is possible with the QLS 236. This makes the printer ideal for the production of prototypes and small batches.
In addition to the higher printing speed, the QLS 236 also has a shorter cooling time compared to other SLS machines. This ensures higher throughput without compromising quality or the mechanical properties.
The QLS 236 is equipped with a 60-watt CO² laser. With this, compared to the Nexa3D® QLS 230 more powerful laser, twice the printing speed can be achieved.
The build space of 230 x 230 x 250 mm is also larger than that of the QLS 230, which means that larger projects are now possible without difficulty.
When using SLS technology, it is not necessary to print additional support structures to hold the component in position during the printing process, as the thermoplastic automatically also serves as a support material. As a result, the printing process conserves resources and the print result is not compromised. Furthermore, multiple models can be stacked and printed in any orientation, increasing productivity and reducing part costs.
The Nexa3D QLS 236 has 6 thermal panels and its build chamber can reach temperatures of up to 220 degrees Celsius.
The modular print chamber module of the Nexa3D QLS 236 enables effective use. You can remove the finished print job from the printer and let it cool down in the postpress station. The removable recycling container also makes it easier to reuse the powder.
Buildware and Nexa3Dprint AM SLS, previously XYZprint AM SLS. are the two software programs used by the QLS 236. Buildware gives the user the possibility to start the print job directly at the printer and to adjust the settings on site. The planning of projects and print processes as well as the monitoring of running print jobs is made possible by Nexa3Dprint AM SLS.
Cold Metal Fusion from Headmade Materials® is a patented process that combines the advantages of rapid sintering with established powder metallurgy processes for the production of titanium and steel parts. Using a polymer-coated metal powder, the QLS 236 produces "green" parts in a low-temperature processing environment. The parts then go through a secondary debinding and sintering process that burns out any residual polymer and sinters the metal particles together to form the final metal components.
Rapid prototyping and low-volume applications can now be used at higher temperatures thanks to the Nexa3D QLS 236 with polyamide 6 powder, which is particularly advantageous in the automotive and electronics industries.
To always find the ideal material for your component, the Nexa3D® QLS 236 can use a wide range of materials. In addition, custom material profiles can be created for special applications and for new materials.
Series components that can even replace injection molded parts.
Produce complex objects quickly and cost-effectively.
HP Multi Jet Fusion technology limits the recyclability of powder material. Once the limit is reached, the powder is end-of-life and can no longer be used. This means HP MJF customers must dispose of large quantities of powder. Now, this end-of-life powder can be recycled and printed on Nexa3D® SLS printers. In addition, this powder can be easily mixed with as little as 5% fresh PA12 powder for brighter parts.
Test form, fit, and function with an accurate representation of the final product.
Fill up the form below and we will send you the data sheet by e-mail.
Cookie settings
We use cookies to provide you with the best possible experience. They also allow us to analyze user behavior in order to constantly improve the website for you. Privacy Policy