3D printers
High quality 3D printers
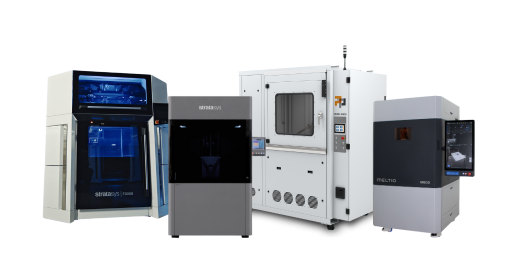
25% discount on your first order of 3D printed components!
SAVE SUMMER DISCOUNT NOW!The perfect symbiosis of quality and quantity!
Complex geometries with ideal properties!
High-resolution components with a wide variety of materials!
High-performance components with sustainable production!
A wide range of materials and ultra-fast production!
Ideal for a wide range of dental indications!
The process from simple component to product!
Fully automate your production!
Fast processing and successful management!
Sorry, there are no results for this combination of filters. Choose another combination of filters.
To ensure that all requests are handled promptly and completely, we ask that you submit all support requests through our support portal.
To the service portalDo you need assistance with your project, do you need advice or a sample part that we can send you?
Send EmailThe PostProcess® DEMI 800™ Series automatic submersion systems are designed to meet the demands of high-volume production.
The Postprocess® DEMI 800™ removes additional resin or PolyJet and FDM carriers using PostProcess® Technologies' patented Submersed Vortex Cavitation (SVC) technology. Using a moving flow and "sink-float" technique, PostProcess® SVC technology efficiently removes PolyJet and FDM carriers. Fast and consistent removal is achieved through alternating motion combined with best-in-class energy delivery and detergent filtration. The PostProcess®DEMI 800™ purge algorithms regulate the movement of fluids in the machine and adjust sensor data in real-time to prevent part damage and ensure consistent carrier and resin removal.
Specifications:
Basin size: 460 x 460 x 460 mm
Consumable capacity: 151 liters
Variable temperature: 30-63°C
PostProcess® SVC solutions use a sophisticated pumping system to rotate the part while it is immersed in the cleaning agent.
The vortex component of SVC technology ensures that the part is uniformly exposed to the cleaning agent and cavitation of the ultrasound, regardless of density or geometry and its effect on the buoyancy of the part.
PostProcess® uses cavitation generated by ultrasound as an additional source of mechanical energy to improve chemistry. The ultrasound creates compression and expansion waves in the cleaning fluid by emitting sound waves with varying frequencies and amplitudes. At the surface of the part, the movement of the liquid causes cavitation and the formation of small bubbles. As the substrate is weakened by the chemical, these bubbles agitate it, accelerating the reaction.
PostProcess®'s unique chemistry is a key factor in the effectiveness of SVC technology.
The three main cleaning agents in the SVC line were all developed by PhD chemists specifically for cleaning additive materials.
In this context, each printing process has its own special cleaning agents, which have been optimized for the materials used.
PostProcess® cleaning solutions dissolve the substrate or uncured resin for each of these technologies without damaging the build material.
In a conventional system, the carrier material disintegrates and falls to the bottom of the machine. The efficiency of the shaft generated by the transducer would then be compromised by this deposited material. By placing them on the side of the machine, PostProcess® SVC machines have reduced this problem and ensured optimal efficiency throughout the cycle.
The PostProcess®DEMI 800™ has an unloading basket to remove the cleaned components from the system for further production steps.
The purging algorithm, which carefully controls the energy, speed and direction of the system, ensures that cleaning time is minimized.
The AUTOMAT3D® software varies the flushing intensity, temperature and process time to achieve ideal cleaning in the shortest possible time.
Fill up the form below and we will send you the data sheet by e-mail.
Cookie settings
We use cookies to provide you with the best possible experience. They also allow us to analyze user behavior in order to constantly improve the website for you. Privacy Policy