3D printers
High quality 3D printers
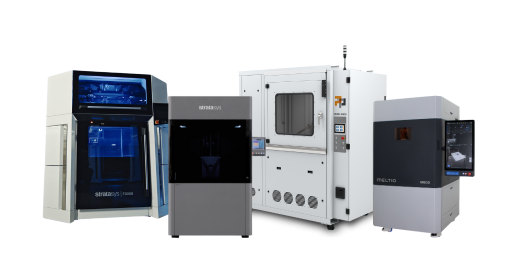
25% discount on your first order of 3D printed components!
SAVE SUMMER DISCOUNT NOW!The perfect symbiosis of quality and quantity!
Complex geometries with ideal properties!
High-resolution components with a wide variety of materials!
High-performance components with sustainable production!
A wide range of materials and ultra-fast production!
Ideal for a wide range of dental indications!
The process from simple component to product!
Fully automate your production!
Fast processing and successful management!
Sorry, there are no results for this combination of filters. Choose another combination of filters.
To ensure that all requests are handled promptly and completely, we ask that you submit all support requests through our support portal.
To the service portalDo you need assistance with your project, do you need advice or a sample part that we can send you?
Send EmailCookie settings
We use cookies to provide you with the best possible experience. They also allow us to analyze user behavior in order to constantly improve the website for you. Privacy Policy