3D printers
High quality 3D printers
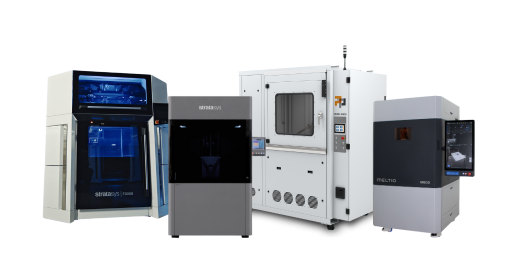
Even if many people only come into contact with it when flying on vacation, aviation is a far more extensive and essential cornerstone of all our lives. This industry provides over 87 million jobs, is expected to set in motion over 40 million flights and nearly 5 billion passengers in 2024, and has an annual turnover of over 950 billion US dollars – by way of comparison, Switzerland's projected GDP for 2024 is 938 billion.
Whether traveling for work or pleasure, transporting consumer and capital goods, providing emergency care in crisis areas or acting as a driver of innovation – aviation enables the fast and efficient connection of people and markets worldwide.
But even such a substantial role does not protect against ever stricter regulations and consumer demands in terms of environmental friendliness, ever more expensive components and parts, and weakening supply chains, which only serve to drive up already strained prices.
However, such challenges are nothing new for the aviation industry. Time and again, this industry has produced new innovations to develop itself further, open up new fields of application and shed old ballast – and for the current difficulties, additive manufacturing has proven to be the method of choice for innovation.
In this blog post, I would like to present applications in which 3D printing is used in aviation and also explain the advantages of this technology, which has allowed it to position itself as a guarantor of innovation.
First, I will identify some of the key application areas for 3D printing and provide specific examples – starting with the original purpose of 3D printing – prototyping – and moving on to tools and end-use parts.
As in almost all industries, prototyping was the first area of application in which 3D printing found its way into aviation. However, in contrast to many other industries, the aviation industry tried to make the prototyping process faster and more cost-efficient with the help of additive manufacturing very early on, from 1989 to be precise.
However, these attempts were initially rather slow. Material limitations and a lack of skills meant that for several decades 3D printing was used exclusively for early prototyping or design validation of small components, with the result that the hoped-for effect of increased speed and reduced costs was only felt to a very limited extent.
The breakthrough for rapid prototyping came in 2012, when the US company GE Aviation used 3D printing to create a prototype fuel nozzle for its LEAP engine. This functional prototype combined twenty components that had previously been individually produced in a laborious process, thereby reducing weight by 25%. This demonstrated to the entire industry that additive manufacturing had now reached a level where complex, lightweight components could be produced quickly.
In the years that followed, rapid prototyping became indispensable. All major aircraft manufacturers – from Airbus to Boeing, Dassault and Textron Aviation – quickly began to ramp up their 3D printing capacity to avoid falling behind.
To this day, additive manufacturing has become the most important prototyping tool in the aerospace industry. Now, large, small, complex and simple components are produced using 3D printing so that they can be subjected to intensive testing and, if necessary, quickly modified.
The breakthrough of the LEAP fuel nozzle in 2012 not only led to the massive expansion of additive manufacturing in prototyping in the long term, but it also made it possible to use it for end-use parts. It took only three years before the first 3D-printed component was used in a commercial aircraft.
In 2015, GE Aviation once again achieved a breakthrough for additive manufacturing in aviation. A housing for a temperature sensor at the compressor inlet for the GE90 engine of the Boeing 777 was produced by 3D printing and certified by the FAA (Federal Aviation Administration) for aviation and was allowed to make its maiden flight that same year.
Just one year later, the fuel nozzle for the GE LEAP engine, which was produced as a prototype in 2012, was approved. These engines, equipped with 19 of these 3D-printed fuel nozzles, are now used in various aircraft – including the Airbus A320neo family, the Boeing 737 MAX and the COMAC C919.
The success of the fuel nozzles on the LEAP engine ensured that other GE engines were also supplied with 3D-printed fuel nozzles – including, in particular, the GE9X engine, which was specially designed for greater fuel efficiency.
GE Aviation has since added a large number of other 3D-printed components to this very engine. More than 300 different components, including low-pressure turbine blades, temperature sensors and others, have been manufactured using additive manufacturing in this engine, undoubtedly demonstrating that the possibilities of additive manufacturing now extend far beyond fuel nozzles – and also further than engines.
In addition to engine components, 3D printing is now also used for a variety of interior components – from small parts such as covers and door locks to large parts such as wall panels and seats – in particular to save weight.
One of the first 3D-printed components in the interior of an aircraft was integrated by Airbus into its A320 family. A partition wall, located between the passenger seats and the galley, may not initially appear particularly eye-catching to outsiders, but it is of the utmost importance for the crew, as it supports the jump seats used by the crew during take-off and landing.
Due to this supporting function, this partition wall must be highly stable, which, with conventional manufacturing methods, has led to a high weight of approx. 66 kilograms. Thanks to 3D printing, however, this weight could be reduced by 45% without any loss of stability. According to Airbus projections, this weight reduction alone could save up to 465,000 tons of CO² each year.
Another specific example is the Airbus A350 XWB, in which over 1,000 different parts and components have been 3D printed. These components, produced using Stratasys® FDM® printing solutions and ULTEM™ material, include a variety of internal brackets, seals, housings and much more.
Additive manufacturing is also used throughout the Airbus A350 XWB for another essential application in aviation where speed is of the essence – namely, spare parts.
More than almost any other industry, aviation is familiar with the problems that can arise from even the smallest damage. A single defective component is enough to prevent an entire aircraft from taking off, costing the airline massive amounts in losses.
Airlines suffer losses of roughly $150,000 per hour in the event of an aircraft being grounded, often referred to as Aircraft on Ground (AOG), due to technical defects, for example. Therefore, it is important for airlines not only to anticipate potential damage, but also to be able to repair it quickly in an emergency.
A large number of airlines are turning to 3D printing as the ideal solution for the rapid on-demand production of spare parts of all kinds – from small screen brackets as with Air New Zealand to large winglets as with Airbus – instead of overcrowded warehouses, which also come at a high cost.
Spare parts from 3D printers can also extend the service life of older aircraft. For many of these older aircraft, spare parts have not been produced for years, which is why the costs for them have skyrocketed. Thanks to digital models and additive manufacturing, however, such spare parts can be produced in-house at a lower cost.
Whether spare or original parts, both have to find their way into or onto the aircraft, which usually requires highly specialized and powerful tools, which is another perfect application for 3D printing in aviation.
Unfortunately, in addition to their performance, tools for the production of aircraft are often also known for long lead times and high costs. The molds for these tools are usually highly complex, the choice of materials is very limited and the manufacturers of such tools are very rare, which unfortunately makes delays in aircraft production a routine occurrence.
To minimize these delays, a large number of manufacturers are relying on the on-demand capabilities of additive manufacturing. In particular, composite materials, such as carbon fiber-reinforced filaments, are used because only such materials can meet the high requirements for resilience and strength.
A practical example is provided by Dassault Aviation, a French manufacturer of commercial jets and military aircraft. Dassault has traditionally used molds made of fiber-reinforced plastic, manufactured using traditional manufacturing methods, to produce aircraft structures made of composite materials. However, the production of these tools could take months and was associated with enormous costs.
Together with Stratasys® and their ULTEM™ 1010 filament, Dassault was not only able to produce their tools faster and more cost-effectively, but also to make them much lighter in weight to simplify handling and, thanks to the high heat and load resistance of the material, guarantee a long service life.
Lufthansa Technik also supports aircraft manufacturers in the production of tools with its in-house Additive Manufacturing Center. With over 30 different printing systems, small, large, polymer- and metal-based tools are produced here to accelerate the lead times for these and thus provide aircraft manufacturers with a massively reduced time-to-flight.
After all these applications, we now come to the reasons why additive manufacturing has evolved over the years from a pure prototyping tool to an all-purpose solution.
In the early phases of prototyping in particular, a very high number of different iterations are carried out in the aviation industry in order to achieve an ideal symbiosis of resilience, weight optimization and durability while keeping costs and material consumption as low as possible.
The combination of fast printing speed, minimal material waste and easy customization of the digital model provides the perfect conditions for producing components in a cost-effective and time-saving manner. This enables aircraft manufacturers to achieve faster iteration cycles and more intensive testing of individual components, which also greatly improves the final safety of the components.
But even outside the prototype stage, this rapid design adaptation can be essential. The aviation industry is one of the most strictly regulated industries, and these regulations are constantly changing. Thanks to 3D printing, aviation manufacturers can respond much more quickly to such changes in order to minimize the aforementioned AOG damage.
When it comes to the complexity of the components, additive manufacturing is unbeatable. The free adaptation of digital models and the layer-by-layer structure enable users to produce even the most complex internal structures with ease.
This increased design freedom offers two advantages for the aviation industry. On the one hand, several previously individual components can be integrated into a single component, as in the LEAP fuel nozzles from GE Aviation mentioned above, which means a massive reduction in time for aviation manufacturers.
On the other hand, this increased complexity is a unique support for the ubiquitous goal of more climate-friendly aviation. As the previous example of the Airbus bulkhead impressively demonstrates, even individual components can have a massive impact on CO2 emissions, and the more such components can be produced with additive manufacturing, the closer we can get to the goal of environmentally friendly flying.
In addition to constant regulatory changes, the aviation industry also struggles with sometimes large production fluctuations. Weakened supply chains, a destructive shortage of skilled workers and a multitude of unforeseen events in recent years have led to a situation in which the number of aircraft delivered is well below the number of orders. For example, only 38% of the Boeing 777s ordered could be delivered between 202
The ability to quickly manufacture a wide range of aircraft components on-demand and in-house using 3D printing has therefore become increasingly important in aviation production, particularly in order to quickly alleviate emergencies, especially since the Covid pandemic.
In the future, 3D printing directly on the aircraft could also become a solution for emergencies. Last year, the first 3D printer in the air was tested by the Center for Additive Manufacturing Research and Innovation (CAMRE) for the US Marine Corp and completed this maiden flight with great
Last but not least, this blog post should also mention the advantages of 3D printing for the future. The advantages of additive manufacturing already mentioned combine perfectly to create an ideal basis for research work in the field of aviation.
An excellent example of this is the AMPHEA project at the Technical University of Munich, which was funded by the German Federal Ministry for Economic Affairs and Energy (funding reference 20Q1955A). This project is actively involved in the development of the first additively manufactured heat exchanger for aircraft, with the aim of enabling decentralized production of these essential components in the future.
The US Army is also actively using 3D printing for research, for example in the Improved Turbine Engine Program. In this program, which sought a replacement for the GE 700 engine, additive manufacturing was integrated from the outset and led to the GE T901 engine, which boasts improved fuel efficiency, performance and durability.
Die Additive Fertigung hat sich in den letzten Jahren, nach langen Schwierigkeiten, dank der großen Entwicklung rund um Drucklösungen, Technologien und Materialien in der Luftfahrt durchsetzen können und bietet nun einer Vielzahl von Herstellern und Luftfahrtgesellschaften mehr Möglichkeiten und schnellere Reaktionszeiten.
Das Ende dieser Entwicklung ist dabei noch lange nicht in Sicht. Mit immer neueren Optionen wird der 3D-Druck seine bereits jetzt eindrucksvolle Applikationsvielfalt immer mehr erweitern können und somit in Zukunft einen noch größeren Beitrag zu Umweltschutz, geringeren Vorlaufzeiten und kostengünstigerer Produktion haben.
Wenn Sie immer auf dem neuesten Stand über die Additive Fertigung in der Luftfahrt bleiben wollen, schauen Sie gerne öfter hier auf diesem Blog vorbei oder abonnieren Sie unseren Newsletter, um neueste Entwicklungen schnellstmöglich zu erhalten.
Vielen Dank für Ihre Aufmerksamkeit – und bis zum nächsten Blogpost!