3D printers
High quality 3D printers
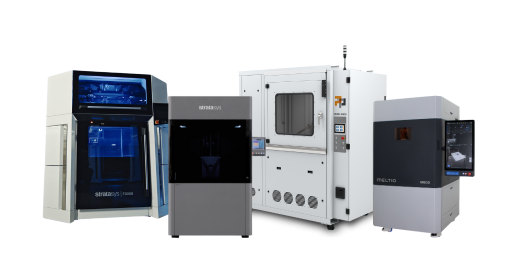
After taking a look at the different types of materials used in the most common 3D printing process, printing with filaments, a few weeks ago, today we are going to take a look at the oldest 3D printing process – 3D printing with resin.
In resin 3D printing, liquid epoxy acrylate resin is used in the vast majority of cases, more rarely silicone or polyamides, which is cured layer by layer by UV light from a laser, screen or lamp. This technology impresses, among other things, with its excellent level of detail, very high printing speeds and the option of printing highly transparent components.
The range of materials available for resin 3D printing is not quite as overwhelming as for 3D printing with filaments, but nonetheless, there are a variety of different properties that the materials can be provided with, which I would like to take a closer look at in this blog post.
The classification of the various resins will not be based on the material itself, i.e. the chemical composition, as it is with filaments, but on the properties. I will divide them into mechanical properties and advanced properties, which include features such as flame retardancy, transparency and others. If you are already familiar with mechanical properties, you can jump directly to advanced properties using the button below.
Mechanical properties refer to the reactions of a material to physical forces and stresses. These include, for example, properties such as tensile strength, hardness, rigidity, toughness, flexural strength and many more. We will start with the so-called “standard resins”, often also called “prototyping resins”.
The category of standard resins is the largest type, with an uncountable number of different manufacturers. This wide selection comes from the fact that this type of resin is undoubtedly the most widely used, since standard resins are used almost exclusively in the hobby sector and are also popular in industry for certain applications.
This broad usability is mainly due to the fact that standard resins have average properties in almost all areas. Moderate hardness, moderate strength, moderate ductility – virtually all the properties of such standard resins are accurately described by the word “moderate”, which makes them perfect all-rounders.
In addition, with a price between 40 and 100 euros per liter, such resins are clearly the cheapest and, in contrast to specialized resins, these materials are very easy and quick to process thanks to good layer adhesion and low shrinkage. Furthermore, the color selection is highest for standard resins and the surface quality is usually very high due to the simple processing.
The biggest advantage of these resins is also their biggest disadvantage. Standard resins can be outperformed by specialized resins in every way. Furthermore, despite their moderate mechanical properties, they are not suitable for use in more demanding applications, especially when heat is added, since standard resins only remain functional and structurally stable at temperatures below 50 to 60 °C.
The largest area of application for such standard resins has already been anticipated with the alternative designation as “prototyping resin”. Thanks to their low price and all-round properties, they are perfectly suited for rapid prototyping of small, medium and large-sized parts and components – across all industries.
Further areas of application include, in particular, the hobby sector, with the production of decorative elements, figures and other merchandise, small holders and devices, and much more that makes the hobbyist's heart beat faster.
Resins with the description “tough” are also widely used and particularly popular in industries where components have to withstand high or repeated mechanical stress.
Tough resins, as their name suggests, are particularly impressive in terms of their excellent toughness. They are exceptionally resistant to cracks or breaks thanks to their very high impact and tensile strength, and offer a good balance between strength and ductility.
The surface quality of tough resins is still very good, although usually a bit rougher than standard resins, and thanks to their low shrinkage, they are only slightly more demanding to work with than standard resins.
However, Tough Resin requires a longer exposure time, which is why the printing speed decreases somewhat. The post-processing time is also increased by a longer post-curing process. Last but not least, Tough Resin has a rather moderate rigidity, which is why applications with high structural rigidity are not among the preferred application areas for this type of resin.
Tool production, on the other hand, is one of these preferred application areas. Tough resins can be used to produce durable, long-lasting tools, fixtures, jigs and other manufacturing aids for a variety of industries on demand.
Tough resins are also popular for functional prototypes that can be used to test mechanical loads. Other areas in which this type of resin is frequently used include robust housings, mechanical components and snap-fit connections.
Rigid resins are resins that impress with their particularly high rigidity. To achieve this, glass or ceramic particles are often added to the resin, which further increase the strength and rigidity. However, many network-forming linking sites can also be incorporated into the monomers, which create a three-dimensional network in the cured state, a huge macromolecule, so to speak, and thus maximize rigidity.
The main advantage of this extraordinary rigidity and strength is that it results in components that are highly dimensionally stable and can withstand strong external forces such as pressure, shear, torque and more without deforming.
In addition, rigid resins offer excellent surface quality, which perfectly accentuates even the smallest details. Shrinkage is very low, which ensures increased dimensional accuracy and easier processing, and at 80 to 160 euros per liter, the price is mid-range.
However, due to their outstanding form stability, rigid resins are also relatively brittle and tend to break or crack when subjected to very strong impacts. Furthermore, certain post-processing steps, such as grinding, are associated with a relatively high level of effort due to the high hardness, and the processing printer requires a calibration designed for rigid resins to ensure maximum rigidity.
The combination of excellent surface quality and dimensional stability makes rigid resins very popular for rigid housings of all kinds. The high level of detail means that small details such as logos or lettering can also be applied directly during the printing process, further streamlining production.
Furthermore, rigid resins are often used to manufacture precision tools and other production aids that require a high degree of rigidity, functional prototypes, as well as consumer goods such as kitchen utensils or decorative elements.
This type of resin is a cross between Tough and Rigid resins and is often mixed with fillers such as glass or carbon fibers to achieve optimal hardness and strength.
Strong resins are particularly impressive due to their very high mechanical strength. These resins are designed for very high and perpetual loads and at the same time have a certain degree of flexibility to prevent breakage.
In addition, strong resins are less susceptible to brittleness, shrink very little or not at all during the printing process to allow for maximum precision, and have a smooth, albeit slightly rougher surface than standard resins, for example.
The price of strong resins is the first to stand out, at 90 to 180 euros per liter, which is above the average. In addition, post-processing, thanks to intensive post-curing for maximum strength, involves slightly longer production times and the necessary exposure times are also above average.
Due to their extraordinary mechanical strength, Strong resins are in particular demand for machine components such as gears, pulleys, clamps, bearing housings, brackets or couplings, where their properties are ideal.
In addition, these resins are also popular for tools and production devices, functional prototypes, but also end-use parts, including structural components in the automotive industry.
Flexible resins are resins that have been treated with plasticizers, for example phthalates, to ensure excellent flexibility and elasticity without the risk of cracking.
Of course, such resins score particularly highly in terms of their moldability, whether simple, cyclic or perpetual, whereby they consistently retain the respective shape they have taken on until they are pushed back into their original shape by manual or mechanical pressure.
Flexible resins offer a very smooth surface with a soft texture, are priced similarly to rigid resins in the mid-range at 80 to 150 euros, have a high elongation at break of up to 20% and offer very high dimensional accuracy and precision in the printing process.
However, the flexibility of the materials makes careful calibration of the respective printing system essential, and the inherent flexibility can also complicate post-curing and further post-processing steps.
Flexible resins have a wide range of applications thanks to their very high flexibility combined with reasonable dimensional stability. In particular, these resins are perfectly suited for applications with light to moderate mechanical loads, such as seals in vehicles or snap-fit connections.
But flexible resins are also an excellent choice for applications such as flexible packaging, covers for electronic devices, clips for plastic housings and various wearables such as wristbands or protective equipment.
When maximum elasticity is required and components must simultaneously return to their original shape independently, there is no way around elastic resins, which are also mixed with various plasticizers.
This elasticity is rounded off with a very soft, rubber-like surface texture, which means that components made with elastic resins not only shine with unique elasticity and resilience, but also with excellent optics and haptics, and an extraordinary elongation at break of up to 300%.
Furthermore, elastic resins have excellent resilience and durability and are usually very abrasion-resistant, which means that the mechanical properties of these materials are retained over a long period of time.
In addition to the obvious weaknesses, such as a lack of strength, particular attention must be paid to the ideal duration when post-curing elastic resins, as overcuring would reduce their elastic properties. Furthermore, at a price of 100 to 200 euros per liter, they are relatively expensive.
The main application for elastic resins is clearly in shock-absorbing components. They are used in particular in the automotive industry, but also in the aerospace industry, for components such as shock absorbers, seals and covers.
In addition, elastic resins are frequently used in the packaging industry, for example for protective packaging of sensitive devices, in the consumer goods industry, including smartphone cases and wearables, and also in medical technology, including customized insoles.
After discussing the most important mechanical properties of the various resin types, we now come to the advanced properties. These can be combined with most of the aforementioned mechanical categories and also with each other, allowing for precise customization to your specific requirements.
The biocompatibility requirements for a material are defined by its use as a medical device. The MDR (Medical Device Regulation) divides medical devices into risk classes I, IIa, IIb and III, with increasing risk for patients, users and third parties when used. In other regions, an analogous classification is used in principle, but with different limits and designations (e.g. FDA, CFDA, JPAL).
Resins are currently only available in classes I and II, which means that they are approved for long-term contact with skin, short penetration through the mouth or nose, and for implants that do not come into contact with the nervous or circulatory systems.
This biocompatibility classification ensures that contact with human tissue does not cause allergic or repulsive reactions, inflammation, poisoning or similar horrendous side effects.
In addition, biocompatible resins impress in the vast majority of cases with very smooth and shiny surfaces to ensure comfort, hygiene and a good appearance. They are also designed for maximum precision to ensure an exact fit for the respective patient.
Due to the necessary certifications of a biocompatible resin, these are unfortunately also relatively expensive, with costs between 150 and 300 euros per liter, depending on the application. Furthermore, it is not enough to simply use a biocompatible material – the printer, printing environment and post-processing must also complete this biocompatibility.
The largest area of application for biocompatible resins is the dental industry. These resins can be used to manufacture a wide range of different indications and applications, from dentures and dental crowns to demonstration models and preoperative models, as well as impression trays, all types of splints and gingival masks.
Biocompatible resins are also ideal for use in medical technology and laboratory equipment. These resins can be used to quickly produce patient-specific surgical templates, implants, prostheses, orthopedic aids and much more.
To test the heat resistance or the heat deflection temperature of resins and other plastics, the DIN EN ISO 75 certification is usually used. In this test, a test specimen made of the respective resin and under bending load is placed in an oil bath whose temperature is increased evenly by 120 K/h (Kelvin per hour). The temperature at which the test specimen reaches the specified 0.2% deflection is determined.
There is no general temperature limit for the term “heat-resistant” – however, resins with this addition can withstand temperatures between 200 and 300 °C, with the polyamide and silicone resins mentioned in the introduction being used at the upper end of this scale.
In addition to their temperature resistance, heat-resistant resins also have excellent mechanical strength, so that not only heat but also mechanical stresses do not pose a problem for such resins. The processing precision of such resins is also usually very high.
However, heat-resistant resins are incompatible with a high degree of flexibility. Although there is a choice between medium, high and very high hardness, this type of resin is not suitable for high flexibility requirements. Furthermore, at 150 to 300 euros per liter, the price is comparatively high and post-processing can be lengthy and labor-intensive, especially with very hard variants.
Thanks to its outstanding heat resistance and mechanical strength, this type of resin is very commonly used in the automotive industry and in motor sports. It can be used for brake system components, cylinder heads, exhaust manifolds and structural components to ensure not only heat resistance but also light weight.
Other applications include aircraft engine components, high-performance tools, molds, brackets and other manufacturing aids, as well as heat-resistant coatings for electronic components, for example.
ESD, short for electrostatic discharge, is a sudden and short-term current flow between two objects with different electrical potential. Such discharges can have serious consequences for component functionality or even human life, which is why protection against them is essential in critical industries.
ESD-safe resins, in which conductive or antistatic additives such as carbon or graphite are added, guarantee this safety. These either prevent the current flow between two components from building up at all or specifically conduct the current flow away, ensuring full functionality of important components even in critical situations.
This type of resin usually also has very smooth and even surfaces in order to be able to conduct electricity consistently and safely in an emergency, and impresses with outstanding dimensional accuracy and repeatability, making it ideal for series production.
However, due to the maximized ESD protection, this type of resin has to compromise on mechanical and thermal properties. They are never suitable for high-temperature applications and have a certain brittleness, which can lead to fractures under long-term mechanical stress. At 100 to 250 euros per liter, the price is lower compared to other resins in this category, but still quite a bit more expensive compared to standard resins.
The main area of application for these resins is, of course, the electronics industry. The ESD-safe properties are in particular demand for housings for electrical devices, printed circuit board casings, tools for the production of semiconductor wafers and chips, and packaging.
But industries such as automotive, aerospace, medical technology, and consumer goods production also use ESD-safe resins for housings, covers, and casings to prevent ESD.
To prevent the potentially devastating consequences of fires, flame-retardant resins that contain special flame-retardant additives such as halogen or phosphorus compounds are perfect. There is a considerable selection of resins that have achieved the highest classification of the UL 94 standard, Class V-0, and can effectively combat the spread of flames.
These resins not only minimize the spread of flames, but also maximize ignition resistance, limit heat emission to prevent surrounding components from melting, and, in the case of the V-0 classification, even self-extinguish within 10 seconds of the fire source being removed, with an afterglow time of no more than 30 seconds.
Furthermore, these materials offer reduced smoke and toxic gas emissions in the event of a fire, very smooth and detailed surfaces and good mechanical properties including high strength and rigidity.
As with heat-resistant resins, flame-retardant resins are not available in flexible form. Furthermore, it is important not to make the mistake of equating flame retardancy with heat resistance – flame retardancy does not necessarily mean that the component will not deform under high temperatures. And as with most other resins in this category, the price is in the higher range, at 150 to 300 euros per liter.
Flame-retardant components are of the utmost importance in many industries, but especially in the aerospace industry, where an unforeseen fire endangers not only components but also human lives. Flame-retardant resins are used in this industry to manufacture interior fittings, structural parts and engine components, among other things.
Flame retardancy regulations also play a major role in the automotive industry, and FR resins fulfill these requirements for a variety of applications such as interior trim, instrument panels, seals and covers. In addition, this type of resin also plays an important role in marine applications and specialty consumer goods, such as appliances.
In contrast to filaments, which have a maximum translucency, certain resins allow the production of highly transparent components with a light transmission of up to 95%.
These resins not only impress with their transparency but also with their exceptional surface quality. Smooth, glossy and with outstanding print resolution for components that are not only functional but also look great.
In most cases, transparent resins are also highly scratch-resistant and have a low yellowing index, even when exposed to UV light for long periods of time, ensuring that light transmission is maintained over the long term.
The price differences for transparent resins are sometimes the greatest of all resin types. Prices range from 40 to 250 euros per liter. This is partly because transparent resins are also very popular in the hobby sector – industrial and long-lasting transparent resins are priced upwards of 150 euros per liter. Transparent resins also require very precise calibration of the printer to ensure that there are no ambiguities or distortions.
For many applications, a high level of translucency is essential. One application in which transparent resins really stand out is in airflow and liquid flow models, for example for the automotive or chemical industry. The combination of the material's translucency and the ability to easily create internal channels means that there is undoubtedly no better solution for such models than transparent resins.
Furthermore, transparent resins are often used for lenses, prisms and other optical components, displays, covers, packaging, decorative elements, merchandise and, in combination with biocompatibility, for indications in the dental and medical industry.
Last but not least, we will take a look at one of the most versatile resin categories. Chemical-resistant resins become resistant to specific chemicals, alkalis and bases through the addition of special fillers or hardeners, whereby the exact resistance can be determined very precisely. This is also where the versatility in this category comes from.
This versatility is also the greatest advantage of this category. There are very specific resins for different applications – from resistance only to alkalis or bases, to resistance to solvents, to highly resistant resins that are fully resistant to almost all inorganic and organic chemicals, which means that the right material can be found for almost any application.
Chemical-resistant resins are also extraordinarily durable and retain their structural integrity even after long-term exposure to aggressive chemicals. They are also usually very corrosion-resistant and often have excellent weather and temperature resistance.
However, where chemical-resistant resins have to admit defeat compared to other resins is in terms of surface quality, which is a good deal rougher than with other resins due to the addition of fillers. Prices, on the other hand, are comparable to other resins in this category and range from 100 to 300 euros per liter, depending on the specific resistances.
The chemical and process industry is, of course, the largest customer for this type of resin. Within this industry, these resins are used, for example, in containers, tanks, pipes, ducts, reactor linings, pumps, valves and much more.
But chemical resistance is also needed in other industries and areas of application, and resins offer the ideal way to create complex structures with ease. The automotive, aerospace, environmental technology, food and beverage industries, among others, benefit from this.
Even though the general selection of resins is somewhat smaller than that of filaments, this blog post should have made it clear that there is nonetheless a resin with suitable properties for almost every application.
I hope this blog post has given you an overview of the different characteristics resins can cover and how they differ from each other.
In one of the next blog posts, we will take a look at the different types of polymer powders used in 3D printing to help you understand the wide range of materials available.
Thank you for reading – and see you in the next blog post!