3D printers
High quality 3D printers
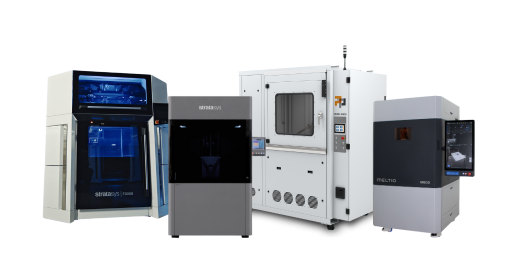
In addition to its ease of use, fast printing speed, large-scale customizable printing parameters and low entry-level prices, 3D printing with filaments offers a very decisive advantage - the largest selection of materials of all 3D printing processes.
From standard materials such as ABS and PLA to high-performance materials such as PEEK and ULTEM™ to composite materials - filament 3D printing can be used to achieve an almost unlimited variety of component properties and cover a wide range of applications.
However, this diversity can sometimes make it difficult for users to keep track of all the different options - especially as new ones are constantly being added. This blog post is designed to simplify this overview and provide a brief and concise introduction to the materials, including some applications for which each filament is ideally suited.
Due to the abundance of material options and especially material combinations, I will limit myself to the most commonly used filaments and divide them into three categories - standard thermoplastics, engineering thermoplastics and high-performance thermoplastics. You can jump directly to the respective categories using the buttons below.
Standard thermoplastics are generally cost-effective, easy to process and ideal for applications such as packaging, prototypes and consumer goods.
Within this category we will discuss PLA, ABS, PET / PETG and PP - starting with the absolute classic in filament 3D printing!
PLA, or polylactide, was one of the first filaments to be used in 3D printing, along with ABS. Scott Crump, inventor of the FDM process and later co-founder of Stratasys®, used PLA for his research and development in the 1980s, and to this day, PLA filament is very popular with users.
There are many reasons for this popularity, but PLA filament scores particularly highly for its very easy processability. With comparatively low printing temperatures of 180 to 220 °C, a very low tendency to warp – a phenomenon in which parts of the printed object deform or detach from the printing plate due to material stresses during cooling – even with non-heated building plates, and a non-hazardous processing, PLA has become particularly popular for beginners and hobbyists as the material of choice.
Other advantages of PLA filament include its high environmental friendliness, thanks to its production from regenerative raw materials such as corn starch or sugar cane, good surface quality with little cracking, high strength, low cost at around 15 to 30 euros per kilogram, and easy post-processing in terms of sanding and painting.
However, PLA is clearly at a disadvantage compared to other filaments when it comes to temperature resistance. With an average heat resistance of 60 to 65 °C, it is clearly not suitable for heat-sensitive applications. In addition, PLA is relatively brittle and hygroscopic, i.e. it draws moisture from the surrounding environment and absorbs it, making drying before printing unavoidable after prolonged unprotected storage.
Despite its perfect suitability for beginners and hobbyists, PLA has also made a name for itself in industry. Especially when it comes to design prototypes, PLA filament is the filament of choice in a variety of industries thanks to its cost efficiency and high strength.
Other applications include decorations such as artwork, merchandise, and model making, housings and housing components for components, as well as packaging, where its biodegradability and non-toxicity make it perfect.
ABS, or acrylonitrile butadiene styrene copolymer to give it its full name, is a polymer composed of two or more different monomers. In the 3D printing industry, it has become particularly popular due to its exceptional versatility.
This versatility stems from the symbiosis of acrylonitrile (C₃H₃N), which gives the material a high chemical and thermal resistance of up to 100 °C, butadiene (C₄H₆), which provides high impact strength, and styrene (C₈H₈), which enables a glossy surface and at the same time increases flowability, thus simplifying processing.
Furthermore, ABS is characterized by good resilience, offers high strength with far less brittleness than PLA, has a low cost of about 20 to 40 euros per kilogram and can be reworked very well, including smoothing with acetone vapor, which gives ABS an excellent surface quality.
The main disadvantage of ABS is that it is difficult to process because it is prone to warping. This makes a heated build plate essential and a closed print enclosure highly recommended. Furthermore, toxic fumes are produced when processing ABS, which makes it difficult to use in very small businesses and educational institutions. This material is also susceptible to moisture, although not as much as PLA.
Due to its properties, ABS has become particularly popular in the consumer goods sector for a wide range of housing applications. Thanks to its good electrical insulation properties, the material is often used for housings of electrical appliances, computer accessories, household appliances and more.
But ABS filament has also become the preferred material in the automotive industry, e.g. for dashboards and interior trim, in the construction industry, e.g. for pipes and fittings, and in toolmaking – for both prototypes and end-use parts.
PET, or polyethylene terephthalate, is the absolute standard for plastic applications in the area of bottles, films and textile fibers. In 3D printing, the glycol-modified PETG is mostly used, since this modification inhibits crystallization and lowers the necessary melting temperature. In addition, the glycol increases the toughness and reduces the britt
PET / PETG filament can, among other things, thanks to its excellent combination of strength and flexibility, which is complemented by a high resistance to cracks and breaks even under heavy loads.
PET/PETG filament also has a very high resistance to chemicals and moisture, a high surface quality, low purchase costs of around 20 to 40 euros per kilogram, and a processing difficulty similar to PLA thanks to its low tendency to warp and no toxic fumes during processing.
However, just like PLA, PET / PETG cannot score points with heat resistance. It can no longer be used at temperatures above 75 to 80 °C. PET / PETG is also very susceptible to scratches due to a lack of abrasion resistance, and its incomplete UV resistance makes it suitable for outdoor use, for which its very high
PET or PETG filament is also very often used in packaging applications when processed in 3D printing. For example, in the case of beverage and oil bottles, salad bowls and yoghurt pots, as well as cosmetic packaging, the processing of PET / PETG using additive manufacturing has become established thanks to the high production speed and cost-effective production.
But PET / PETG is also an ideal choice for the production of protective covers, especially in humid or chemically contaminated environments, functional prototypes for a variety of industries and outdoor components that do not come into contact with excessive UV radiation.
Polypropylene (PP) is a semi-crystalline thermoplastic and the second most commonly used standard plastic after polyethylene (PE). This material is also becoming increasingly popular in 3D printing.
This popularity stems from its excellent heat resistance of up to 110 °C, as well as its outstanding robustness and durability. PP filament also offers an exceptional strength-to-weight ratio for standard thermoplastics, which means that the weight in various applications can be reduced without loss of mechanical strength.
Other positive properties of PP filament include a very smooth surface, good resistance to acids, bases and solvents, very high toughness, good flexibility and very low water absorption, including water-repellent properties.
Printing all these properties is difficult compared to other standard thermoplastics – even ABS. PP filament requires temperatures between 220 and 250 °C for processing, has a relatively strong tendency to warp and shrink, and can quickly cause blockages in the extruder if the temperatures are too low or the calibration is incorrect. Furthermore, it does not adhere well to many standard building boards, which means that special adhesion methods or print bed coatings are necessary to print PP. At €30–60 per kilogram, its price is also on the higher end of the standard thermoplastics range.
As with PET/PETG filaments, the packaging industry is the largest area of application for PP filaments. The widespread use of PP filaments can be seen above all in food containers and films, although further applications in this area are bound to emerge in the future.
PP also represents a transition to our next category to a certain extent, because PP can also be used for technical applications, e.g. in functional prototypes, seals, hoses and containers. The first applications for PP filament can also be found in automotive and mechanical engineering, although the future will certainly hold even more possibilities here.
Engineering thermoplastics are characterized, among other things, by improved mechanical, thermal and chemical properties and are intended for technical applications, for example in the automotive or chemical industry.
In this category, we will look at TPE / TPU, Nylon, PC and PBT – starting with the guarantor for maximum elasticity!
TPE, the abbreviation for thermoplastic elastomers, is not strictly speaking a designation for a specific filament, but rather an umbrella term for several different filaments – including TPA, TPC and TPU. TPU is mostly used in filament 3D printing, which is why the main focus of this blog post is on this particular filament.
However, all TPE filaments have one major thing in common – elasticity. The materials are known for delivering extraordinary elongation at break, with TPU undoubtedly excelling in this property, with an elongation at break between 300 and 600 %.
TPU also offers a wide range of different Shore A hardnesses, between 60 and 95, very high chemical resistance, excellent abrasion resistance and mechanical strength, and outstanding resistance to weathering.
The main disadvantage of TPU is that it prints at a lower speed than other, harder filaments. To ensure precision and maximum quality, TPU should be printed between 20 and 50% slower on average than PLA, for example. In addition, Bowden extruders are not suitable for TPU filaments, as these can quickly become clogged, and the costs are slightly higher than for most standard filaments, at 30 to 60 euros.
The largest application area for TPU filaments is in shock absorbers of all kinds. Whether in large formats, such as in motor vehicles, or in small formats, such as protective covers, seals and membranes, the high elasticity combined with excellent abrasion resistance makes TPU the ideal choice.
Other applications for TPU include housings for portable devices, sports equipment such as bicycle handles and shoe soles, protective equipment such as knee pads and gloves, and medical technology.
Nylon filaments, often also referred to as PA filaments, include several different types of nylon, such as nylon 6, nylon 6/66 or nylon 12, which come in different specifications. For the sake of simplicity, I will summarize all nylon filaments and show the general properties and applications of this type of filament.
Nylon stands out with its outstanding tensile strength combined with very high resistance to impacts and mechanical stresses. Nylon can easily deform under stress without cracking or even breaking – and it does so with a very long service life.
These main properties are complemented by a very high wear resistance, which makes nylon filaments ideal for moving mechanical parts, excellent chemical resistance and moderate heat resistance of 80 to 100°C.
Unfortunately, these properties are associated with a difficult printing process. Nylon is hygroscopic, which makes dry storage and dedicated drying before printing essential. It also requires printing temperatures of 220 to 240°C and is prone to warping and shrinkage. Furthermore, at a price of 40 to 70 euros per kilogram, it is also relatively expensive.
However, this increased effort is particularly worthwhile for machine components that require high wear resistance and outstanding strength. For example, nylon filaments can be used to produce high-quality gears, bushings, ball bearings, flanges and many other machine components that impress with their durability and resistance.
The properties of nylon filaments have also proven indispensable for technical functional prototypes and illustrative models in the chemical and automotive industries, as well as for sports and outdoor equipment.
Polycarbonate filament is a thermoplastic polymer made by polymerizing carbonic acid ester. It is one of the few filaments that has a high translucency and has thus become particularly popular for applications that require a higher degree of light transmission.
In addition to this translucency, PC filament is also known for its high heat resistance. PC can withstand long-term temperatures of up to 130°C and there are also some PC variants that have received UL-94 V-0 certification for flame retardancy.
PC also offers very high strength and impact resistance, is resistant to mechanical loads and shocks, has an aesthetically smooth surface quality, good weather resistance and very high rigidity.
However, this rigidity also means that PC filament is not particularly flexible. Although it provides some resistance to breakage, PC filament will not withstand large or permanent deformations. Furthermore, it is susceptible to solvents such as acetone. Its prices, which can reach up to 100 euros per kilogram, are among the highest of all engineering thermoplastics. Processing it is similarly difficult to processing nylon, and even higher temperatures of 260 to 300 °C are required.
PC filament has become particularly established in the production of manufacturing aids due to its high durability, longevity and heat resistance. It can be used for tools, brackets, devices, molds and much more.
In addition, PC is used above all in the already mentioned field of application of translucent components, for example, demonstration models for complex internal geometries, and PC filament is also very suitable for machine parts, housings and functional prototypes.
PBT is a semi-crystalline thermoplastic that has been used relatively infrequently in 3D printing to date, but is being used more and more frequently in the electronics industry in particular.
PBT filament owes this use to its very good electrical properties, including its excellent volume resistance of up to 10^16 Ohm·cm, its high dielectric strength of around 20 to 30 kV/mm and a tracking resistance with a CTI (Comparative Tracking Index) value of usually over 600 volts.
In addition, PBT is very heat resistant and can withstand short-term temperatures of up to 240°C and long-term temperatures of up to 140°C. There are also many flame-retardant versions of PBT filament. Furthermore, it has very low moisture absorption and fantastic mechanical strength and robustness.
As with the previous PC filament, the lack of flexibility in PBT can also lead to difficulties in certain applications. Due to its high toughness, PBT does achieve moderate break resistance, but it is still not suitable for applications with stronger deformations. Processing is in the “demanding” category with the other engineering thermoplastics, and at 40 to 70 euros per kilogram, the price is also on a par with other engineering thermoplastics.
As already mentioned, PBT filament is mainly used in the electronics industry. It can be used for connectors, switch housings, insulators, coil bodies, circuit board holders and many more.
PBT can also be found in the automotive industry when it comes to components that require high strength as well as temperature and chemical resistance. Tools, holders and prototypes are also possible with PBT.
High-performance thermoplastics have been developed for the most demanding of all application areas, for example the aerospace industry, and impress with extraordinary heat resistance and mechanical properties, among other things.
In this category, we will look at carbon fiber-reinforced filaments, PPS and PEEK – starting with the material of choice for reducing weight!
Carbon fiber-reinforced filaments always consist of a matrix material, such as PLA, ABS or nylon, which is combined with carbon fibers with a diameter of five to seven micrometers to combine the properties of the carbon fibers with those of the matrix material. The mass fraction of carbon fibers is usually between 15 and 20 percent.
The exact properties of a carbon fiber-reinforced material depend on the matrix material. However, in principle, the combination with carbon fibers offers the advantage of increased rigidity with simultaneous weight reduction. Due to these improved mechanical properties, wall thicknesses can be significantly reduced, which can lead to weight savings of up to 30% without compromising strength.
Other properties that are improved by carbon fiber reinforcement include heat resistance, abrasion resistance, stiffness, mechanical strength and even processing difficulty, since carbon fibers have little tendency to warp without significantly increasing the necessary processing temperature.
Why not every printer can easily process carbon fibers is mostly due to the nozzles. Due to the highly abrasive properties of carbon fibers, the use of conventional brass nozzles leads to rapid wear. Therefore, special high-strength nozzles made of hardened steel, tungsten or sapphire are required for these materials. In addition, the price of carbon fiber-reinforced filaments is up to 150% higher than that of the pure matrix material, and the surface is rougher due to the carbon fibers than with the pure matrix material.
The improved weight optimization of carbon fiber-reinforced filaments has been widely adopted in the automotive industry and motorsports, among others. Spoilers, panels, bumpers, structural components, dashboards, engine covers, and a variety of other vehicle components can be made lighter and thus more energy efficient than ever before with carbon fiber-reinforced filaments.
Other areas that benefit from this weight optimization include aerospace, military, and sports. High-performance tools can also be printed with carbon fiber-reinforced filaments, which are easier to handle thanks to their lower weight, while still providing the necessary performance.
PPS is one of the oldest high-performance plastics, having been discovered by Charles Friedel and James Mason Crafts as early as 1888. However, it took almost 80 years for PPS to be commercialized, and it was only towards the end of the 2010s that it was finally certified for 3D printing.
The biggest advantage of PPS is its extraordinary chemical resistance. Only a limited number of highly aggressive substances in concentrated form can attack and damage the material. These include extremely strong acids such as hydrofluoric acid, concentrated alkalis (e.g. caustic soda) and solvents such as benzene or dichloromethane.
When it comes to heat resistance, PPS filament is also in the Champions League. With long-term heat resistance up to 260 °C and inherent flame retardancy, this material is also suitable for high-temperature applications. In addition, the material impresses with high mechanical stability, low moisture absorption and, at least compared to other high-performance thermoplastics, relatively easy processing thanks to a very low tendency to warp.
However, PPS requires printing temperatures of at least 300 °C, which most printing systems cannot achieve. Special nozzles made of hardened steel or ruby are also needed, and at 150 to 250 euros per kilogram, the material costs are undoubtedly in the higher range.
Due to its exceptional chemical resistance, the chemical industry is naturally one of the main areas of application. Some specific applications include filter media, sealing rings, pump parts, membranes and piping.
Other applications for PPS filament include housings, machine parts, brackets and structural components in industries such as the automotive industry, the electronics industry and industrial series production.
PEEK has proven to be a miracle material for the most demanding of applications due to its unrivaled mechanical, thermal and chemical properties.
PEEK filament has outstanding resistance to almost all organic and inorganic chemicals, as well as to gamma and X-ray radiation and, up to approx. 280 °C, it is also completely resistant to hydrolysis.
Temperatures are a good keyword, because here, too, PEEK is unique. 250 °C is not a problem for PEEK filaments, even over the long term, and it can even work at 300 °C for short periods without losing its properties. It is also extremely abrasion-resistant, offers outstanding rigidity, toughness, tensile strength and flexural strength, and is biocompatible.
So why isn't PEEK used by all industries that don't require flexible components? The main reason is its very high price of 300 to 600 euros per kilogram. In addition, PEEK is sometimes the most difficult filament to process, with a high tendency to warp and necessary temperatures of up to 400°C.
Nevertheless, PEEK has taken on a pioneering role in 3D printing in certain industries – especially in aerospace. Here, components come into contact with the most extreme temperatures and a wide range of chemicals, and the failure of a small component could cost not only massive amounts of money but also human lives, which is why maximum health is the order of the day in aerospace – and this is what PEEK filament offers.
Another major area of application is in medicine, where PEEK's biocompatibility means that it can be used to manufacture implants such as skull bones or surgical tools. In addition, PEEK is also used in the chemical industry, electronics and aviation.
Filament types are ten a penny – which also explains the length of this blog post. There are many more potential filaments, but we didn't discuss them in this blog post due to time constraints.
Nevertheless, I hope that this overview of some of the most common filaments has shed some light on the right choice for certain applications and industries.
In one of the next blog posts, we will take a look at the different types of resins used in 3D printing to provide an ideal overview there as well.
Thank you for reading – and see you in the next blog post!