3D printers
High quality 3D printers
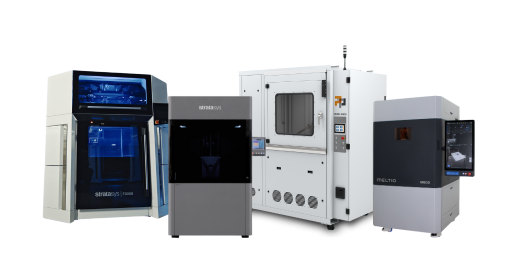
A 3D printer, whether for one-off or batch production, large or small production facilities, industrial operations or dental laboratories, offers the opportunity to increase production efficiency.
Additive Manufacturing is increasingly finding its way into production. More and more companies are recognizing the opportunities that 3D printing offers. Unfortunately, however, no technology comes without its pitfalls.
In this blogpost, I would like to address some of the smaller points that can make your own 3D printer even more effective. One sees within Additive Manufacturing, especially but not exclusively among newcomers, the same small mistakes or carelessness again and again, which prevents a full exploitation of the potential of their machine(s).
The purpose of this blogpost is to point out these small mistakes and hopefully minimize them in the future.
Many people like to experiment a little. Many people don't read instruction manuals and specifications. And many other people do read them, but skillfully ignore them.
I don't want to dampen some people's enthusiasm for experimenting here, I myself like to experiment around a bit. After all, rules are there to be broken! But some are not. Especially not when maximum effectiveness and success rate are the goal since experiments not infrequently provoke a misprint.
There are a lot of sub-points around the specified printing process and its compliance, but we will focus on the most important ones in this blog.
Every 3D printer and every material is connected with so-called "design rules". In simple terms, these design rules specify the properties of the print job that are necessary for error-free production.
This includes many things. Maximum and minimum tolerances, maximum and minimum dimensions, necessary support structures, maximum and minimum size of certain features such as holes, cavities, small details and much more is recorded in these design rules.
Is it possible in some circumstances to get a flawless print even though it violates one of these design rules? Yes, no question. However, the error rate is increased for print jobs that violate these design rules, and especially in volume production, even small increases in this rate are massively noticeable.
But what if the required properties of a project cannot meet these design rules? For smaller deviations and single projects, there is nothing to stop experimentation, as long as you are aware in advance that the success rate will not be at the same level. However, for larger deviations and serial productions, it is not advisable.
For this reason, especially in industrial companies where mass production is ubiquitous, it is only recommended that you learn about the design rules of the machines and materials available for selection.
The spatial conditions are essential, especially for powder and resin 3D printers, to ensure error-free printing, but should not be ignored for the other printing technologies either.
With powder 3D printing, it is imperative to ensure that the powder is not contaminated with dust or dirt of any kind.
While filaments and metals can be cleaned before use, this is much more difficult with powders. There are sieves that can remove contamination, but to be on the safe side, the powders should be protected from contamination right from the start.
When 3D printing with resin, sunlight must be considered in addition to safe storage of the material. Since resin 3D printing works with the use of UV light, sunlight can cause prints to cure in the wrong places, resulting in misproductions. Therefore, a room completely protected from sunlight is essential for resin 3D printing. Simple shutters or even curtains do not fulfill this requirement!
With all Additive Manufacturing technologies, attention should also always be paid to an appropriate room temperature and humidity. The values required here depend on the technology and printer. Here, too, it is advisable to obtain information before purchase in order to prevent a surprising incompatibility between the machine and the room.
The last sub-item for compliance with specified printing processes is material selection. It should be obvious, yet mistakes still happen because of it. If a 3D printer does not have an open material platform, only materials compatible with the printer can be used to ensure effective use!
Can a 3D printer print third-party materials without an open material platform? It may print them, but there will be massive losses in quality and success rate.
Therefore, information about the material selection of the printer and the respective properties of the usable material must also be collected here before the purchase in order to guarantee the most effective use of the 3D printer.
So surely the success rate with adherence to the specified printing process will be 100%, right? Unfortunately not.
Even if you follow all the tips in this blog, the success rate will never rise to 100%. At the end of the day, even Additive Manufacturing is not completely free of errors.
But as mentioned earlier, especially in series production, even small increases in the success rate have a massive impact. Productivity is increased and the cost per part is reduced. To achieve these two essential goals in production, the basic specifications of the printing process must always be adhered to.
In contrast to compliance with the printing process, no research is needed in advance to achieve full utilization of the build plate. However, this does not make this point less important.
With some printing technologies, such as (Metal) Binder Jetting or Selective Laser Sintering, the entire build plate is processed with each individual print, regardless of whether it is fully loaded or not.
Therefore, especially with these technologies, but also in general, it is worthwhile to utilize the building plate as fully as possible through correct planning and efficient placement of the individual components.
This greatly reduces the costs per part, especially for series production. After all, whether the build plate is only being used at 20% or 95% of its capacity does not change anything in terms of power usage, wear on the printer or the time required for removing the build plate, for example.
But how can the prints now be planned most efficiently? On the one hand, some individual questions that depend on the component itself must be answered. How many of these components will be needed in the near future? Is pre-production or even rather just-in-time production worthwhile? These are questions which, because of their individuality, do not permit a generally valid answer. However, the maximum utilization of the building plate should always be considered in production planning, no matter what the answer to these questions is.
On the other hand, some 3D printing software now offer help to achieve maximum utilization of the build plate. The process of 3D nesting describes the software-controlled placement of individual components in cuboid ratios on the build platform. The components do not have to be cuboid-shaped, but in order to give the components the minimum required space, the cuboid shape is also used for differently shaped components.
This nesting can happen manually. Within the software, the user places the individual cuboids next to each other to get as many individual components as possible onto a build plate.
However, this process is now automated in certain software solutions. The software therefore decides for itself how the individual components can be placed on the building panel as efficiently as possible. Necessary support structures are also automatically included in the calculation.
This automation both minimizes human error and saves time. As a result, the maximum effectiveness of component placement is achieved, and with it, the maximum utilization of the build plate.
Automation is the appropriate keyword, because to increase the effectiveness of the 3D printer and the printing process, additional accessories are perfect for further automation of the printing process.
Additive Manufacturing already offers a high degree of automation in principle. Today, industrial printing equipment in particular can produce precise, high-quality components with little human interaction. But with the right accessories, human interaction can be reduced even further, and with it labor costs and the risk of human error.
There are three major sub-areas that can be used to further automate the printing process. Software, post-processing and production cells.
The automated 3D nesting function of some software has already been explained in the previous point, but there are many more automation possibilities, which can be implemented by the appropriate software.
The generation of support structures, the start of the print job, the adjustment of parameters, error corrections, the removal of air bubbles and an uncountable number of other smaller and larger steps in the printing process can now be automated with suitable software.
The right 3D printing software also provides support for other processes. Whether error messages are sent by e-mail, saving of the printing process in the event of a sudden stop (e.g. due to a power failure) or an indication of material consumption, the software plays an essential role in 3D printing in order to make the production of the components as effective as possible.
Can a 3D printer be operated without high-end software? In most cases, yes. Can the same productivity ever be achieved without such software as with it? In no case. Therefore, the right 3D printing software is almost as important as the machine itself to achieve maximum effectiveness.
Post-processing of components is a mandatory requirement for the best possible quality in many printing technologies. At the same time, post-processing can be very time-consuming. Cleaning, polishing, inking, curing, or even several of these steps for hundreds of components - it adds up to a lot of work. Fortunately, there is now relief thanks to automated post-processing solutions!
Powder handling stations that autonomously sift leftover powder and thus make it reusable, machines that combine several of the post-processing steps just mentioned and thus prevent constant removal, walking and insertion, and automatic resin removers for components now make it possible to massively minimize human interaction in this step of the printing process as well.
This minimum consists almost exclusively of inserting and removing the components into and from the respective machine. But what if even this step could become obsolete with the right accessories? Cross out the "could", because it is already possible!
Production cells, e.g. the V1 production cell from Additive Automation, offer the maximum degree of automation for Additive Manufacturing. They reduce human interaction to an absolute minimum.
The robotic arm of the production cell independently pushes the components into the printer, removes them again after the printing process, places them in the appropriate post-processing station, then starts the next print job and deposits the fully post-processed components in a suitable location.
Such a production cell achieves the highest possible level of automation, increases the effectiveness of the entire printing process, and completely eliminates human error. Occupational safety is also improved by such automation.
However, such production cells are still at the beginning of a long development. Currently, for example, the V1 production cell from Additive Automation is only compatible with resin 3D printing and certain steps, such as material feed or post-curing, are not yet integrated in this automation solution and therefore have to be taken over manually. But in the near future, the possibilities of this full automation will multiply and improve in big steps.
If automation has now advanced to the point where almost the entire printing process can take place without human interaction, will human knowledge still be needed at all? Are trained specialists still needed or will anyone soon be able to keep the printing process running?
The fact that automation at least minimizes the need for trained specialists cannot be denied. But what all the automation in the world cannot replace, and what was an essential factor in the effective use of a 3D printer even before automation was possible, is experience.
People like to overestimate themselves very often. But in few things as much as in the understanding of technology and thus also the understanding of 3D printers.
It likes to look so simple in videos. Press a button, let the printer do its work, remove components and the printing process is finished. Anyone can do that, right?
The fact that not only the actual printing process, but also the creation of or at least the correct handling of the digital files must be mastered for 3D printing is all too often ignored. Even dealing with error messages, the correct leveling of the print bed or the exact sequence of the individual post-processing steps are not quite as obvious to many as "simply pressing a button" on the printer itself.
Therefore, experience in 3D printing is an often underestimated, but probably the most essential factor to ensure the effectiveness of a 3D printer. But what is the best way to gain this experience?
As simple as it sounds: try and experiment. For this reason, I made it clear at the beginning of the blog post that I don't want to take away the joy of experimenting, because it is an important step to gain experience.
However, the expectations must be adjusted accordingly for such experiments. Many, if not most, of these experiments will fail. 3D printing is not as simple as it sometimes seems.
But, as it is in life: Failures are part of it and are perfect for gaining new experiences.