3D printers
High quality 3D printers
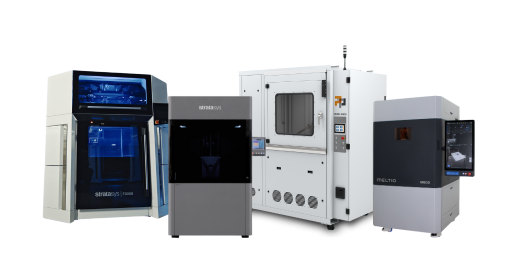
25% discount on your first order of 3D printed components!
SAVE SUMMER DISCOUNT NOW!The perfect symbiosis of quality and quantity!
Complex geometries with ideal properties!
High-resolution components with a wide variety of materials!
High-performance components with sustainable production!
A wide range of materials and ultra-fast production!
Ideal for a wide range of dental indications!
The process from simple component to product!
Fully automate your production!
Fast processing and successful management!
Sorry, there are no results for this combination of filters. Choose another combination of filters.
To ensure that all requests are handled promptly and completely, we ask that you submit all support requests through our support portal.
To the service portalDo you need assistance with your project, do you need advice or a sample part that we can send you?
Send EmailTeeth can be quite a troublesome subject. Even with good care, individual clinical pictures cannot be ruled out - and there are quite a few of these clinical pictures. Bruxism, caries, gingivitis, pulpitis, tooth root inflammation and many other diseases exist that people have to deal with on a daily basis.
Every day is no exaggeration. The health insurance companies' expenditure on dental treatment are rising around the word. The reasons for this are obvious - life expectancy is increasing and at the same time our eating habits are becoming increasingly tooth-unfriendly.
Unfortunately, additive manufacturing cannot reverse these trends. Nor can it prevent dental diseases. But it can simplify and improve treatment methods, make them more cost-effective and at the same time increase patient safety and comfort - and it is already achieving all of this on a large scale.
Before we come to the many possibilities of 3D printing in dentistry, we should first clarify which of the many different technologies within additive manufacturing are suitable to fulfill these possibilities for the dental industry. The answer to this question is also quickly given - resin 3D printing.
Resin 3D printing, which cures liquid biocompatible resins using UV light, has long been a guarantee for the fast and detailed production of various indications and tools for dentistry thanks to its immense accuracy and the wide range of materials available that are specially designed for the dental industry.
The sub-category of the resin 3D printer basically plays a subordinate role. Whether stereolithography (SLA), digital light processing (DLP), lubricant sublayer photo-curing (LSPc®) or PolyJet™ - all of these technologies are capable of producing high-quality parts, although certain details, such as speed, may vary. To get a more detailed overview of the individual subcategories of resin 3D printing, I recommend the following introduction to the topic.
In addition to resin 3D printing, 3D printing with powder is also suitable for illustrative models and prototypes. However, fully functional indications are not yet possible with this printing technology, which is why resin 3D printing remains the only option for additive manufacturing, at least for the time being.
So now we know the ideal 3D printing technology for dentistry - all well and good. But how exactly can additive manufacturing help to make the dental industry more productive?
3D printing offers various advantages over traditional subtractive manufacturing. One of the biggest advantages, especially in the dental industry, is the high speed of 3D printers.
Many dental diseases cause severe pain for patients and even if the waiting time for the right indication can be bridged with painkillers, this is still associated with great discomfort for the patient. Additive manufacturing makes it possible to provide the relief that patients hope for more quickly, thus increasing their satisfaction and comfort.
Additive manufacturing methods have also reached an enormously high level in terms of precision. Particularly when it comes to fine details, which are essential for many indications in the dental industry, 3D printing can outshine conventional manufacturing methods.
The increased design freedom offered by additive manufacturing provides another significant advantage - individuality. No two rows of teeth, jaw shapes or alveolar processes are identical. It is therefore essential that dental indications are precisely adapted to the individual patient to ensure functionality as well as patient safety and comfort. In addition, precise customization also saves time for the dental laboratory or dentist, as multiple adjustments do not have to be made.
However, the benefits of 3D printing in dentistry do not just start with production - the process surrounding this is also simplified and improved by additive manufacturing.
In Germany, the word digitization usually elicits either tired laughter or sad looks. Digitalization is too slow, too intransparent and too complicated in many areas, so that it could almost be described as a utopian fantasy.
Fortunately for us, the dental industry is different and digitalization is not a utopian figment of the imagination. Digitalization in dentistry does not just begin during production, but long before that - namely during the impression-taking process.
Whereas traditionally a negative mold of the oral area is created by the patient's bite on alginate or polyether, which is then filled with plaster, additive manufacturing works exclusively digitally and therefore uses intraoral scanners to obtain an image of the teeth or jaw.
Such intraoral scanners offer several advantages. On the one hand, the level of detail is much higher than with conventional impressions, while on the other hand, error correction is also greatly simplified, as this can simply be carried out on the digital model. At the same time, the running costs for the dental practice can be minimized, as new impression material does not have to be constantly procured, and the reduced space required for the practice should not be underestimated.
This reduced space requirement is achieved through the digital storage of the patient image, which has another major advantage - the complete digitization of the patient file. No more printed images in brown and beige folders, but long-term storage as a CAD model, which also makes it much easier to compare several images over time, which can be extremely important for long-term treatments in particular.
Additive manufacturing therefore not only improves production, but also makes the entire in-house process more efficient. And in-house is the right keyword here, as additive manufacturing enables dental practices to produce their indications in-house as a further advantage.
Just a few years ago, dental 3D printing was reserved exclusively for large dental laboratories. The machines were too expensive and large, and their handling too complex. However, with the widespread introduction of desktop 3D printing solutions, this oligopoly has been broken and smaller dental laboratories and even dental practices can now enjoy the benefits of additive manufacturing.
This increased availability, especially for dental practices, brings massive benefits to both patients and dentists themselves. For patients it means even shorter waiting times and therefore, as already discussed, less pain and for dentists it massively reduces costs as there is no longer a middle man between them and their indications.
Of course, this does not mean that dental laboratories are outcompeted by these desktop solutions. Industrial dental 3D printers are still necessary, especially for complex indications or large production volumes, and the experience of large dental laboratories should not be disregarded, despite the future potential of the technology - especially for costly indications where errors not only affect honor, but also the wallet.
As essential as the quality of the indications and patient well-being are, at the end of the day the work and production must be worthwhile in terms of costs. Fortunately for us, 3D printing also scores highly in this aspect of dentistry.
Dental materials for 3D printing are generally in a similar price segment to traditional materials for subtractive manufacturing. However, where additive outperforms subtractive manufacturing is in material economy - and therefore in cost efficiency.
In subtractive manufacturing, material is removed in order to produce components, which inevitably leads to waste. In contrast, with additive manufacturing, the component is created layer by layer, which means that no excessive waste is produced. Only the thin support structures on the respective indication have to be disposed of, which nevertheless means a massive reduction in waste production.
Another cost item that 3D printing can reduce is personnel costs. Whereas conventional production still requires a lot of manual or supervised work, 3D printing solutions are now equipped with highly automated functions that make it possible to simply "press start - walk away - receive indication".
Last but not least, a banal economic fact that is nonetheless extremely important. Those who produce more can earn more money. The massively increased production speed through 3D printing provides more capacity and therefore more opportunities to earn money - both for dental laboratories, through the resale of indications, and for dental practices, through the greater patient capacity.
Now that the advantages of additive manufacturing within the dental industry have been outlined, it is of course essential to highlight the tools and indications that can be additively manufactured.
The classic application of 3D printing in dentistry is models of all kinds. Whether simple illustrative models, models with dies or models with crown margins to check the fit. The high degree of individualization is particularly important here, as it allows models to be produced that can precisely reproduce the characteristics of each individual patient.
Individual impression trays are another long-established application. Even though intraoral scanners are becoming increasingly popular and offer many advantages, classic impression trays are still widely used and 3D printing allows them to be produced more individually, faster, more cost-effectively and to a higher quality.
Customized surgical guides from the 3D printer are also very popular with dentists, as autoclavable and biocompatible surgical guides for placing implants, for example, can now be ideally produced additively.
The list of indications for which additive manufacturing is now used is long. Splints of all kinds, whether grinding, transfer or occlusal splints, dentures, bridges, crowns - the list could go on for quite some time.
While most materials were not suitable for use on the human body when 3D printing first became widespread in dentistry, there are now several manufacturers who produce and sell materials for short-term contact, e.g. Class IIa, or for permanent contact with the human body.
This now enables the additive manufacture of permanent dental prostheses, which in classic production causes much higher costs and waiting times. Unfortunately, the choice of manufacturers and materials for such permanent indications is still relatively limited - but the future will almost certainly bring further development and progress.
While the gradual digitalization of the dental industry began back in the 1970s with the first digital scans and was further advanced with the first 3D printers in the 1990s, the progress was only very pale for a long time - especially for patients.
However, dental 3D printing has been flourishing for several years now. The spread of desktop 3D printing solutions in particular has led to a renaissance in dental digitization. More and more dentists are switching to additive production for their indications and more and more dental laboratories are offering the option of purchasing 3D-printed parts.
This trend is unlikely to stop in the future. The advantages of additive manufacturing are too great. Where exactly research will take us, however, is still written in the stars. The new indications, materials and printing solutions that will be added are still a mystery.
But as soon as these secrets are revealed, you can be sure that a new article on the advances in the dental industry will be eagerly awaited. So check back here regularly!
Cookie settings
We use cookies to provide you with the best possible experience. They also allow us to analyze user behavior in order to constantly improve the website for you. Privacy Policy