3D printers
High quality 3D printers
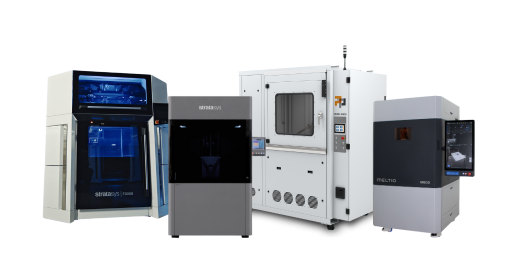
Metal 3D printing is one of the most versatile technologies around. It now involves a wide range of different processes, different material forms and a cross-industry variety of applications, which is why more and more industries are turning to this technology.
The range of applications for metal 3D printing has grown enormously in recent years. What was once only suitable for simple prototyping now enables ready-to-use end-use components for the most demanding industries, such as automotive, aerospace and maritime.
Despite the many advantages and applications, metal 3D printing has also meant a major change. For decades, traditional metalworking methods, such as CNC machines, were the norm, and integrating 3D printing seemed to be too costly for many companies, at least in the short term.
However, thanks to our new partnership with the Spanish company Meltio, this paradigm has been rendered obsolete. Meltio has focused specifically on equipment that is perfectly suited for integration with traditional manufacturing methods – not to replace them, but to work in symbiosis with them to make metal processing more productive than ever before.
Meltio has a unique role in our portfolio. With these systems, we offer our customers an ideal option for expanding their capabilities, options and applications in the field of industrial metal processing without having to make any changes to their workflow or construct special premises.
This blog post will discuss these unique systems, their advantages and applications. First, we will look at the technology behind Meltio's solutions. Then I will present the individual systems briefly and concisely before moving on to the application areas and advantages.
This blog post will give you an ideal insight into Meltio's solutions – and thus also into the latest generation of metal 3D printing. If you are already familiar with Meltio's technology and solutions, you can jump directly to the advantages and application areas using the button below.
All Meltio systems use the same process, known as Laser Metal Deposition (LMD for short). This process is a subcategory of the DED (Direct Energy Deposition) printing process and is also referred to as laser deposition welding in German-speaking countries.
In this process, the top layer of an existing metal component or a substrate, for example a simple metal plate, is melted by a high-power laser. The material, in the form of metal powder or metal wire, is applied to this now hot and liquid metal – the so-called molten pool. With the help of the laser and the temperature of the molten pool, it then melts with the existing component or base to form a single, continuous surface. The Meltio systems focus on wire processing, which is why Meltio also refers to its technology as “Wire-LMD”.
However, for most applications, a single layer is not sufficient, which is why the newly created surface is melted again by the laser. After that, more powder or wire is applied, which melts again in the molten pool to form the new surface. This process is repeated layer by layer until the component is finished.
However, classic laser deposition welding differs from Meltio's LMD technology in some aspects. One of these differences concerns the laser used. While conventional laser deposition welding uses a single laser beam entering through the center of the application head, Meltio's LMD process relies on several smaller diode lasers evenly distributed around the center axis of the head. This allows the power of the laser to be adjusted much more precisely and significantly improves the uniformity of the temperature in the weld pool.
Another unique feature of Meltio's LMD technology is the special application head. This has been designed so that both the weld pool and the wire can be processed by the laser from any position. This allows the direction of work to be changed freely without affecting the temperature of the weld pool or the processing of the wire.
Another key difference is the ability to use multiple materials simultaneously. All Meltio systems feature dual-wire functionality, which allows two wires to be processed simultaneously. This makes it possible to precisely adapt the performance characteristics of the components to the respective requirements and to reduce costs, for example by using more expensive materials only where they are actually needed. This function also increases design freedom, as engineers can create complex components with different properties within the same structure.
The last significant difference is the use of what is known as “hot-wire technology”. In this process, the metal wire is electrically preheated before it comes into contact with the weld pool and the laser, which offers a number of advantages. For one thing, the application process is accelerated and the consistency and precision of the application are increased. In addition, the thermal shock to the weld pool is reduced by the higher base temperature of the wire.
Now that we have discussed the basic technology of the Meltio systems, we will now turn to the specific solutions that Meltio offers. We will proceed chronologically by market launch date, starting with the Meltio M450.
The Meltio M450 is a compact turnkey solution for metal 3D printing and is equipped with six 200-watt direct diode lasers with a wavelength of 976 nm. This provides unparalleled control over energy distribution and the molten pool, ensuring optimal material deposition and faster build rates.
The entire printing process of the M450 is continuously and real-time monitored by a closed-loop system. Using high-speed cameras and a pyrometer, the size and temperature of the melt pool are detected and reported to the system. Based on this data, the system continuously adjusts parameters such as laser power and material feed. Thanks to this closed-loop control, potential anomalies can be quickly identified and remedied, significantly increasing the reliability of the entire system.
Thanks to inert environment control, the M450 can also process reactive metals. Compatibility with various shielding gases, such as argon, nitrogen and helium, makes it possible to adapt the pressure environment to the respective material in order to completely avoid stress corrosion cracking.
In terms of material selection, the M450 offers a very wide variety thanks to its open material system. Meltio provides a wide range of materials – from stainless and tool steels to high-carbon steels and various nickel and titanium alloys. The open material system considerably expands this selection, so that other steels, nickel and titanium alloys, as well as materials such as copper and gold, can be processed with the Meltio M450.
All these advantages are complemented by the dual-wire and hot-wire functions already mentioned and rounded off by a powerful software ecosystem. With a print area of up to 150 x 170 x 425 mm, the M450 is ideal for the production of small series, spare parts, as well as for subsequent adjustments and repairs to metal components.
The second system in Meltio's portfolio, and thus now in ours, is the Meltio M600 metal 3D printer. This takes over important functions of the M450, such as closed-loop process control, hot-wire technology, inert environment control and the open material system, but significantly expands the range of applications with new and improved features.
The most important innovation concerns the lasers. Instead of six lasers, nine lasers are now mounted on the application head, which have a wavelength of 450 nm and are therefore referred to as “blue lasers”. This changeover to a different type of laser enables a significantly higher printing speed – up to 60% faster than the M450 – as well as lower energy consumption, without any compromise on print quality.
The dual-wire technology of the M450 has also been improved and is now available as quad-wire technology. With up to four different materials that can be processed simultaneously, components with gradual transitions in material composition are possible, opening up a wide range of new applications.
The size of the print area has also been expanded on the M600. Users now have a print volume of 300 x 400 x 600 mm, which allows for both large-format components and the simultaneous production of several smaller components.
Last but not least, a 3-axis touch probe and a zero-point clamping system have been integrated into the M600. These features were designed with the machining of existing metal parts in mind. Whether it's repairs or part enhancements, the touch probe allows the system to detect the exact location and orientation of a workpiece and perform precise machining. The zero-point clamping system also makes it easy to switch between workpieces and facilitates a seamless transition between the M600 and traditional manufacturing methods.
As mentioned at the beginning of the blog post, the strength of Meltio solutions lies particularly in their interoperability with traditional manufacturing methods, especially with CNC machines. Meltio achieves this specifically through the Meltio Engine CNC integration, which allows the M600 print head to be directly connected to CNC machines to enable hybrid manufacturing solutions.
This hybrid solution opens up numerous advantages for conformal manufacturing. Integrating subtractive and additive manufacturing processes into a single workflow is a significant step towards Industry 4.0 and enables companies to work more efficiently, quickly and with higher quality.
A key advantage of the Meltio Engine CNC Integration is that there is no inherent size limit to this solution. The print head's working area is limited only by the size of the CNC system's motion system, enabling the production of components in dimensions that would be either impossible or uneconomical with standard printing systems.
The focus on interoperability goes hand in hand with a strong focus on compatibility when it comes to Meltio Engine CNC integration. The engine is designed to be compatible with almost any CNC machine. Whether it's a Haas Automation, LAGUN, Jupiter, KUKA, Siemens or many others, Meltio Engine integration is a cost-effective solution for seamlessly retrofitting additive manufacturing capacity. This significantly expands metal processing capabilities without the need to purchase dedicated additive manufacturing equipment.
In addition, this solution offers all the advantages already described for the M600, such as closed-loop process control including laser and wire modulation, extensive material selection, blue lasers, dual wire and hot wire functionality.
The M600 print head is not only suitable for CNC machines. To further maximize design freedom and productivity, Meltio also offers the Meltio Engine Robot Integration, in which the M600 print head is installed on robot arms.
This transforms robot arms into flexible and highly autonomous metal 3D printing systems that are limited in component size only by the robot arm's range of motion.
Meltio also places a strong emphasis on compatibility with different robot arms for this solution. The engine is compatible with most industrial robot arms, as only the payload – at least 45 kg – and the number of digital inputs and outputs – at least eight – are crucial for optimal integration.
Meltio also offers the Meltio Space software specifically for this solution, a customized solution for integrating the print head and robot arm. Meltio Space allows the user to set numerous parameters and choose from a range of slicing strategies, so that the process can be customized down to the smallest detail.
This solution also includes all the advantages of the M600 already mentioned, making the Meltio Engine Robot Integration a powerful all-purpose solution for metal 3D printing.
When you think of industrial manufacturing and highly autonomous robotic arms, the terms “plug and play” do not usually come to mind. Rather, you think of lengthy setup processes, complex cabling and numerous test cycles to optimize the system for maximum productivity.
However, the Meltio Robot Cell focuses on the plug-and-play principle. This solution, developed by Meltio, comes with a six-axis robotic arm that is fully pre-integrated and only needs to be connected to a power source and inert gas to be ready for use. Instead of complex integration processes and time-consuming assembly, all that is needed to get started is these two simple connections before production can begin.
In terms of part size, Meltio placed particular emphasis on flexibility in the Robot Cell. The Robot Cell is compatible with three different actively cooled build plates in different sizes. In addition, Meltio offers the option of integrating customized build plates, making the system suitable for small, medium and large-sized parts.
Another focus in the development of the Robot Cell was safety for users and the system. The Meltio Robot Cell is certified as a Class 1 laser product in accordance with the laser safety standards EN 60825-1 and EN 60825-4, has a fire protection classification of B-s2, d0 according to DIN EN 13501-1, is CE certified and combines all control options on a central screen for quick emergency response. As a result, the Robot Cell does not require any special safety infrastructure and can be used in a standard industrial environment without any problems.
Finally, it should be noted that the advantages of the M600 print head fully apply to the Meltio Robot Cell and, thanks to the integration of robotics, can be taken to a new and impressive level of performance.
Even though some advantages have already been mentioned in the course of this blog post, I would like to take a closer look at some of the many positive aspects that users get from using Meltio's metal 3D printing solutions – starting, of course, with the main focus of the machines.
Meltio's guiding principle is to close the gap between additive and subtractive manufacturing. Starting with the M450 as a standalone system, further developed with the M600 specifically in the area of integration, and finally through various engine integrations, Meltio is constantly creating new possibilities for combining additive and subtractive manufacturing methods.
With its solutions, Meltio occupies a unique position in the market. By providing industrial print quality in a modular way, Meltio is making a huge contribution to the expansion of additive manufacturing. Companies no longer have to choose between different manufacturing methods, convert their production or purchase expensive dedicated 3D printing systems to additively manufacture metal components. Instead, they can flexibly leverage the advantages of 3D printing in symbiosis with their existing manufacturing capabilities.
Meltio's hybrid solutions thus lay the foundation for efficiently scaling up and future-proofing metal processing. The speed and scale of this scaling is left to the individual companies and their requirements. Some may start with a CNC integration engine, others may go for a dedicated machine with maximum interoperability, and still others may go straight for the plug-and-play Robot Cell. Regardless of the path to scale, all options benefit from increased productivity through easy integration into existing production cycles.
Particularly in the field of spare parts production and the repair of damaged metal components, high speed is not only desirable but absolutely essential to minimize downtime – which in industries such as aviation or the maritime industry can cause millions of dollars in damage after just a few hours.
Meltio's systems and solutions have established themselves as an excellent option in this area. On the one hand, the high speed is achieved by focusing on wire instead of powder, which significantly increases deposition rates. On the other hand, the unique hot-wire technology ensures that the wire does not have to be fully heated by the weld pool.
Another advantage for the printing speed is the laser configuration. By using several small lasers instead of a single large one, the temperature of the molten pool can be increased faster and stabilized better. This reduces the lead time while increasing the consistency of the process. Overall, the Meltio systems achieve an application rate of 1 kg/h and are thus many times faster than conventional metal 3D printing systems.
The ability to process multiple metal wires simultaneously while maintaining outstanding quality opens up a world of new possibilities for engineers.
In addition to the aforementioned option of manufacturing components with gradually changing material properties, this function also offers the unique possibility of producing metal matrix composites (MMCs) – without the use of powder metallurgy, which is associated with high costs and a complex manufacturing process.
By customizing the material properties in a single material, extraordinary combinations can be created. Particularly in terms of the strength-to-weight ratio, for example in the aerospace or automotive industries, MMCs based on titanium or nickel are an excellent choice.
One advantage of Meltio's technology and equipment that has not yet been mentioned, but which is undoubtedly very important, is the very high density of over 99.99% that components manufactured by LMD can achieve immediately after printing.
This excellent density is achieved through the uniform connection between the substrate and the wire. In other processes, such as binder jetting or material extrusion, such a uniform connection can never be achieved. Even after the sintering process, these components still have an inherent porosity. Although the density can be increased through post-processing steps, in particular infiltration, it will never reach the level of density of LMD components.
Thanks to this high density, Meltio's LMD process can be used to produce components with exceptional strength, resilience, durability, stability and abrasion resistance. This is particularly important for industries in which components are subject to permanent or repeated stresses, such as the automotive and mechanical engineering industries.
Many metals are expensive. To maximize profit margins and minimize environmental impact, it is essential for metalworking companies to avoid wasting material and to use the available material efficiently.
In addition to the advantages of the dual or quad wire function, which have already been discussed in detail, and which allow metal components to be manufactured from several materials so that more expensive metal is only used where it is really necessary, Meltio's LMD process is also characterized by a fundamentally high material efficiency.
The average scrap rate in Meltio's LMD process is only 1 to 2% of the total wire, with this scrap occurring mainly at the end of the wire spool. For a standard 15 kg capacity spool, this results in only between 150 and 300 grams of material scrap, which can significantly increase material efficiency in metal processing companies.
Particularly when processing and repairing existing components, the highest precision is required because an existing or formerly existing contour must be reproduced without errors in order to avoid extensive rework and the associated downtime.
In this regard, Meltio's technology and equipment shine. Thanks to the multi-laser configuration, the uniformity of the weld pool and thus also of the deposition process is optimized. In addition, the closed-loop process control ensures automated intervention in the event of potential errors.
Meltio's solutions also feature an integrated wire feeding system that ensures that the distance the wire has to travel before it reaches the molten pool remains constant. This further increases precision and almost completely eliminates errors in the application process.
Finally, I would like to turn to the most important areas of application that are made possible by Meltio's solutions. In doing so, I will consider both specific applications and entire industries that can benefit from the advantages of Meltio technology.
One of the biggest unique selling points of Meltio systems within additive manufacturing is their ability to be used to precisely repair existing components. Classic metal 3D printing processes such as binder jetting can also be used to produce repair parts that can then be manually welded onto the component, but Meltio simply combines these two process steps into one, ensuring maximum consistency in the bond.
Thanks to their built-in touch sensor and zero-point clamping system, the Meltio M600 and the associated engine integrations are particularly suitable for precisely repairing components. With the Meltio Engine CNC Integration, for example, the areas in need of repair can first be milled down to a uniform level and then rebuilt by the M600 print head without the need for a further, dedicated process.
With Meltio solutions, even the most complex fractures or cracks can be repaired quickly and easily – even in large components. This gives industries such as aerospace, maritime and automotive an enormous advantage, as the seamless transition between subtractive and additive manufacturing methods can greatly accelerate repair processes.
Surface treatment of components is similar to repair. Meltio solutions enable users to modify and improve the surfaces of existing metal parts quickly and cost-effectively.
Meltio systems offer a wide range of options, from surface coating, for example with tungsten carbide to increase wear resistance, to hardfacing, for example with Stellite 6, to improving surface quality thanks to a new, seamless bond between layers.
The MMCs already mentioned can also be used here. By precisely adapting the surface properties through the combination of several materials, unique combinations can be created that are particularly useful in high-performance industries.
Large-format capabilities are essential, especially when it comes to integrating multiple components into a single part. Such integration offers several advantages, from cost reduction through avoided labor and assembly steps, to weight reduction, and increased reliability.
All these advantages can be easily achieved with Meltio systems, especially the engines for CNC and robot integration. Due to the non-existent inherent size limit, components that measure several meters diagonally can be produced with the Meltio engines, and even the M600, with its considerable build volume of 72 liters, can produce large components quickly and easily.
The maximized design freedom offered by additive manufacturing can further increase the advantage of lightweight construction for large-format components by, for example, simply integrating cavities, lattice structures or honeycomb shapes into the component. This way, weight can be saved in non-critical areas, for example to achieve improved fuel efficiency in aviation.
The defense industry and the military are two of the biggest beneficiaries of Meltio's LMD technology. For example, the US Navy, on board the amphibious warship USS Bataan, and the French Navy, to repair their flagship Charles de Gaulle, already rely on Meltio's solutions.
This trust is based on several reasons. On the one hand, the excellent scalability that goes hand in hand with the modular design and the easy integration of the systems into existing production cycles, and on the other hand, the ability to carry out repairs without lead times, thus minimizing downtime, which can be expensive in the military.
Other reasons for using Meltio LMD technology in the military include its excellent precision and wide range of materials. This is particularly beneficial in terms of safety, as it means that soldiers and other military personnel can rely on their equipment being operational and functional even in crisis situations.
In motorsport, many factors are of crucial importance, but two of them play an exceptional role when it comes to the decision between victory and mid-field: lightweight and speed of reaction. Both are provided by Meltio solutions.
Lightweight design plays a particularly important role in development. With ever newer methods, motorsport teams are trying to reduce the weight of components such as piston heads, cylinder heads, brake discs and many more, and Meltio systems are the ideal tool for implementing these methods quickly and precisely – whether for prototypes or end-use parts.
Speed of response is also of the essence when it comes to repairs. In many motor racing leagues, there are only a few days between races, which is why damaged components have to be repaired as quickly as possible. The on-demand capacity of Meltio systems is ideal here, as repairs can be carried out quickly and safely.
The final major application area for Meltio's systems is the oil and gas industry, where a wide range of components have to withstand particularly abrasive environments that can cause wear, corrosion and fatigue damage to expensive components.
To prevent such damage from occurring in the first place, the LMD process enables critical components to be precisely coated with wear-resistant materials, such as tungsten carbide.
Should damage nevertheless occur, the combination of subtractive and additive manufacturing methods means that the affected areas can be fully repaired, even in potentially difficult-to-reach places such as on drilling rigs.
With Meltio's systems, we can open up completely new possibilities for our users. In particular, processing existing components has never been easier, and the systems from Meltio also show outstanding results in the production of new components.
We are proud to be working with such a revolutionary and forward-looking manufacturer from now on. We are pleased to be able to offer Meltio's solutions to our customers as well, to help advance the future of metal additive manufacturing in leaps and bounds.
Specific information about the individual Meltio systems can be found here. Thank you for your attention – and see you in the next blog post!