3D printers
High quality 3D printers
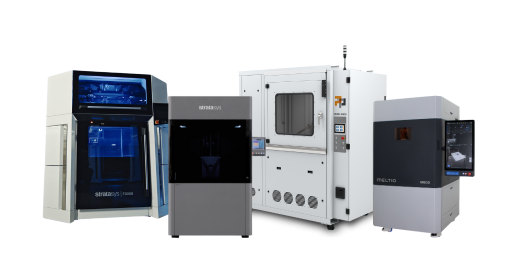
25% discount on your first order of 3D printed components!
SAVE SUMMER DISCOUNT NOW!The perfect symbiosis of quality and quantity!
Complex geometries with ideal properties!
High-resolution components with a wide variety of materials!
High-performance components with sustainable production!
A wide range of materials and ultra-fast production!
Ideal for a wide range of dental indications!
The process from simple component to product!
Fully automate your production!
Fast processing and successful management!
Sorry, there are no results for this combination of filters. Choose another combination of filters.
To ensure that all requests are handled promptly and completely, we ask that you submit all support requests through our support portal.
To the service portalDo you need assistance with your project, do you need advice or a sample part that we can send you?
Send EmailWhile additive manufacturing has been at the center of ART’s business since the beginning, today about half of the end products they produce are not 3D printed, but cast urethane. Casting in urethane has allowed ART to produce low cost plastic parts with a quick turnaround. It is a very hands on process that takes a minimum of 24 hours per mold, requires a significant amount of labor, and the end result is a mold capable of up to 25 parts depending on the material being cast. That said, the effort appears worthwhile based on the high demand from their customers. “Our cast urethane is about 50% of our business right now and we’re almost maxed out,” says Bruce LeMaster, Founder and Vice President of ART. In addition to urethane, ART follows a similar 24 hour process for silicone molding. With such high demand, LeMaster and the team at ART were all but maxed out with a very real cap on the volume of projects they could take on.
Cookie settings
We use cookies to provide you with the best possible experience. They also allow us to analyze user behavior in order to constantly improve the website for you. Privacy Policy