3D printers
High quality 3D printers
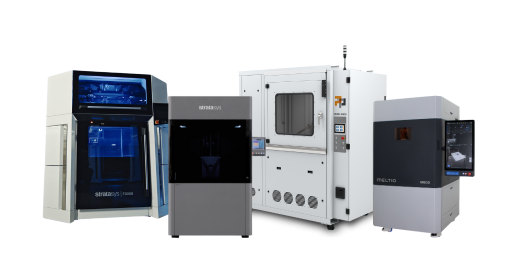
25% discount on your first order of 3D printed components!
SAVE SUMMER DISCOUNT NOW!The perfect symbiosis of quality and quantity!
Complex geometries with ideal properties!
High-resolution components with a wide variety of materials!
High-performance components with sustainable production!
A wide range of materials and ultra-fast production!
Ideal for a wide range of dental indications!
The process from simple component to product!
Fully automate your production!
Fast processing and successful management!
Sorry, there are no results for this combination of filters. Choose another combination of filters.
To ensure that all requests are handled promptly and completely, we ask that you submit all support requests through our support portal.
To the service portalDo you need assistance with your project, do you need advice or a sample part that we can send you?
Send EmailUnlike laser-based systems that selectively melt metal powder, the StudioSystem™2 extrudes metal rods (80% metal / 20% binder )- similar to an FDM / FFF printer. As a result, we eliminate all safety requirements often associated with metal 3D printing. The technology enables lightweight parts, through the use of a honeycomb structure inside the part.
Build space: 300 x 200 x 200 mm (12 x 8 x 8 in)
Min layer height: 50 µm
Metal rods offer several advantages over metal filaments: rods contain a higher percentage of metal powder, as they do not require the flexibility of a wound filament coil. This has a direct impact on part shrinkage and allows for higher density in the final product. In addition, users can use the entire cartridge during printing and replace it without stopping printing. This is not possible with filaments, which require a constant feed rate.
In addition to a printhead with a standard resolution (400 µm diameter), we offer an optional printhead with higher resolution (250 µm diameter). All print profiles are matched and optimized for both extruders. The high-quality extruder allows four times the resolution - ideal for small parts and/or complex part geometry.
Quick-release printheads and push-to-release material cassettes allow material changes within one minute while preventing contamination when you switch from one alloy to another. Material changes on laser-based systems involve long changeover times and can even take days.
A broad material portfolio guarantees the right choice of materials, depending on the requirements. Even non-weldable materials can be processed in comparison to the DMLS process. A homogeneous microstructure is achieved in the microstructure.
The Desktop Metal® Studio System™ 2 sintering furnace was designed to be as easy to use as possible. It first heats parts to remove all binders from the parts, then raises the temperature to near melting to provide industrial-grade sintering in an office-friendly package. Built-in temperature profiles, tuned for specific materials, ensure uniform heat treatment. This avoids the residual stress that occurs with laser-based processes.
Max. Temp.: 1400 °C
Outer dimensions: h 162 w 138 d 75 cm (64 x 54 x 30 in)
The sintering furnace has a fully accessible chamber with a stackable retort. Unlike standard tube furnaces, loading and unloading of parts are quick, easy, and clean.
An adjustable shelf system allows sintering of one or more chambers. The number of chambers can be adapted to the component size and thus offers the highest possible efficiency.
Automatic opening and closing of the furnace door with a simple push of a button ensures reliable and precise sealing for all sintering runs, without the need for tools or manual tightening of screws.
The graphite retort provides a thermally conductive, uniform heating chamber with integrated gas channels. Compared to tube furnaces, this ensures greater thermal uniformity and a consistent gas flow throughout the process.
To sinter a fine and homogeneous structure, high temperatures and thermal uniformity are required. The sintering furnace reaches a peak temperature of 1,400 ° C - a temperature required to sinter many metals to the highest possible density. Furnaces that only reach 1300 ° C can only produce many steels with a density of 94%.
The sintering furnace utilizes heating elements surrounding the retort on all sides. This arrangement of heating elements contributes to the unique ability to maintain a ± 5 °C tolerance on sintering temperatures, which contributes to uniform sintering throughout the chamber.
During the thermal debinding process, which takes place at the beginning of sintering, the binder remaining in the part is heated and converted into steam. The furnace vacuum pump draws the binder vapors out of the chamber into the binder trap, where they cool and condense. This prevents contamination and ensures uniform shrinkage. The vacuum pump contributes significantly to lower gas consumption and has a positive influence on the density of the components.
The sintering volume of the Desktop Metal furnace is 10 times larger than comparable standard tube furnaces. The total volume allows the user to sinter large parts with a maximum size of 300 x 200 x 200 mm. Sintering of complete batches is of course possible and can significantly reduce unit costs.
Call or email us and we will be happy to help you.
Cookie settings
We use cookies to provide you with the best possible experience. They also allow us to analyze user behavior in order to constantly improve the website for you. Privacy Policy