3D printers
High quality 3D printers
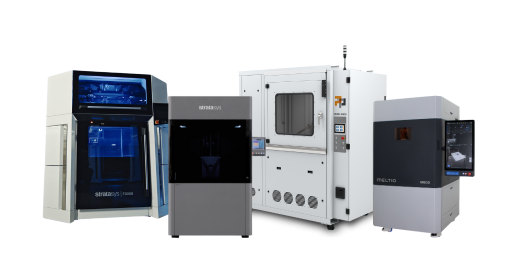
25% discount on your first order of 3D printed components!
SAVE SUMMER DISCOUNT NOW!The perfect symbiosis of quality and quantity!
Complex geometries with ideal properties!
High-resolution components with a wide variety of materials!
High-performance components with sustainable production!
A wide range of materials and ultra-fast production!
Ideal for a wide range of dental indications!
The process from simple component to product!
Fully automate your production!
Fast processing and successful management!
Sorry, there are no results for this combination of filters. Choose another combination of filters.
To ensure that all requests are handled promptly and completely, we ask that you submit all support requests through our support portal.
To the service portalDo you need assistance with your project, do you need advice or a sample part that we can send you?
Send EmailFill up the form below and we will send you the data sheet by e-mail.
BAC launched the next generation of its world-renowned Mono single-seater at the Goodwood Festival of Speed in July 2019. BAC partnered with DSM to co-develop 3D printing applications used in the manufacturing of the Mono, to create a cutting-edge, more organic and lighter design. 3D printing offered BAC significant advantages that included freedom to produce prototype parts with sinuous, organic designs, and considerable weight savings that could not be achieved with traditional methods of manufacturing.
Fill up the form below and we will send you the use case by e-mail.
The ‘formula’ behind Formula One is a series of complex rules and regulations that must be adhered to by the competing drivers and teams. The rules frame a technological window within which each team must produce the fastest car, all within a maximum permissible budget. These regulations create a fiercely competitive landscape where fractions of a gram here, a micron or two there, and the overarching speed of development separate podium finishers from the ‘also rans’.
Fill up the form below and we will send you the use case by e-mail.
Environmental design house Koringa Systems Limited approached Ogle to help develop a prototype for a hand-held chemical and contaminant analysis tool called the Agrichem Residue Tester. The tool was designed to be used in the agricultural sector, to test for possible contaminants in food or hard surfaces, from seed to final harvest, and identify chemicals, pesticides, herbicides and fungicides. Koringa needed to present a realistic prototype of the tool at exhibitions to generate business and investment.
Fill up the form below and we will send you the use case by e-mail.
3D printed lens prototypes are the latest innovation in automotive lighting system applications. One3D uses them for companies including HELLA, Varroc and MSV Elektronika rail vehicle parts. The companies use the lenses as a visual aid to confirm designs before going into large-scale production. Companies are moving away from the high lead times and production costs of PMMA and turning to 3D printing to produce new lens design prototypes for future development and innovation concept products.
Fill up the form below and we will send you the use case by e-mail.
Located in Darlington, County Durham, Paragon Rapid Technologies Limited provides high-level support throughout the product development cycle. With a wide range of customers in many industries, Paragon must adapt to the often-meticulous demands that are required as well as the ever-changing nature of markets. The team is often commissioned to produce prototypes, jigs & fixtures, pattern masters and even end-use models that are needed quickly, making traditional production/manufacturing less viable.
Fill up the form below and we will send you the use case by e-mail.
According to the US Energy Information Administration, a standard wind turbine installed in 2020 generates enough electricity in 46 minutes to power an average US household for a month. However, this type of energy generation would not be possible without the rotors of the wind turbine, which use wind power thanks to the rotor blades or air guide profiles, and Gulf Wind Technology produces these parts. But the design of the rotor blades has been stretching the company's already tight development schedule to the limit. Using conventional manufacturing processes, the production of wind tunnel models is time-consuming. This hinders rapid iteration of the designs.
Fill up the form below and we will send you the use case by e-mail.
![]() |
|
On-demand Webinar |
![]() |
|
On-demand Webinar |
![]() |
|
Photos of the event |
![]() |
|
Watch the video |
![]() |
|
On-demand Webinar |
![]() |
|
On-demand Webinar |
![]() |
|
On-demand Webinar |
![]() |
|
Read more |
![]() |
|
Read more |
![]() |
|
Read more |
![]() |
|
Read more |
![]() |
|
Read more |
![]() |
|
Read more |
![]() |
|
Read more |
![]() |
|
Read more |
![]() |
|
Read more |
![]() |
|
Read more |
Cookie settings
We use cookies to provide you with the best possible experience. They also allow us to analyze user behavior in order to constantly improve the website for you. Privacy Policy