3D printers
High quality 3D printers
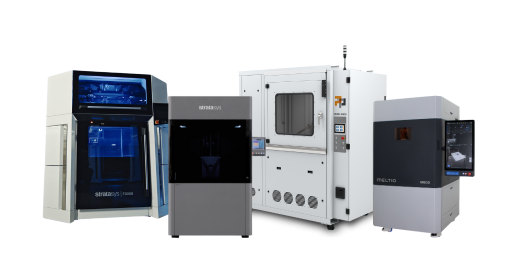
25% discount on your first order of 3D printed components!
SAVE SUMMER DISCOUNT NOW!The perfect symbiosis of quality and quantity!
Complex geometries with ideal properties!
High-resolution components with a wide variety of materials!
High-performance components with sustainable production!
A wide range of materials and ultra-fast production!
Ideal for a wide range of dental indications!
The process from simple component to product!
Fully automate your production!
Fast processing and successful management!
Sorry, there are no results for this combination of filters. Choose another combination of filters.
To ensure that all requests are handled promptly and completely, we ask that you submit all support requests through our support portal.
To the service portalDo you need assistance with your project, do you need advice or a sample part that we can send you?
Send EmailFill up the form below and we will send you the data sheet by e-mail.
Fill up the form below and we will send you the data sheet by e-mail.
Fill up the form below and we will send you the data sheet by e-mail.
Fill up the form below and we will send you the data sheet by e-mail.
While working at ProductionToGo, our employee Johannes accidentally strained his watch band too much, causing one of the links on his watch strap to break. Since this is his favorite watch, he wanted to find a solution as soon as possible to be able to wear it again. Johannes didn't hesitate for long and looked around the web for suitable replacement bracelets. He quickly discovered that these bracelet links are quite expensive, and have long delivery times.
Fill up the form below and we will send you the use case by e-mail.
PepsiCo products are enjoyed by consumers more than one billion times a day in more than 200 countries and territories around the world. PepsiCo generated more than $79 billion in net revenue in 2021, driven by a complementary beverage and convenient foods portfolio that includes Lay’s, Doritos, Cheetos, Gatorade, Pepsi-Cola, Mountain Dew, Quaker, and SodaStream. PepsiCo’s product portfolio includes a wide range of enjoyable foods and beverages, including many iconic brands that generate more than $1 billion each in estimated annual retail sales.
Fill up the form below and we will send you the use case by e-mail.
During the 1990s, KADEN produced several toy car models made of zinc alloy and plastic. KADEN, along with many other companies in Europe, had been facing increasing foreign competition due to the lower costs of outsourcing labor and production to Asia (particularly to China). Leading up to 2020, KADEN had been reduced to a company of about 40 workers. Despite its diverse team of experts, KADEN faced the challenge of straying from its roots in production. A return to those roots was limited by lack of access to impactful, cost-effective, and timely manufacturing solutions.
Fill up the form below and we will send you the use case by e-mail.
Before embarking on this entrepreneurial journey Max Männel and Dario Dill, Co-Founders of MaxResolution3D, knew they needed an AM platform that could scale along with their business. The initial months, Männel and Dill scoured trade shows, attended demonstrations, and sought out to find the ideal AM platform on which to base their services. The MaxResolution3D team narrowed down their scope between a DLP system and the fully automated production cell for the Nexa3D® LSPc® printers. While speed and resolution were relatively comparable, there were many aspects that pointed to Nexa3D® as the right choice.
Fill up the form below and we will send you the use case by e-mail.
As a specialized bike manufacturer, integrating 3D components into their product designs gives FLYER a lot of flexibility and design freedom. Their innovation team utilized two in-house FDM 3D printers for prototyping, research and development. As the company continues to grow, FLYER must innovate quickly and release new products in order to keep pace. In order to support this growth, they saw a need to upgrade to an industrial stereolithography (SLA) style printer that could yield more parts, with a smooth, detailed surface finish, at faster speeds.
Fill up the form below and we will send you the use case by e-mail.
Since its founding in 1980, HAUX-LIFE-SUPPORT has stood for outstanding technical performance, innovation, quality and reliability. The company develops and manufactures state-of-the-art systems and equipment and provides tailor-made solutions for customers. The company needed to produce high and low preassure equipment for medical applications and diving bells for under water applications. The medical devices are used to treat certain illnesses; diving bells are used to rescue divers, for example, who had an accident under water and cannot rise above sea level.
Fill up the form below and we will send you the use case by e-mail.
Since the onset of the COVID 19 pandemic, demand for personal protective equipment (PPE) has increased rapidly. In addition to healthcare professionals, first responders and other essential workers are taking additional precautions to minimize the risk of infection. As a result, supply chains are overwhelmed and organizations everywhere are scrambling to ensure their employees are properly protected. Of particular concern is a shortage of facial protection. In many cases front line workers use face masks either in place of, or in addition to surgical masks.
Fill up the form below and we will send you the use case by e-mail.
Contract manufacturing — especially for smaller operations — is a game of profitable job portfolio management. The margins between competitive and non-competitive, successful, and unsuccessful are thinner than the metal chips the machines throw. Optimiz3D saw the opportunity to transform traditional contract manufacturing by integrating highly productive Additive Manufacturing into their process – enabling low-overhead, fast response and flexible manufacturing.Their goal was to maximize productivity and yield while also producing high-quality parts in less time with high machine utilization.
Fill up the form below and we will send you the use case by e-mail.
SKOP was conceptualized during the first lockdown in France, in April 2020. During this period, people with Covid-19 were in intensive care or sent home without any possibility of medical follow-up, due to the risk of infection. To help mitigate this, WeMed wanted to create a stethoscope that allows access to a truly remote medical diagnosis, to help substitute the visit to the doctor’s office. The goal was to make SKOP universal, in its ease of use, connecting to all tablets or phones, as well as telemedicine and communication platforms such as FaceTime, WhatsApp, and Zoom.
Fill up the form below and we will send you the use case by e-mail.
The Wilson R&D team was looking for more effective means to produce prototype injection mold tooling for a line of youth baseball bat handle. To implement these design changes within an existing baseball handle, the product development team was in search of an alternative prototyping process to significantly reduce the time it takes from “art-to-part”. Straying away from their traditional metal tooling methodologies, the team dove head first into redesigning this baseball component using 3D printing as the sole means towards producing this mold.
Fill up the form below and we will send you the use case by e-mail.
Though useful to an extent, traditional 3D printing technologies could not keep pace with VÚTS’ production of machines. Delays while parts were printed caused hold ups in the expedition of near-complete products, which were forced to sit in the production hall while the team waited for components to finish 3D printing. To overcome this challenge, VÚTS contacted its partner Industrial Technology Systems (ITS) s.r.o, tasking it to procure a 3D printer that could dramatically reduce lead times. “Nexa3D®’s platform has a clear differentiator to other printers — speed,” explained Filip Erdeljac, director of sales and business development at Industrial Technology Systems. “Speed is a common request from our customers, who often struggle to find a printer that meet their demands. Being a Nexa3D® reseller is pretty incredible, as it means our customers can produce multiple parts in under an hour!”
Fill up the form below and we will send you the use case by e-mail.
MaxResolution3D is filling the gap in an important sector of 3D printing – the space between prototyping and full-scale production via injection molding projects that need volumes up to ten thousand parts. FormFoundation, a trade-fair construction and shop-fitting partner, came to MaxResolution3D with a perfect use-case for their automated production cell. Foundation had an issue with the spotlights in their trade fair construction that created unwanted shadows. Previously, employees had to manually cut around these overhangs, which was time-consuming. They initially looked for a solution from a metals manufacturing company but found it too expensive for their needs. FormFoundation approached MaxResolution3D for a custom solution, needing 500-1000 small and mechanically strong parts to hold up the spotlights. The parts were required for an upcoming tradeshow booth installation.
Fill up the form below and we will send you the use case by e-mail.
While Alstom produces advanced, next-generation high-speed engines and rail cars, they also provide service to a large existing customer base with fleets that can be over 30 years old. With aging rolling stock there are a wide range of components that need to be maintained or replaced in order to extend a rail car’s life. “In 30 years maybe the original suppliers of the product no longer exist, maybe the molds used to produce the parts were destroyed because after 30 years there’s a cost to just maintain a mold.,” says Lorenzo. Suffice to say, it can be a challenge to find or produce spare parts. In mid-2022, Lorenzo’s team was tasked with producing hundreds of footrests that were in need of replacements – they would use 3D printing as an alternative to machine a new tool and molding for relatively low volumes. A higher speed 3D printer would also serve to improve their overall ability to respond better to customers’ urgent needs, “For our customer to stop a train to wait for spare parts is not economical, so we need to be able to provide them a quick solution.”
Fill up the form below and we will send you the use case by e-mail.
Complexity is a cost driver in manufacturing processes. Manufacturers have turned to additive manufacturing to simplify the production of complex objects. The flange wheel presented additional challenges due to its design complexity and the goal of replacing metal with a carbon-filled PEEK, a difficult thermoplastic to prototype. In the manufacturing of PEEK parts, process parameters need to be tightly controlled to achieve target performance, and Liebherr worked with Aitiip to develop and verify a manufacturing process that would meet the following requirements: - High-speed manufacturing process that will lead to 30% cost reductions - Recyclable materials - Light-weighting – with a goal of reaching a 40% weight reduction - One-shot manufacturing
Fill up the form below and we will send you the use case by e-mail.
With over 25 years of experience as an automotive and aeronautical engineer, Patrick Gaspard knows a thing or two about how vehicles work. After years of industry work, he founded R3D – an engineering and 3D printing service provider. In early 2021, automotive powerhouse Stellantis posted a bid for the design and manufacture of aftermarket components for 400 police cars for the French Gendarmerie. The request was to outfit the Peugeot 3008 Gendarmerie with nine individual brackets that would fixture various, expensive radio and computer components securely in place. The parts needed to be strong enough to secure the heavy electronics in both the driver compartment and in the trunk of the vehicle, even in extreme driving scenarios. On top of the required part performance, the vendor would have only three months to turn around 7200 components (18 individual components for each of the 400 vehicles). Not a lot of time when you consider these parts had to be custom designed from scratch.
Fill up the form below and we will send you the use case by e-mail.
While additive manufacturing has been at the center of ART’s business since the beginning, today about half of the end products they produce are not 3D printed, but cast urethane. Casting in urethane has allowed ART to produce low cost plastic parts with a quick turnaround. It is a very hands on process that takes a minimum of 24 hours per mold, requires a significant amount of labor, and the end result is a mold capable of up to 25 parts depending on the material being cast. That said, the effort appears worthwhile based on the high demand from their customers. “Our cast urethane is about 50% of our business right now and we’re almost maxed out,” says Bruce LeMaster, Founder and Vice President of ART. In addition to urethane, ART follows a similar 24 hour process for silicone molding. With such high demand, LeMaster and the team at ART were all but maxed out with a very real cap on the volume of projects they could take on.
Fill up the form below and we will send you the use case by e-mail.
Murtfeldt had a new customer that needed to produce a specific type of high-resolution electrical connector requiring extreme precision as well as an excellent surface finish in order to be effective. The team determined that it could not achieve its aims using its existing SLS or FDM equipment, so they worked closely with ProductionToGo to investigate available alternative technologies. The NXE 400 industrial resin 3D printer from Nexa3D® provides an ultrafast production solution for the team at Murtfeldt Additive Solutions. “After benchmarking, it became clear that only the Nexa3D® machine provided the required part performance with an appropriate material, combined with the high throughput that was needed,” explained Maximilian Neck, ProductionToGo’s head of additive manufacturing. “They essentially bought the Nexa3D® NXE 400 in order to fulfill this customer and this project.” Post-sale, ProductionToGo provided Murtfeldt with user training, benchmarking and other support, as well.
Fill up the form below and we will send you the use case by e-mail.
Perrigo is a leading over-the-counter (OTC) pharmaceutical company selling products that are familiar to most grocery stores across the US and globally. The company recently turned to 3D resin printing to manufacture previously outsourced original equipment manufacturer (OEM) items, such as cartoners and caps, to ensure they were always in stock and available for production.
Fill up the form below and we will send you the use case by e-mail.
![]() |
|
Photos of the event |
![]() |
|
Photos of the event |
![]() |
|
On-demand Webinar |
![]() |
|
Watch the video |
![]() |
|
Watch the video |
![]() |
|
Watch the video |
![]() |
|
On-demand Webinar |
![]() |
|
Read more |
![]() |
|
Read more |
![]() |
|
Read more |
![]() |
|
Read more |
![]() |
|
Read more |
![]() |
|
Read more |
![]() |
|
Read more |
![]() |
|
Read more |
![]() |
|
Read more |
![]() |
|
Read more |
Cookie settings
We use cookies to provide you with the best possible experience. They also allow us to analyze user behavior in order to constantly improve the website for you. Privacy Policy