3D printers
High quality 3D printers
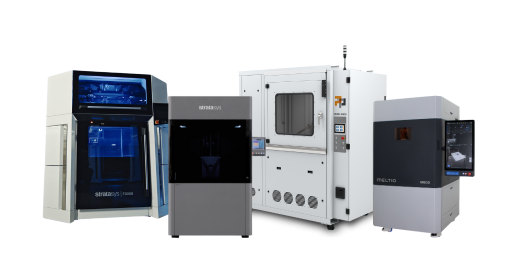
![]() |
All About Automation - Friedrichshafen 2025 |
Photos of the event |
![]() |
DENTAL Bern 2024 |
Photos of the Event |
![]() |
Tag der offenen Tür – Desktop-3D-Druck |
Watch the video |
![]() |
What is possible with dental 3D printing? Crowns, bridges, full-color models and more! |
On-demand Webinar |
![]() |
All About Automation - Friedrichshafen 2024 |
Photos of the event |
![]() |
No acquisition costs, high quality - 3D printing on-demand with PartsToGo |
On-demand Webinar |
![]() |
Nexa3D® Road Show – Karlsbad |
Watch the video |
![]() |
Nexa3D® Road Show – Cologne |
Watch the video |
![]() |
Nexa3D® Road Show – Munich |
Watch the video |
![]() |
Licht macht fest - Photopolymere im 3D-Druck |
On-demand Webinar |
![]() |
How to correctly choose a professional 3D printer for 2023 |
On-demand Webinar |
![]() |
The digital dentistry solution for speed and precision - Nexa3D |
On-demand Webinar |
![]() |
Nexa3D XiP - The ultrafast desktop 3D printer |
On-demand Webinar |
![]() |
The definitive guide to the different resins available for 3D printing |
Read more |
![]() |
Digital Teeth - the possibilities of Additive Manufacturing in the dental industry |
Read more |
![]() |
Wie die Effektivität eines 3D-Druckers weiter gesteigert werden kann |
Read more |
![]() |
Additive Manufacturing in Medicine - How 3D Printing can save Lives |
Read more |
![]() |
Additive Manufacturing with Resin - An Introduction |
Read more |
![]() |
How to choose the correct professional 3D printer |
Read more |
![]() |
How Additive Manufacturing is revolutionizing the automotive industry |
Read more |
![]() |
Product development with the help of 3D printing |
Read more |
![]() |
3D printing and the benefits for aviation |
Read more |